What is a PCB Stencil?
A PCB (Printed Circuit Board) stencil is a thin sheet of material, typically stainless steel or polyester, with precise openings that correspond to the pads on a PCB. The stencil is used to apply solder paste onto the PCB pads before component placement and soldering. This process ensures precise and consistent solder paste application, which is crucial for achieving reliable solder joints and high-quality PCB Assembly.
Benefits of Using PCB Stencils
Using PCB stencils offers several advantages in the PCB assembly process:
- Precision: Stencils allow for accurate and consistent solder paste application, ensuring the right amount of paste is deposited on each pad.
- Efficiency: Stencil printing is a fast and efficient method for applying solder paste to multiple PCBs simultaneously.
- Repeatability: Stencils provide consistent results across multiple PCBs, reducing variations and improving overall quality.
- Cost-effectiveness: Using stencils reduces solder paste waste and minimizes the need for rework, resulting in cost savings.
Types of PCB Stencils
There are several types of PCB stencils available, each with its own characteristics and applications. The most common types include:
1. Stainless Steel Stencils
Stainless steel stencils are the most widely used type in PCB assembly. They are durable, long-lasting, and suitable for high-volume production. Stainless steel stencils are typically laser-cut or chemically etched to create precise openings for solder paste application.
Advantages of Stainless Steel Stencils
- High durability and long lifespan
- Excellent precision and repeatability
- Suitable for high-volume production
- Resistant to wear and tear
- Easy to clean and maintain
Disadvantages of Stainless Steel Stencils
- Higher initial cost compared to other materials
- Not suitable for low-volume or prototype production
- Requires proper storage to prevent damage
2. Polyester Stencils
Polyester stencils, also known as mesh stencils, are made from a thin, flexible polyester material. They are commonly used for low-volume production, prototyping, and quick turnaround projects. Polyester stencils are created using a high-resolution printing process, which allows for fine detail and complex patterns.
Advantages of Polyester Stencils
- Lower cost compared to stainless steel stencils
- Suitable for low-volume production and prototyping
- Quick turnaround time
- Flexibility allows for conformity to uneven surfaces
- Ideal for applying solder paste to small, fine-pitch components
Disadvantages of Polyester Stencils
- Lower durability compared to stainless steel stencils
- Not suitable for high-volume production
- May stretch or deform over time
- Requires careful handling and storage
3. Electroformed Nickel Stencils
Electroformed nickel stencils are created using an electroplating process, where nickel is deposited onto a mandrel with the desired stencil pattern. These stencils offer high precision and are suitable for applications requiring fine details and tight tolerances.
Advantages of Electroformed Nickel Stencils
- Excellent precision and detail
- Smooth surface finish
- Suitable for fine-pitch components and high-density PCBs
- Durable and long-lasting
Disadvantages of Electroformed Nickel Stencils
- Higher cost compared to other stencil types
- Longer lead time for manufacturing
- Not suitable for large-volume production
4. Framed Stencils
Framed stencils consist of a stencil material (stainless steel or polyester) mounted on a rigid frame. The frame provides stability and prevents the stencil from warping or deforming during use. Framed stencils are commonly used in manual or semi-automated solder paste application processes.
Advantages of Framed Stencils
- Improved stability and rigidity
- Easier to handle and align with PCBs
- Suitable for manual or semi-automated processes
- Reduces stencil warping and deformation
Disadvantages of Framed Stencils
- Increased cost due to the additional framing material
- Larger storage space required
- Limited flexibility for conforming to uneven surfaces
5. Stepped Stencils
Stepped stencils, also known as multi-level stencils, have varying thicknesses across different areas of the stencil. This allows for different solder paste deposit volumes on specific components or regions of the PCB. Stepped stencils are useful for PCBs with components of varying heights or when different solder paste volumes are required.
Advantages of Stepped Stencils
- Allows for different solder paste deposit volumes on a single PCB
- Accommodates components with varying heights
- Improves solder joint reliability for specific components
- Reduces the need for multiple stencils
Disadvantages of Stepped Stencils
- Higher manufacturing cost compared to standard stencils
- Increased complexity in stencil design and fabrication
- Requires precise alignment during solder paste application
Factors to Consider When Choosing a PCB Stencil
When selecting a PCB stencil, several factors should be considered to ensure optimal results:
1. Material
The choice of stencil material depends on factors such as production volume, budget, and required precision. Stainless steel stencils are ideal for high-volume production and durability, while polyester stencils are suitable for low-volume or prototype work.
2. Thickness
Stencil thickness affects the amount of solder paste deposited on the PCB pads. Thicker stencils deposit more paste, while thinner stencils deposit less. The optimal thickness depends on the component sizes, pad dimensions, and desired solder joint profiles.
Stencil Thickness | Typical Application |
---|---|
0.1 mm | Very fine-pitch components (0.3 mm pitch or smaller) |
0.12 mm | Fine-pitch components (0.4 mm to 0.5 mm pitch) |
0.15 mm | Standard SMD components (0.5 mm pitch or larger) |
0.2 mm | Large components or high-volume solder paste deposit |
3. Aperture Size and Shape
The aperture size and shape of the stencil openings determine the amount and distribution of solder paste on the PCB pads. Aperture sizes should be optimized based on the pad dimensions and desired solder paste volume. Common aperture shapes include square, rectangular, and circular.
4. Aspect Ratio
The aspect ratio of a stencil aperture is the ratio of its width to its thickness. A higher aspect ratio (larger width compared to thickness) allows for better solder paste release and reduces the risk of clogging. However, too high an aspect ratio may compromise the structural integrity of the stencil.
5. Surface Finish
The surface finish of the stencil affects the release characteristics of the solder paste. A smooth, polished surface promotes better paste release and reduces the likelihood of clogging. Stainless steel stencils are often electropolished to achieve a smooth surface finish.
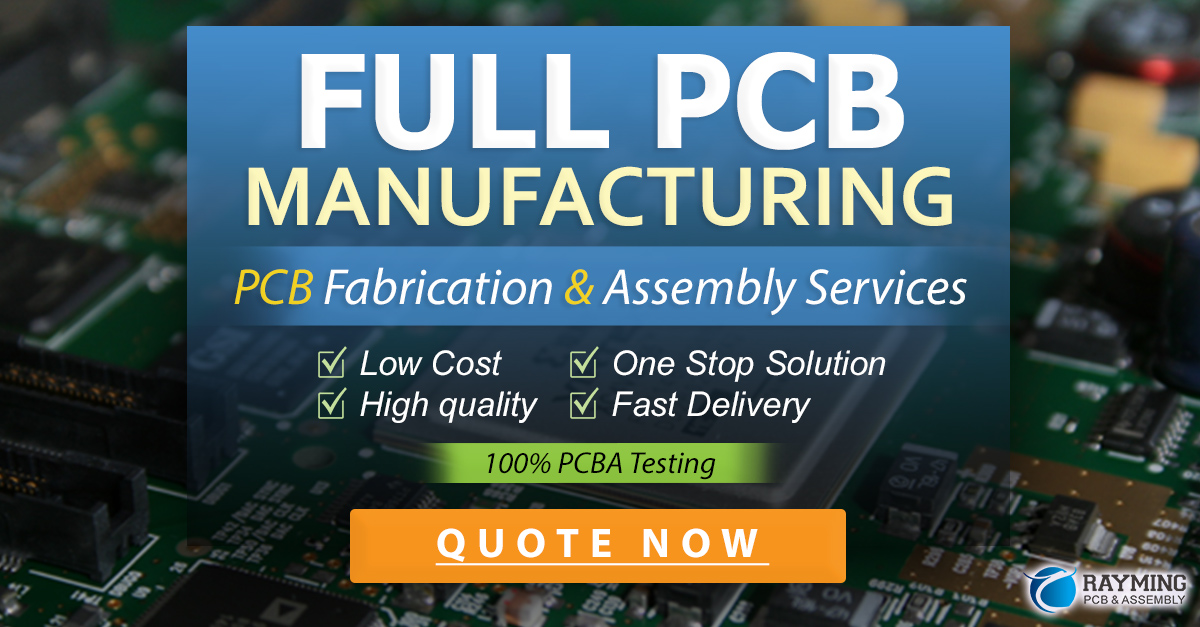
PCB Stencil Maintenance and Cleaning
Proper maintenance and cleaning of PCB stencils are essential for ensuring consistent performance and long-term durability. Regular cleaning prevents solder paste buildup, clogging, and contamination, which can affect the quality of the solder paste deposits.
Cleaning Methods
- Manual Cleaning: Manual cleaning involves using solvents and wiping the stencil with a lint-free cloth or brush. This method is suitable for small-scale production or quick cleaning between prints.
- Ultrasonic Cleaning: Ultrasonic cleaning uses high-frequency sound waves to agitate a cleaning solution, effectively removing solder paste residue and contamination from the stencil. This method is more thorough and efficient than manual cleaning.
- Automated Cleaning: Automated stencil cleaning systems use a combination of solvents, brushes, and air knives to clean the stencil. These systems are designed for high-volume production and provide consistent cleaning results.
Cleaning Frequency
The frequency of stencil cleaning depends on factors such as production volume, solder paste type, and environmental conditions. As a general guideline:
- Clean the stencil after every print cycle for high-volume production
- Clean the stencil every few print cycles for low-volume production
- Clean the stencil whenever there are signs of solder paste buildup or contamination
Storage and Handling
Proper storage and handling of PCB stencils are crucial for maintaining their quality and longevity:
- Store stencils in a clean, dry environment
- Use protective covers or containers to prevent damage and contamination
- Handle stencils with care to avoid bending, warping, or scratching
- Use gloves when handling stencils to prevent skin oils and contamination
Frequently Asked Questions (FAQ)
1. How do I choose the right stencil thickness for my PCB?
The choice of stencil thickness depends on factors such as component size, pad dimensions, and desired solder paste volume. As a general rule, use thinner stencils (0.1 mm to 0.12 mm) for fine-pitch components and thicker stencils (0.15 mm to 0.2 mm) for larger components or higher solder paste volumes. It’s important to consult with your PCB assembly provider or stencil manufacturer for specific recommendations based on your PCB design.
2. Can I reuse a PCB stencil?
Yes, PCB stencils can be reused multiple times with proper cleaning and maintenance. Regular cleaning removes solder paste buildup and contamination, ensuring consistent performance across multiple print cycles. However, stencils will eventually wear out and need to be replaced to maintain print quality.
3. How often should I replace my PCB stencil?
The lifespan of a PCB stencil depends on factors such as the stencil material, usage frequency, and maintenance practices. Stainless steel stencils generally have a longer lifespan compared to polyester stencils. As a general guideline, replace your stencil when you notice signs of wear, damage, or consistent print quality issues that cannot be resolved with cleaning or adjustments.
4. Can I use the same stencil for different PCB designs?
A stencil is specific to a particular PCB design, as the aperture sizes and locations are tailored to match the pads on the PCB. Using the same stencil for different PCB designs may result in incorrect solder paste placement and compromised solder joint quality. It’s recommended to use a dedicated stencil for each unique PCB design.
5. How do I store my PCB stencils when not in use?
To ensure the longevity and quality of your PCB stencils, store them in a clean, dry environment. Use protective covers or containers to prevent damage and contamination. Avoid storing stencils in areas with high humidity or extreme temperatures, as this can cause warping or corrosion. Handle stencils with care and use gloves to prevent skin oils and contamination.
Conclusion
Selecting the appropriate PCB stencil is crucial for achieving high-quality solder paste application and reliable PCB assembly. Understanding the different stencil types, materials, and factors to consider when choosing a stencil will help you make informed decisions based on your specific PCB assembly requirements.
Regular maintenance, cleaning, and proper storage of PCB stencils are essential for ensuring consistent performance and long-term durability. By following best practices and working closely with your PCB assembly provider or stencil manufacturer, you can optimize your solder paste application process and achieve high-quality PCB assembly results.
As PCB designs continue to evolve with smaller components and higher densities, the importance of selecting the right PCB stencil becomes even more critical. By staying informed about the latest stencil technologies and best practices, you can adapt to these changes and maintain a competitive edge in PCB assembly.
Leave a Reply