What is Defined Impedance in PCB Design?
Defined impedance, also known as controlled impedance, refers to the precise control of impedance values for PCB Traces and interconnects. Impedance, measured in ohms (Ω), is the total opposition a circuit presents to alternating current. It is determined by the combined effect of resistance, capacitance, and inductance.
In high-speed digital and RF/microwave circuits, it is crucial to maintain consistent impedance across PCB traces to ensure signal integrity and prevent reflections, crosstalk, and electromagnetic interference (EMI). By carefully designing the PCB Stackup, trace widths, spacing, and dielectric materials, engineers can achieve the desired characteristic impedance for each signal path.
Types of Defined Impedance
There are two main types of defined impedance used in PCB design:
-
Single-ended impedance: This refers to the impedance between a signal trace and its corresponding reference plane (usually ground). Common single-ended impedance values include 50Ω, 75Ω, and 100Ω.
-
Differential impedance: This is the impedance between two coupled signal traces, such as in differential pairs used for high-speed interfaces like USB, HDMI, and Ethernet. Typical differential impedance values range from 90Ω to 120Ω.
Factors Affecting Impedance in PCBs
Several factors influence the characteristic impedance of PCB traces:
-
Trace geometry: The width, thickness, and cross-sectional shape of the trace impact its impedance. Wider traces have lower impedance, while narrower traces have higher impedance.
-
Dielectric constant: The dielectric constant (Dk) of the insulating material between the trace and reference plane affects impedance. Higher Dk materials result in lower impedance.
-
Dielectric thickness: The distance between the trace and reference plane, determined by the thickness of the dielectric layer, influences impedance. Thicker dielectrics lead to higher impedance.
-
Trace spacing: For differential pairs, the spacing between the two traces affects the differential impedance and coupling.
-
Copper roughness: The surface roughness of the copper traces can impact impedance, especially at higher frequencies.
Designing for Defined Impedance
To achieve defined impedance in PCB designs, engineers must follow these steps:
-
Determine the required impedance: Based on the application and interface requirements, identify the target impedance values for single-ended and differential traces.
-
Choose suitable dielectric materials: Select PCB substrate materials with the appropriate Dk and dissipation factor (Df) to meet the impedance and loss requirements.
-
Calculate trace dimensions: Use impedance calculators or simulation tools to determine the trace width, thickness, and spacing needed to achieve the target impedance, considering the chosen dielectric materials and layer stackup.
-
Design the PCB stackup: Arrange the signal, power, and ground layers to minimize crosstalk and EMI while providing adequate reference planes for controlled impedance traces.
-
Route controlled impedance traces: During PCB layout, route the controlled impedance traces according to the calculated dimensions and spacing, ensuring consistent geometry and avoiding discontinuities.
-
Verify the design: Perform impedance simulations and time-domain reflectometry (TDR) analysis to validate the impedance of the routed traces and make any necessary adjustments.
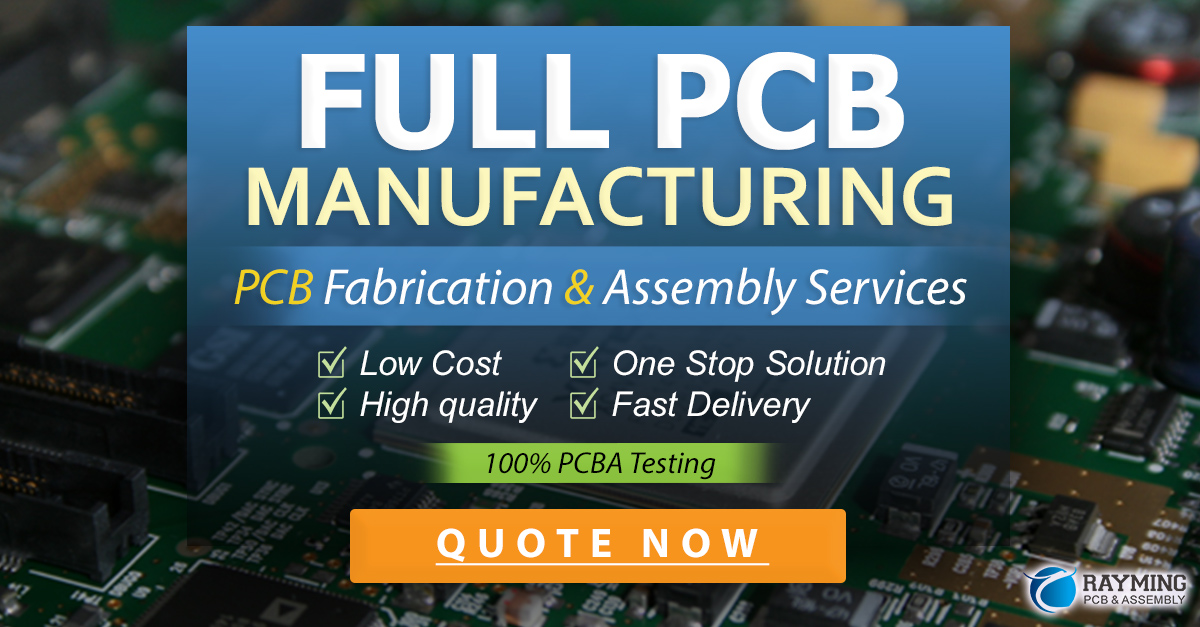
PCB Stackup Considerations for Defined Impedance
The PCB stackup plays a critical role in achieving defined impedance and maintaining signal integrity. Here are some key considerations:
-
Reference planes: Provide uninterrupted reference planes (ground or power) adjacent to controlled impedance traces to establish a clear return path and minimize crosstalk.
-
Dielectric thickness: Choose dielectric thicknesses that allow for practical trace widths while meeting the target impedance. Thinner dielectrics enable narrower traces but may increase manufacturing complexity.
-
Symmetry: For multilayer boards, maintain symmetry in the stackup to balance copper distribution and minimize warpage.
-
Shielding: Use ground planes to shield sensitive controlled impedance traces from external noise sources and crosstalk from other signals.
-
Impedance uniformity: Ensure consistent dielectric thickness and properties across the PCB to maintain uniform impedance for all controlled impedance traces.
Manufacturing Considerations for Defined Impedance PCBs
Fabricating PCBs with defined impedance requires strict process control and specialized equipment. Here are some manufacturing aspects to consider:
-
Tolerances: Specify the acceptable impedance tolerance (e.g., ±10%) for each controlled impedance trace, considering the capabilities of the PCB fabricator.
-
Material selection: Choose PCB materials with consistent dielectric properties and work with the fabricator to ensure the availability and suitability of the selected materials.
-
Plating: Control the plating process to achieve consistent trace thickness and minimize copper roughness, which can affect impedance.
-
Etching: Use advanced etching techniques, such as high-density interconnect (HDI) or modified semi-additive process (mSAP), to achieve precise trace geometries and maintain impedance control.
-
Impedance testing: Request impedance testing from the PCB fabricator to verify that the manufactured board meets the specified impedance requirements.
Simulation and Verification Tools for Defined Impedance
Various software tools are available to simulate, calculate, and verify the impedance of PCB traces. Some popular options include:
-
Impedance calculators: Many PCB design software packages, such as Altium Designer and Cadence Allegro, include built-in impedance calculators that help determine trace dimensions based on the target impedance and stackup parameters.
-
2D field solvers: Tools like Polar Instruments’ Si8000m and Ansys’ 2D Extractor use 2D field-solving techniques to accurately simulate and optimize trace impedance, considering the actual cross-sectional geometry and dielectric properties.
-
3D electromagnetic (EM) simulators: Full-wave 3D EM simulators, such as Ansys HFSS and Keysight EMPro, provide more comprehensive analysis of impedance, crosstalk, and EMI, taking into account the complete PCB geometry and surrounding environment.
-
Time-domain reflectometry (TDR): TDR instruments, like those from Tektronix and Keysight, measure the impedance profile of PCB traces in the time domain, helping to identify discontinuities and validate the actual impedance of the manufactured board.
Collaborating with PCB Fabricators for Defined Impedance
Successful implementation of defined impedance in PCBs requires close collaboration between the design team and the PCB fabricator. Here are some tips for effective collaboration:
-
Early engagement: Involve the PCB fabricator early in the design process to discuss impedance requirements, stackup options, and manufacturing capabilities.
-
Documentation: Provide clear and comprehensive documentation, including the PCB stackup, material specifications, impedance requirements, and tolerance expectations.
-
Design reviews: Conduct design reviews with the fabricator to identify any potential issues or improvements related to impedance control and manufacturability.
-
Feedback and optimization: Incorporate feedback from the fabricator to optimize the design for better impedance control and yields.
Troubleshooting Defined Impedance Issues
If a manufactured PCB fails to meet the specified impedance requirements or experiences signal integrity issues, consider the following troubleshooting steps:
-
Review the stackup: Verify that the actual PCB stackup matches the designed stackup, including dielectric thicknesses, material properties, and layer arrangement.
-
Check trace dimensions: Measure the width, thickness, and spacing of the controlled impedance traces to ensure they align with the designed values.
-
Analyze the TDR profile: Use TDR Measurements to identify any impedance discontinuities or mismatches along the trace length.
-
Simulate with actual parameters: Update the impedance simulations using the measured trace dimensions and dielectric properties to understand the root cause of the impedance mismatch.
-
Collaborate with the fabricator: Work closely with the PCB fabricator to identify and resolve any manufacturing issues that may have led to the impedance deviation.
Best Practices for Defined Impedance PCB Design
To ensure successful defined impedance designs, follow these best practices:
-
Establish clear requirements: Define the impedance requirements for each interface and signal type, considering the operating frequency, rise/fall times, and signal integrity targets.
-
Select appropriate materials: Choose PCB materials with stable dielectric properties, low loss, and suitable Dk for the desired impedance and frequency range.
-
Optimize the stackup: Design a symmetrical and well-balanced stackup that provides the necessary reference planes and dielectric thicknesses for controlled impedance traces.
-
Minimize discontinuities: Avoid abrupt changes in trace geometry, such as sharp bends or width variations, which can cause impedance discontinuities and reflections.
-
Simulate and verify: Use impedance simulation tools to validate the design before manufacturing and perform post-fabrication TDR measurements to ensure compliance with the specified impedance.
-
Document and communicate: Maintain clear documentation of the impedance requirements, stackup, and design decisions, and communicate effectively with the PCB fabricator throughout the process.
Frequently Asked Questions (FAQs)
-
What is the difference between single-ended and differential impedance?
Single-ended impedance refers to the impedance between a signal trace and its reference plane, while differential impedance is the impedance between two coupled traces in a differential pair. -
How does the dielectric constant affect impedance?
The dielectric constant (Dk) of the insulating material between the trace and reference plane impacts the impedance. Higher Dk materials result in lower impedance, while lower Dk materials lead to higher impedance. -
What is the purpose of impedance control in PCB design?
Impedance control ensures consistent and predictable impedance along PCB traces, minimizing signal reflections, crosstalk, and EMI, thereby improving signal integrity and overall system performance. -
How can I determine the right trace dimensions for a specific impedance?
Use impedance calculators or simulation tools that take into account the target impedance, dielectric properties, and stackup parameters to calculate the appropriate trace width, thickness, and spacing. -
What are some common impedance values used in PCB design?
Common single-ended impedance values include 50Ω, 75Ω, and 100Ω, while typical differential impedance values range from 90Ω to 120Ω. The specific impedance value depends on the application, interface standards, and system requirements.
Conclusion
Defined impedance is a critical aspect of modern PCB design, enabling high-speed digital and RF/microwave systems to achieve optimal signal integrity and performance. By carefully controlling the impedance of PCB traces through proper stackup design, material selection, and manufacturing processes, engineers can minimize signal distortion, reflections, and crosstalk.
Successful implementation of defined impedance requires close collaboration between the design team and PCB fabricator, as well as the use of advanced simulation and verification tools. By following best practices and leveraging the expertise of experienced professionals, companies can ensure their PCBs meet the stringent impedance requirements demanded by today’s high-performance electronics.
Leave a Reply