What is PCB Warpage?
PCB warpage is the deviation of a PCB from its intended flat shape. It occurs when the board experiences uneven stress or thermal expansion, causing it to bend or twist. The warpage can be classified into two types:
- Convex Warpage: The PCB bends outward, forming a dome-like shape.
- Concave Warpage: The PCB bends inward, creating a bowl-like shape.
The severity of warpage is measured in terms of the maximum deviation from the flat plane, typically expressed in millimeters or mils (thousandths of an inch).
Reasons for PCB Warpage
Several factors can contribute to PCB warpage. Understanding these reasons is crucial for implementing effective prevention and treatment strategies.
1. Thermal Stress
One of the primary causes of PCB warpage is thermal stress. During the manufacturing process, PCBs undergo various heating and cooling cycles, such as soldering, reflow, and curing. The different materials used in PCB construction, such as the substrate, copper layers, and solder mask, have different coefficients of thermal expansion (CTE). When subjected to temperature changes, these materials expand and contract at different rates, leading to internal stresses and potential warpage.
2. Moisture Absorption
PCBs are susceptible to moisture absorption, especially if they are exposed to humid environments or not properly stored. When moisture is absorbed by the PCB substrate, it can cause the board to swell and deform. This is particularly problematic during the reflow soldering process, where the rapid heating can cause the moisture to vaporize, resulting in delamination, blistering, and warpage.
3. Unbalanced Copper Distribution
The copper layers on a PCB play a crucial role in its structural integrity. An unbalanced distribution of copper, where one side of the board has significantly more copper than the other, can lead to warpage. This is because the side with more copper expands and contracts at a different rate than the side with less copper, causing the board to bend.
4. Mechanical Stress
Mechanical stress can also contribute to PCB warpage. This can occur during the handling, transportation, or assembly of the PCBs. Improper handling techniques, such as bending or twisting the board, can introduce stresses that lead to permanent deformation. Additionally, the use of excessive force during component placement or the application of uneven pressure during the assembly process can cause warpage.
5. Design Factors
The design of the PCB itself can influence its susceptibility to warpage. Factors such as the board thickness, aspect ratio (length to width ratio), and the placement of components can all play a role. Thin PCBs are more prone to warpage compared to thicker boards, as they have less structural rigidity. High aspect ratio boards, where the length is significantly greater than the width, are also more susceptible to warpage due to their increased flexibility.
Treatment Methods for PCB Warpage
To address PCB warpage, several treatment methods can be employed. These methods aim to minimize the stresses that cause warpage and restore the board to its intended flat shape.
1. Thermal Management
Proper thermal management is essential for preventing and treating PCB warpage. This involves controlling the temperature profiles during the manufacturing process, particularly during soldering and reflow. Gradual heating and cooling cycles can help reduce thermal stress and minimize warpage. Additionally, using materials with similar CTEs can help maintain the board’s flatness.
2. Moisture Control
Controlling moisture levels is crucial for preventing PCB warpage caused by moisture absorption. This can be achieved through proper storage and handling of the PCBs. Storing PCBs in moisture-barrier bags with desiccants can help maintain low humidity levels. Prior to the reflow process, PCBs should be baked to remove any absorbed moisture, following the manufacturer’s recommended baking procedures.
3. Copper Balancing
To mitigate warpage caused by unbalanced copper distribution, designers can implement copper balancing techniques. This involves adding copper fills or dummy traces on the side with less copper to achieve a more balanced distribution. Copper balancing helps equalize the thermal expansion and contraction of both sides of the PCB, reducing the likelihood of warpage.
4. Mechanical Support
Providing mechanical support to the PCB during the assembly process can help prevent warpage caused by mechanical stress. This can be achieved through the use of fixtures, support pins, or specialized equipment that holds the board flat during component placement and soldering. Proper handling techniques, such as avoiding excessive bending or twisting, should also be practiced to minimize mechanical stress.
5. Design Optimization
Optimizing the PCB design can help reduce the risk of warpage. This includes selecting an appropriate board thickness based on the application requirements and the expected thermal and mechanical stresses. Minimizing the aspect ratio of the board can also improve its resistance to warpage. Additionally, strategic placement of components, such as distributing heavy components evenly across the board, can help balance the stresses and minimize warpage.
6. Post-Warpage Correction
In cases where warpage has already occurred, post-warpage correction methods can be employed. These methods aim to flatten the warped PCB and restore its intended shape. One common technique is to apply controlled heating and pressure to the board, gradually flattening it over time. Specialized equipment, such as a warpage correction press, can be used for this purpose. However, it is important to note that post-warpage correction may not always be feasible or effective, especially if the warpage is severe or has caused permanent damage to the board or components.
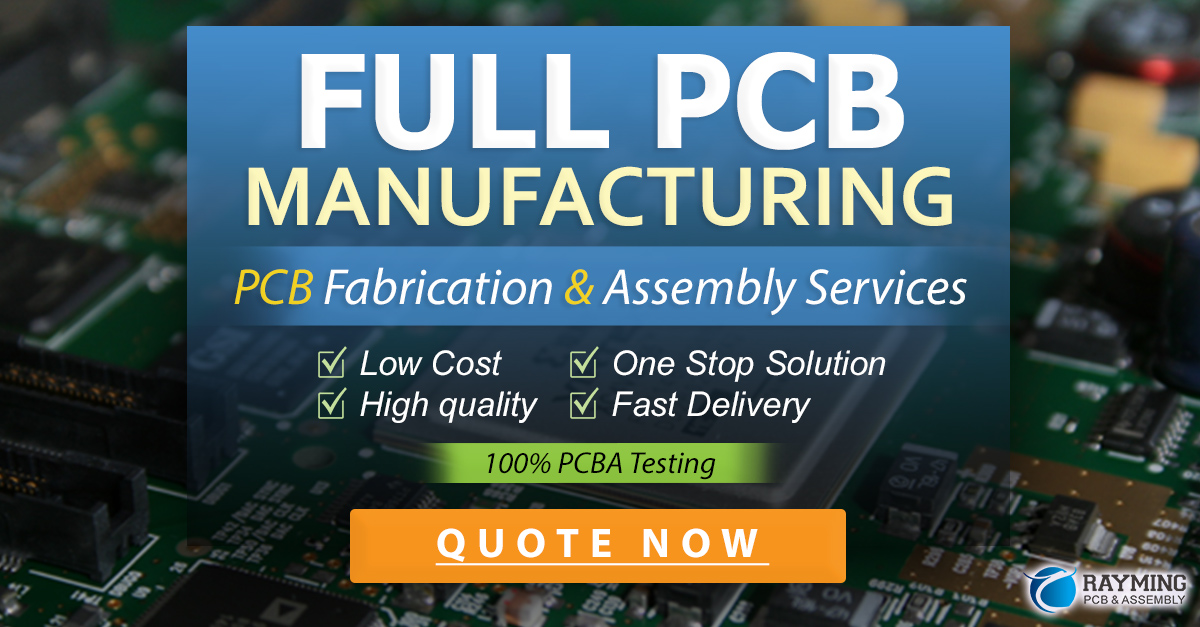
PCB Warpage Standards and Specifications
To ensure the quality and reliability of PCBs, various standards and specifications have been established that address PCB warpage. These standards provide guidelines for acceptable warpage levels and measurement techniques. Some of the key standards related to PCB warpage include:
- IPC-TM-650 2.4.22: Bow and Twist Measurement of Printed Boards
- IPC-6012: Qualification and Performance Specification for Rigid Printed Boards
- IPC-A-600: Acceptability of Printed Boards
Manufacturers and designers should refer to these standards to ensure compliance and maintain the quality of their PCBs.
Prevention is Key
While treatment methods can help address PCB warpage, prevention is always the best approach. By understanding the root causes of warpage and implementing preventive measures during the design and manufacturing stages, manufacturers can minimize the occurrence of warpage and ensure the production of high-quality PCBs.
Some key preventive measures include:
- Selecting materials with similar CTEs
- Implementing proper thermal management during manufacturing
- Controlling moisture levels through appropriate storage and handling
- Balancing copper distribution in the PCB design
- Optimizing the board thickness and aspect ratio
- Providing mechanical support during assembly
- Following industry standards and best practices
By proactively addressing the factors that contribute to PCB warpage, manufacturers can improve the reliability, functionality, and overall quality of their products.
Frequently Asked Questions (FAQ)
-
What is the main cause of PCB warpage?
The main cause of PCB warpage is thermal stress. During the manufacturing process, PCBs are subjected to various heating and cooling cycles, which can lead to uneven expansion and contraction of the different materials used in the board, resulting in warpage. -
How can moisture absorption contribute to PCB warpage?
When PCBs absorb moisture, the substrate can swell and deform. During the reflow soldering process, the rapid heating causes the absorbed moisture to vaporize, leading to delamination, blistering, and warpage. -
What is copper balancing, and how does it help prevent PCB warpage?
Copper balancing is a technique used to achieve a more even distribution of copper on both sides of the PCB. By adding copper fills or dummy traces on the side with less copper, designers can equalize the thermal expansion and contraction of both sides, reducing the likelihood of warpage. -
Can PCB warpage be corrected after it has occurred?
Yes, post-warpage correction methods can be employed to flatten warped PCBs. This typically involves applying controlled heating and pressure to gradually reshape the board. However, the effectiveness of post-warpage correction depends on the severity of the warpage and the potential damage to the board or components. -
What can manufacturers do to prevent PCB warpage?
Manufacturers can take several preventive measures to minimize PCB warpage, including selecting materials with similar CTEs, implementing proper thermal management during manufacturing, controlling moisture levels, balancing copper distribution in the design, optimizing board thickness and aspect ratio, providing mechanical support during assembly, and following industry standards and best practices.
Conclusion
PCB warpage is a significant challenge in the electronics industry, affecting the quality, reliability, and functionality of PCBs. By understanding the reasons behind warpage, such as thermal stress, moisture absorption, unbalanced copper distribution, mechanical stress, and design factors, manufacturers can implement effective treatment methods and preventive measures.
Proper thermal management, moisture control, copper balancing, mechanical support, and design optimization are key strategies for mitigating PCB warpage. Additionally, following industry standards and best practices can help ensure compliance and maintain the quality of PCBs.
By proactively addressing the factors that contribute to PCB warpage, manufacturers can improve the overall performance and reliability of their products, leading to increased customer satisfaction and success in the competitive electronics market.
Leave a Reply