PCB Fabrication Specifications
Board Thickness
The default board thickness for most PCB Proto Services is 1.6mm (0.062″). This is the most common PCB Thickness used across the industry. However, other standard thicknesses are available if needed for your design:
Thickness (mm) | Thickness (mils) |
---|---|
0.4 | 15.7 |
0.6 | 23.6 |
0.8 | 31.5 |
1.0 | 39.4 |
1.2 | 47.2 |
1.6 | 62.9 |
2.0 | 78.7 |
2.4 | 94.5 |
Thicker PCBs of 3.2mm (0.126″) or more can also be manufactured by some proto services, but these are less common. The thickness required depends on your specific application – thinner boards provide flexibility and space savings, while thicker boards offer increased durability.
Copper Weight
The amount of copper cladding on a PCB is indicated by its “copper weight” in ounces per square foot (oz/ft2). The typical default is 1 oz/ft2, or 35 μm thickness. This is suitable for most general purpose PCB designs. Other common copper weights include:
Copper Weight (oz/ft2) | Thickness (μm) |
---|---|
0.5 | 17.5 |
1 | 35 |
2 | 70 |
3 | 105 |
Heavier 2 or 3 oz copper is often used for high-current designs, while 0.5 oz is used when finer trace widths and space savings are priorities. Not all PCB proto services offer all copper weights, so check the capabilities of your vendor.
Minimum Trace/Space
The “trace/space” or “track/gap” refers to the minimum width of copper traces on the PCB and the minimum spacing between them. As PCB manufacturing has advanced, finer trace and space dimensions have become more readily available. The default supported by most PCB proto services is now 6/6mil (0.15/0.15mm).
However, many services offer 5/5mil or even 4/4mil for an additional cost. These finer pitch options are useful for dense SMD designs. On the other end, low-cost services may use 8/8mil or 10/10mil defaults. Always confirm the minimum trace/space a vendor can fabricate to.
Solder Mask Color
The default solder mask color used by virtually all PCB proto services is green. This is such a common default that “green PCB” has almost become synonymous with prototype circuit boards.
However, many proto services offer other solder mask color options at no additional cost. Typical color choices include:
- Red
- Yellow
- Blue
- Purple
- Black
- White
Using a non-standard mask color can be a good way to visually distinguish your prototype PCBs. But for most applications, there is no significant benefit beyond appearance.
Silkscreen Color
The silkscreen is used to print text and graphics onto the PCB. The default silkscreen color is usually white, as it provides good contrast against most solder mask colors.
Some proto services also offer black, yellow, or other silkscreen colors. Black is a popular alternative on white solder mask PCBs. However, many low-cost proto services only have white silkscreen available, so other colors may incur additional cost.
Surface Finish
The surface finish on a PCB affects its solderability, durability, and shelf life. There are several common types of PCB Surface Finishes:
Finish | Composition | Pros | Cons |
---|---|---|---|
HASL | Tin-lead alloy | Low cost, good solderability | Not RoHS compliant, uneven surface |
Lead-free HASL | Tin alloy | Widely available, RoHS compliant | Uneven surface, air-bridge risk |
ENIG | Electroless nickel / immersion gold | Flat surface, long shelf life, aluminum wire bonding | Higher cost |
OSP | Organic solderability preservatives | Low cost, flat surface, quick to manufacture | Short shelf life, no aluminum bonding |
Immersion silver | Thin silver layer | Inexpensive, flat surface, quick process | Prone to tarnishing over time |
Immersion tin | Thin tin layer | Low cost, good solderability | Can form tin whiskers, limited shelf life |
The default surface finish from most PCB proto services is currently lead-free HASL. It offers good solderability and wide availability with RoHS Compliance. However, many services provide ENIG as a default for a small added cost due to its superior planarity, durability, and shelf life. ENIG is recommended for dense SMD designs or boards that will be stored for an extended period before assembly.
Via Type
Vias are used extensively in multi-layer PCBs to route signals between layers. Through-hole vias that go through the entire board thickness are the default type supported by virtually all PCB proto services.
However, blind and buried vias are also available from many vendors for an added cost. Blind vias connect an outer layer to one or more inner layers, while buried vias connect inner layers without reaching the surface. These can enable greater routing density in complex designs.
Via-in-pad (VIP) is another option that allows traces or components to be placed over vias. This is very useful for BGA and other high pin count parts. VIP requires precise drilling and plating capabilities, so it is not offered by all proto services.
Via Size
In additional to via type, the diameter of the via drill hole and the size of the annular ring are also important parameters. Most proto services will default to the smallest via size they support, which is typically 0.3mm or 0.4mm diameter.
Smaller 0.2mm microvias are also available from some vendors, which are used for HDI designs. On the other end of the spectrum, vias up to 3.0mm or larger can be fabricated. These larger sizes may be needed for high-current vias, mounting holes, or plated slots.
The default annular ring size is usually 0.15-0.2mm depending on via diameter. Smaller annular rings allow for tighter routing but are more challenging to manufacture reliably.
PCB Design Checks and Default Rules
When a PCB proto service receives your design files, they will typically run them through a series of automated checks to verify manufacturability. These design rule checks (DRCs) help catch issues like insufficient clearances, missing solder mask openings, acid traps, and so on. The default parameters used for these checks vary between proto services.
Clearances
PCB proto services will verify that your design has sufficient clearance between copper features and the board edge, holes, and other components. The default minimum clearances are usually:
- Copper to board edge: 0.2mm
- Copper to drill hole: 0.25mm
- Copper to copper: 0.2mm
If space is tight, tighter clearances of 0.15mm or even 0.1mm may be permitted. But these are more difficult to fabricate, so yields may be lower.
Annular Ring
In addition to checking minimum clearances, the DRC will also verify the annular ring size on vias and pads. The default minimum annular ring is typically:
- 0.15mm for vias under 0.5mm diameter
- 0.2mm for larger vias and pads
A smaller annular ring down to 0.1mm may be allowed in some cases. However, the annular ring should be at least 50% of the via drill size to avoid breakout.
Solder Mask Openings
Solder mask openings that are too small can lead to soldering difficulties and unreliable solder joints. Most proto services have a default minimum solder mask opening of 0.1mm all around the copper pad.
For fine-pitch components like 0402 or smaller, the solder mask opening may need to be only 0.05mm or the mask may be removed entirely. On the other end, parts like connectors or large power components may require solder mask pullback of 0.5mm or more.
Acid Traps
Acid traps are acute angles or narrow channels in the copper layer that can trap chemical etchant during fabrication. This can lead to over-etching and result in open circuits or weak traces.
Most PCB design software will automatically flag potential acid traps. But if not, proto services usually check for acute angles less than 60° or channels narrower than 0.2mm as part of their DRC.
Assembly and Testing Options
Some PCB proto services also offer assembly and testing as optional add-on services. This can be very convenient for getting fully functional prototypes. But the available options and default configurations for assembly and testing vary significantly between vendors.
Assembly Type
The most basic assembly option is material procurement and kitting. The proto service will source the components per your bill of materials (BOM) and package them with your bare PCBs for assembly elsewhere.
The next level is PCB Assembly (PCBA) service, where the components are actually soldered to the board. This is typically done with a combination of automated SMT placement for most parts and manual assembly for through-hole and odd-form components.
For simple PCBAs, the proto service may offer full turnkey assembly as a default option. More complex assemblies with BGAs, tight pitches, or unusual parts may be treated as a custom quote.
Soldering
If PCBA service is offered, the default soldering is usually lead-free reflow and wave soldering. This is compatible with a wide range of components and is RoHS compliant.
Some proto services may also offer leaded solder as a default for designs that are not RoHS sensitive. Hand soldering may be used by default for small quantities or large through-hole parts.
Testing
Different levels of testing may be offered by PCB assembly services:
- Basic continuity and shorts testing is often included by default to check for solder bridges or open pins.
- In-circuit testing (ICT) verifies each component is properly soldered using a bed-of-nails test fixture. This is sometimes offered as an optional add-on.
- Functional circuit testing to verify the operation of the complete PCBA may be available for an extra fee, if the proto service has the necessary expertise and test development resources.
Conformal Coating
Finally, conformal coating may be an optional finishing step for PCBAs that will be exposed to moisture, chemicals, or debris. The default coating, if offered, is usually a clear acrylic spray. Alternatives like urethane, epoxy, or silicone may incur additional cost.
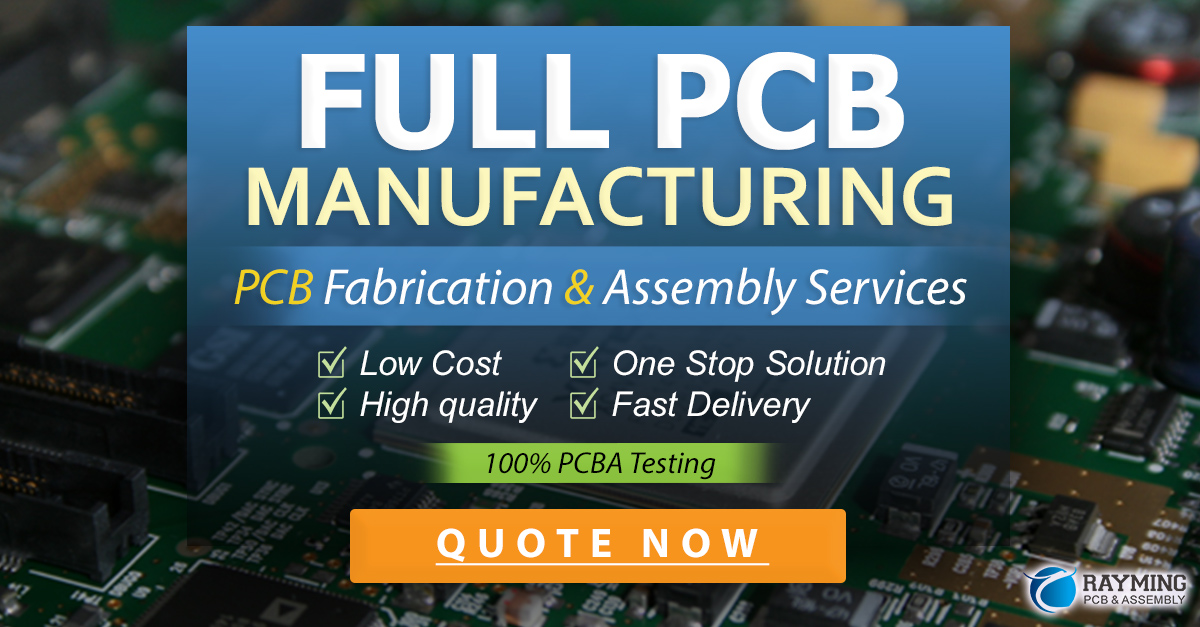
Summary
We’ve covered a lot of ground in this deep dive into PCB proto service default values. Some key points to remember:
- Always check your proto vendor’s capabilities and default options, as these can vary significantly.
- The most common defaults are 1.6mm board thickness, 1 oz copper, 6/6mil trace/space, green solder mask, and lead-free HASL finish.
- Smaller vias, finer pitches, unique surface finishes, or additional colors may incur added cost over the baseline offering.
- Design rule checks are essential to verify your board meets the fabricator’s tolerances and clearance limits.
- Not all proto services offer assembly and testing – for those that do, the specific options can range from basic kitting to full turnkey.
By understanding the typical defaults and carefully specifying your requirements, you can get reliable PCB Prototypes that meet your needs without paying for more than you require.
FAQ
What if my design requires specs tighter than the default values?
If your PCB demands features finer than the standard defaults – like 4/4 mil trace/space, 0.2mm microvias, or 0.5 oz copper – it’s important to discuss your needs upfront with your proto vendor. Many services can support these tighter specs, but they may entail additional cost and lead time.
Are the cheapest PCB proto services good enough?
The lowest-cost prototype services often use a limited menu of materials and conservative design rules. This allows them to pool many designs onto a single panel for cost efficiency. While these can be good for simple PCBs or early development, designs with fine-pitch BGAs, RF circuits, or tight tolerances usually benefit from a more capable proto service.
Should I just default to the tightest specs and highest quality?
While it may be tempting to default to the most stringent specs across the board, this is usually cost prohibitive, especially for simple prototype designs. Paying for ultra-fine traces or an expensive surface finish you don’t really need is not a good use of your development budget. It’s better to choose reasonable defaults and only tighten the specs as your specific design requires.
What’s the best surface finish to use?
The ideal surface finish depends a lot on your PCB design and assembly process. ENIG is a great general-purpose option due to its excellent corrosion resistance, great solderability, and long shelf life. But it costs more than OSP or HASL. For prototypes that will be assembled immediately, lead-free HASL can provide good results at a lower cost.
How much extra does colored solder mask or silkscreen cost?
It depends on the specific vendor, but it’s often no extra cost to choose an alternate solder mask color like red, blue, black, or white. Non-standard silkscreen colors may carry a small added cost, as the masks and materials are less common. It’s best to check your proto service’s specific color options and pricing.
Leave a Reply