Introduction to PCB Soldering
PCB soldering is a critical process in the manufacturing of electronic devices. It involves joining electronic components to a printed circuit board (PCB) using solder, a metal alloy that melts at a relatively low temperature. Proper PCB soldering ensures the reliability and functionality of the electronic device, while poor soldering can lead to malfunctions, short circuits, and even device failure.
In this ultimate guide, we will cover everything you need to know about PCB soldering, from the basics of soldering to advanced techniques and troubleshooting tips.
What is PCB Soldering?
PCB soldering is the process of joining electronic components to a PCB using solder. The solder is melted and then cooled to create a permanent electrical and mechanical connection between the component and the PCB. There are two main types of PCB soldering: through-hole soldering and surface-mount soldering.
Through-Hole Soldering
Through-hole soldering involves inserting the leads of a component through holes drilled in the PCB and soldering them to pads on the opposite side of the board. This type of soldering is typically used for larger components, such as capacitors, resistors, and connectors.
Surface-Mount Soldering
Surface-mount soldering involves soldering components directly to pads on the surface of the PCB. This type of soldering is typically used for smaller components, such as integrated circuits (ICs) and surface-mount devices (SMDs).
Tools and Equipment for PCB Soldering
To perform PCB soldering, you will need the following tools and equipment:
- Soldering iron
- Solder
- Flux
- Tweezers
- Wire cutters
- Solder wick
- Solder sucker
- Magnifying glass
- ESD-safe workstation
Soldering Iron
A soldering iron is the most essential tool for PCB soldering. It consists of a heated metal tip that is used to melt the solder and create the connection between the component and the PCB. When choosing a soldering iron, consider the following factors:
- Wattage: A higher wattage soldering iron will heat up faster and maintain its temperature better, but it may be more difficult to control for precise work.
- Temperature control: Some soldering irons have adjustable temperature controls, which can be useful for working with different types of solder and components.
- Tip size and shape: The size and shape of the soldering iron tip will affect the precision and accuracy of your soldering. Choose a tip that is appropriate for the size of the components you will be working with.
Solder
Solder is a metal alloy that is used to create the electrical and mechanical connection between the component and the PCB. There are two main types of solder: lead-based and lead-free.
- Lead-based solder: Lead-based solder is easier to work with and has a lower melting point than lead-free solder. However, it is toxic and has been banned in many countries due to environmental and health concerns.
- Lead-free solder: Lead-free solder is more environmentally friendly and safer to use, but it has a higher melting point and can be more difficult to work with.
When choosing solder, consider the following factors:
- Alloy composition: Different solder alloys have different melting points, wetting properties, and mechanical strengths. Choose an alloy that is appropriate for your application.
- Diameter: Solder comes in different diameters, typically ranging from 0.5mm to 1.5mm. Choose a diameter that is appropriate for the size of the components and the PCB pads.
- Flux core: Some solder comes with a flux core, which helps to remove oxides and improve the wetting of the solder. Choose a solder with a flux core that is appropriate for your application.
Flux
Flux is a chemical that is used to remove oxides from the surface of the PCB and the component leads, and to improve the wetting of the solder. There are three main types of flux: rosin, water-soluble, and no-clean.
- Rosin flux: Rosin flux is the most common type of flux used in PCB soldering. It is easy to use and provides good wetting and oxide removal. However, it leaves a sticky residue that must be cleaned after soldering.
- Water-soluble flux: Water-soluble flux is easier to clean than rosin flux, but it is more corrosive and can cause damage to the PCB and components if not cleaned properly.
- No-clean flux: No-clean flux is designed to leave minimal residue and does not require cleaning after soldering. However, it may not provide as good wetting and oxide removal as other types of flux.
When choosing flux, consider the following factors:
- Activity level: Flux comes in different activity levels, ranging from low to high. Higher activity fluxes provide better oxide removal and wetting, but they also leave more residue and require more cleaning.
- Compatibility: Make sure the flux is compatible with the solder and the components you are using. Some fluxes may not be suitable for certain types of components or finishes.
- Application method: Flux can be applied using a brush, pen, syringe, or spray. Choose an application method that is appropriate for your soldering setup and the size of the components.
Other Tools and Equipment
In addition to the soldering iron, solder, and flux, there are several other tools and equipment that can be useful for PCB soldering:
- Tweezers: Tweezers are used for handling small components and positioning them on the PCB.
- Wire cutters: Wire cutters are used for trimming the leads of through-hole components after soldering.
- Solder wick: Solder wick is a braided wire that is used for removing excess solder from the PCB.
- Solder sucker: A solder sucker is a vacuum tool that is used for removing solder from through-hole components.
- Magnifying glass: A magnifying glass can be helpful for inspecting solder joints and identifying defects.
- ESD-safe workstation: An ESD-safe workstation is essential for preventing electrostatic discharge (ESD) damage to sensitive components.
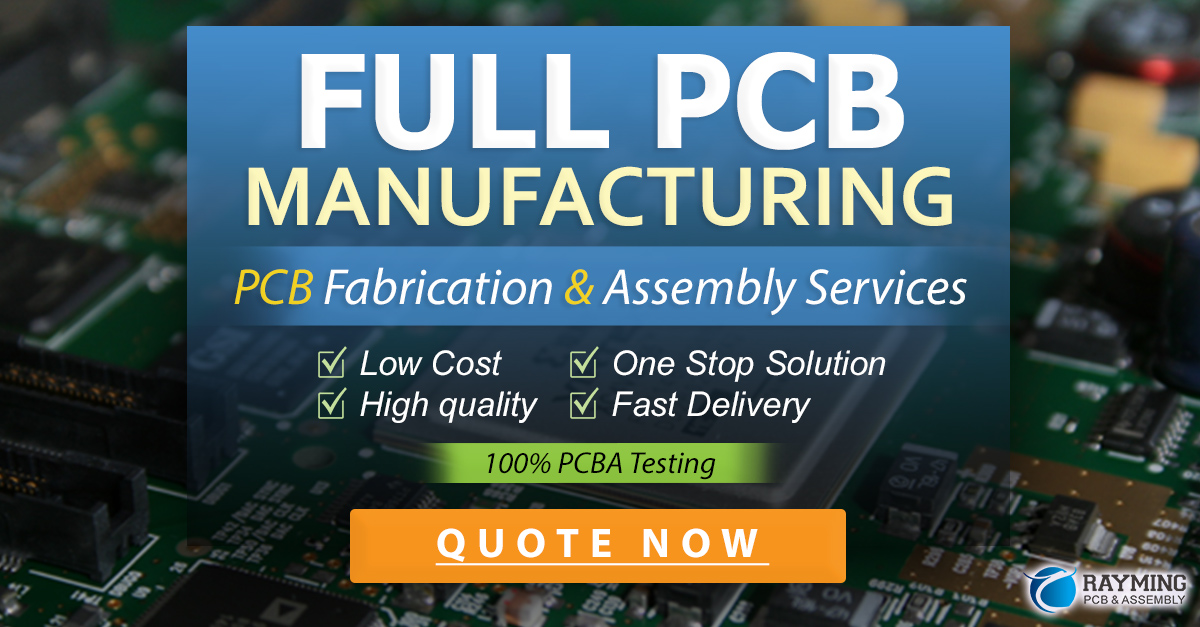
PCB Soldering Techniques
There are several techniques that can be used for PCB soldering, depending on the type of components and the soldering setup. Here are some of the most common techniques:
Through-Hole Soldering
- Insert the component leads through the holes in the PCB.
- Bend the leads outward slightly to hold the component in place.
- Apply flux to the component leads and the PCB pads.
- Touch the soldering iron tip to the component lead and the PCB pad simultaneously.
- Feed solder into the joint until it forms a concave fillet around the lead and the pad.
- Remove the soldering iron and allow the joint to cool.
- Trim the excess lead length with wire cutters.
Surface-Mount Soldering
- Apply solder paste to the PCB pads using a stencil or syringe.
- Place the surface-mount component on the pads using tweezers.
- Reflow the solder paste using a hot air gun or reflow oven.
- Inspect the solder joints for defects and rework if necessary.
Drag Soldering
Drag soldering is a technique used for soldering multiple surface-mount components in a row. Here’s how it works:
- Apply solder paste to the PCB pads using a stencil or syringe.
- Place the surface-mount components on the pads using tweezers.
- Touch the soldering iron tip to the first component lead and drag it across the leads of the other components in the row.
- Feed solder into the joints as you drag the iron across the leads.
- Remove the soldering iron and allow the joints to cool.
- Inspect the solder joints for defects and rework if necessary.
Rework and Repair
Sometimes, solder joints may need to be reworked or repaired due to defects or damage. Here are some techniques for reworking and repairing solder joints:
- Desoldering: To remove a component from the PCB, use a solder sucker or solder wick to remove the solder from the joints. Then, use tweezers to remove the component from the board.
- Resoldering: To resolder a joint, apply flux to the joint and touch the soldering iron tip to the joint to melt the solder. Feed additional solder into the joint if necessary, and remove the iron to allow the joint to cool.
- Jumper wire: If a trace on the PCB is damaged, you can use a jumper wire to bypass the damaged section and restore connectivity.
Common PCB Soldering Defects and How to Avoid Them
PCB soldering defects can cause reliability issues and even device failure. Here are some of the most common PCB soldering defects and how to avoid them:
Cold Joints
Cold joints occur when the solder does not melt completely and form a proper bond with the component lead and PCB pad. Cold joints can cause intermittent connections and even device failure. To avoid cold joints:
- Make sure the soldering iron is hot enough to melt the solder completely.
- Apply enough heat to the joint to allow the solder to flow properly.
- Use fresh solder and clean the soldering iron tip regularly.
Bridges
Bridges occur when solder inadvertently connects two adjacent pads or traces on the PCB. Bridges can cause short circuits and damage to the components. To avoid bridges:
- Use a fine-tipped soldering iron and apply solder carefully to avoid accidentally touching adjacent pads or traces.
- Use solder wick or a solder sucker to remove excess solder from the joint.
- Inspect the solder joints carefully for bridges and remove them if necessary.
Tombstoning
Tombstoning occurs when a surface-mount component stands up on one end due to uneven heating or poor solder paste application. Tombstoning can cause open circuits and affect the reliability of the device. To avoid tombstoning:
- Apply solder paste evenly to both pads.
- Use a reflow oven or hot air gun to heat the component evenly on both sides.
- Make sure the component is seated properly on the pads before reflowing the solder.
Insufficient Wetting
Insufficient wetting occurs when the solder does not flow properly onto the component lead or PCB pad, resulting in a weak or incomplete bond. Insufficient wetting can cause intermittent connections and reduce the reliability of the device. To avoid insufficient wetting:
- Use fresh solder and clean the soldering iron tip regularly.
- Apply enough heat to the joint to allow the solder to flow properly.
- Use flux to improve the wetting of the solder and remove oxides from the surfaces.
Excess Solder
Excess solder can cause bridges, short circuits, and affect the mechanical strength of the joint. To avoid excess solder:
- Use a fine-tipped soldering iron and apply solder carefully to avoid applying too much.
- Use solder wick or a solder sucker to remove excess solder from the joint.
- Inspect the solder joints carefully for excess solder and remove it if necessary.
PCB Soldering Safety and Best Practices
PCB soldering involves working with hot tools and chemicals, so it’s important to follow safety and best practices to avoid injury and ensure the quality of the solder joints. Here are some safety and best practices to keep in mind:
- Wear safety glasses to protect your eyes from solder splashes and fumes.
- Work in a well-ventilated area to avoid inhaling solder fumes.
- Use a fume extractor or fan to remove solder fumes from the work area.
- Wear gloves to protect your hands from hot tools and chemicals.
- Use an ESD-safe workstation to prevent electrostatic discharge damage to sensitive components.
- Keep the soldering iron in a stand when not in use to avoid accidental burns.
- Clean the soldering iron tip regularly to remove oxide buildup and ensure good heat transfer.
- Use fresh solder and flux to ensure good wetting and strong solder joints.
- Inspect the solder joints carefully for defects and rework if necessary.
- Follow the manufacturer’s instructions for the soldering iron, solder, and flux.
FAQs
1. What is the difference between lead-based and lead-free solder?
Lead-based solder contains lead, while lead-free solder does not. Lead-based solder is easier to work with and has a lower melting point, but it is toxic and has been banned in many countries due to environmental and health concerns. Lead-free solder is more environmentally friendly and safer to use, but it has a higher melting point and can be more difficult to work with.
2. How do I choose the right soldering iron for my project?
When choosing a soldering iron, consider the following factors:
- Wattage: A higher wattage soldering iron will heat up faster and maintain its temperature better, but it may be more difficult to control for precise work.
- Temperature control: Some soldering irons have adjustable temperature controls, which can be useful for working with different types of solder and components.
- Tip size and shape: The size and shape of the soldering iron tip will affect the precision and accuracy of your soldering. Choose a tip that is appropriate for the size of the components you will be working with.
3. How do I prevent electrostatic discharge (ESD) damage to sensitive components?
To prevent ESD damage to sensitive components, use an ESD-safe workstation that includes an ESD mat, wrist strap, and grounding points. Make sure to wear the wrist strap and connect it to a grounding point before handling sensitive components.
4. How do I remove excess solder from a joint?
To remove excess solder from a joint, use solder wick or a solder sucker. Solder wick is a braided wire that is used to absorb excess solder when heated with a soldering iron. A solder sucker is a vacuum tool that is used to suck up molten solder from the joint.
5. How do I know if my solder joint is good?
A good solder joint should have a concave fillet that completely surrounds the component lead and PCB pad. The solder should be shiny and smooth, with no cracks, pits, or voids. The joint should also be mechanically strong and able to withstand stress and vibration.
Defect | Cause | Prevention |
---|---|---|
Cold joint | Insufficient heat, poor wetting | Use fresh solder, clean iron tip, apply enough heat |
Bridge | Excess solder, accidentally touching adjacent pads | Use fine-tipped iron, remove excess solder, inspect carefully |
Tombstoning | Uneven heating, poor paste application | Apply paste evenly, use reflow oven or hot air, seat component properly |
Insufficient wetting | Poor flux, oxide buildup, insufficient heat | Use fresh solder and flux, clean iron tip, apply enough heat |
Excess solder | Applying too much solder | Use fine-tipped iron, remove excess solder, inspect carefully |
Conclusion
PCB soldering is a critical process in the manufacturing of electronic devices. Proper soldering ensures the reliability and functionality of the device, while poor soldering can lead to malfunctions and even device failure. By understanding the basics of soldering, choosing the right tools and equipment, following proper techniques, and avoiding common defects, you can ensure high-quality solder joints and reliable electronic devices.
Remember to always prioritize safety and follow best practices when soldering, including wearing protective gear, working in a well-ventilated area, and using an ESD-safe workstation. With practice and attention to detail, you can master the art of PCB soldering and create high-quality electronic devices.
Leave a Reply