What is PCB Wiring?
PCB wiring refers to the process of connecting components on a printed circuit board using conductive traces, usually made of copper. These traces are designed to carry electrical signals and power between components, allowing the board to function as a complete electronic system.
Tools for PCB Wiring
Before diving into the wiring process, it’s essential to have the right tools on hand. Some of the most common tools used for PCB wiring include:
Soldering Iron
A soldering iron is a hand tool used to melt solder, a metal alloy, to create electrical connections between components and the PCB. When choosing a soldering iron, consider factors such as wattage, temperature control, and tip size.
Solder
Solder is a metal alloy, typically made of tin and lead, that melts at a relatively low temperature. It is used to create electrical and mechanical connections between components and the PCB. When selecting solder, consider the alloy composition, diameter, and flux type (rosin core or lead-free).
Soldering Wick
Soldering wick, also known as Desoldering Braid, is a braided copper wire coated with flux. It is used to remove excess solder from connections or to correct soldering mistakes.
Wire Cutters and Strippers
Wire cutters and strippers are used to prepare wires for soldering. Cutters trim the wires to the desired length, while strippers remove the insulation from the ends of the wires, exposing the bare metal for soldering.
Tweezers and Pliers
Tweezers and pliers are helpful for handling small components and wires during the soldering process. They can also be used to bend component leads and hold parts in place while soldering.
PCB Wiring Techniques
There are several techniques for wiring a PCB, each with its own advantages and disadvantages. Some of the most common methods include:
Through-Hole Soldering
Through-hole soldering involves inserting component leads through holes drilled in the PCB and soldering them to pads on the opposite side of the board. This method is often used for larger components and provides a strong mechanical connection.
Step-by-Step Through-Hole Soldering
- Insert the component leads through the corresponding holes in the PCB.
- Bend the leads slightly outward to hold the component in place.
- Apply heat to the pad using the soldering iron, and then touch the solder to the pad and the component lead.
- Allow the solder to flow around the connection, creating a smooth, shiny joint.
- Trim any excess lead length with wire cutters.
Surface Mount Soldering
Surface mount soldering involves attaching components directly to pads on the surface of the PCB without using through-holes. This method is often used for smaller components and allows for higher component density on the board.
Step-by-Step Surface Mount Soldering
- Apply a small amount of solder paste to the pads using a stencil or syringe.
- Place the surface mount component onto the pads, ensuring proper alignment.
- Use tweezers to hold the component in place while applying heat to the pads with the soldering iron.
- Allow the solder paste to melt and flow around the connection, creating a solid joint.
Wire Wrapping
Wire wrapping is a solderless wiring method that involves tightly wrapping a small gauge wire around a square post on the PCB. This method is often used for prototyping or low-volume production, as it allows for easy modifications and repairs.
Step-by-Step Wire Wrapping
- Strip a small amount of insulation from the end of the wire using a wire stripper.
- Insert the wire into the wire wrapping tool and align it with the square post on the PCB.
- Rotate the tool around the post, tightly wrapping the wire and creating a secure connection.
- Trim any excess wire with wire cutters.
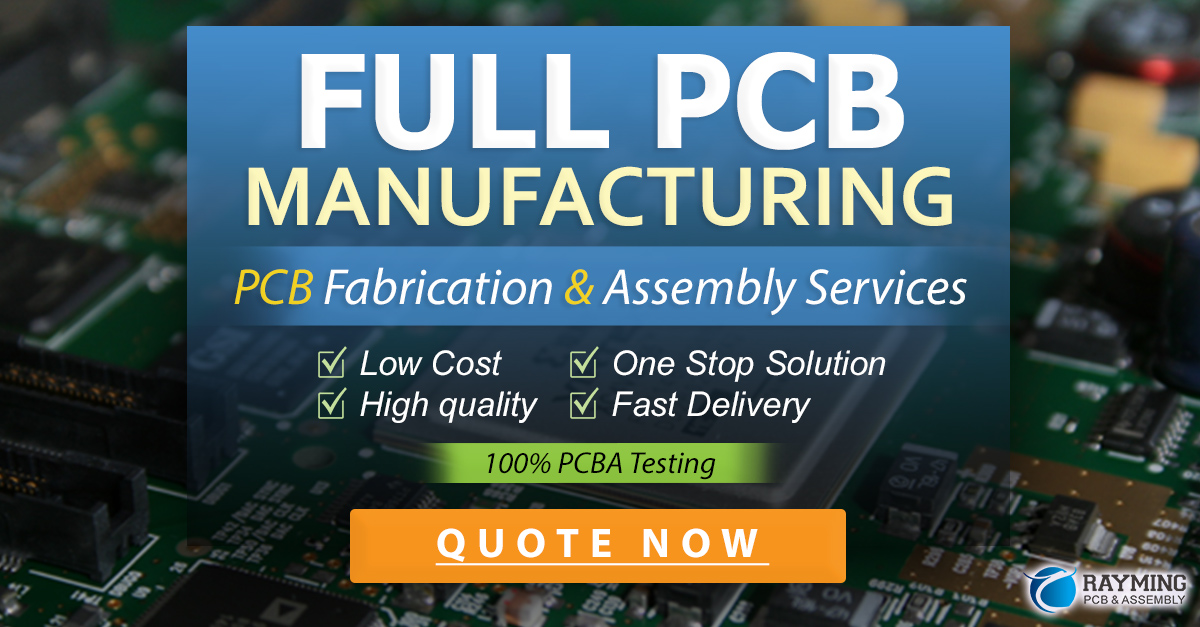
PCB Wiring Tips and Best Practices
To ensure the best results when wiring a PCB, consider the following tips and best practices:
- Keep soldering iron tips clean and well-maintained to ensure proper heat transfer and prevent contamination.
- Use the appropriate solder and flux for your application, considering factors such as temperature requirements and environmental concerns.
- Maintain proper ventilation when soldering to avoid inhaling fumes.
- Wear protective gear, such as safety glasses and gloves, to prevent injuries.
- Practice good soldering techniques, such as applying the right amount of heat and solder, and creating smooth, shiny joints.
- Double-check component orientation and polarity before soldering to avoid mistakes.
- Use a multimeter to test connections and ensure proper functionality.
Common PCB Wiring Mistakes and How to Avoid Them
Even experienced PCB designers and technicians can make mistakes during the wiring process. Some common errors include:
Cold Solder Joints
Cold solder joints occur when the solder fails to melt completely, resulting in a dull, grainy appearance and a weak connection. To avoid cold joints, ensure that the soldering iron is at the proper temperature and that you apply heat to both the pad and the component lead simultaneously.
Bridging
Bridging occurs when excess solder creates an unintended connection between two or more pads or traces. To prevent bridging, use the appropriate amount of solder and be careful not to apply too much heat, which can cause the solder to flow excessively.
Incorrect Component Orientation
Incorrectly oriented components can lead to circuit malfunctions or damage. Always double-check component orientation and polarity before soldering, referring to the PCB layout and component datasheets as needed.
Overheating Components
Applying too much heat during soldering can damage sensitive components. To avoid overheating, use the lowest temperature setting that still allows for proper solder flow, and limit the time the soldering iron is in contact with the component.
Frequently Asked Questions (FAQ)
-
What is the difference between lead-based and lead-free solder?
Lead-based solder contains a mixture of tin and lead, while lead-free solder is made of tin and other metals, such as silver and copper. Lead-free solder is becoming more common due to environmental and health concerns, but it typically requires higher soldering temperatures and may be more prone to joint defects. -
Can I use a regular soldering iron for surface mount soldering?
While it is possible to use a regular soldering iron for surface mount soldering, it is recommended to use a soldering iron with a finer tip and adjustable temperature control for better precision and to avoid damaging small components. -
How do I remove a soldered component from a PCB?
To remove a soldered component, use a desoldering wick or a desoldering pump to remove the solder from the joints. Apply heat to the joint while gently pulling on the component with tweezers or pliers until it comes free. -
What is the best way to clean a PCB after soldering?
Use a commercial PCB cleaner or isopropyl alcohol to remove any flux residue or contaminants from the board. Apply the cleaner with a soft brush or lint-free cloth, then rinse the board with distilled water and dry it thoroughly. -
How can I improve my PCB wiring skills?
Practice is key to improving your PCB wiring skills. Start with simple projects and gradually work your way up to more complex designs. Invest in quality tools and materials, and seek guidance from experienced professionals or online resources when needed.
Soldering Method | Advantages | Disadvantages |
---|---|---|
Through-Hole | – Strong mechanical connection – Easier for beginners |
– Requires drilling holes – Lower component density |
Surface Mount | – Higher component density – Faster assembly |
– Requires more precise soldering skills – Components can be damaged by heat |
Wire Wrapping | – Solderless – Easy to modify and repair |
– Not suitable for high-volume production – Requires special tools and skills |
In conclusion, PCB wiring is a critical aspect of creating functional and reliable electronic devices. By understanding the various tools, techniques, and best practices involved in the process, you can ensure that your PCBs are wired correctly and perform as intended. Whether you are a beginner or an experienced professional, investing time in developing your PCB wiring skills will pay off in the long run, leading to better quality products and more efficient workflows.
Leave a Reply