Introduction to PCB Thermal Resistance
Printed Circuit Boards (PCBs) are the backbone of modern electronics, providing a platform for components to be mounted and interconnected. As electronic devices become more compact and powerful, managing heat dissipation becomes a critical factor in ensuring optimal performance and reliability. This is where the concept of PCB thermal resistance comes into play.
Thermal resistance is a measure of a PCB’s ability to dissipate heat from its components to the surrounding environment. It is expressed in units of degrees Celsius per watt (°C/W) and represents the temperature rise of a component or PCB per unit of power dissipated. A lower thermal resistance indicates better heat dissipation capabilities, while a higher thermal resistance suggests potential thermal management challenges.
Factors Affecting PCB Thermal Resistance
Several factors influence a PCB’s thermal resistance, including:
- Material properties: The thermal conductivity of the PCB substrate, copper layers, and any additional thermal management materials used.
- Board thickness: Thicker PCBs generally have lower thermal resistance due to increased heat spreading capabilities.
- Copper thickness and coverage: Thicker copper layers and larger copper coverage can enhance heat dissipation.
- Component placement: The layout and spacing of components on the PCB affect heat distribution and dissipation.
- Thermal vias: The use of thermal vias, which are conductive pathways through the PCB, can improve heat transfer between layers and to heat sinks.
Thermal Conductivity of PCB Materials
The thermal conductivity of the materials used in PCB Construction plays a crucial role in determining the board’s thermal resistance. Some common PCB substrate materials and their thermal conductivities are listed in the table below:
Material | Thermal Conductivity (W/m·K) |
---|---|
FR-4 | 0.3 – 0.4 |
Alumina (Al2O3) | 20 – 30 |
Aluminum Nitride (AlN) | 150 – 180 |
Copper | 385 – 400 |
As evident from the table, copper has the highest thermal conductivity among the listed materials, making it an excellent choice for heat dissipation. However, the overall thermal resistance of a PCB is determined by the combination of all materials used, including the substrate, copper layers, and any additional thermal management materials.
The Role of Copper in PCB Thermal Management
Copper is the most commonly used conductor in PCBs due to its excellent electrical and thermal properties. The thickness and coverage of copper layers on a PCB have a significant impact on its thermal resistance.
Increasing the thickness of copper layers can improve heat spreading and reduce thermal resistance. The table below shows the relationship between copper thickness and its contribution to thermal conductivity:
Copper Thickness (oz) | Thickness (mm) | Thermal Conductivity Contribution (W/m·K) |
---|---|---|
0.5 | 0.018 | 0.069 |
1 | 0.036 | 0.138 |
2 | 0.071 | 0.276 |
3 | 0.107 | 0.414 |
In addition to copper thickness, the coverage of copper on the PCB also affects thermal resistance. Larger copper pour areas, such as ground planes and power planes, can help spread heat more effectively across the board.
Thermal Vias and Heat Transfer
Thermal vias are conductive pathways that run through the PCB, connecting different layers and providing a means for heat to transfer between them. They are essential for multi-layer PCBs, where heat needs to be dissipated from inner layers to outer layers and eventually to the surrounding environment or attached heat sinks.
The effectiveness of thermal vias depends on several factors, including:
- Via diameter: Larger diameter vias have lower thermal resistance and can transfer heat more efficiently.
- Via pitch: The spacing between vias affects the overall thermal conductivity of the PCB. Closer spacing results in better heat transfer.
- Via fill material: Filling thermal vias with conductive materials, such as copper or thermal epoxy, can enhance heat transfer and reduce thermal resistance.
The table below compares the thermal resistance of different via configurations:
Via Configuration | Via Diameter (mm) | Via Pitch (mm) | Thermal Resistance (°C/W) |
---|---|---|---|
Unfilled | 0.3 | 1.0 | 120 |
Copper-filled | 0.3 | 1.0 | 40 |
Copper-filled | 0.5 | 1.0 | 20 |
As shown in the table, copper-filled vias with larger diameters and closer spacing provide the lowest thermal resistance, making them an effective solution for heat transfer in PCBs.
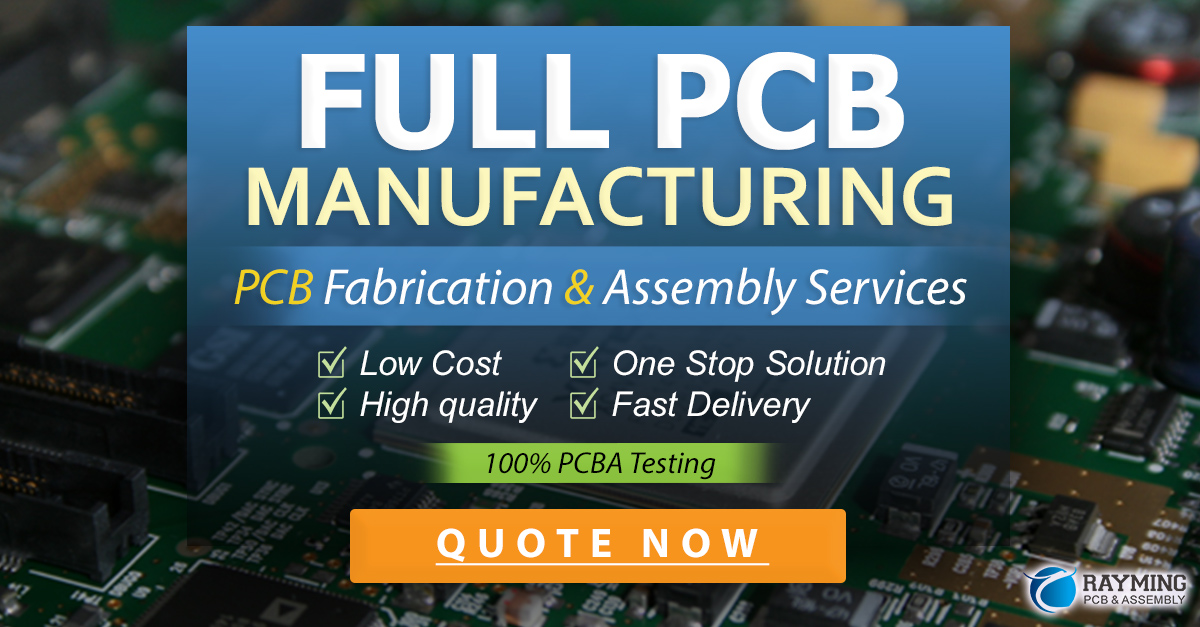
Calculating PCB Thermal Resistance
To calculate the thermal resistance of a PCB, several methods can be employed, including analytical calculations, finite element analysis (FEA), and experimental measurements.
Analytical Calculations
Analytical calculations involve using equations and material properties to estimate the thermal resistance of a PCB. One commonly used equation is:
Rth = (L) / (k × A)
Where:
– Rth is the thermal resistance (°C/W)
– L is the thickness of the PCB (m)
– k is the thermal conductivity of the PCB material (W/m·K)
– A is the cross-sectional area of the PCB (m²)
This equation provides a simplified approximation of the PCB’s thermal resistance, assuming one-dimensional heat flow and uniform material properties. However, it does not account for the complexities of real-world PCBs, such as component placement, copper distribution, and thermal vias.
Finite Element Analysis (FEA)
Finite Element Analysis (FEA) is a numerical method that divides a PCB into smaller elements and solves heat transfer equations for each element. This approach provides a more accurate representation of the PCB’s thermal behavior, taking into account factors such as component placement, copper distribution, and thermal vias.
FEA software packages, such as ANSYS and COMSOL, allow designers to create detailed 3D models of PCBs and simulate their thermal performance under various operating conditions. These simulations can help identify hot spots, optimize component placement, and evaluate the effectiveness of thermal management strategies.
Experimental Measurements
Experimental measurements involve testing physical PCB Prototypes to determine their actual thermal resistance. This can be done using thermocouples, infrared cameras, or other temperature measurement devices.
To measure the thermal resistance of a PCB, the following steps can be followed:
- Apply a known power dissipation to a component on the PCB.
- Measure the temperature rise of the component relative to the ambient temperature.
- Calculate the thermal resistance using the equation:
Rth = (Tcomponent – Tambient) / Pdissipated
Where:
– Rth is the thermal resistance (°C/W)
– Tcomponent is the temperature of the component (°C)
– Tambient is the ambient temperature (°C)
– Pdissipated is the power dissipated by the component (W)
Experimental measurements provide the most accurate assessment of a PCB’s thermal resistance, as they account for real-world conditions and manufacturing variability. However, they require physical prototypes and specialized equipment, making them more time-consuming and costly compared to analytical calculations and FEA simulations.
Thermal Management Techniques for PCBs
To mitigate the effects of high thermal resistance and ensure proper heat dissipation, various thermal management techniques can be employed in PCB design and assembly.
Component Placement and Spacing
Proper component placement and spacing are crucial for optimal heat distribution and dissipation on a PCB. Some guidelines to follow include:
- Place high-power components, such as processors and power regulators, away from heat-sensitive components to minimize thermal interference.
- Provide adequate spacing between components to allow for air circulation and heat dissipation.
- Position components in a way that promotes natural convection cooling, with hot components placed higher on the board.
Copper Pour and Thermal Planes
Increasing the copper coverage on a PCB can significantly improve its heat spreading capabilities. This can be achieved by:
- Using larger copper pour areas for ground and power planes.
- Placing copper fills in unused areas of the PCB to create additional heat spreading paths.
- Utilizing thermal planes, which are dedicated copper layers designed to spread heat evenly across the board.
Thermal Interface Materials (TIMs)
Thermal Interface Materials (TIMs) are substances applied between components and heat sinks to enhance heat transfer by filling air gaps and reducing thermal resistance. Common TIMs include:
- Thermal greases and pastes: These are viscous materials that conform to surface irregularities and provide good thermal conductivity.
- Thermal pads: These are pre-cut, thermally conductive materials that offer ease of application and consistent thickness.
- Phase Change Materials (PCMs): These materials change from solid to liquid at a specific temperature, allowing them to conform to surfaces and provide excellent thermal conductivity.
Heat Sinks and Cooling Solutions
In cases where the PCB’s inherent thermal management capabilities are insufficient, external cooling solutions can be employed to dissipate heat more effectively. Some common options include:
- Heat sinks: These are metal structures with fins or pins that increase the surface area for heat dissipation. They are typically attached to high-power components using thermal adhesives or mechanical fasteners.
- Fans and blowers: Forced air cooling using fans or blowers can significantly enhance heat dissipation by increasing airflow over the PCB and its components.
- Liquid cooling: For high-performance applications, liquid cooling systems can be used to remove heat from the PCB and its components more efficiently than air cooling solutions.
PCB Thermal Design Considerations
When designing a PCB with thermal management in mind, several key considerations should be taken into account:
-
Power dissipation estimation: Determine the expected power dissipation of each component on the PCB to identify potential thermal hotspots and design appropriate thermal management solutions.
-
Material selection: Choose PCB materials with suitable thermal conductivity and dielectric properties based on the application requirements and operating conditions.
-
Layer stack-up: Optimize the PCB layer stack-up to promote heat spreading and minimize thermal resistance. This may involve using thicker copper layers, adding dedicated thermal planes, or incorporating high-conductivity materials.
-
Via placement and design: Strategically place thermal vias to provide efficient heat transfer paths between layers and to heat sinks. Consider via diameter, pitch, and fill material to maximize thermal performance.
-
Component placement and routing: Arrange components and route traces in a way that minimizes thermal interference and promotes heat dissipation. Avoid placing high-power components close to heat-sensitive components, and provide adequate spacing for airflow.
-
Thermal simulation and analysis: Utilize FEA tools to simulate the PCB’s thermal behavior and identify potential issues early in the design process. Iterate the design based on simulation results to optimize thermal performance.
-
Manufacturing and assembly considerations: Collaborate with the PCB manufacturer and assembly team to ensure proper implementation of thermal management features, such as thermal vias, copper pour, and heat sink attachment.
By addressing these considerations throughout the PCB design process, engineers can create boards with lower thermal resistance and improved heat dissipation capabilities, ultimately leading to more reliable and high-performing electronic devices.
Conclusion
PCB thermal resistance is a critical factor in the performance and reliability of electronic devices. By understanding the concepts of thermal resistance, thermal conductivity, and heat transfer, designers can make informed decisions when selecting materials, designing layer stack-ups, and implementing thermal management techniques.
Through the use of analytical calculations, FEA simulations, and experimental measurements, engineers can quantify and optimize the thermal resistance of PCBs. This, combined with proper component placement, copper pour, thermal vias, and external cooling solutions, enables the creation of PCBs that effectively dissipate heat and maintain optimal operating temperatures.
As electronic devices continue to push the boundaries of performance and miniaturization, effective thermal management will remain a key priority in PCB design. By staying up-to-date with the latest materials, techniques, and tools, engineers can overcome thermal challenges and deliver innovative, reliable, and high-performing electronic solutions.
Frequently Asked Questions (FAQ)
- What is PCB thermal resistance, and why is it important?
PCB thermal resistance is a measure of a PCB’s ability to dissipate heat from its components to the surrounding environment. It is important because high thermal resistance can lead to component overheating, reduced performance, and decreased reliability in electronic devices.
- What factors influence a PCB’s thermal resistance?
Several factors influence a PCB’s thermal resistance, including the thermal conductivity of the materials used (substrate, copper, etc.), board thickness, copper thickness and coverage, component placement, and the presence of thermal vias.
- How can thermal vias help in reducing PCB thermal resistance?
Thermal vias are conductive pathways that run through the PCB, connecting different layers and allowing heat to transfer between them. They help reduce thermal resistance by providing efficient heat transfer paths from inner layers to outer layers and eventually to heat sinks or the surrounding environment.
- What are some common thermal management techniques used in PCB design?
Common thermal management techniques in PCB design include:
– Proper component placement and spacing
– Increasing copper pour and using thermal planes
– Employing thermal interface materials (TIMs) between components and heat sinks
– Using external cooling solutions, such as heat sinks, fans, and liquid cooling systems
- What should designers consider when creating a PCB with thermal management in mind?
When designing a PCB with thermal management in mind, designers should consider factors such as power dissipation estimation, material selection, layer stack-up optimization, strategic via placement and design, component placement and routing, thermal simulation and analysis, and manufacturing and assembly considerations. By addressing these factors, designers can create PCBs with lower thermal resistance and improved heat dissipation capabilities.
Leave a Reply