Introduction to PCB Design and PCBHacks
Printed Circuit Board (PCB) design is the process of creating the layout and circuitry for an electronic device. As technology advances and devices become more complex, efficient PCB design becomes increasingly crucial. This article will explore various PCBHacks – tips and tricks to optimize your PCB design process, resulting in better performance, reliability, and cost-effectiveness.
The Importance of Proper PCB Design
A well-designed PCB ensures:
– Optimal device performance
– Reduced electromagnetic interference (EMI)
– Improved signal integrity
– Enhanced reliability and durability
– Cost-effectiveness in manufacturing
PCBHacks for Schematic Design
Keep Your Schematic Organized
- Use a consistent naming convention for components and nets
- Group related components together
- Use hierarchical design for complex circuits
- Clearly label power and ground nets
Use Schematic Design Tools Effectively
Tool | Purpose |
---|---|
Library Manager | Organize and manage component libraries |
Design Rule Check | Verify the schematic against design rules |
Bill of Materials | Generate a list of required components |
Netlist Generation | Create a netlist for PCB layout |
Simulate Your Circuit
- Use SPICE simulation to verify circuit behavior
- Perform worst-case and Monte Carlo analysis
- Simulate critical paths and high-speed signals
PCBHacks for Component Placement
Group Related Components
- Place components with similar functions together
- Keep sensitive components away from noise sources
- Consider the flow of signals through the circuit
Optimize for Manufacturing
- Use standard component packages when possible
- Provide adequate spacing between components
- Orient components for easy soldering and inspection
Consider Thermal Management
- Place heat-generating components away from sensitive devices
- Provide sufficient copper area for heat dissipation
- Use thermal vias to transfer heat to other layers
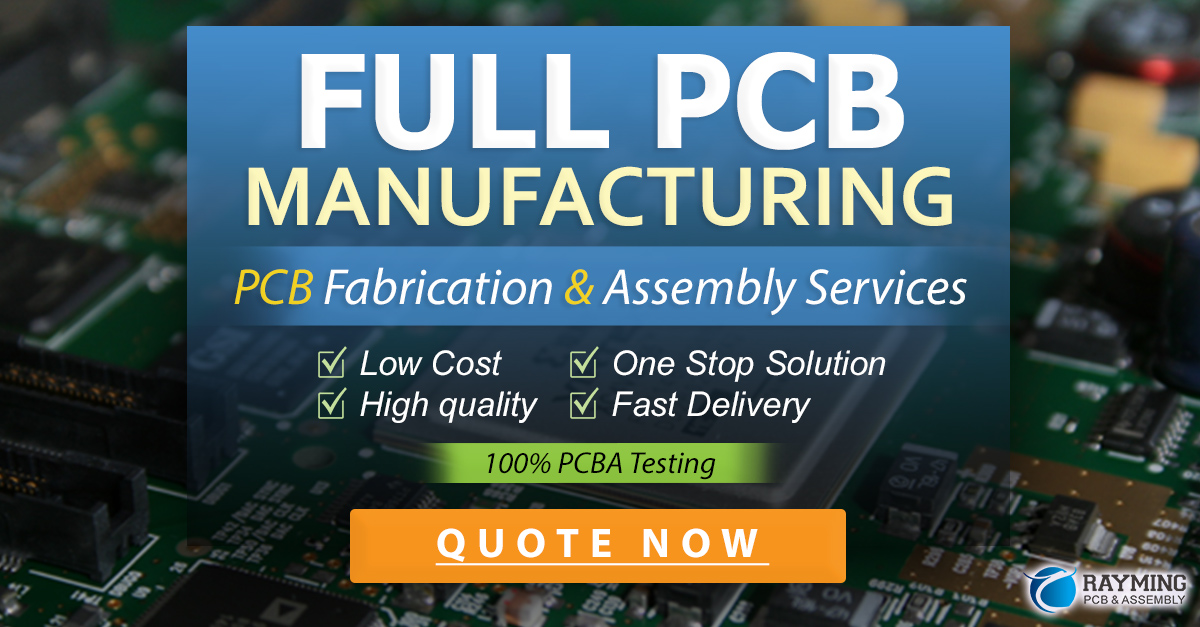
PCBHacks for Routing and Layout
Use a Ground Plane
- Dedicate a layer for ground to reduce EMI and improve signal integrity
- Connect components to the ground plane with short traces
- Use a ground pour on the top and bottom layers
Minimize Crosstalk and EMI
- Route sensitive signals away from noise sources
- Use guard traces or ground shields for critical signals
- Avoid parallel routing of high-speed signals
Optimize Trace Widths and Spacing
Signal Type | Trace Width (mil) | Trace Spacing (mil) |
---|---|---|
Power | 20-50 | 20-30 |
Ground | 20-50 | 20-30 |
High-speed | 8-12 | 12-20 |
Low-speed | 10-16 | 8-12 |
Consider Signal Integrity
- Match trace lengths for differential pairs
- Use termination resistors for high-speed signals
- Avoid sharp bends in traces to reduce reflections
PCBHacks for Power Distribution
Use Separate Power and Ground Planes
- Dedicate layers for power and ground distribution
- Use a star or grid topology for power distribution
- Place Decoupling capacitors close to ICs
Choose the Right Decoupling Capacitors
Frequency Range | Capacitor Type | Value Range |
---|---|---|
High (>100 MHz) | Ceramic | 0.01-0.1 µF |
Mid (1-100 MHz) | Ceramic | 0.1-10 µF |
Low (<1 MHz) | Tantalum | 10-100 µF |
Minimize Voltage Drop
- Use wide traces for power distribution
- Place Voltage Regulators close to the loads
- Use copper pours to increase current capacity
PCBHacks for Testing and Debugging
Include Test Points
- Place test points at critical nodes in the circuit
- Use standard test point sizes and spacing
- Label test points clearly on the silk screen
Design for Accessibility
- Provide access to components for probing and rework
- Use connectors for easy connection to test equipment
- Consider using a Bed-of-Nails Test fixture
Use Built-In Self-Test (BIST)
- Implement BIST features in your design
- Use boundary scan (JTAG) for testing complex ICs
- Include LED indicators for power, status, and faults
Advanced PCBHacks
Use High-Speed PCB Material
- Choose materials with low Dielectric Constant and dissipation factor
- Consider using high-Tg materials for improved thermal stability
- Use low-loss materials for high-frequency applications
Optimize Via Design
- Use microvias for high-density designs
- Minimize via stubs to reduce signal reflections
- Use blind and Buried Vias for complex multilayer boards
Implement Electromagnetic Compatibility (EMC) Measures
- Use shielding and filtering to reduce EMI
- Place sensitive components away from board edges
- Use ferrite beads for high-frequency noise suppression
FAQ
Q1: What is the most important factor in PCB design?
A1: Signal integrity is one of the most critical factors in PCB design. Ensuring that signals reach their intended destinations without distortion, crosstalk, or interference is essential for optimal device performance and reliability.
Q2: How can I reduce electromagnetic interference (EMI) in my PCB design?
A2: To reduce EMI, use a dedicated ground plane, route sensitive signals away from noise sources, use guard traces or ground shields for critical signals, and implement shielding and filtering measures.
Q3: What are some common mistakes to avoid in PCB design?
A3: Common mistakes include poor component placement, inadequate power distribution, incorrect trace sizing and spacing, neglecting thermal management, and failing to consider manufacturing constraints.
Q4: How can I optimize my PCB design for manufacturing?
A4: To optimize for manufacturing, use standard component packages, provide adequate spacing between components, orient components for easy soldering and inspection, and consider using design for manufacturing (DFM) tools to identify potential issues.
Q5: What tools are essential for efficient PCB design?
A5: Essential tools for PCB design include schematic capture software, PCB layout software, library management tools, design rule check (DRC) tools, and simulation software for verifying circuit behavior and signal integrity.
Conclusion
Effective PCB design is a combination of art and science, requiring a deep understanding of electronic principles, manufacturing constraints, and design best practices. By employing the PCBHacks discussed in this article – from schematic organization to advanced techniques like high-speed materials and EMC measures – you can create PCBs that are high-performing, reliable, and cost-effective. As technology continues to evolve, staying up-to-date with the latest design techniques and tools will be essential for success in the ever-changing world of PCB design.
Leave a Reply