What is PCB Thermal Conductivity?
PCB (Printed Circuit Board) thermal conductivity refers to the ability of a PCB material to conduct heat. It is a measure of how efficiently heat can transfer through the PCB, from the heat-generating components to the surrounding environment or heat sinks. Thermal conductivity is typically expressed in watts per meter-kelvin (W/mK).
The thermal conductivity of a PCB is dependent on several factors, including:
- The base material of the PCB (e.g., FR-4, polyimide, ceramic)
- The thickness of the copper layers
- The presence of thermal vias or heat spreaders
- The layout and design of the PCB
Common PCB Base Materials and Their Thermal Conductivity
Material | Thermal Conductivity (W/mK) |
---|---|
FR-4 | 0.3 – 0.4 |
Polyimide | 0.2 – 0.3 |
Alumina (Ceramic) | 20 – 30 |
Aluminum | 150 – 200 |
Why is PCB Thermal Conductivity Important?
PCB thermal conductivity plays a crucial role in the reliability, performance, and longevity of electronic devices. Here are some key reasons why it is important:
1. Preventing Component Overheating
Electronic components generate heat during operation, and if this heat is not efficiently dissipated, it can lead to component overheating. Overheating can cause a variety of issues, such as:
- Reduced component lifespan
- Decreased performance
- Intermittent failures
- Complete device failure
A PCB with high thermal conductivity allows heat to be quickly transferred away from the components, helping to maintain safe operating temperatures.
2. Improving Device Reliability
By preventing component overheating, a PCB with good thermal conductivity contributes to the overall reliability of the electronic device. When components operate within their specified temperature ranges, they are less likely to experience failures or malfunctions, resulting in a more dependable product.
3. Enabling High-Power Applications
In high-power applications, such as power electronics or high-performance computing, components can generate significant amounts of heat. A PCB with high thermal conductivity is essential in these cases to ensure that the heat can be effectively dissipated, allowing the components to operate at their full potential without the risk of thermal damage.
4. Facilitating Compact Designs
As electronic devices become smaller and more compact, the challenge of managing heat becomes more critical. A PCB with good thermal conductivity allows for more efficient heat dissipation in a smaller form factor, enabling the development of compact, high-performance devices.
Strategies for Improving PCB Thermal Conductivity
There are several strategies that can be employed to improve the thermal conductivity of a PCB:
1. Choosing High Thermal Conductivity Base Materials
One of the most effective ways to improve PCB thermal conductivity is to select a base material with inherently high thermal conductivity. Some examples include:
-
Aluminum-based PCBs: These PCBs use an aluminum substrate, which has a thermal conductivity of 150-200 W/mK, significantly higher than traditional FR-4 material.
-
Ceramic-based PCBs: Ceramic materials, such as alumina, have thermal conductivities in the range of 20-30 W/mK, making them suitable for high-power applications.
-
Metal Core PCBs: These PCBs feature a metal core, typically aluminum, which acts as a heat spreader, improving thermal conductivity.
2. Increasing Copper Thickness
Copper is an excellent thermal conductor, with a thermal conductivity of around 400 W/mK. Increasing the thickness of the copper layers on a PCB can help to improve its overall thermal conductivity. This can be achieved by using thicker copper foils during the PCB manufacturing process or by using additional copper layers.
3. Incorporating Thermal Vias
Thermal vias are small, plated holes that are strategically placed on a PCB to provide a low-resistance thermal path between the heat-generating components and the heat sinks or other cooling solutions. By allowing heat to flow more easily through the PCB, thermal vias can significantly improve the overall thermal conductivity of the board.
4. Optimizing PCB Layout and Design
The layout and design of a PCB can also have a significant impact on its thermal conductivity. Some strategies for optimizing PCB layout for thermal performance include:
- Placing high-power components near the edge of the board, where they can be more easily cooled
- Providing adequate spacing between components to allow for better airflow
- Using large, uninterrupted copper areas (known as “copper pours”) to help spread heat evenly across the board
- Strategically placing thermal vias near high-power components
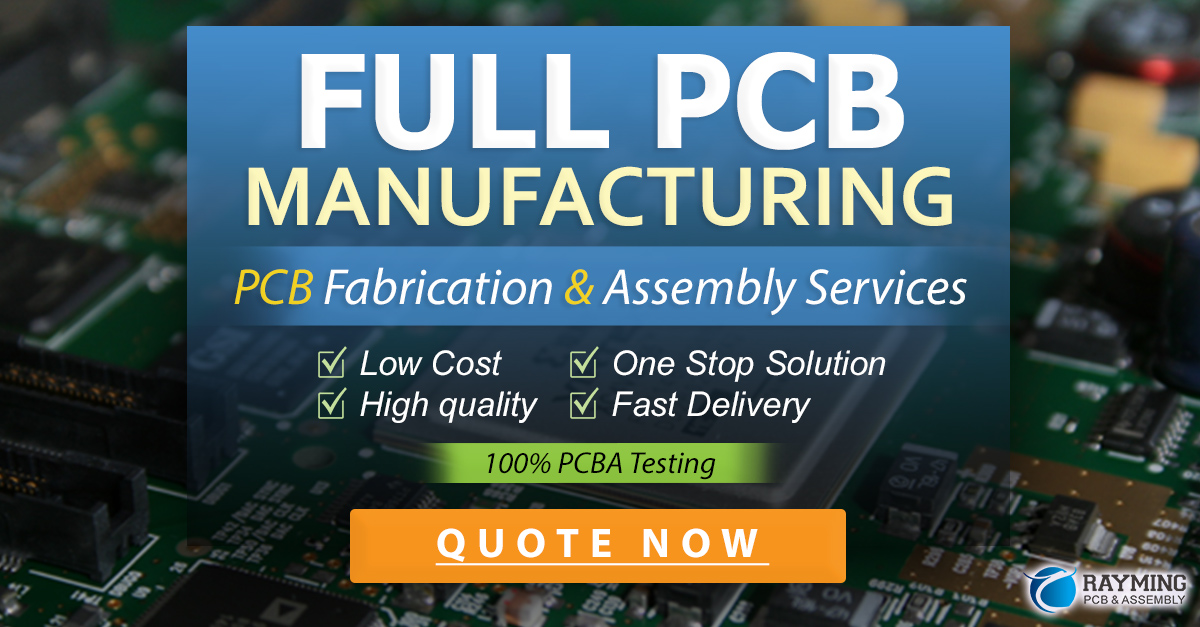
Real-World Applications
PCB thermal conductivity is a critical consideration in a wide range of electronic applications, from consumer devices to industrial equipment. Some examples include:
1. Smartphones and Tablets
Modern smartphones and tablets are packed with high-performance components, such as powerful processors and high-resolution displays, which generate significant amounts of heat. To ensure reliable operation and prevent thermal throttling, these devices often employ PCBs with high thermal conductivity, along with other cooling solutions like heat pipes and thermal interface materials.
2. Power Electronics
In power electronic applications, such as inverters, converters, and motor drives, PCBs must handle high currents and voltages, which can lead to substantial heat generation. Using PCBs with high thermal conductivity, along with appropriate cooling solutions, is essential for ensuring the reliability and longevity of these systems.
3. Automotive Electronics
The harsh operating environment in automotive applications, combined with the increasing complexity of electronic systems in modern vehicles, makes PCB thermal conductivity a critical consideration. Automotive PCBs must be able to withstand high temperatures and efficiently dissipate heat to ensure reliable operation over the vehicle’s lifespan.
4. Aerospace and Defense
In aerospace and defense applications, electronic systems must often operate in extreme environments, including high temperatures and high altitudes. PCBs with high thermal conductivity are essential for ensuring that these systems can perform reliably under these challenging conditions.
Frequently Asked Questions (FAQ)
- Q: What is the difference between thermal conductivity and thermal resistance?
A: Thermal conductivity is a material property that describes how well a material conducts heat, while thermal resistance is a measure of how much a material resists the flow of heat. In general, materials with high thermal conductivity will have low thermal resistance, and vice versa.
- Q: Can I use thermal interface materials to improve PCB thermal conductivity?
A: Thermal interface materials (TIMs), such as thermal greases, pads, and adhesives, are primarily used to improve the thermal contact between a component and a heat sink. While they do not directly affect the thermal conductivity of the PCB itself, they can help to improve overall heat transfer from the components to the cooling solution.
- Q: How do I choose the right base material for my PCB based on thermal conductivity requirements?
A: The choice of base material depends on several factors, including the power requirements of the components, the operating environment, and the overall design constraints. In general, for high-power applications or environments with high ambient temperatures, materials with higher thermal conductivity, such as aluminum or ceramic-based PCBs, may be necessary. For less demanding applications, standard FR-4 material may be sufficient.
- Q: Can I use software to simulate the thermal performance of my PCB design?
A: Yes, there are various software tools available that can help you simulate the thermal performance of your PCB design. These tools, such as Ansys Icepak or Mentor Graphics FloTHERM, allow you to model the heat generation and dissipation in your PCB, helping you to identify potential thermal issues and optimize your design for better thermal performance.
- Q: How do I determine the thermal conductivity of a PCB material?
A: The thermal conductivity of a PCB material is typically provided by the manufacturer in the material’s datasheet. If this information is not readily available, you can also find general thermal conductivity values for common PCB materials in various online resources and engineering handbooks. In some cases, you may need to perform your own tests or consult with a material science expert to determine the thermal conductivity of a specific material.
Conclusion
PCB thermal conductivity is a critical factor in the design and performance of electronic devices. By understanding the importance of thermal conductivity and employing strategies to improve it, engineers can design PCBs that efficiently dissipate heat, ensuring reliable operation and long-term durability. As electronic systems continue to become more complex and power-dense, the role of PCB thermal conductivity will only become more important in enabling the development of advanced, high-performance devices.
Leave a Reply