What is a PCB Inductor?
A PCB inductor, also known as a printed circuit board inductor, is a passive electronic component that stores energy in a magnetic field when electric current flows through it. It consists of a coil of conductive material, usually copper, that is wound around a core or substrate. PCB inductors are essential components in various electronic circuits, such as power supplies, filters, and oscillators, where they are used to filter noise, smooth voltage ripples, and store energy.
PCB inductors come in various shapes and sizes, depending on their intended application and the required inductance value. Some common types of PCB inductors include:
- Surface Mount Device (SMD) Inductors
- Through-Hole Inductors
- Multilayer Inductors
- Toroidal Inductors
- Planar Inductors
Advantages of PCB Inductors
PCB inductors offer several advantages over traditional wire-wound inductors:
- Compact size: PCB inductors are much smaller than wire-wound inductors, making them suitable for use in space-constrained applications.
- Lower cost: The manufacturing process for PCB inductors is more automated, resulting in lower production costs compared to wire-wound inductors.
- Better performance: PCB inductors have lower parasitic capacitance and resistance, leading to better high-frequency performance.
- Consistent quality: The automated manufacturing process ensures consistent quality and repeatability of PCB inductors.
Inductance Value and Its Importance
Inductance is a measure of a coil’s ability to store energy in a magnetic field. It is measured in henries (H) and is represented by the symbol L. The inductance value of a PCB inductor is crucial because it determines the component’s performance in a given circuit.
The inductance value depends on several factors, including:
- Number of turns in the coil
- Cross-sectional area of the coil
- Length of the coil
- Material of the core or substrate
A higher number of turns, larger cross-sectional area, and shorter length of the coil generally result in a higher inductance value. The core material also plays a significant role in determining the inductance value, with materials like ferrite and iron powder offering higher permeability and, consequently, higher inductance values.
Methods of Computing Inductance Value
There are several methods to compute the inductance value of a PCB inductor, ranging from simple empirical formulas to more complex numerical simulations. Some of the most common methods are:
1. Empirical Formulas
Empirical formulas are simple, closed-form equations that provide an approximate estimate of the inductance value based on the physical dimensions of the inductor. These formulas are derived from experimental data and are suitable for quick, rough estimations.
One of the most widely used empirical formulas for calculating the inductance of a square planar spiral inductor is the Modified Wheeler formula:
L = K1 * μ0 * n^2 * d_avg / (1 + K2 * ρ)
Where:
– L is the inductance in henries (H)
– K1 and K2 are constants that depend on the inductor geometry (see table below)
– μ0 is the permeability of free space (4π × 10^-7 H/m)
– n is the number of turns
– d_avg is the average diameter of the coil in meters
– ρ is the fill ratio, defined as (d_out – d_in) / (d_out + d_in)
Inductor Geometry | K1 | K2 |
---|---|---|
Square | 2.34 | 2.75 |
Hexagonal | 2.33 | 3.82 |
Octagonal | 2.25 | 3.55 |
While empirical formulas provide a quick way to estimate the inductance value, they have limited accuracy and do not account for all the factors that influence the inductor’s performance, such as the substrate material and thickness, and the presence of ground planes.
2. Analytical Methods
Analytical methods involve solving Maxwell’s equations to derive closed-form expressions for the inductance value. These methods provide more accurate results than empirical formulas but are more complex and require a deeper understanding of electromagnetic theory.
One example of an analytical method is the Greenhouse formula, which calculates the inductance of a rectangular planar spiral inductor:
L = 0.0002 * l_tot * (ln(2 * l_tot / w) + 0.50049 + w / (3 * l_tot))
Where:
– L is the inductance in microhenries (μH)
– l_tot is the total length of the coil in centimeters
– w is the width of the trace in centimeters
The Greenhouse formula considers the self-inductance of the straight segments and the mutual inductance between parallel segments, providing a more accurate estimation than empirical formulas. However, it still has limitations, such as not accounting for the presence of ground planes or the effects of the substrate material.
3. Numerical Simulations
Numerical simulations are the most accurate method for computing the inductance value of a PCB inductor. These simulations use computational electromagnetics techniques, such as the Finite Element Method (FEM) or the Method of Moments (MoM), to solve Maxwell’s equations numerically.
Numerical simulations can account for various factors that influence the inductor’s performance, including:
- Complex geometry of the inductor
- Presence of ground planes and other conductive structures
- Material properties of the substrate and conductors
- Frequency-dependent effects, such as skin effect and proximity effect
Some popular software tools for numerical simulations of PCB inductors include:
- Ansys HFSS
- Keysight ADS
- Sonnet Software
- CST Studio Suite
While numerical simulations provide the most accurate results, they are also the most time-consuming and computationally intensive method. They require specialized software tools and a good understanding of electromagnetic theory and numerical methods.
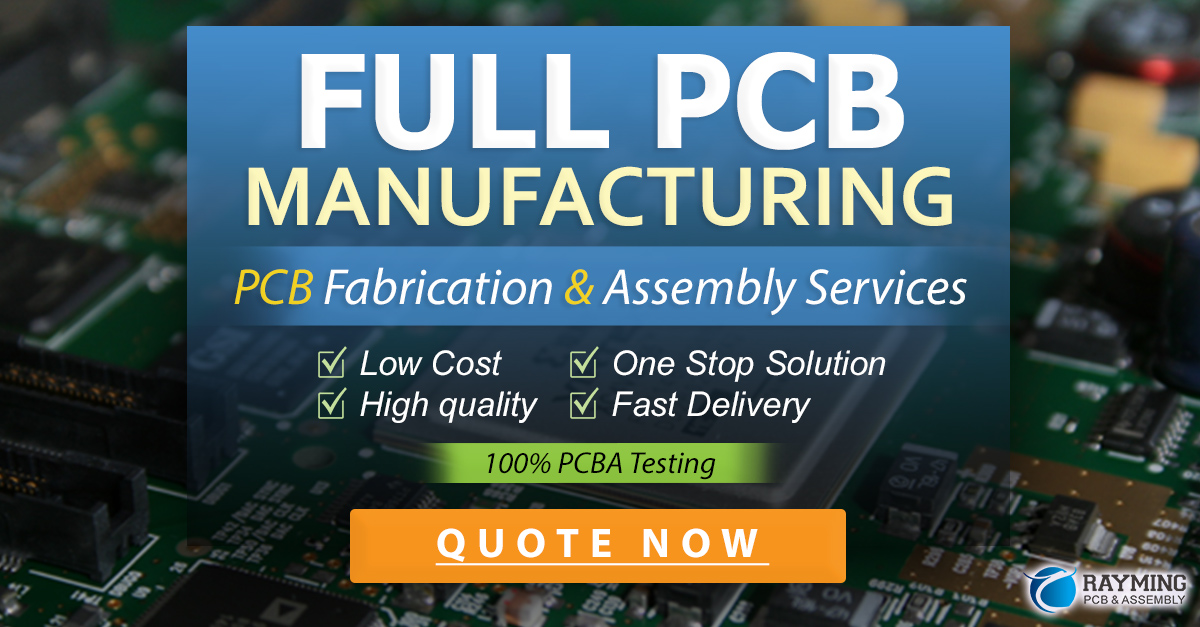
Factors Affecting Inductance Value
Several factors can influence the inductance value of a PCB inductor:
- Number of turns: Increasing the number of turns in the coil leads to a higher inductance value.
- Cross-sectional area: A larger cross-sectional area of the coil results in a higher inductance value.
- Length of the coil: A shorter coil length leads to a higher inductance value.
- Core material: Using a core material with higher permeability, such as ferrite or iron powder, increases the inductance value.
- Spacing between turns: Decreasing the spacing between turns increases the mutual inductance and, consequently, the overall inductance value.
- Trace width: Wider traces have lower resistance and lower inductance, while narrower traces have higher resistance and higher inductance.
- Substrate material: The substrate material’s Dielectric Constant and thickness can affect the inductor’s performance and inductance value.
- Frequency: The inductance value can vary with frequency due to skin effect and proximity effect, which cause the current to flow primarily on the surface of the conductor at high frequencies.
FAQ
1. What is the difference between a PCB inductor and a wire-wound inductor?
PCB inductors are fabricated directly on a printed circuit board using conductive traces, while wire-wound inductors are made by winding a wire around a core or former. PCB inductors are generally smaller, cheaper, and have better high-frequency performance than wire-wound inductors.
2. How do I choose the right PCB inductor for my application?
When selecting a PCB inductor, consider the following factors:
- Required inductance value
- Current rating
- Frequency range of operation
- Size constraints
- Operating temperature range
- Cost
Consult the manufacturer’s datasheet and application notes to ensure that the chosen inductor meets your circuit’s requirements.
3. Can I increase the inductance value of a PCB inductor?
Yes, you can increase the inductance value of a PCB inductor by:
- Increasing the number of turns
- Increasing the cross-sectional area of the coil
- Decreasing the length of the coil
- Using a core material with higher permeability
However, these modifications may also affect other properties of the inductor, such as its resistance, self-resonant frequency, and quality factor.
4. What is the self-resonant frequency of a PCB inductor?
The self-resonant frequency (SRF) of a PCB inductor is the frequency at which the inductor’s inductive reactance is equal to its capacitive reactance. At frequencies above the SRF, the inductor behaves more like a capacitor than an inductor. The SRF depends on the inductor’s inductance value and its parasitic capacitance, which arises from the capacitance between the turns and between the inductor and the ground plane.
5. How do I measure the inductance value of a PCB inductor?
You can measure the inductance value of a PCB inductor using several methods:
- LCR meter: An LCR meter is an instrument that measures the inductance, capacitance, and resistance of a component. Connect the inductor to the LCR meter and read the inductance value at the desired frequency.
- Impedance analyzer: An impedance analyzer measures the complex impedance of a component over a range of frequencies. Connect the inductor to the impedance analyzer and measure its impedance at the desired frequency. The inductance value can be calculated from the imaginary part of the impedance.
- Network analyzer: A network analyzer measures the scattering parameters (S-parameters) of a component or circuit. Connect the inductor to the network analyzer and measure its S-parameters. The inductance value can be extracted from the S-parameters using circuit analysis techniques.
When measuring the inductance value, ensure that the measurement frequency is well below the inductor’s self-resonant frequency to obtain accurate results.
Conclusion
PCB inductors are essential components in modern electronic circuits, offering a compact, cost-effective, and high-performance solution for energy storage and filtering applications. Understanding the factors that influence the inductance value and the methods for computing it is crucial for designing and optimizing PCB inductors.
While empirical formulas and analytical methods provide quick estimates of the inductance value, numerical simulations offer the most accurate results, considering the complex geometry and material properties of the inductor. As with any electronic component, careful selection and design of PCB inductors based on the application requirements are essential for ensuring optimal circuit performance.
Leave a Reply