1. Choose the Right PCB Design Software
Selecting the appropriate PCB design software is crucial for creating accurate and efficient PCB layouts. Consider factors such as ease of use, compatibility with your existing tools, and the availability of libraries and components. Some popular PCB design software options include:
Software | Manufacturer | Key Features |
---|---|---|
Altium Designer | Altium | Comprehensive design tools, 3D visualization, and simulation capabilities |
Eagle | Autodesk | User-friendly interface, extensive component libraries, and free version available |
KiCad | Open Source | Free and open-source, cross-platform compatibility, and active community support |
Tips for Choosing PCB Design Software
- Evaluate your design requirements and budget
- Consider the learning curve and available resources
- Look for software with a wide range of component libraries
- Check for compatibility with your manufacturing partners
2. Optimize Your PCB Layout
An optimized PCB layout is essential for ensuring proper functionality, minimizing interference, and facilitating efficient assembly. Follow these guidelines to create a well-designed PCB layout:
- Keep signal traces as short as possible to minimize noise and interference
- Maintain adequate spacing between components and traces to prevent short circuits
- Use ground planes to provide a low-impedance return path and reduce EMI
- Place decoupling capacitors close to power pins to suppress high-frequency noise
- Consider the placement of heat-generating components for optimal thermal management
PCB Layout Optimization Techniques
Technique | Description | Benefits |
---|---|---|
Trace Routing | Route traces using the shortest path while maintaining proper spacing and avoiding sharp angles | Reduces signal integrity issues and improves manufacturing yield |
Ground Planes | Incorporate ground planes on one or more layers of the PCB | Provides a stable reference voltage, reduces EMI, and improves signal integrity |
Component Placement | Place components strategically to minimize trace lengths and optimize signal flow | Enhances performance, reduces noise, and simplifies assembly |
3. Select the Appropriate PCB Materials
The choice of PCB materials can significantly impact the performance, reliability, and cost of your final product. Consider the following factors when selecting PCB materials:
- Dielectric constant and dissipation factor of the substrate material
- Thermal conductivity and coefficient of thermal expansion (CTE)
- Copper weight and trace thickness for current carrying capacity
- Flame retardance and environmental resistance requirements
Common PCB Materials and Their Properties
Material | Dielectric Constant | Dissipation Factor | Thermal Conductivity (W/mK) | CTE (ppm/°C) |
---|---|---|---|---|
FR-4 | 4.2 – 4.5 | 0.02 | 0.3 | 12 – 16 |
Rogers 4003C | 3.38 | 0.0027 | 0.71 | 11 |
Isola 370HR | 4.17 | 0.016 | 0.4 | 12 – 14 |
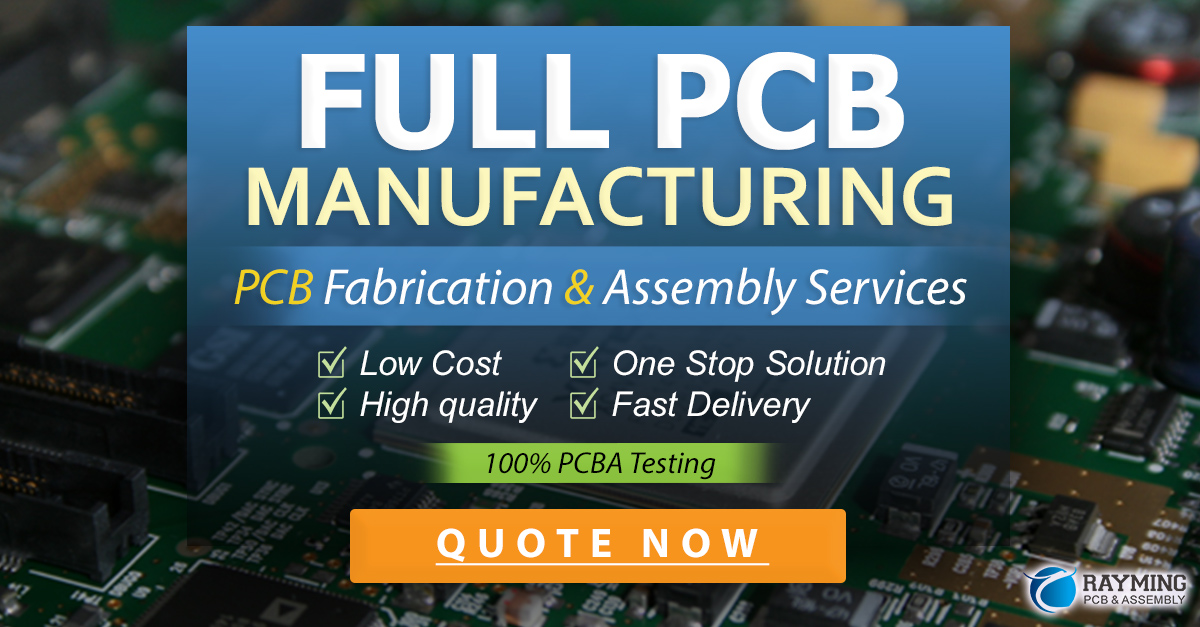
4. Ensure Proper Component Sourcing and Management
Sourcing and managing components is a critical aspect of the PCB Assembly process. Follow these tips to ensure a smooth and efficient component sourcing and management process:
- Use reputable suppliers and distributors to ensure the authenticity and quality of components
- Verify component availability and lead times to avoid delays in the assembly process
- Maintain accurate and up-to-date component inventory records
- Implement a system for tracking and managing component revisions and replacements
Component Sourcing Best Practices
- Establish relationships with multiple suppliers to mitigate supply chain risks
- Regularly review and update your approved vendor list (AVL)
- Implement a component incoming inspection process to ensure quality
- Use automated inventory management systems to track component stock levels and usage
5. Adhere to DFM (Design for Manufacturability) Guidelines
Designing your PCB with manufacturability in mind can significantly improve the efficiency and reliability of the assembly process. Adhere to the following DFM guidelines:
- Use standard component packages and footprints whenever possible
- Maintain adequate spacing between components for automated assembly
- Avoid using components with fine pitch or BGA packages unless necessary
- Provide clear and accurate assembly drawings and documentation
- Collaborate with your manufacturing partners to identify and address potential DFM issues early in the design process
DFM Checklist
- [ ] Use standard component packages and footprints
- [ ] Maintain adequate component spacing
- [ ] Avoid using fine pitch or BGA components unless necessary
- [ ] Provide clear and accurate assembly documentation
- [ ] Collaborate with manufacturing partners for DFM review
6. Implement Rigorous Quality Control Measures
Implementing rigorous quality control measures throughout the PCB assembly process is essential for ensuring the reliability and performance of your final product. Consider the following quality control measures:
- Perform automated optical inspection (AOI) to detect component placement and soldering defects
- Use X-ray inspection for BGA and other hidden solder joints
- Conduct electrical testing to verify functionality and performance
- Implement a traceability system to track components and assemblies throughout the manufacturing process
- Establish a process for identifying and addressing quality issues in a timely manner
Quality Control Methods
Method | Description | Purpose |
---|---|---|
AOI | Automated optical inspection using cameras and image processing software | Detects component placement and soldering defects |
X-ray Inspection | Non-destructive inspection using X-rays to image hidden solder joints | Verifies the integrity of BGA and other hidden solder joints |
Electrical Testing | Functional and performance testing using specialized equipment | Ensures the PCB operates as intended and meets specifications |
7. Foster Clear Communication and Collaboration
Clear communication and collaboration between all stakeholders involved in the PCB assembly process are essential for ensuring a smooth and successful outcome. Consider the following tips for fostering effective communication and collaboration:
- Establish clear lines of communication between design, manufacturing, and quality control teams
- Use a centralized project management system to track progress and share information
- Conduct regular project status meetings to identify and address potential issues
- Encourage open and honest feedback between team members
- Celebrate successes and learn from failures as a team
Communication and Collaboration Best Practices
- Define roles and responsibilities for each team member
- Use a shared project management platform to centralize communication and documentation
- Establish a regular meeting schedule to review project status and address issues
- Encourage a culture of transparency and continuous improvement
- Foster a sense of shared ownership and accountability among team members
8. Stay Up-to-Date with Industry Trends and Technologies
The PCB assembly industry is constantly evolving, with new technologies and best practices emerging regularly. To ensure that your PCB assembly process remains competitive and efficient, stay up-to-date with the latest industry trends and technologies:
- Attend industry conferences and trade shows to learn about new products and techniques
- Participate in online forums and communities to share knowledge and experiences
- Invest in ongoing training and education for your team members
- Explore new technologies such as 3D printing, embedded components, and flexible PCBs
- Continuously evaluate and improve your processes based on industry best practices
Trending Technologies in PCB Assembly
- 3D Printing: Enables rapid prototyping and customization of PCBs
- Embedded Components: Allows for smaller and more compact PCB designs
- Flexible PCBs: Provides increased design flexibility and durability for wearable and IoT applications
- Advanced Materials: Offers improved thermal, electrical, and mechanical properties for high-performance applications
9. Partner with Experienced and Reliable PCB Assembly Providers
Partnering with experienced and reliable PCB assembly providers can significantly streamline your assembly process and ensure the highest quality final product. Consider the following factors when selecting a PCB Assembly Partner:
- Experience and expertise in your specific industry or application
- Quality certifications and standards compliance
- Capacity and flexibility to accommodate your production needs
- Ability to provide value-added services such as design support, testing, and logistics
- Positive references and customer testimonials
Questions to Ask When Choosing a PCB Assembly Partner
- What experience do you have with projects similar to ours?
- What quality certifications and standards do you adhere to?
- How do you ensure the quality and reliability of your assembly process?
- What value-added services do you offer to support our project?
- Can you provide references or case studies of successful projects?
Frequently Asked Questions (FAQ)
1. How do I choose the right PCB design software for my project?
When choosing PCB design software, consider factors such as your design requirements, budget, ease of use, and compatibility with your existing tools and manufacturing partners. Popular options include Altium Designer, Autodesk Eagle, and KiCad.
2. What are some common PCB materials, and how do I select the appropriate one?
Common PCB materials include FR-4, Rogers 4003C, and Isola 370HR. When selecting a material, consider factors such as dielectric constant, dissipation factor, thermal conductivity, and CTE. Choose a material that meets your performance, reliability, and cost requirements.
3. How can I ensure the quality and reliability of my PCB assembly?
To ensure the quality and reliability of your PCB assembly, implement rigorous quality control measures such as AOI, X-ray inspection, and electrical testing. Partner with experienced and reliable PCB assembly providers that adhere to industry quality standards and best practices.
4. What is DFM, and why is it important in PCB assembly?
DFM stands for Design for Manufacturability. It is a set of guidelines and best practices that help ensure your PCB design can be efficiently and reliably manufactured. Adhering to DFM guidelines can improve the quality, yield, and cost-effectiveness of your PCB assembly process.
5. How can I stay up-to-date with the latest trends and technologies in PCB assembly?
To stay up-to-date with the latest trends and technologies in PCB assembly, attend industry conferences and trade shows, participate in online forums and communities, invest in ongoing training and education, and continuously evaluate and improve your processes based on industry best practices.
By following these nine tips and best practices, you can ensure a smooth and successful PCB assembly process that results in high-quality, reliable, and cost-effective products. Remember to prioritize communication, collaboration, and continuous improvement throughout the entire process, and don’t hesitate to seek guidance and support from experienced professionals and partners in the industry.
Leave a Reply