Understanding PCB Troubleshooting
PCB troubleshooting is the process of identifying and resolving issues that arise in PCB manufacturing, assembly, or operation. It involves a systematic approach to diagnose the problem, isolate the root cause, and implement an effective solution. PCB troubleshooting requires a combination of technical knowledge, problem-solving skills, and the use of appropriate tools and techniques.
Common PCB Problems
Before diving into PCB troubleshooting techniques, let’s take a look at some of the most common problems encountered in PCB electronics:
- Short circuits
- Open circuits
- Incorrect component placement
- Solder joint issues
- Dry joints
- Broken traces
- Damaged components
- Electromagnetic interference (EMI)
- Thermal issues
- Manufacturability problems
These issues can lead to malfunctions, reduced performance, or complete failure of the PCB. Understanding these common problems is crucial for effective PCB troubleshooting.
PCB Troubleshooting Techniques
Visual Inspection
The first step in PCB troubleshooting is to perform a thorough visual inspection of the board. This involves examining the PCB for any visible defects or anomalies. Some key areas to focus on during visual inspection include:
- Solder joints: Look for any cold solder joints, excessive solder, or insufficient solder.
- Component placement: Verify that all components are correctly placed and oriented.
- Traces: Check for any broken, damaged, or shorted traces.
- Cleanliness: Ensure that the PCB is free from dirt, debris, or contaminants.
Visual inspection can often reveal obvious issues that can be quickly resolved.
Continuity Testing
Continuity testing is a technique used to verify the electrical connectivity between two points on a PCB. It helps identify open circuits or breaks in the conductive paths. To perform continuity testing, you can use a multimeter set to the continuity or resistance mode. Follow these steps:
- Identify the two points you want to test for continuity.
- Place one probe of the multimeter on each point.
- If the multimeter beeps or shows a low resistance value, it indicates continuity between the points.
- If there is no beep or the resistance is high, it suggests an open circuit or break in the conductive path.
Continuity testing is particularly useful for checking the integrity of traces, solder joints, and component connections.
Power Supply Testing
Power supply issues are a common cause of PCB malfunctions. To troubleshoot power supply problems, follow these steps:
- Verify the input voltage: Ensure that the correct voltage is being supplied to the PCB.
- Check voltage regulators: Test the output of voltage regulators to ensure they are providing the expected voltage levels.
- Measure voltage at key points: Use a multimeter to measure the voltage at various points on the PCB, such as power rails and component power pins.
- Check for short circuits: Look for any short circuits that may be causing excessive current draw or voltage drops.
Power supply testing helps identify issues related to power distribution, regulation, and short circuits.
Signal Tracing
Signal tracing involves following the path of a signal through the PCB to identify any abnormalities or disruptions. It is particularly useful for troubleshooting issues related to signal integrity, such as noise, distortion, or attenuation. To perform signal tracing, you can use an oscilloscope or logic analyzer. Follow these steps:
- Identify the signal of interest and its expected behavior.
- Connect the oscilloscope or logic analyzer probes to the appropriate test points on the PCB.
- Observe the signal waveform and compare it to the expected behavior.
- Look for any deviations, such as excessive noise, distortion, or incorrect timing.
- Trace the signal path to identify the source of the issue.
Signal tracing requires knowledge of the PCB schematic and an understanding of the expected signal characteristics.
Thermal Imaging
Thermal imaging is a non-invasive technique used to identify hot spots or thermal issues on a PCB. It involves using a thermal camera or infrared thermometer to capture the temperature distribution across the board. Thermal imaging can help detect:
- Overheating components
- Insufficient heat dissipation
- Thermal runaway conditions
- Inadequate cooling or airflow
By identifying thermal issues, you can take appropriate measures to improve heat dissipation, optimize component placement, or adjust cooling mechanisms.
In-Circuit Testing
In-circuit testing (ICT) is a powerful technique used to test individual components on a PCB without removing them from the board. It involves using specialized test equipment, such as an ICT fixture or a bed-of-nails tester, to access the component pins and perform electrical measurements. ICT can help detect:
- Component failures
- Incorrect component values
- Short circuits
- Open circuits
- Incorrect component placement
ICT is particularly useful for high-volume production testing and ensures that each component meets its specified tolerances.
PCB Troubleshooting Tools
To effectively troubleshoot PCB issues, it is essential to have the right tools at your disposal. Some common PCB troubleshooting tools include:
Tool | Description |
---|---|
Multimeter | Measures voltage, current, resistance, and continuity |
Oscilloscope | Displays and analyzes waveforms and signal characteristics |
Logic Analyzer | Captures and analyzes digital signals and bus transactions |
Thermal Camera | Captures thermal images and identifies hot spots |
Soldering Iron | Used for soldering and desoldering components |
Desoldering Pump | Removes solder from joints for component replacement |
Tweezers | Assists in handling small components and probing test points |
Magnifying Glass | Provides enhanced visual inspection of PCB Components |
ESD-Safe Workstation | Protects sensitive components from electrostatic discharge |
Having the right tools and knowing how to use them effectively is crucial for successful PCB troubleshooting.
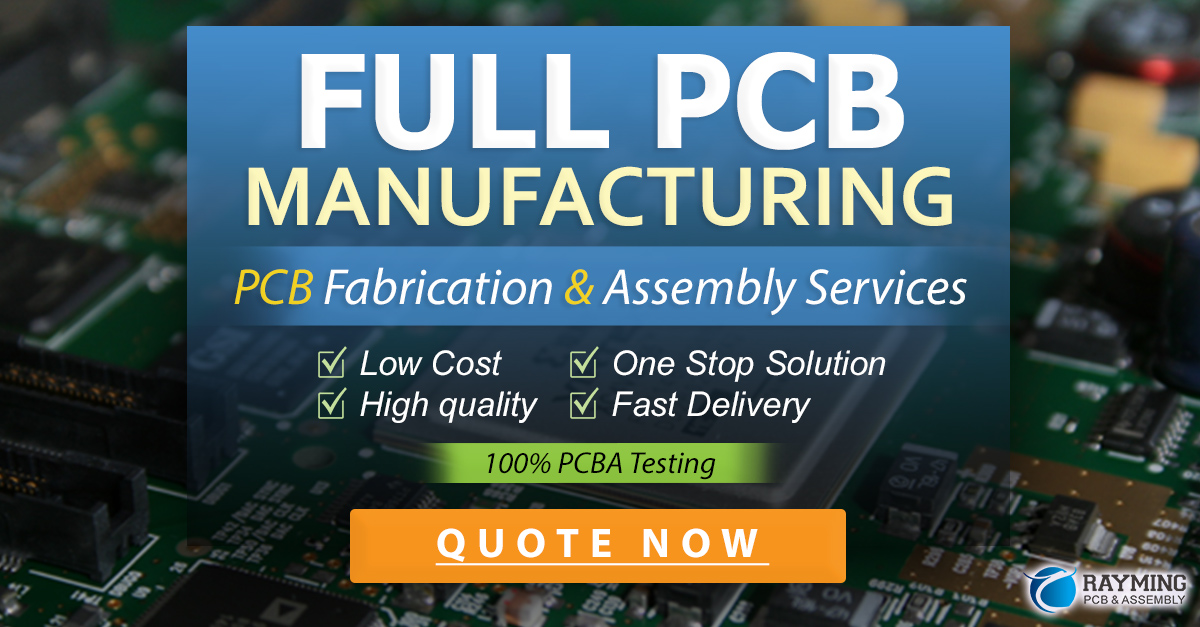
Troubleshooting Specific PCB Issues
Short Circuits
Short circuits occur when two or more points on a PCB that should not be connected become electrically connected. This can happen due to solder bridges, damaged insulation, or conductive debris. To troubleshoot short circuits:
- Perform visual inspection to identify any visible shorts.
- Use a multimeter to measure resistance between the shorted points.
- Carefully remove any solder bridges or debris causing the short.
- Repair any damaged traces or insulation.
- Retest the PCB to ensure the short circuit is resolved.
Open Circuits
Open circuits occur when there is a break or discontinuity in a conductive path on the PCB. This can be caused by broken traces, damaged components, or poor solder joints. To troubleshoot open circuits:
- Perform continuity testing to identify the location of the open circuit.
- Visually inspect the affected area for any visible damage or breaks.
- Repair any broken traces or solder joints.
- Replace any damaged components.
- Retest the PCB to ensure the open circuit is resolved.
Incorrect Component Placement
Incorrect component placement can lead to PCB malfunctions or complete failure. It is important to ensure that all components are placed in their correct locations and oriented properly. To troubleshoot incorrect component placement:
- Compare the PCB to the assembly diagram or schematic.
- Visually inspect each component for correct placement and orientation.
- Use a multimeter to verify the correct pin connections.
- Replace any incorrectly placed components.
- Retest the PCB to ensure proper functionality.
Solder Joint Issues
Solder joint issues, such as cold solder joints, excessive solder, or insufficient solder, can cause intermittent connections or complete failure. To troubleshoot solder joint issues:
- Perform visual inspection to identify any problematic solder joints.
- Use a soldering iron to reflow or rework the affected solder joints.
- Apply the appropriate amount of solder and ensure good wetting.
- Clean any flux residue or debris from the solder joints.
- Retest the PCB to ensure reliable connections.
Electromagnetic Interference (EMI)
EMI can cause signal integrity issues, such as noise, crosstalk, or distortion. It occurs when electronic devices or circuits generate unwanted electromagnetic signals that interfere with the operation of other devices. To troubleshoot EMI issues:
- Identify the source of the interference using spectrum analyzers or EMI probes.
- Implement proper grounding and shielding techniques to reduce EMI.
- Use ferrite beads or EMI filters to suppress high-frequency noise.
- Optimize PCB layout to minimize coupling and crosstalk.
- Retest the PCB to ensure EMI levels are within acceptable limits.
Thermal Issues
Thermal issues can cause components to overheat, leading to reduced performance or eventual failure. To troubleshoot thermal issues:
- Use thermal imaging to identify hot spots on the PCB.
- Verify that components are operating within their specified temperature ranges.
- Improve heat dissipation through the use of heat sinks, thermal pads, or cooling fans.
- Optimize PCB layout to promote better airflow and heat distribution.
- Retest the PCB to ensure acceptable thermal performance.
Frequently Asked Questions (FAQ)
-
What is the first step in PCB troubleshooting?
The first step in PCB troubleshooting is to perform a thorough visual inspection of the board. This involves examining the PCB for any visible defects, such as solder joint issues, incorrect component placement, or damaged traces. -
What tools are commonly used for PCB troubleshooting?
Some common tools used for PCB troubleshooting include multimeters, oscilloscopes, logic analyzers, thermal cameras, soldering irons, desoldering pumps, tweezers, magnifying glasses, and ESD-safe workstations. -
How can I identify short circuits on a PCB?
To identify short circuits on a PCB, you can perform visual inspection to look for any visible shorts, use a multimeter to measure resistance between the shorted points, and carefully remove any solder bridges or debris causing the short. -
What causes open circuits on a PCB?
Open circuits on a PCB can be caused by broken traces, damaged components, or poor solder joints. These issues can lead to a break or discontinuity in the conductive path, resulting in an open circuit. -
How can I troubleshoot EMI issues on a PCB?
To troubleshoot EMI issues on a PCB, you can start by identifying the source of the interference using spectrum analyzers or EMI probes. Then, implement proper grounding and shielding techniques, use ferrite beads or EMI filters to suppress high-frequency noise, and optimize the PCB layout to minimize coupling and crosstalk.
Conclusion
PCB troubleshooting is a critical skill for anyone involved in electronics design, manufacturing, or maintenance. By understanding common PCB problems and applying systematic troubleshooting techniques, you can effectively identify and resolve issues, ensuring the proper functioning of your electronic devices.
Remember to start with a visual inspection, use appropriate tools, and follow a logical troubleshooting approach. Don’t hesitate to seek assistance from experienced professionals or refer to PCB design guidelines and best practices when faced with complex issues.
With patience, perseverance, and the right knowledge, you can become proficient in PCB troubleshooting and tackle any challenges that come your way in the world of PCB electronics.
Leave a Reply