What is a PCB Prototype?
A PCB prototype, short for Printed Circuit Board prototype, is an early version of a PCB design used for testing and validation before mass production. It is a physical representation of the electronic circuit, created to ensure that the design functions as intended and meets all the necessary requirements.
PCB prototypes are essential in the product development process, as they allow engineers and designers to:
– Test the functionality of the circuit design
– Verify the layout and component placement
– Identify and fix any design flaws or errors
– Optimize the design for performance and manufacturability
– Evaluate the overall quality and reliability of the PCB
Types of PCB Prototypes
There are several types of PCB prototypes, each serving a specific purpose in the development process:
- Visual Prototype: A non-functional PCB prototype used for visual representation and layout verification.
- Proof-of-Concept (PoC) Prototype: A functional PCB prototype used to demonstrate the basic functionality of the design.
- Engineering Prototype: A fully functional PCB prototype used for extensive testing and validation of the design.
- Pre-Production Prototype: A PCB prototype that closely resembles the final product, used for final testing and certification before mass production.
Prototype Type | Purpose | Functionality |
---|---|---|
Visual Prototype | Layout verification | Non-functional |
PoC Prototype | Basic functionality demonstration | Functional |
Engineering Prototype | Extensive testing and validation | Fully functional |
Pre-Production Prototype | Final testing and certification | Closely resembles final product |
Why You Need a PCB Prototype
1. Design Verification and Optimization
One of the primary reasons for creating a PCB prototype is to verify the design and optimize it for performance and manufacturability. By testing the prototype, engineers can identify any design flaws, such as signal integrity issues, power distribution problems, or component placement errors. This allows them to make necessary adjustments and improvements before proceeding to mass production, saving time and resources in the long run.
2. Cost Savings
Creating a PCB prototype can help save costs in several ways:
– Identifying and fixing design errors early in the development process, reducing the risk of costly mistakes during mass production.
– Optimizing the design for manufacturability, which can lead to lower production costs and higher yields.
– Allowing for the selection of cost-effective components and materials based on prototype testing results.
3. Time-to-Market Reduction
By thoroughly testing and validating the PCB design through prototyping, companies can reduce the overall development time and bring their products to market faster. PCB prototypes help streamline the development process by:
– Enabling parallel testing and validation of different design aspects
– Facilitating early collaboration between design, engineering, and manufacturing teams
– Allowing for quick iterations and improvements based on prototype testing feedback
4. Compliance and Certification
In many industries, such as automotive, aerospace, and medical, electronic products must comply with strict regulations and standards. PCB prototypes play a crucial role in ensuring that the design meets all the necessary requirements for compliance and certification. By testing the prototype against relevant standards, companies can identify and address any compliance issues before final production, avoiding potential legal and financial consequences.
5. Investor and Stakeholder Engagement
PCB prototypes can be valuable tools for engaging investors and stakeholders in the product development process. A functional prototype demonstrates the feasibility and potential of the product, making it easier to secure funding, partnerships, and customer interest. Prototypes also facilitate communication and collaboration between different stakeholders, such as designers, engineers, manufacturers, and end-users, ensuring that everyone is aligned on the product vision and requirements.
PCB Prototype Development Process
The PCB prototype development process typically involves the following steps:
- Schematic Design: Create a schematic diagram of the electronic circuit, specifying the components and their interconnections.
- Component Selection: Choose the appropriate components based on the design requirements, such as functionality, performance, cost, and availability.
- PCB Layout: Design the physical layout of the PCB, including component placement, routing, and layer stackup.
- Design Rule Check (DRC): Verify that the PCB layout adheres to the manufacturing and design guidelines to ensure manufacturability and reliability.
- Prototype Fabrication: Manufacture the PCB prototype using the selected materials and components.
- Assembly: Assemble the components onto the PCB prototype, either through manual soldering or automated assembly processes.
- Testing and Validation: Test the PCB prototype to verify its functionality, performance, and compliance with design requirements.
- Iteration and Optimization: Based on the testing results, make necessary adjustments and improvements to the design, and repeat the prototyping process until the desired results are achieved.
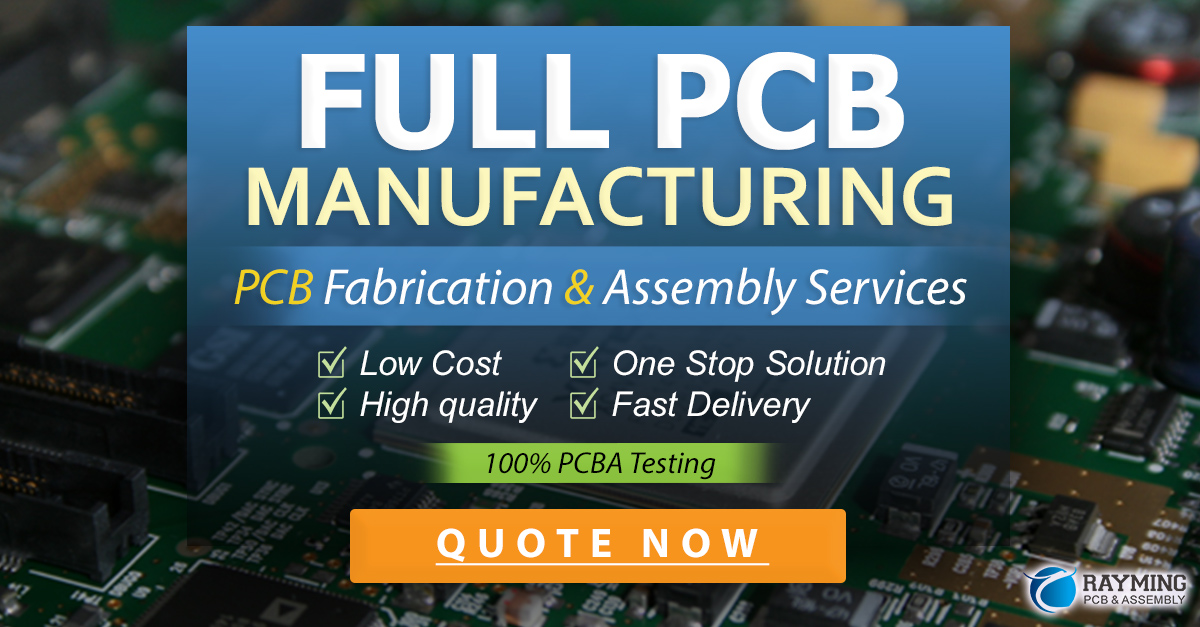
Choosing the Right PCB Prototype Manufacturer
Selecting the right PCB prototype manufacturer is crucial for ensuring the quality and reliability of your prototype. When choosing a manufacturer, consider the following factors:
- Experience and Expertise: Look for a manufacturer with extensive experience in PCB Prototyping and a proven track record of delivering high-quality prototypes.
- Technology and Capabilities: Ensure that the manufacturer has the necessary technology and capabilities to meet your specific prototyping requirements, such as multilayer PCBs, high-density interconnects, or specialized materials.
- Turnaround Time: Consider the manufacturer’s turnaround time for prototyping, especially if you have tight deadlines or need multiple iterations.
- Customer Support: Choose a manufacturer that offers reliable customer support and communication throughout the prototyping process to ensure smooth collaboration and quick resolution of any issues.
- Cost and Value: While cost is an important factor, prioritize manufacturers that offer a balance between competitive pricing and high-quality services to ensure the best value for your investment.
Frequently Asked Questions (FAQ)
-
What is the difference between a PCB prototype and a final production PCB?
A PCB prototype is an early version of the PCB design used for testing and validation, while a final production PCB is the finalized version used for mass production. Prototypes may have different materials, components, or manufacturing processes compared to the final production PCB. -
How long does it take to develop a PCB prototype?
The development time for a PCB prototype varies depending on the complexity of the design, the chosen manufacturer, and the required iterations. Simple prototypes can be developed within a few days, while more complex designs may take several weeks. -
How much does a PCB Prototype Cost?
The cost of a PCB prototype depends on factors such as the size, complexity, materials, and quantity of the prototype. Simple prototypes can cost a few hundred dollars, while more complex designs can cost several thousand dollars. It’s essential to discuss your requirements and budget with potential manufacturers to get accurate quotes. -
Can I use a PCB prototype for final production?
While PCB prototypes are primarily used for testing and validation, in some cases, they can be used for final production if they meet all the necessary requirements and have been thoroughly tested. However, it’s essential to discuss this with your manufacturer to ensure that the prototype is suitable for final production. -
What should I do if my PCB prototype fails during testing?
If your PCB prototype fails during testing, the first step is to identify the root cause of the failure. This may involve analyzing the test results, inspecting the prototype, or conducting further investigations. Based on the findings, you can make necessary adjustments to the design, components, or manufacturing process and create a new prototype for testing. It’s essential to work closely with your manufacturer and engineering team to address any issues and ensure the success of your PCB design.
Conclusion
PCB prototypes are essential tools in the electronic product development process, enabling designers and engineers to test, validate, and optimize their designs before mass production. By investing in PCB prototyping, companies can save costs, reduce development time, ensure compliance, and engage stakeholders effectively. When selecting a PCB prototype manufacturer, consider factors such as experience, capabilities, turnaround time, customer support, and value to ensure the best outcome for your project. By following a structured prototyping process and collaborating closely with your manufacturer, you can bring your electronic product vision to life and succeed in the competitive market.
Leave a Reply