Introduction to PCB Classification
Printed Circuit Boards (PCBs) are essential components in modern electronic devices, providing a platform for electrical connections and mechanical support. To ensure proper functionality and reliability, PCBs are classified based on various criteria, including the pattern class and drill class. These classifications help manufacturers and designers determine the appropriate fabrication processes, materials, and quality control measures required for a specific PCB design.
In this article, we will delve into the intricacies of PCB classification, focusing on pattern class and drill class. We will explore the definitions, standards, and implications of these classifications, enabling readers to make informed decisions when designing and manufacturing PCBs.
Understanding Pattern Class
What is Pattern Class?
Pattern class, also known as conductor width and spacing, refers to the minimum width of the copper traces and the minimum spacing between them on a PCB. It is a crucial factor in determining the manufacturability and performance of a PCB.
The pattern class is typically defined by a combination of a letter and a number, such as Class 2, Class 3, or Class 4. The higher the class number, the smaller the minimum trace width and spacing, indicating a more precise and complex PCB design.
IPC Standards for Pattern Class
The IPC (Association Connecting Electronics Industries) is a global trade association that develops standards for the electronic interconnect industry. IPC-6012, a widely recognized standard, defines the requirements for PCB pattern classes.
According to IPC-6012, the pattern classes are categorized as follows:
Pattern Class | Minimum Trace Width | Minimum Spacing |
---|---|---|
Class 1 | 0.2 mm (0.008 in) | 0.2 mm (0.008 in) |
Class 2 | 0.1 mm (0.004 in) | 0.1 mm (0.004 in) |
Class 3 | 0.075 mm (0.003 in) | 0.075 mm (0.003 in) |
Class 4 | 0.05 mm (0.002 in) | 0.05 mm (0.002 in) |
It is essential to note that these values are minimum requirements, and designers can choose to use larger trace widths and spacings based on their specific design needs.
Factors Affecting Pattern Class Selection
When selecting the appropriate pattern class for a PCB design, several factors must be considered:
-
Circuit Complexity: More complex circuits with high component density may require a higher pattern class to accommodate the smaller trace widths and spacings.
-
Signal Integrity: High-speed or high-frequency signals may demand a higher pattern class to minimize signal integrity issues such as crosstalk and electromagnetic interference (EMI).
-
Manufacturing Capabilities: The chosen pattern class must be compatible with the manufacturing capabilities of the PCB fabricator. Higher pattern classes require more advanced manufacturing processes and equipment.
-
Cost: Higher pattern classes typically result in higher manufacturing costs due to the increased precision and specialized equipment required.
Designers must strike a balance between these factors to select the most suitable pattern class for their PCB design.
Understanding Drill Class
What is Drill Class?
Drill class refers to the minimum hole size and the associated tolerances for the drilled holes on a PCB. These holes are used for component leads, vias, and mounting purposes. The drill class determines the accuracy and precision of the drilled holes, which is crucial for ensuring proper component fit and reliable electrical connections.
IPC Standards for Drill Class
IPC-6012 also defines the requirements for PCB drill classes. The drill classes are categorized based on the hole size range and the associated tolerances.
Drill Class | Hole Size Range | Tolerance |
---|---|---|
Class 1 | > 0.8 mm | ± 0.15 mm |
Class 2 | 0.4 mm – 0.8 mm | ± 0.1 mm |
Class 3 | 0.2 mm – 0.4 mm | ± 0.05 mm |
Class 4 | < 0.2 mm | ± 0.025 mm |
The tolerances specified in the table represent the maximum allowable deviation from the nominal hole size. Tighter tolerances require more precise drilling processes and equipment.
Factors Affecting Drill Class Selection
When choosing the appropriate drill class for a PCB design, designers must consider the following factors:
-
Component Requirements: The hole sizes and tolerances must accommodate the leads of the components used in the design. Smaller components may require a higher drill class for accurate hole placement.
-
Layer Count: Multi-layer PCBs with a higher number of layers may require a higher drill class to ensure proper registration and alignment of the drilled holes across all layers.
-
Manufacturing Capabilities: The selected drill class must be compatible with the drilling capabilities of the PCB fabricator. Higher drill classes demand more precise drilling equipment and processes.
-
Cost: Similar to pattern class, higher drill classes generally result in higher manufacturing costs due to the increased precision and specialized equipment required.
Designers must carefully evaluate these factors to select the most appropriate drill class for their PCB design, balancing performance, manufacturability, and cost.
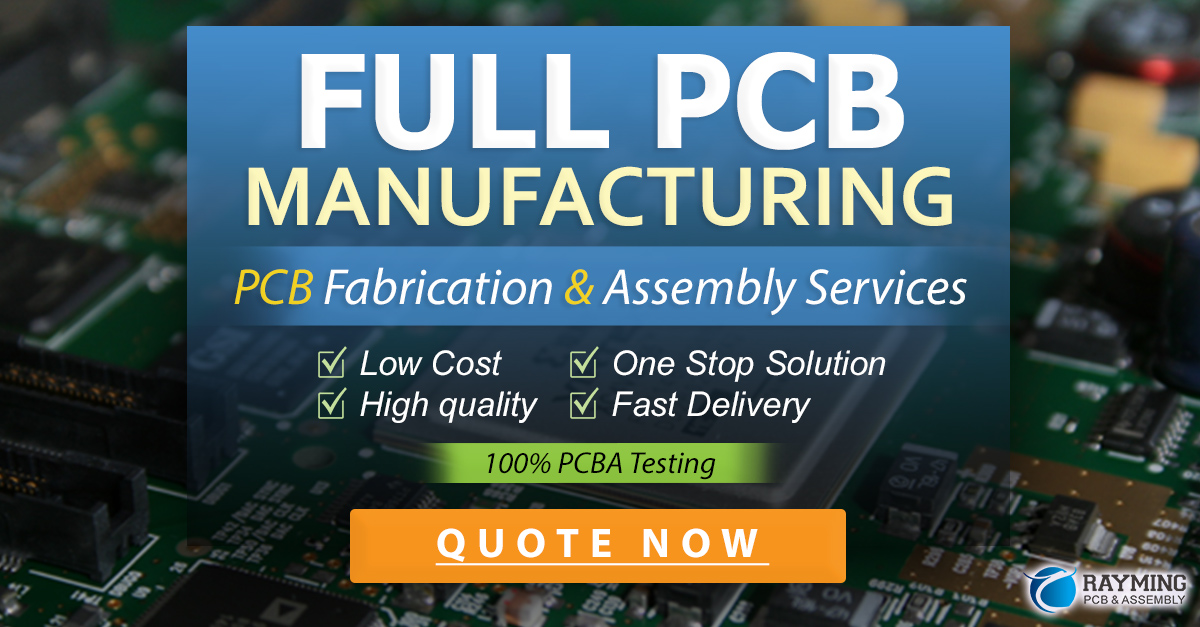
PCB Classification and Manufacturing Process
Impact on Manufacturing Process
The chosen pattern class and drill class have a significant impact on the PCB manufacturing process. Higher classes require more advanced equipment, tighter process controls, and skilled operators to achieve the necessary precision and accuracy.
-
Etching: Higher pattern classes demand more precise Etching Processes to achieve the smaller trace widths and spacings. This may involve using advanced etching techniques such as plasma etching or laser direct imaging (LDI).
-
Drilling: Higher drill classes require more accurate and precise drilling equipment, such as computer numerical control (CNC) drilling machines with high-speed spindles and fine drill bits.
-
Plating: The plating process must be carefully controlled to ensure uniform coverage and avoid any defects, especially in high-aspect-ratio holes associated with higher drill classes.
-
Inspection: More stringent inspection procedures are necessary for higher pattern and drill classes to verify that the manufactured PCB meets the specified requirements. This may involve using automated optical inspection (AOI) systems and electrical testing.
Quality Control and Testing
To ensure the quality and reliability of PCBs, manufacturers employ various quality control measures and testing procedures based on the pattern class and drill class.
-
Visual Inspection: PCBs are visually inspected for any surface defects, such as scratches, dents, or discoloration, which may affect their performance.
-
Automated Optical Inspection (AOI): AOI systems use high-resolution cameras and image processing algorithms to detect any manufacturing defects, such as short circuits, open circuits, or missing components.
-
Electrical Testing: PCBs undergo electrical testing to verify their functionality and performance. This may include Continuity Testing, insulation resistance testing, and high-potential (hipot) testing.
-
Microsectioning: In some cases, microsectioning may be performed to examine the cross-section of the PCB, verifying the integrity of the copper traces, drilled holes, and plated through-holes.
Rigorous quality control and testing procedures help ensure that the manufactured PCBs meet the specified pattern class and drill class requirements, guaranteeing their reliability and performance in the intended application.
Choosing the Right PCB Classification
Considerations for Designers
When designing a PCB, it is crucial to select the appropriate pattern class and drill class based on the specific requirements of the application. Designers should consider the following factors:
-
Functionality: The PCB design must meet the functional requirements of the intended application, including signal integrity, power distribution, and thermal management.
-
Manufacturing Feasibility: The chosen pattern class and drill class must be compatible with the manufacturing capabilities of the PCB fabricator. Designers should consult with the fabricator to ensure that the design can be manufactured reliably and cost-effectively.
-
Cost: Higher pattern and drill classes generally result in higher manufacturing costs. Designers should strive to find a balance between the required performance and the associated costs, selecting the lowest suitable class that meets the design requirements.
-
Time-to-Market: The complexity of the PCB design and the selected classification can impact the manufacturing lead time. Designers should factor in the time-to-market constraints when choosing the pattern class and drill class.
Collaborating with PCB Fabricators
Effective collaboration between PCB designers and fabricators is essential for ensuring the successful manufacturing of PCBs. Designers should engage with fabricators early in the design process to discuss the feasibility of the chosen pattern class and drill class, as well as any potential design improvements or optimizations.
Fabricators can provide valuable insights into the manufacturing process, suggesting alternative materials, processes, or design modifications that can enhance the manufacturability and reliability of the PCB. This collaborative approach helps minimize design iterations, reduces manufacturing risks, and ultimately leads to a more successful product.
Frequently Asked Questions (FAQ)
-
Q: What is the difference between pattern class and drill class in PCB classification?
A: Pattern class refers to the minimum trace width and spacing on a PCB, while drill class refers to the minimum hole size and associated tolerances for the drilled holes. Pattern class determines the precision of the copper traces, while drill class determines the accuracy of the drilled holes. -
Q: How does the choice of pattern class and drill class affect the manufacturing cost of a PCB?
A: Higher pattern and drill classes typically result in higher manufacturing costs due to the increased precision and specialized equipment required. Designers must balance the required performance with the associated costs, selecting the lowest suitable class that meets the design requirements. -
Q: Can a PCB have different pattern classes and drill classes on different layers?
A: Yes, it is possible to have different pattern classes and drill classes on different layers of a multi-layer PCB. This allows designers to optimize the design for specific requirements, such as using a higher pattern class for high-speed signals on certain layers while using a lower class on other layers to reduce costs. -
Q: What are the consequences of selecting an inappropriately low pattern class or drill class for a PCB design?
A: Selecting an inappropriately low pattern class or drill class can lead to manufacturing issues, such as short circuits, open circuits, or poor component fit. This can result in reduced reliability, performance issues, and potential product failures. It is essential to choose the appropriate classification based on the design requirements and manufacturing capabilities. -
Q: How can PCB designers ensure that their design is compatible with the chosen pattern class and drill class?
A: PCB designers should collaborate closely with PCB fabricators throughout the design process. Fabricators can provide guidance on the manufacturability of the chosen pattern class and drill class, suggesting any necessary design modifications or optimizations. Designers should also adhere to the relevant IPC standards and guidelines to ensure compliance with the selected classification.
Conclusion
PCB classification based on pattern class and drill class is a critical aspect of PCB design and manufacturing. Understanding the definitions, standards, and implications of these classifications enables designers to make informed decisions, balancing performance, manufacturability, and cost.
By selecting the appropriate pattern class and drill class, designers can ensure that their PCB design meets the functional requirements of the intended application while being compatible with the manufacturing capabilities of the PCB fabricator. Effective collaboration between designers and fabricators throughout the design process is essential for optimizing the PCB design and minimizing manufacturing risks.
As PCB technology continues to advance, with increasing complexity and miniaturization, the importance of accurate PCB classification becomes even more significant. Designers must stay up-to-date with the latest industry standards and best practices to create reliable, high-performance PCBs that meet the evolving demands of modern electronic devices.
Leave a Reply