What is PCB Warpage?
PCB warpage refers to the deviation of a printed circuit board from its intended flat shape. It is a dimensional instability that occurs when the board experiences uneven thermal expansion or contraction during the manufacturing process or during its operational life. The warpage can manifest as twisting, bowing, or curving of the PCB, which can be classified into different types based on the direction and severity of the deformation.
Types of PCB Warpage
- Diagonal warpage: The PCB deforms along its diagonal axis, resulting in a twisted appearance.
- Convex warpage: The PCB bows outwards, forming a convex shape.
- Concave warpage: The PCB bows inwards, forming a concave shape.
- Complex warpage: A combination of diagonal, convex, and concave warpage, resulting in a complex deformation pattern.
The severity of PCB warpage is typically measured in mils (thousandths of an inch) or micrometers (μm) and can range from a few mils to several hundred mils, depending on the size and thickness of the board.
Causes of PCB Warpage
Several factors can contribute to PCB warpage during the manufacturing process and the board’s operational life. Understanding these causes is crucial for preventing and mitigating warpage issues.
Material Properties
The choice of materials used in PCB fabrication plays a significant role in determining the board’s susceptibility to warpage. Some key material properties that influence warpage include:
- Coefficient of Thermal Expansion (CTE): Different materials expand and contract at different rates when exposed to temperature changes. A mismatch in CTE between the PCB substrate, copper layers, and components can lead to warpage.
- Glass Transition Temperature (Tg): The temperature at which a material transitions from a rigid, glassy state to a more flexible, rubbery state. Materials with lower Tg values are more prone to warpage at elevated temperatures.
- Moisture absorption: Some PCB materials, such as FR-4, can absorb moisture from the environment, leading to dimensional changes and potential warpage.
Manufacturing Process
The PCB manufacturing process involves several steps that can introduce stresses and contribute to warpage:
- Lamination: Uneven pressure or temperature distribution during the lamination of multiple layers can cause warpage.
- Etching: Non-uniform etching of copper layers can result in unbalanced stress distribution, leading to warpage.
- Soldering: High-temperature soldering processes, such as reflow soldering, can induce thermal stresses and cause warpage.
Design Factors
Certain design choices can also increase the risk of PCB warpage:
- Board thickness: Thinner boards are more susceptible to warpage due to their reduced stiffness.
- Copper distribution: Uneven copper distribution across the layers can create unbalanced stress, leading to warpage.
- Component placement: The location and orientation of heavy components can affect the board’s balance and contribute to warpage.
Effects of PCB Warpage
PCB warpage can have several detrimental effects on the performance and reliability of electronic devices:
Component Misalignment
Warped PCBs can cause component misalignment during the assembly process. Surface-mount components, such as BGAs and QFPs, are particularly sensitive to warpage-induced misalignment. This can lead to poor soldering joints, reduced electrical conductivity, and potential short circuits or open connections.
Soldering Defects
Warpage can also result in soldering defects, such as bridging, tombstoning, and insufficient solder joint formation. These defects can compromise the mechanical and electrical integrity of the solder joints, leading to premature failure or intermittent issues.
Mechanical Stress
A warped PCB can experience increased mechanical stress during the assembly process and in the final product. This stress can cause component cracking, delamination of layers, and reduced overall reliability of the device.
Thermal Management Issues
Warpage can affect the thermal management of the PCB by altering the contact between the board and heatsinks or thermal interface materials. This can lead to uneven heat dissipation, hotspots, and potential thermal runaway, which can degrade the performance and lifespan of electronic components.
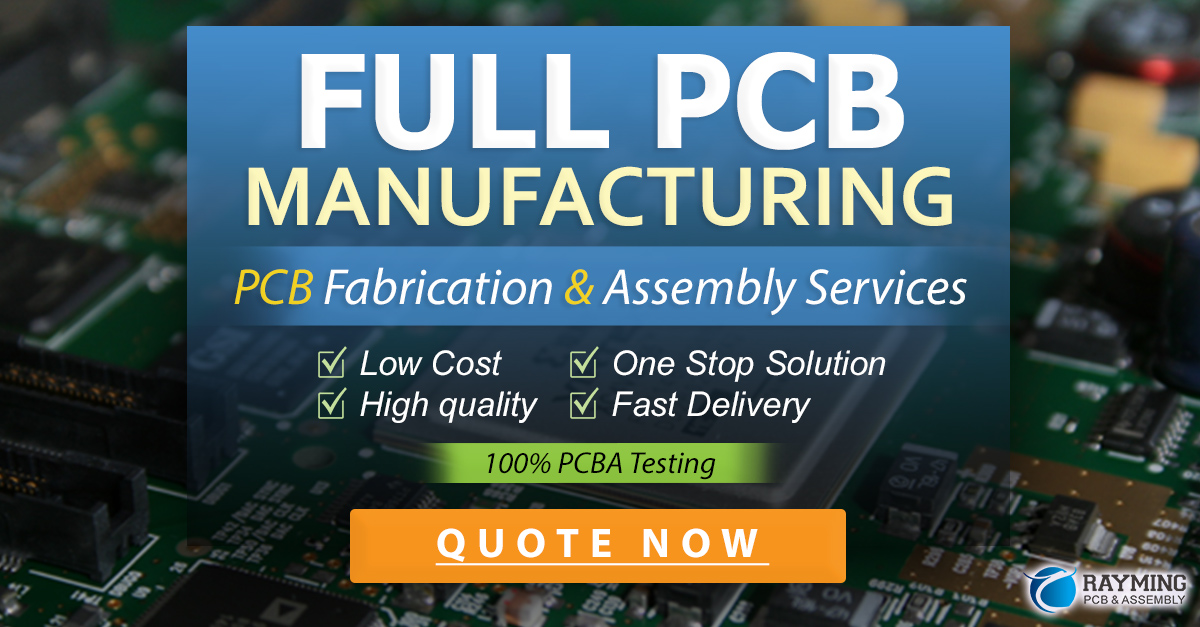
Prevention and Mitigation Strategies
To minimize the risk of PCB warpage and its associated effects, several prevention and mitigation strategies can be employed:
Material Selection
Choosing appropriate materials for PCB fabrication is crucial for reducing warpage:
- Use materials with similar CTE values to minimize thermal expansion mismatches.
- Select materials with higher Tg values to improve thermal stability.
- Opt for low-moisture-absorption materials to reduce dimensional changes due to humidity.
Design Optimization
Optimizing the PCB design can help prevent warpage:
- Increase board thickness, especially for larger PCBs, to improve stiffness and resist deformation.
- Balance copper distribution across layers to minimize uneven stress distribution.
- Position heavy components near the center of the board to maintain balance and reduce warpage.
Manufacturing Process Control
Implementing strict process controls during PCB manufacturing can help mitigate warpage:
- Ensure uniform pressure and temperature distribution during lamination.
- Monitor and control the etching process to achieve consistent copper removal.
- Optimize soldering profiles to minimize thermal stress and warpage.
Warpage Measurement and Inspection
Regular measurement and inspection of PCBs for warpage can help identify and address issues early in the manufacturing process:
- Use 3D scanning or shadow moiré techniques to measure warpage.
- Establish warpage acceptance criteria based on industry standards and specific application requirements.
- Implement automated optical inspection (AOI) systems to detect warpage-related defects during assembly.
Simulation and Modeling
Utilizing simulation and modeling tools can help predict and optimize PCB warpage behavior:
- Perform finite element analysis (FEA) to simulate thermal and mechanical stresses on the PCB.
- Use design of experiments (DOE) techniques to identify critical factors affecting warpage.
- Optimize the PCB layout and material properties based on simulation results.
Frequently Asked Questions (FAQ)
1. What is the acceptable level of PCB warpage?
The acceptable level of PCB warpage depends on the specific application, component types, and manufacturing processes involved. Industry standards, such as IPC-TM-650 2.4.22, provide guidelines for measuring and evaluating PCB warpage. Generally, warpage should be kept within a few mils (0.001 inches) to ensure proper component assembly and reliability.
2. Can PCB warpage be corrected after the board is manufactured?
In some cases, minor PCB warpage can be corrected through techniques such as baking, pressing, or selective heating. However, these methods may not be effective for severe warpage or may introduce additional stresses to the board. It is always better to prevent warpage through proper material selection, design optimization, and process control.
3. How does PCB thickness affect warpage?
Thicker PCBs are generally less susceptible to warpage due to their increased stiffness and resistance to deformation. However, increasing the board thickness may not always be practical due to design constraints, cost considerations, or weight limitations. A balance must be struck between thickness and other design factors to minimize warpage while meeting the application requirements.
4. What role does the reflow soldering process play in PCB warpage?
The reflow soldering process, which involves exposing the PCB and components to high temperatures, can significantly contribute to warpage. During reflow, the PCB and components experience thermal expansion and contraction, which can lead to uneven stress distribution and deformation. Optimizing the reflow profile, such as ramp rates, peak temperatures, and dwell times, can help minimize thermal stress and reduce warpage.
5. How can PCB warpage simulation tools help in the design process?
PCB warpage simulation tools, such as finite element analysis (FEA) software, can help designers predict and optimize the warpage behavior of a PCB before it is manufactured. These tools can simulate the thermal and mechanical stresses on the board, allowing designers to identify potential warpage issues and make necessary adjustments to the layout, material properties, or layer stack-up. By utilizing simulation tools, designers can reduce the risk of warpage-related problems and improve the overall reliability of the final product.
Conclusion
PCB warpage is a critical issue that can have significant impacts on the performance, reliability, and manufacturing yield of electronic devices. Understanding the causes, effects, and mitigation strategies for PCB warpage is essential for electronics manufacturers to ensure the production of high-quality, reliable products.
By selecting appropriate materials, optimizing PCB designs, implementing strict process controls, and utilizing simulation and measurement tools, manufacturers can effectively prevent and manage PCB warpage. Addressing this issue early in the design and manufacturing process can lead to reduced costs, improved product quality, and enhanced customer satisfaction.
As the electronics industry continues to evolve, with increasing demands for miniaturization, higher performance, and lower costs, the importance of managing PCB warpage will only grow. By staying informed about the latest techniques and best practices for preventing and mitigating warpage, electronics manufacturers can remain competitive and deliver innovative, reliable products to their customers.
Leave a Reply