What is a PCB Substrate?
A PCB (Printed Circuit Board) substrate is the foundation material on which the electronic components and circuitry are mounted and interconnected. It is a critical component of any PCB, as it provides the mechanical support and electrical insulation necessary for the proper functioning of the board. The substrate material chosen for a PCB can significantly impact its performance, reliability, and cost.
Common PCB Substrate Materials
There are several materials commonly used as PCB substrates, each with its own unique properties and advantages. Some of the most popular PCB substrate materials include:
-
FR-4: A composite material made of woven fiberglass cloth and epoxy resin, FR-4 is the most widely used PCB substrate. It offers good mechanical strength, electrical insulation, and thermal stability.
-
Polyimide: Known for its excellent thermal resistance and flexibility, polyimide is often used in high-temperature applications or flexible PCBs.
-
Aluminum: Metal-Core PCBs, particularly those using aluminum substrates, are used in applications requiring efficient heat dissipation, such as high-power LED lighting or power electronics.
-
Ceramic: Ceramic substrates, such as alumina or beryllia, are used in high-frequency and high-power applications due to their excellent thermal conductivity and low dielectric loss.
Material | Dielectric Constant | Thermal Conductivity (W/mK) | Tg (°C) | CTE (ppm/°C) |
---|---|---|---|---|
FR-4 | 4.3-4.8 | 0.3-0.4 | 130-140 | 12-16 |
Polyimide | 3.4-3.5 | 0.2-0.3 | 250-400 | 12-60 |
Aluminum | – | 150-200 | – | 23-24 |
Alumina | 9.8-10.1 | 20-30 | – | 6-8 |
Tg: Glass transition temperature, CTE: Coefficient of thermal expansion
Factors to Consider When Choosing a PCB Substrate
When selecting a PCB substrate material, several factors should be taken into account to ensure the best performance and reliability for your application:
Electrical Properties
-
Dielectric Constant: The dielectric constant of the substrate material affects the signal propagation speed and impedance of the PCB traces. A lower dielectric constant is generally preferred for high-frequency applications.
-
Loss Tangent: The loss tangent is a measure of the energy dissipation in the substrate material. A lower loss tangent is desirable to minimize signal attenuation and maintain signal integrity.
Thermal Properties
-
Thermal Conductivity: The thermal conductivity of the substrate material determines its ability to dissipate heat generated by the components on the PCB. Higher thermal conductivity is essential for applications with high power densities or operating in high-temperature environments.
-
Coefficient of Thermal Expansion (CTE): The CTE of the substrate should be closely matched to that of the components and materials used on the PCB to minimize stress and prevent failures caused by thermal expansion mismatches.
Mechanical Properties
-
Strength and Stiffness: The substrate material should provide sufficient mechanical support for the components and withstand the stresses encountered during manufacturing, assembly, and operation.
-
Flexibility: For applications requiring flexible PCBs, the substrate material must be able to withstand repeated bending and flexing without cracking or losing its electrical properties.
Cost and Availability
The cost and availability of the substrate material should also be considered, as they can impact the overall project budget and lead times. FR-4 is generally the most cost-effective and readily available option, while specialty materials like polyimide or ceramic can be more expensive and have longer lead times.
PCB Substrate Selection Process
To select the most appropriate PCB substrate for your application, follow these steps:
-
Define the application requirements, including the operating environment, electrical performance, thermal management needs, and mechanical constraints.
-
Evaluate the electrical, thermal, and mechanical properties of the available substrate materials against your application requirements.
-
Consider the cost and availability of the substrate materials that meet your technical requirements.
-
Consult with your PCB manufacturer or material suppliers to discuss your specific needs and obtain recommendations based on their expertise and experience.
-
If necessary, conduct prototyping and testing to validate the performance of the chosen substrate material in your application.
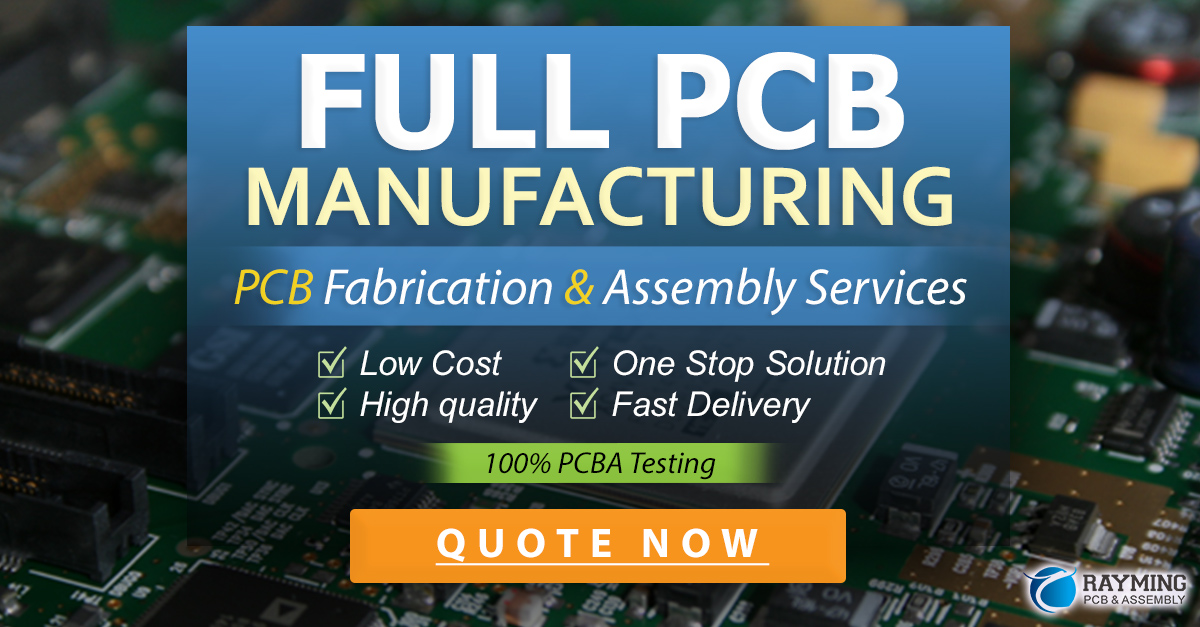
FAQ
Q1: What is the most common PCB substrate material?
A1: FR-4, a composite material made of woven fiberglass cloth and epoxy resin, is the most widely used PCB substrate material due to its good balance of mechanical, electrical, and thermal properties, as well as its cost-effectiveness and availability.
Q2: What are the advantages of using a metal-core PCB substrate?
A2: Metal-core PCB substrates, such as those made of aluminum, offer excellent thermal conductivity, which makes them ideal for applications that require efficient heat dissipation. This is particularly important in high-power applications like LED lighting or power electronics, where heat management is critical for ensuring reliable operation and long service life.
Q3: What factors should I consider when choosing a PCB substrate for high-frequency applications?
A3: When selecting a PCB substrate for high-frequency applications, it is essential to consider the electrical properties of the material, particularly the dielectric constant and loss tangent. A lower dielectric constant helps to maintain signal integrity by reducing signal propagation delays and impedance mismatches. A low loss tangent minimizes signal attenuation, which is crucial for maintaining signal quality in high-frequency applications.
Q4: How does the coefficient of thermal expansion (CTE) impact PCB reliability?
A4: The CTE of the PCB substrate should be closely matched to that of the components and materials used on the board. A significant mismatch in CTE can lead to mechanical stress and strain during thermal cycling, which can cause component failures, solder joint cracking, or delamination of the PCB Layers. By selecting a substrate material with a CTE that closely matches the other materials on the board, you can minimize these thermal expansion-related issues and improve the overall reliability of the PCB.
Q5: Are there any special considerations for choosing a substrate for flexible PCBs?
A5: When selecting a substrate material for flexible PCBs, it is crucial to consider the mechanical properties of the material, particularly its flexibility and ability to withstand repeated bending and flexing. Polyimide is a common choice for flexible PCBs due to its excellent flexibility and thermal resistance. Additionally, the thickness of the substrate material should be carefully chosen to ensure the desired level of flexibility while maintaining the necessary electrical and mechanical properties.
Conclusion
Selecting the appropriate PCB substrate is crucial for ensuring the performance, reliability, and cost-effectiveness of your electronic devices. By understanding the key properties of common substrate materials and considering the specific requirements of your application, you can make an informed decision when choosing a PCB substrate. Factors such as electrical properties, thermal management, mechanical stability, and cost should all be taken into account during the selection process. Consulting with experienced PCB Manufacturers and material suppliers can provide valuable insights and guidance to help you find the best substrate solution for your project.
Leave a Reply