Introduction to PCB Handling
Printed Circuit Boards (PCBs) are the backbone of modern electronics. They are used in almost every electronic device, from smartphones and computers to industrial equipment and medical devices. PCBs are delicate and require careful handling to ensure their reliability and longevity. In this article, we will discuss the best practices for PCB handling, including storage, transportation, and assembly.
What is a PCB?
A PCB is a flat board made of insulating material, such as fiberglass or plastic, with conductive tracks, pads, and other features etched onto its surface. These conductive tracks are used to electrically connect various components, such as resistors, capacitors, and integrated circuits (ICs), to create a functional electronic circuit.
PCBs come in various sizes and shapes, depending on the application. They can be single-sided, double-sided, or multi-layered. Single-sided PCBs have conductive tracks on one side only, while double-sided PCBs have tracks on both sides. Multi-layered PCBs have multiple layers of conductive tracks sandwiched between insulating layers.
Why is PCB Handling Important?
Proper PCB handling is crucial for several reasons:
-
Damage Prevention: PCBs are delicate and can be easily damaged by mishandling. Improper handling can cause physical damage, such as cracks, scratches, or bent components, which can affect the functionality of the PCB.
-
Electrostatic Discharge (ESD) Protection: PCBs are sensitive to ESD, which can cause permanent damage to the components on the board. Proper handling techniques can minimize the risk of ESD damage.
-
Contamination Prevention: PCBs can be contaminated by dust, dirt, oils, and other substances, which can affect their performance and reliability. Proper handling can help prevent contamination and ensure the PCB remains clean.
-
Solderability: Improper handling can affect the solderability of the PCB, making it difficult to assemble components onto the board. This can lead to poor solder joints and reduced reliability.
PCB Storage
Proper storage is essential to ensure the longevity and reliability of PCBs. Here are some best practices for PCB storage:
Storage Environment
PCBs should be stored in a clean, dry, and temperature-controlled environment. The ideal storage temperature range is between 10°C and 30°C (50°F to 86°F), with a relative humidity of 30% to 70%. Extreme temperatures and humidity can cause damage to the PCB and its components.
ESD Protection
PCBs should be stored in ESD-safe packaging, such as ESD bags or boxes, to protect them from electrostatic discharge. ESD bags are made of a conductive material that dissipates any static charge, preventing it from damaging the PCB.
Moisture Protection
PCBs should be stored in moisture-barrier bags (MBBs) to protect them from moisture absorption. MBBs are made of a moisture-resistant material that prevents moisture from penetrating the bag and affecting the PCB. Desiccant packs can also be used inside the MBB to absorb any moisture that may be present.
Stacking and Handling
PCBs should be stacked vertically, with the heaviest boards at the bottom to prevent damage from the weight of the boards above. They should also be handled carefully, avoiding any unnecessary bending or twisting, which can cause physical damage to the board and its components.
Storage Condition | Recommended Range |
---|---|
Temperature | 10°C to 30°C |
Relative Humidity | 30% to 70% |
PCB Transportation
Proper transportation is crucial to ensure PCBs arrive at their destination safely and without damage. Here are some best practices for PCB transportation:
Packaging
PCBs should be packaged in ESD-safe and moisture-resistant packaging, similar to the storage requirements. The packaging should also provide adequate physical protection to prevent damage during transportation.
Labeling
PCBs should be clearly labeled with the necessary information, such as the part number, quantity, and any special handling instructions. This helps ensure the PCBs are handled correctly and reduces the risk of errors during transportation and receiving.
Shipping Method
The shipping method should be chosen based on the sensitivity of the PCBs and the urgency of the delivery. For sensitive or high-value PCBs, it may be necessary to use a specialized courier service that provides additional protection and tracking.
Customs and Regulations
When shipping PCBs internationally, it is important to comply with all relevant customs and regulations. This may include providing the necessary documentation, such as commercial invoices and certificates of origin, and ensuring the PCBs are properly classified and declared.
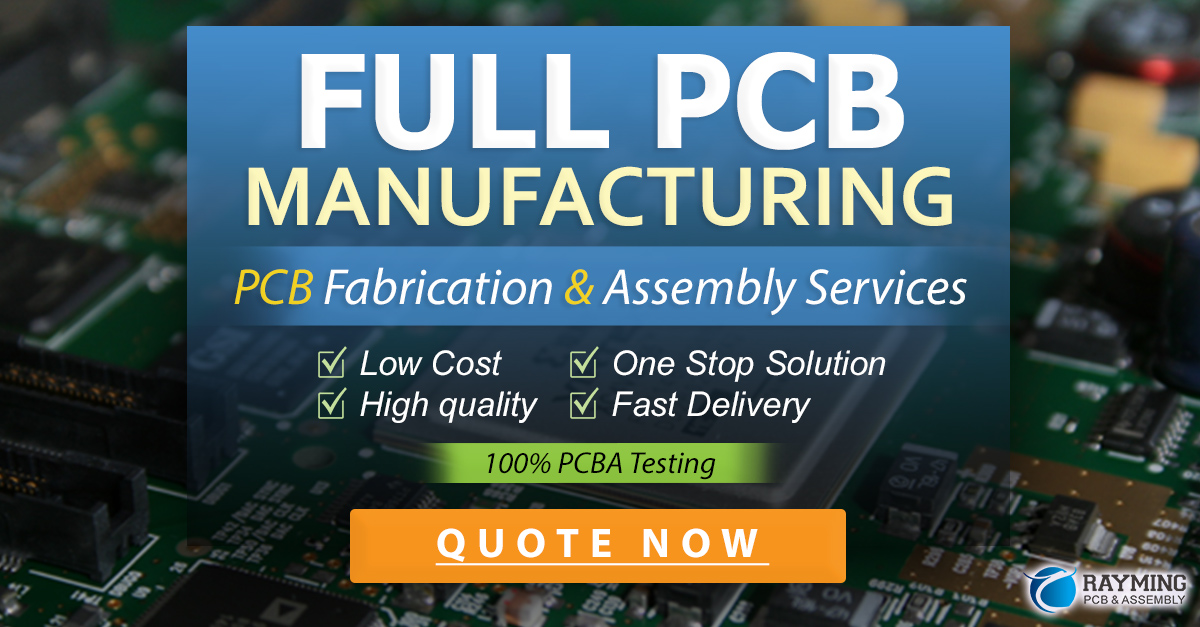
PCB Assembly
PCB assembly is the process of soldering components onto the PCB to create a functional electronic circuit. Proper handling during assembly is critical to ensure the reliability and performance of the finished product.
ESD Protection
ESD protection is crucial during PCB assembly. Assembly personnel should wear ESD-safe clothing, such as ESD smocks and wrist straps, and work on ESD-safe workstations. All tools and equipment used during assembly should also be ESD-safe.
Cleanliness
PCBs should be kept clean during assembly to prevent contamination. Assembly personnel should wear gloves to avoid transferring oils and other contaminants onto the PCB. The work area should also be kept clean and free of dust and debris.
Soldering
Proper soldering techniques are essential for creating reliable solder joints. The soldering iron should be set to the correct temperature for the type of solder being used, and the tip should be kept clean and well-tinned. The solder joint should be heated evenly, and the solder should flow smoothly onto the joint.
Inspection
After assembly, the PCB should be inspected to ensure all components are properly soldered and oriented. Visual inspection can be done using a magnifying glass or microscope, while automated optical inspection (AOI) can be used for larger production runs.
Assembly Step | Key Considerations |
---|---|
ESD Protection | Wear ESD-safe clothing and use ESD-safe equipment |
Cleanliness | Wear gloves and keep work area clean |
Soldering | Use correct temperature and technique |
Inspection | Visually inspect or use automated inspection |
Frequently Asked Questions (FAQ)
1. What is the ideal storage temperature and humidity for PCBs?
The ideal storage temperature range for PCBs is between 10°C and 30°C (50°F to 86°F), with a relative humidity of 30% to 70%. Extreme temperatures and humidity can cause damage to the PCB and its components.
2. Why is ESD protection important for PCBs?
PCBs are sensitive to electrostatic discharge (ESD), which can cause permanent damage to the components on the board. ESD protection, such as using ESD-safe packaging and clothing, helps minimize the risk of ESD damage.
3. What is the purpose of moisture-barrier bags (MBBs) in PCB storage?
MBBs are used to protect PCBs from moisture absorption during storage. They are made of a moisture-resistant material that prevents moisture from penetrating the bag and affecting the PCB. Desiccant packs can also be used inside the MBB to absorb any moisture that may be present.
4. What should I consider when shipping PCBs internationally?
When shipping PCBs internationally, it is important to comply with all relevant customs and regulations. This may include providing the necessary documentation, such as commercial invoices and certificates of origin, and ensuring the PCBs are properly classified and declared.
5. Why is inspection important after PCB assembly?
Inspection after PCB assembly is important to ensure all components are properly soldered and oriented. Visual inspection can be done using a magnifying glass or microscope, while automated optical inspection (AOI) can be used for larger production runs. Inspection helps identify any defects or issues that may affect the functionality or reliability of the PCB.
Conclusion
Proper PCB handling is essential for ensuring the reliability and longevity of electronic devices. From storage and transportation to assembly and inspection, each stage of the PCB lifecycle requires careful attention to detail and adherence to best practices.
By following the guidelines outlined in this article, you can minimize the risk of damage, contamination, and other issues that can affect the performance of your PCBs. This includes using ESD-safe packaging and equipment, storing PCBs in a clean and temperature-controlled environment, and using proper soldering techniques during assembly.
Remember, the success of your electronic products depends on the quality and reliability of your PCBs. By prioritizing PCB handling and following industry best practices, you can ensure your products meet the highest standards of performance and durability.
Leave a Reply