Introduction to PCB Material Selection
Printed Circuit Boards (PCBs) are the backbone of modern electronics, providing a platform for interconnecting and mounting electronic components. The choice of materials used in PCB fabrication plays a crucial role in determining the performance, reliability, and cost of the final product. PCB Services offer a wide range of material options to cater to the specific requirements of different applications. In this article, we will explore the various aspects of PCB material selection and how it impacts the PCB services provided.
Factors Influencing PCB Material Selection
When selecting materials for PCB fabrication, several key factors need to be considered:
Electrical Properties
The electrical properties of the PCB material are of utmost importance as they directly affect the signal integrity and performance of the circuit. Some key electrical properties to consider include:
- Dielectric Constant (Dk): The dielectric constant determines the speed of signal propagation and the impedance of the traces. Materials with lower Dk values are preferred for high-speed applications.
- Dissipation Factor (Df): The dissipation factor represents the energy loss in the material. Lower Df values are desirable to minimize signal attenuation and power loss.
- Insulation Resistance: The insulation resistance of the material should be high to prevent leakage currents and maintain signal integrity.
Thermal Properties
PCBs are subjected to various thermal stresses during operation, and the choice of material should ensure reliable performance under these conditions. Important thermal properties include:
- Glass Transition Temperature (Tg): The glass transition temperature indicates the point at which the material transitions from a rigid to a more flexible state. Higher Tg values are preferred for applications with high operating temperatures.
- Coefficient of Thermal Expansion (CTE): The CTE represents the material’s expansion rate with temperature changes. A close match between the CTE of the PCB material and the components is necessary to prevent thermal stresses and ensure reliability.
- Thermal Conductivity: Materials with higher thermal conductivity help dissipate heat more effectively, preventing hot spots and improving the overall thermal management of the PCB.
Mechanical Properties
The mechanical properties of the PCB material determine its ability to withstand physical stresses and maintain structural integrity. Key mechanical properties include:
- Flexural Strength: The flexural strength indicates the material’s ability to resist bending and maintain its shape under stress. Higher flexural strength is desirable for applications with mechanical stresses.
- Tensile Strength: The tensile strength represents the material’s ability to resist pulling forces. It is important for applications where the PCB may be subjected to stretching or pulling.
- Impact Resistance: Impact resistance is crucial for PCBs that may be exposed to shocks or impacts during handling or operation.
Environmental Factors
PCBs may be exposed to various environmental conditions, and the choice of material should ensure reliable performance under these conditions. Environmental factors to consider include:
- Temperature Range: The material should be able to withstand the expected temperature range of the application, including both low and high temperatures.
- Humidity Resistance: The material should have good moisture resistance to prevent degradation and maintain performance in humid environments.
- Chemical Resistance: In applications where the PCB may be exposed to chemicals or solvents, the material should have adequate chemical resistance to prevent damage.
Common PCB Materials and Their Properties
There are several commonly used PCB materials, each with its own set of properties and advantages. Let’s take a closer look at some of these materials:
FR-4
FR-4 is the most widely used PCB material, offering a good balance of electrical, thermal, and mechanical properties at a relatively low cost. It is a glass-reinforced epoxy laminate with the following properties:
Property | Value |
---|---|
Dielectric Constant (Dk) | 4.2 – 4.6 (at 1 MHz) |
Dissipation Factor (Df) | 0.02 (at 1 MHz) |
Glass Transition Temperature (Tg) | 130°C – 140°C |
Coefficient of Thermal Expansion (CTE) | 14-17 ppm/°C |
Thermal Conductivity | 0.3 W/m·K |
Flexural Strength | 415 MPa |
FR-4 is suitable for a wide range of applications, including consumer electronics, industrial controls, and telecommunications equipment.
High Tg FR-4
High Tg FR-4 is a variant of the standard FR-4 material with improved thermal properties. It has a higher glass transition temperature, making it suitable for applications with higher operating temperatures. The properties of High Tg FR-4 are as follows:
Property | Value |
---|---|
Dielectric Constant (Dk) | 4.2 – 4.6 (at 1 MHz) |
Dissipation Factor (Df) | 0.02 (at 1 MHz) |
Glass Transition Temperature (Tg) | 170°C – 180°C |
Coefficient of Thermal Expansion (CTE) | 12-14 ppm/°C |
Thermal Conductivity | 0.3 W/m·K |
Flexural Strength | 415 MPa |
High Tg FR-4 is commonly used in automotive electronics, aerospace applications, and high-temperature environments.
Polyimide
Polyimide is a high-performance PCB material known for its excellent thermal stability and mechanical strength. It offers superior performance compared to FR-4 in demanding applications. The properties of polyimide are as follows:
Property | Value |
---|---|
Dielectric Constant (Dk) | 3.4 – 3.5 (at 1 MHz) |
Dissipation Factor (Df) | 0.002 – 0.003 (at 1 MHz) |
Glass Transition Temperature (Tg) | 250°C – 260°C |
Coefficient of Thermal Expansion (CTE) | 12-16 ppm/°C |
Thermal Conductivity | 0.2 W/m·K |
Flexural Strength | 620 MPa |
Polyimide is often used in aerospace, military, and high-reliability applications where extreme temperatures and harsh environments are encountered.
Rogers Materials
Rogers materials are a family of high-frequency laminates designed for applications requiring excellent electrical performance and controlled dielectric properties. Some popular Rogers materials include:
- RO4003C: A hydrocarbon ceramic laminate with low dielectric constant and low loss, suitable for high-frequency applications up to 77 GHz.
- RO4350B: A glass-reinforced hydrocarbon ceramic laminate with a low dielectric constant and low loss, ideal for high-frequency and high-speed digital applications.
- RT/duroid 5880: A glass microfiber-reinforced PTFE composite with a very low dielectric constant and low loss, suitable for microwave and millimeter-wave applications.
Rogers materials are commonly used in RF and microwave circuits, antenna systems, and high-speed digital designs.
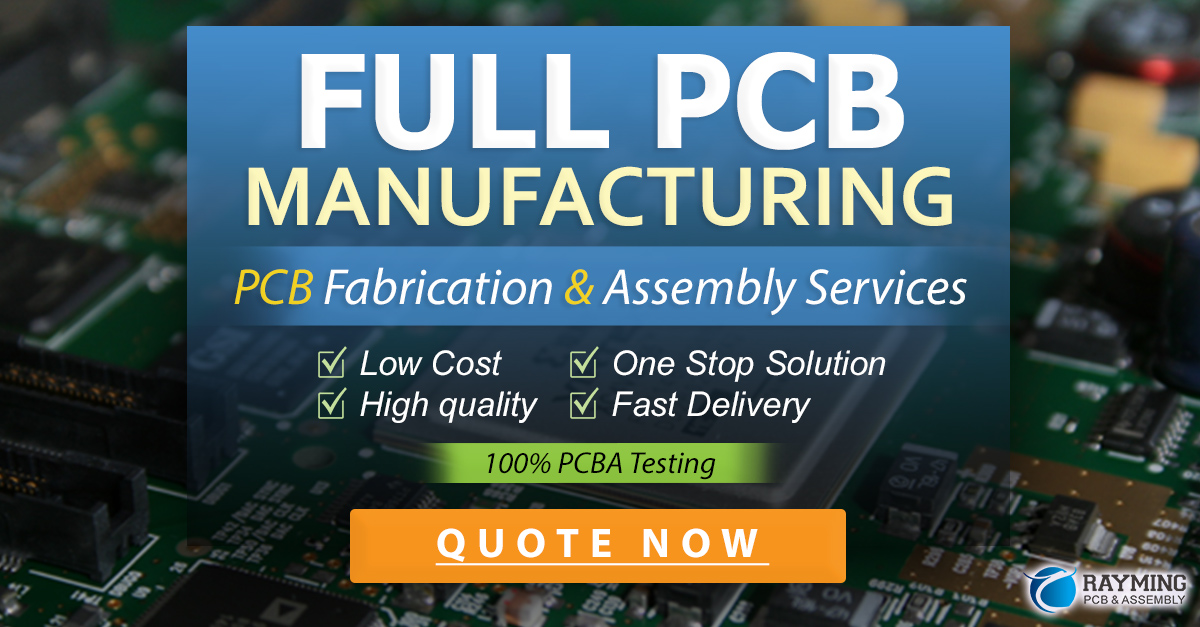
PCB Services Based on Material Choice
PCB services providers offer a range of options based on the chosen PCB material. The specific services and capabilities may vary depending on the manufacturer, but some common services include:
Material Selection Guidance
PCB services providers often offer guidance and recommendations on material selection based on the specific requirements of the application. They can help designers choose the most suitable material considering factors such as operating frequency, temperature range, and environmental conditions.
Fabrication Capabilities
Different PCB materials may require specialized fabrication processes and equipment. PCB services providers should have the necessary capabilities to handle the chosen material, including:
- Multilayer Fabrication: The ability to fabricate Multilayer PCBs using the selected material, ensuring proper lamination and adhesion between layers.
- Controlled Impedance: The capability to fabricate PCBs with controlled impedance traces, which is crucial for high-speed and RF applications.
- Tight Tolerances: The ability to maintain tight tolerances on trace widths, spacing, and hole sizes, as required by the selected material and application.
Material Certification and Traceability
PCB services providers should offer material certification and traceability to ensure the quality and consistency of the PCB materials used. This includes providing material datasheets, certificates of conformance, and lot traceability information.
Testing and Quality Control
PCB services providers should have robust testing and quality control processes in place to verify the performance and reliability of the PCBs based on the chosen material. This may include:
- Electrical Testing: Conducting electrical tests such as continuity, insulation resistance, and high-potential (HiPot) testing to ensure the electrical integrity of the PCB.
- Thermal Cycling: Subjecting the PCBs to thermal cycling tests to evaluate their performance and reliability under temperature variations.
- Environmental Testing: Performing environmental tests such as humidity, vibration, and shock testing to assess the PCB’s ability to withstand the intended operating conditions.
Frequently Asked Questions (FAQ)
-
Q: How do I choose the right PCB material for my application?
A: Choosing the right PCB material depends on several factors, including the operating frequency, temperature range, environmental conditions, and mechanical requirements of your application. Consider the electrical, thermal, and mechanical properties of the material and consult with a PCB services provider for guidance and recommendations. -
Q: Can I use different PCB materials within the same design?
A: Yes, it is possible to use different PCB materials within the same design, depending on the specific requirements of different circuit sections. For example, you may use a high-frequency material like Rogers for the RF portion of the circuit and a standard FR-4 material for the digital section. However, this may increase the complexity and cost of the fabrication process. -
Q: What are the limitations of using FR-4 material for high-frequency applications?
A: FR-4 material has limitations when used in high-frequency applications due to its higher dielectric constant and dissipation factor compared to specialized high-frequency materials like Rogers. This can result in higher signal loss, reduced signal integrity, and increased dielectric heating at higher frequencies. For high-frequency applications, it is recommended to use materials specifically designed for those frequencies. -
Q: How does the choice of PCB material affect the cost of PCB services?
A: The choice of PCB material can significantly impact the cost of PCB services. Speciality materials like high-frequency laminates and polyimide are generally more expensive than standard FR-4 material. Additionally, the fabrication processes and equipment required for certain materials may be more specialized and costly. However, the cost should be balanced against the performance and reliability requirements of the application. -
Q: Are there any environmental concerns associated with certain PCB materials?
A: Yes, some PCB materials may have environmental concerns. For example, materials containing halogenated flame retardants (such as brominated or chlorinated compounds) can release harmful substances during manufacturing or disposal. There are also concerns about the use of certain substances like lead in PCB Finishes. It is important to consider environmental regulations and choose materials that comply with relevant standards such as RoHS (Restriction of Hazardous Substances) and REACH (Registration, Evaluation, Authorization, and Restriction of Chemicals).
Conclusion
PCB material selection is a critical aspect of PCB design and fabrication, as it directly impacts the performance, reliability, and cost of the final product. PCB services providers offer a range of materials and associated services to cater to the specific requirements of different applications. By understanding the electrical, thermal, mechanical, and environmental properties of PCB materials and working closely with PCB services providers, designers can make informed decisions and ensure the success of their projects.
Leave a Reply