What is PCA Electronics?
PCA Electronics, or Printed Circuit Assembly Electronics, refers to the process of assembling electronic components onto a printed circuit board (PCB) to create a functional electronic device. PCBs are the foundation of modern electronics and are used in a wide range of applications, from consumer gadgets to industrial equipment and aerospace systems.
The Importance of PCA Electronics
PCA Electronics plays a crucial role in the electronics industry for several reasons:
- Miniaturization: PCBs allow for the compact and efficient packaging of electronic components, enabling the creation of smaller, more portable devices.
- Reliability: Well-designed and manufactured PCBs ensure reliable connections between components, reducing the risk of failures and malfunctions.
- Mass Production: PCA Electronics enables the mass production of electronic devices, making them more affordable and accessible to consumers.
- Customization: PCBs can be designed and tailored to meet specific requirements, allowing for the creation of unique and specialized electronic devices.
The PCA Electronics Process
The PCA Electronics process involves several key steps:
Step 1: PCB Design
The first step in PCA Electronics is designing the PCB. This involves creating a schematic diagram that shows the interconnections between the electronic components and then translating that schematic into a physical layout of the PCB.
PCB Design Software
Several software tools are available for PCB design, including:
Software | Description |
---|---|
Altium Designer | A comprehensive PCB design software suite used by professionals |
KiCad | A free and open-source PCB design software |
Eagle | A popular PCB design software for hobbyists and small businesses |
OrCAD | A powerful PCB design software used in the industry |
Step 2: PCB fabrication
Once the PCB design is complete, the next step is to fabricate the physical PCB. This involves several sub-steps:
- PCB Material Selection: The most common PCB material is FR-4, a glass-reinforced epoxy laminate. Other materials, such as aluminum or flexible substrates, may be used for specific applications.
- Copper Cladding: A thin layer of copper is laminated onto the PCB material to create the conductive traces that connect the electronic components.
- Etching: The unwanted copper is removed using a chemical etching process, leaving behind the desired conductive traces.
- Drilling: Holes are drilled into the PCB to accommodate through-hole components and to create vias that connect different layers of the PCB.
- Soldermask and Silkscreen: A protective soldermask layer is applied to the PCB, and a silkscreen layer is added to label components and provide assembly instructions.
Step 3: Component Placement
With the fabricated PCB in hand, the next step is to place the electronic components onto the board. This can be done manually for low-volume production or using automated pick-and-place machines for high-volume manufacturing.
Common Electronic Components
Component | Description |
---|---|
Resistors | Passive components that limit current flow |
Capacitors | Passive components that store electrical energy |
Inductors | Passive components that store energy in a magnetic field |
Diodes | Semiconductor devices that allow current to flow in one direction |
Transistors | Semiconductor devices used for amplification and switching |
Integrated Circuits (ICs) | Miniaturized electronic circuits packaged into a single chip |
Step 4: Soldering
After the components are placed, they need to be soldered onto the PCB to create permanent electrical connections. Soldering can be done by hand using a soldering iron or using automated wave soldering or reflow soldering machines.
Soldering Techniques
Technique | Description |
---|---|
Through-Hole Soldering | Components with long leads are inserted through holes in the PCB and soldered on the opposite side |
Surface Mount Soldering | Components are soldered directly onto pads on the surface of the PCB |
Wave Soldering | The PCB is passed over a wave of molten solder, which solders the components to the board |
Reflow Soldering | Solder paste is applied to the PCB, components are placed, and the board is heated to melt the solder and create connections |
Step 5: Inspection and Testing
After soldering, the assembled PCB undergoes inspection and testing to ensure that all connections are properly made and that the device functions as intended.
Inspection Methods
Method | Description |
---|---|
Visual Inspection | A visual check for proper component placement, soldering, and any obvious defects |
Automated Optical Inspection (AOI) | A camera-based system that automatically inspects the PCB for defects |
X-Ray Inspection | Used to detect hidden defects, such as voids in solder joints or misaligned components |
Testing Methods
Method | Description |
---|---|
In-Circuit Testing (ICT) | Checks for proper connectivity and component values using a Bed-of-Nails Test fixture |
Functional Testing | Verifies that the assembled device performs its intended function |
Boundary Scan Testing | Uses built-in test circuitry to test for defects in complex digital ICs |
PCA Electronics Best Practices
To ensure the success of a PCA Electronics project, consider the following best practices:
- Design for Manufacturability (DFM): Design the PCB with manufacturing in mind, following guidelines for component placement, trace widths, and spacing to ensure reliable and cost-effective production.
- Component Selection: Choose components that are readily available, have a long lifecycle, and meet the performance and environmental requirements of the application.
- Documentation: Maintain clear and comprehensive documentation, including schematic diagrams, bill of materials (BOM), and assembly instructions, to ensure accurate and efficient production.
- Quality Control: Implement a robust quality control process, including inspection and testing at various stages of production, to identify and correct any defects or issues.
- Continuous Improvement: Monitor the performance of the assembled devices and gather feedback from users to identify opportunities for improvement in design, manufacturing, or testing processes.
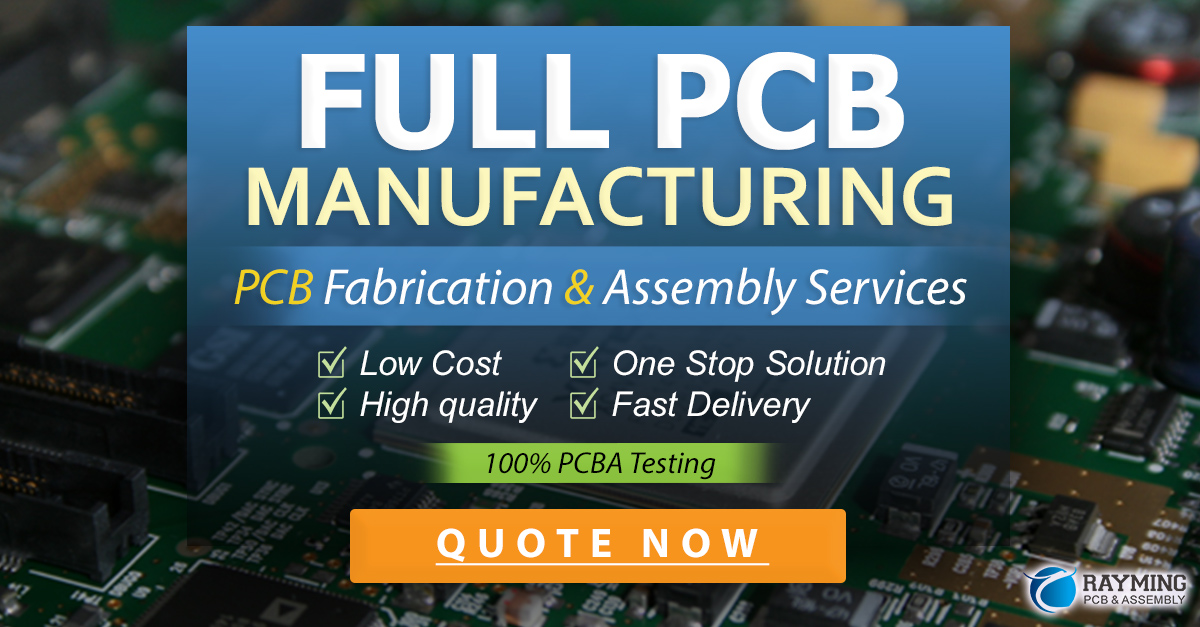
Frequently Asked Questions (FAQ)
-
What is the difference between through-hole and surface mount components?
Through-hole components have long leads that are inserted through holes in the PCB and soldered on the opposite side, while surface mount components are soldered directly onto pads on the surface of the PCB. Surface mount components are generally smaller and more suitable for high-density designs. -
What is the purpose of a soldermask layer on a PCB?
The soldermask layer is a protective coating applied to the PCB that prevents solder from bridging between adjacent traces and pads. It also provides insulation and protects the copper traces from oxidation and damage. -
What is the difference between wave soldering and reflow soldering?
Wave soldering involves passing the PCB over a wave of molten solder, which solders the components to the board. It is typically used for through-hole components. Reflow soldering involves applying solder paste to the PCB, placing the components, and then heating the board to melt the solder and create connections. It is typically used for surface mount components. -
What is the purpose of a bill of materials (BOM) in PCA Electronics?
A bill of materials is a comprehensive list of all the components, materials, and quantities required to assemble a PCB. It is used to ensure that all necessary components are procured and available for production and to track inventory and costs. -
What are some common defects that can occur during PCB Assembly?
Common defects in PCB assembly include solder bridges (unintended connections between adjacent pads or traces), cold solder joints (weak or incomplete solder connections), component misalignment, and damaged or missing components. Proper design, manufacturing processes, and quality control can help minimize these defects.
Conclusion
PCA Electronics is a critical process in the creation of modern electronic devices. By understanding the steps involved in PCB design, fabrication, component placement, soldering, and inspection and testing, engineers and technicians can ensure the production of reliable, high-quality electronic assemblies. Adopting best practices and continuously improving processes can help optimize the efficiency and effectiveness of PCA Electronics projects.
Leave a Reply