What is PCB Quality?
PCB (Printed Circuit Board) quality refers to the overall performance, reliability, and durability of a printed circuit board. It encompasses various factors such as the materials used, the manufacturing process, the design, and the adherence to industry standards and specifications. High-quality PCBs are essential for ensuring the proper functioning and longevity of electronic devices.
Factors Affecting PCB Quality
Several key factors contribute to the quality of a PCB:
-
Materials: The choice of materials, including the substrate (usually FR-4), copper foil, solder mask, and silkscreen, plays a crucial role in determining the quality of a PCB. High-quality materials ensure better electrical properties, thermal stability, and resistance to environmental factors.
-
Manufacturing Process: The manufacturing process, including etching, drilling, plating, and soldering, must be carried out with precision and adherence to industry standards. Any defects or inconsistencies during the manufacturing process can compromise the quality of the final product.
-
Design: A well-designed PCB layout is essential for ensuring proper functionality and minimizing signal interference. Factors such as trace width, spacing, and impedance control must be carefully considered during the design phase to maintain high quality.
-
Testing and Inspection: Rigorous testing and inspection procedures are necessary to identify and eliminate any defects or anomalies in the PCB. This includes visual inspection, automated optical inspection (AOI), and electrical testing to verify the functionality and reliability of the board.
The Importance of PCB Quality
Reliability and Durability
High-quality PCBs are crucial for ensuring the reliability and durability of electronic devices. Poor-quality PCBs are more prone to failures, such as short circuits, open circuits, and component damage, which can lead to device malfunctions and reduced lifespan. By investing in high-quality PCBs, manufacturers can minimize the risk of product failures and enhance customer satisfaction.
Cost Savings
While high-quality PCBs may have a higher initial cost, they can ultimately lead to significant cost savings in the long run. Poor-quality PCBs are more likely to fail, resulting in increased warranty claims, product returns, and repair costs. By using high-quality PCBs, manufacturers can reduce the overall cost of ownership and maintain a positive brand reputation.
Performance and Functionality
The quality of a PCB directly impacts the performance and functionality of the electronic device it powers. High-quality PCBs ensure optimal signal integrity, reduced electromagnetic interference (EMI), and proper power distribution. This translates to better device performance, faster data transmission, and enhanced user experience.
Industry Standards and Certifications
To ensure PCB quality, manufacturers adhere to various industry standards and certifications. These standards provide guidelines for design, manufacturing, and testing processes to maintain consistency and reliability across the industry.
IPC Standards
The Association Connecting Electronics Industries (IPC) is a global trade association that develops and publishes standards for the electronic interconnect industry. Some of the key IPC standards related to PCB quality include:
- IPC-A-600: Acceptability of Printed Boards
- IPC-6011: Generic Performance Specification for Printed Boards
- IPC-6012: Qualification and Performance Specification for Rigid Printed Boards
- IPC-2221: Generic Standard on Printed Board Design
These standards provide detailed requirements for PCB fabrication, assembly, and quality assessment.
UL Certification
Underwriters Laboratories (UL) is a global safety certification company that provides testing and certification services for electronic products. UL certification ensures that PCBs meet specific safety and performance requirements. PCBs that bear the UL mark have undergone rigorous testing and are deemed safe for use in electronic devices.
ISO Certification
The International Organization for Standardization (ISO) develops and publishes international standards for various industries, including electronics. ISO certifications, such as ISO 9001 (Quality Management Systems) and ISO 14001 (Environmental Management Systems), demonstrate a manufacturer’s commitment to quality and environmental responsibility.
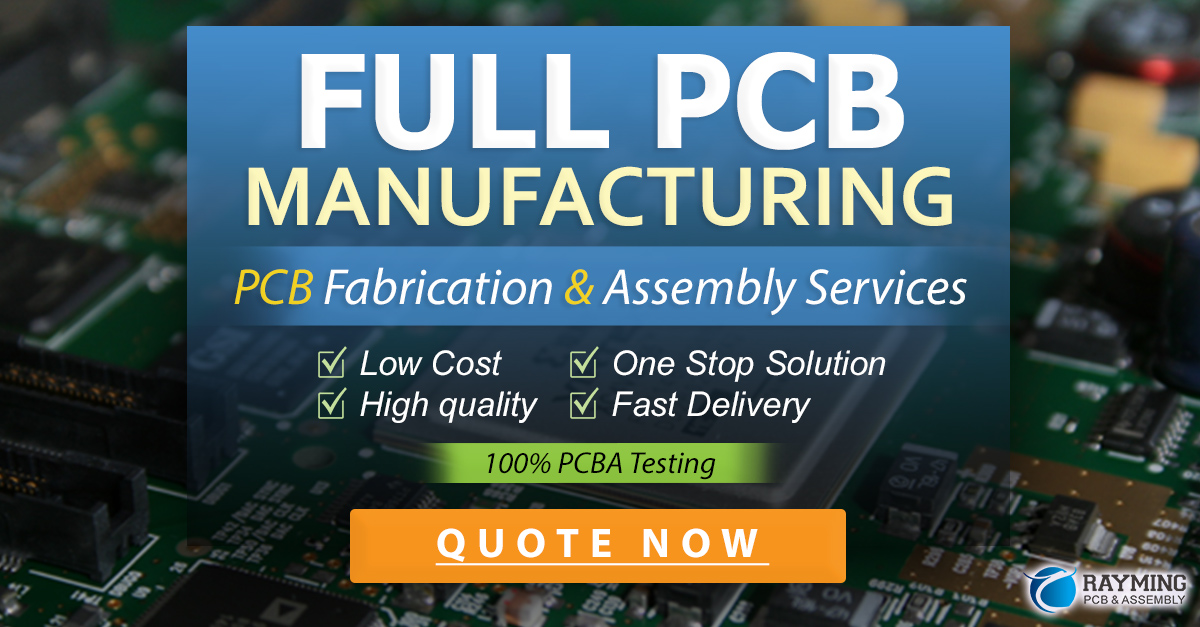
PCB Quality Control Processes
To ensure the consistent production of high-quality PCBs, manufacturers implement various quality control processes throughout the manufacturing lifecycle.
Incoming Material Inspection
Quality control begins with the inspection of incoming raw materials, such as substrates, copper foil, and solder mask. Manufacturers verify the quality and conformance of these materials to specified requirements before using them in the production process.
In-Process Inspection
During the manufacturing process, in-process inspections are performed at critical stages to identify and correct any defects or deviations. This includes inspections after etching, drilling, plating, and solder mask application. Automated optical inspection (AOI) systems are commonly used to detect surface defects, while electrical testing verifies the functionality of the PCB.
Final Inspection
Before packaging and shipping, PCBs undergo a final inspection to ensure they meet all the specified requirements. This includes visual inspection, dimensional checks, and functional testing. Any defective boards are segregated and either reworked or scrapped, depending on the nature of the defect.
Traceability and Documentation
Maintaining proper traceability and documentation is essential for ensuring PCB quality and facilitating problem-solving in case of issues. Manufacturers assign unique identifiers to each PCB and maintain records of the materials used, process parameters, and test results. This documentation helps in identifying the root cause of any quality issues and implementing corrective actions.
Common PCB Quality Issues
Despite stringent quality control measures, PCBs may sometimes exhibit quality issues. Some common PCB quality issues include:
-
Shorts and Opens: Shorts occur when unintended connections are formed between conductive traces, while opens happen when there is a break in the conductive path. These issues can be caused by manufacturing defects, design flaws, or material defects.
-
Solder Defects: Solder defects, such as bridging, insufficient solder, or solder balls, can occur during the assembly process. These defects can lead to poor electrical connections and reduced reliability.
-
Delamination: Delamination is the separation of the layers within a PCB, often caused by improper bonding or exposure to extreme temperatures. Delamination can result in electrical failures and reduced board strength.
-
Plating Defects: Plating defects, such as voids, nodules, or thin plating, can compromise the electrical and mechanical properties of the PCB. These defects are often caused by improper plating processes or contamination.
-
Component Placement Issues: Incorrect component placement, orientation, or alignment can lead to functional failures and assembly difficulties. Automated pick-and-place machines and vision systems help minimize these issues.
Troubleshooting PCB Quality Issues
When PCB quality issues arise, it is essential to have a systematic approach to troubleshooting and resolving the problem. The following steps can help in identifying and addressing PCB quality issues:
-
Identify the Symptom: Clearly define the observed problem, such as a functional failure, visual defect, or inconsistent performance.
-
Gather Information: Collect relevant information, including the PCB design files, manufacturing process data, and test results.
-
Analyze the Problem: Examine the PCB using visual inspection, microscopy, or other analytical tools to identify the root cause of the issue. This may involve cross-sectioning, x-ray imaging, or electrical testing.
-
Develop a Hypothesis: Based on the analysis, develop a hypothesis about the potential cause of the quality issue. This could be related to design, materials, manufacturing processes, or handling.
-
Implement Corrective Actions: Once the root cause is identified, implement appropriate corrective actions to resolve the issue. This may involve design changes, process improvements, material substitutions, or operator training.
-
Verify and Validate: After implementing the corrective actions, verify and validate the effectiveness of the solution through further testing and inspection.
-
Document and Communicate: Document the problem, analysis, and corrective actions taken, and communicate the findings to relevant stakeholders to prevent recurrence and share knowledge.
Frequently Asked Questions (FAQs)
-
Q: What is the difference between PCB quality and reliability?
A: PCB quality refers to the overall performance and conformance of a PCB to specified requirements at the time of manufacture. Reliability, on the other hand, is the ability of a PCB to maintain its quality and function over an extended period under specified operating conditions. -
Q: How can I ensure the quality of PCBs from a new supplier?
A: When sourcing PCBs from a new supplier, it is essential to conduct thorough due diligence. This includes reviewing the supplier’s quality certifications (e.g., ISO, UL), requesting sample boards for evaluation, and conducting on-site audits to assess their manufacturing processes and quality control measures. -
Q: What are the most critical factors to consider when designing a high-quality PCB?
A: When designing a high-quality PCB, the most critical factors to consider are the choice of materials, the layout and routing of traces, impedance control, power distribution, and thermal management. Adhering to industry design guidelines and conducting thorough design reviews can help ensure a robust and reliable PCB design. -
Q: How often should I perform quality audits on my PCB supplier?
A: The frequency of quality audits depends on various factors, such as the criticality of the PCBs, the supplier’s performance history, and the industry requirements. Generally, it is recommended to conduct initial audits before engaging with a new supplier and periodic audits (e.g., annually) to ensure ongoing compliance and continuous improvement. -
Q: What are the environmental factors that can affect PCB quality?
A: Environmental factors such as temperature, humidity, vibration, and chemical exposure can affect the quality and reliability of PCBs. High temperatures can cause thermal stress and delamination, while humidity can lead to corrosion and electrical failures. Vibration and mechanical stress can cause component dislodging and solder joint failures. Chemical exposure, such as to cleaning agents or pollutants, can degrade the PCB materials over time.
Factor | Impact on PCB Quality |
---|---|
Materials | Electrical properties, thermal stability |
Manufacturing Process | Precision, consistency, defects |
Design | Functionality, signal integrity, reliability |
Testing and Inspection | Defect detection, functionality verification |
Environmental Factors | Thermal stress, corrosion, mechanical stress |
Conclusion
PCB quality is a critical aspect of electronic product development and manufacturing. It directly impacts the reliability, performance, and cost-effectiveness of the end product. By understanding the factors that influence PCB quality, adhering to industry standards and best practices, and implementing robust quality control processes, manufacturers can ensure the production of high-quality PCBs that meet customer requirements and exceed expectations.
Investing in PCB quality is not just a matter of compliance but also a strategic decision that can provide a competitive edge in the market. High-quality PCBs lead to reduced field failures, enhanced customer satisfaction, and a positive brand reputation. As the electronics industry continues to evolve, with increasing complexity and miniaturization of devices, the importance of PCB quality will only continue to grow.
By staying updated with the latest advancements in materials, manufacturing technologies, and quality management systems, manufacturers can continuously improve their PCB quality and deliver reliable, high-performance products to their customers.
Leave a Reply