Understand the PCB Design Process
Before diving into the specific guidelines, it’s important to understand the overall PCB design process. The typical steps involved in PCB design are:
- Schematic design
- Component selection
- PCB layout
- Design rule checks (DRC)
- Manufacturing
Each step plays a critical role in the success of the final product. Let’s explore these steps in more detail.
Schematic Design
The schematic design is the first step in the PCB design process. It involves creating a diagram that represents the electrical connections between components. The schematic should be clear, well-organized, and easy to understand. Use consistent naming conventions and provide clear labels for all components and signals.
Component Selection
Selecting the right components is crucial for the performance and reliability of the PCB. Consider factors such as:
- Functionality
- Size and package type
- Power requirements
- Cost
- Availability
Choose components that meet the design requirements and are readily available from reliable suppliers.
PCB Layout
The PCB layout is the process of arranging components and routing traces on the board. Follow these guidelines for an effective PCB layout:
- Keep the layout organized and symmetric
- Minimize the distance between components
- Use proper trace widths and spacing
- Avoid sharp angles in traces
- Provide adequate clearance between components and traces
- Consider signal integrity and EMI (electromagnetic interference)
Design Rule Checks (DRC)
Design rule checks help ensure that the PCB layout meets the manufacturing requirements. Common DRC checks include:
- Minimum trace width and spacing
- Minimum drill size and spacing
- Solder mask and silkscreen clearance
- Copper pour and thermal relief
- Acute angles and Acid Traps
Perform DRC checks regularly during the layout process to catch and fix any issues early on.
Manufacturing
Once the PCB design is complete and has passed all DRC checks, it’s ready for manufacturing. Provide clear and complete manufacturing files, including:
- Gerber Files
- Drill files
- Bill of Materials (BOM)
- Assembly drawings
Communicate with the manufacturing partner to ensure they have all the necessary information to fabricate and assemble the PCB correctly.
PCB design guidelines
Now that we have an understanding of the PCB design process, let’s dive into specific guidelines for creating high-quality PCBs.
Board Size and Shape
The size and shape of the PCB should be determined based on the enclosure and mechanical requirements of the final product. Consider the following:
- Available space in the enclosure
- Mounting holes and mechanical supports
- Connector and user interface locations
- Manufacturing constraints (e.g., panelization)
Choose a board size and shape that balances functionality, manufacturability, and cost.
Layer Stack-up
The layer stack-up refers to the arrangement of copper layers and insulating materials in the PCB. A typical stack-up consists of the following layers:
Layer | Description |
---|---|
Top Layer | Components and signals |
Ground Plane | Provides a low-impedance return path for signals |
Power Plane | Distributes power to components |
Bottom Layer | Components and signals |
Additional layers can be added as needed for more complex designs. Choose a stack-up that provides good signal integrity, power distribution, and manufacturability.
Component Placement
Proper component placement is critical for signal integrity, manufacturability, and ease of assembly. Follow these guidelines:
- Group related components together
- Place components on a grid for easy pick-and-place assembly
- Orient components in the same direction when possible
- Provide adequate spacing between components for ease of assembly and rework
- Consider the placement of heat-generating components and provide appropriate thermal management
Routing and Trace Design
Routing is the process of connecting components with traces on the PCB. Follow these guidelines for effective routing:
- Use appropriate trace widths based on the current requirements and manufacturing constraints
- Provide adequate spacing between traces to minimize crosstalk and EMI
- Route critical signals first, such as clocks and high-speed signals
- Use appropriate via sizes and spacing
- Avoid routing traces under components or through mounting holes
- Use curved traces instead of sharp angles to minimize signal reflections
Power and Ground Distribution
Proper power and ground distribution is essential for the stability and performance of the PCB. Follow these guidelines:
- Use dedicated power and ground planes when possible
- Provide adequate decoupling capacitors near power pins of components
- Use appropriate via sizes and spacing for power and ground connections
- Avoid splitting power or ground planes unless necessary
- Use star routing for power distribution to minimize voltage drops
Signal Integrity
Signal integrity refers to the quality of the electrical signals on the PCB. Poor signal integrity can lead to issues such as crosstalk, reflections, and EMI. Follow these guidelines to maintain good signal integrity:
- Use appropriate trace widths and spacing for the signal frequency and rise time
- Minimize the distance between components to reduce the trace length
- Use termination resistors for high-speed signals to minimize reflections
- Avoid routing signals near power or ground planes to minimize crosstalk
- Use ground planes to provide a low-impedance return path for signals
Electromagnetic Compatibility (EMC)
EMC refers to the ability of the PCB to operate without causing or being affected by electromagnetic interference. Follow these guidelines to improve EMC:
- Provide proper shielding for sensitive components and signals
- Use appropriate grounding techniques, such as ground planes and shielding
- Minimize the loop area of current paths to reduce radiated emissions
- Use filters and suppressors to minimize conducted emissions
- Follow regulatory guidelines for EMC, such as FCC and CE requirements
Thermal Management
Thermal management is important for the reliability and longevity of the PCB. Follow these guidelines for effective thermal management:
- Identify heat-generating components and provide appropriate heatsinks or Thermal Pads
- Use appropriate copper pour and thermal vias to dissipate heat
- Consider the use of thermal interface materials (TIM) between components and heatsinks
- Provide adequate airflow for convection cooling
Manufacturing Considerations
Designing a PCB with manufacturing in mind can save time, cost, and improve the overall quality of the final product. Consider the following manufacturing guidelines:
- Use standard component sizes and packages when possible
- Provide adequate spacing between components and traces for ease of assembly
- Use appropriate solder mask and silkscreen clearance
- Follow the manufacturer’s guidelines for minimum trace width, spacing, and drill sizes
- Consider the use of panelization for efficient manufacturing
Frequently Asked Questions (FAQ)
- What is the difference between a schematic and a PCB layout?
-
A schematic is a diagram that represents the electrical connections between components, while a PCB layout is the physical arrangement of components and traces on the board.
-
What is the purpose of a ground plane in a PCB?
-
A ground plane provides a low-impedance return path for signals, helps reduce EMI, and improves signal integrity.
-
What is the importance of DRC in PCB design?
-
DRC (Design Rule Check) helps ensure that the PCB layout meets the manufacturing requirements, such as minimum trace width, spacing, and drill sizes. It catches and fixes issues early in the design process.
-
How can I improve the signal integrity of my PCB?
-
To improve signal integrity, use appropriate trace widths and spacing, minimize the distance between components, use termination resistors for high-speed signals, and provide a low-impedance return path using ground planes.
-
What are some common manufacturing considerations for PCB design?
- Common manufacturing considerations include using standard component sizes and packages, providing adequate spacing between components and traces, following the manufacturer’s guidelines for minimum trace width and spacing, and considering the use of panelization for efficient manufacturing.
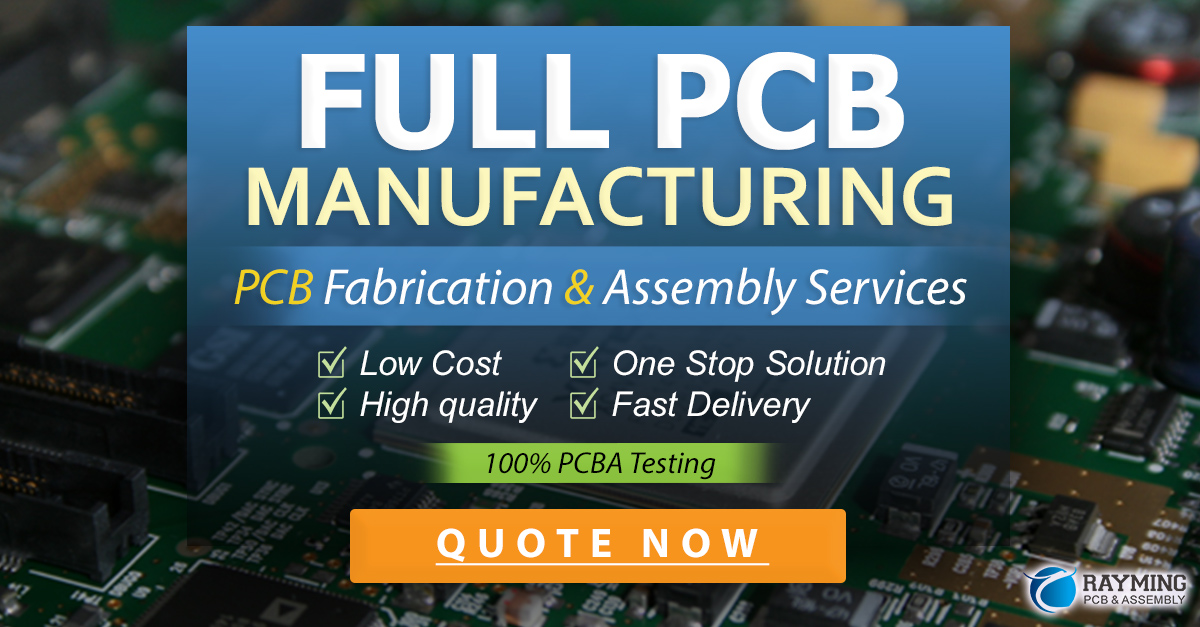
Conclusion
Designing a high-quality PCB requires careful consideration of various factors, from schematic design to manufacturing. By following the guidelines discussed in this article, you can create PCBs that are reliable, functional, and manufacturable. Remember to consider the specific requirements of your project and consult with experienced PCB designers and manufacturers when needed. With proper planning and execution, you can bring your electronic product ideas to life with well-designed PCBs.
Leave a Reply