Introduction to Single Layer PCB Production
Single layer PCB (Printed Circuit Board) production is a crucial process in the electronics industry. These boards are used in a wide range of applications, from simple consumer devices to complex industrial equipment. Understanding the process of single layer PCB production is essential for anyone involved in the design, manufacturing, or procurement of electronic components.
What is a Single Layer PCB?
A single layer PCB is a circuit board that has only one layer of conductive material, typically copper, on one side of the insulating substrate. The copper layer is etched to form the desired circuit pattern, which connects the various electronic components mounted on the board.
Advantages of Single Layer PCBs
Single layer PCBs offer several advantages over multi-layer boards:
- Lower production costs
- Faster manufacturing process
- Easier to design and modify
- Suitable for simple circuits with fewer components
The Single Layer PCB Production Process
The production of single layer PCBs involves several key steps:
1. PCB Design
The first step in the production process is the design of the PCB. This involves creating a schematic diagram of the circuit and a layout of the components on the board. The design is typically done using specialized PCB design software, such as Altium Designer or Eagle.
2. PCB Fabrication
Once the design is finalized, the PCB fabrication process begins. This involves several sub-steps:
2.1 Substrate Preparation
The insulating substrate, usually made of fiberglass or epoxy, is cut to the desired size and shape. Copper foil is then laminated onto one side of the substrate using heat and pressure.
2.2 Drilling
Holes are drilled into the board to accommodate through-hole components and to create vias for electrical connections between layers (if applicable).
2.3 Patterning
The copper layer is then patterned using a photoresist and UV light exposure. The exposed areas are etched away using a chemical solution, leaving behind the desired circuit pattern.
2.4 Plating
If required, additional copper plating can be applied to the board to increase the thickness of the conductive tracks or to create a solderable surface finish.
3. Component Mounting
After the PCB fabrication is complete, the electronic components are mounted onto the board. This can be done manually or using automated pick-and-place machines. The components are soldered onto the board using either through-hole or surface-mount techniques.
4. Testing and Inspection
The assembled PCB undergoes rigorous testing and inspection to ensure proper functionality and quality. This may include visual inspection, automated optical inspection (AOI), and electrical testing.
Factors Affecting Single Layer PCB Production
Several factors can impact the quality and efficiency of single layer PCB production:
1. Material Selection
Choosing the right materials for the substrate, copper foil, and solder mask is crucial for ensuring the reliability and performance of the final product. Factors to consider include:
- Thermal stability
- Electrical insulation properties
- Mechanical strength
- Cost
2. Manufacturing Equipment
The quality and capability of the manufacturing equipment used in the production process can significantly impact the final product. Key equipment includes:
- PCB fabrication machines (drilling, etching, plating)
- Pick-and-place machines for component mounting
- Soldering equipment (wave soldering, reflow ovens)
- Inspection and testing equipment
3. Quality Control
Implementing strict quality control measures throughout the production process is essential for minimizing defects and ensuring consistent product quality. This may include:
- Incoming material inspections
- In-process inspections at various stages of production
- Final product testing and inspection
4. Operator Skills and Training
The skills and training of the operators involved in the production process can also impact the quality and efficiency of single layer PCB production. Proper training in PCB design, fabrication, assembly, and testing techniques is essential for maintaining high standards.
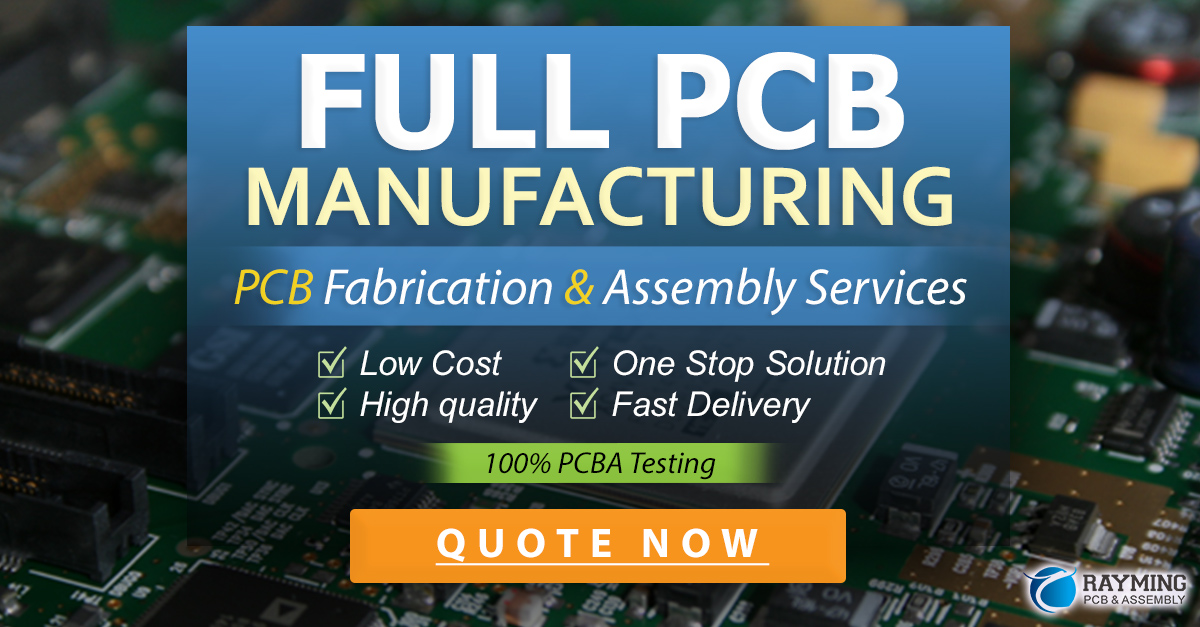
Trends in Single Layer PCB Production
Despite the increasing complexity of modern electronic devices, single layer PCBs remain a vital component in many applications. However, the industry is constantly evolving to meet new challenges and demands:
1. Miniaturization
There is a growing trend towards miniaturization in electronic devices, which requires smaller and more compact PCBs. This has led to the development of advanced fabrication techniques, such as high-density interconnect (HDI) PCBs, which allow for finer pitch components and narrower track widths.
2. Flexible PCBs
Flexible PCBs are gaining popularity in applications that require bendable or conformable circuits, such as wearable devices and automotive electronics. Single layer flexible PCBs can be produced using similar techniques to rigid boards, but with flexible substrate materials like polyimide.
3. Sustainable Production
As environmental concerns grow, there is an increasing focus on sustainable PCB production practices. This includes the use of eco-friendly materials, such as halogen-free substrates and lead-free solders, as well as the adoption of green manufacturing processes that minimize waste and energy consumption.
Frequently Asked Questions (FAQ)
1. What is the typical turnaround time for single layer PCB production?
The turnaround time for single layer PCB production can vary depending on the complexity of the design, the quantity ordered, and the manufacturer’s capacity. However, in general, single layer PCBs can be produced relatively quickly, often within a few days to a week.
2. Can single layer PCBs be used for high-frequency applications?
Single layer PCBs can be used for high-frequency applications, but their performance may be limited compared to multi-layer boards. This is because single layer boards have limited options for controlling impedance and minimizing signal interference. For demanding high-frequency applications, multi-layer PCBs with dedicated power and ground planes are often preferred.
3. What are the most common materials used for single layer PCB substrates?
The most common materials used for single layer PCB substrates are:
- FR-4: A fiberglass-reinforced epoxy laminate, known for its good mechanical and electrical properties, as well as its cost-effectiveness.
- CEM-1: A composite material made of a cellulose paper core with woven glass reinforcement and epoxy resin. It is less expensive than FR-4 but has lower performance.
- Polyimide: A flexible polymer material used for flexible PCBs, offering high heat resistance and excellent mechanical properties.
4. How can I ensure the quality of my single layer PCBs?
To ensure the quality of your single layer PCBs, consider the following:
- Work with a reputable PCB manufacturer with a proven track record of quality and reliability.
- Provide clear and accurate design files, including Gerber files and drill files, to minimize the risk of manufacturing errors.
- Specify your quality requirements and tolerances upfront, and communicate closely with your manufacturer throughout the production process.
- Request a pre-production sample or prototype to verify the quality and functionality of the PCBs before proceeding with full-scale production.
5. Are single layer PCBs suitable for automated assembly?
Yes, single layer PCBs can be suitable for automated assembly, as long as they are designed with the appropriate considerations in mind. This includes:
- Choosing components with package sizes and pitches that are compatible with automated pick-and-place equipment.
- Providing adequate clearances and spacing between components to allow for efficient placement and soldering.
- Specifying the appropriate solder mask and silkscreen markings to facilitate automated optical inspection (AOI) and quality control.
Conclusion
Single layer PCB production remains a critical process in the electronics industry, despite the growing complexity of modern devices. By understanding the key steps involved in the production process, as well as the factors that can impact quality and efficiency, designers and manufacturers can ensure the successful creation of reliable and high-performing single layer PCBs.
As the industry continues to evolve, it is essential to stay informed about new trends and technologies, such as miniaturization, flexible PCBs, and sustainable production practices. By embracing these developments and maintaining a focus on quality and innovation, the single layer PCB production sector can continue to play a vital role in the advancement of the electronics industry.
Leave a Reply