What Makes Military PCBs Different from Commercial PCBs?
Military PCBs differ from their commercial counterparts in several key ways:
- Durability: Military PCBs must be able to withstand extreme conditions, such as high temperatures, humidity, vibration, and shock.
- Reliability: These boards are used in mission-critical applications, so they must have a very low failure rate and a long lifespan.
- Security: Military PCBs often contain sensitive information, so they must be designed and manufactured with security in mind.
- Compliance: Fabrication companies must adhere to strict military standards and regulations, such as MIL-PRF-31032, MIL-PRF-55110, and IPC-6012.
Top Military PCB Fabrication Companies
Several companies specialize in the production of military-grade PCBs. Here are some of the leading fabrication companies in the industry:
Company | Location | Specialties |
---|---|---|
ACE Electrotechnics | Canada | Rigid, flexible, and rigid-flex PCBs |
Advanced Circuits | USA | Quick-turn prototypes and production runs |
Eltek | Israel | High-density interconnect (HDI) and flex-rigid PCBs |
Kinwong Electronic | China | High-reliability, multilayer, and heavy copper PCBs |
Schweizer Electronic AG | Germany | Embedded components and high-frequency PCBs |
These companies have extensive experience in manufacturing PCBs that meet the stringent requirements of the military sector.
Challenges in Military PCB Fabrication
Producing PCBs for the military comes with a unique set of challenges:
- Stringent Standards: Military PCBs must meet rigorous standards, which can be difficult and costly to achieve.
- Specialized Materials: The materials used in military PCBs, such as high-temperature laminates and conformal coatings, can be expensive and difficult to source.
- Long Lead Times: Due to the complex nature of military PCBs and the extensive testing required, lead times can be much longer than for commercial boards.
- Security Concerns: Fabrication companies must have strict security measures in place to protect sensitive information and prevent unauthorized access.
Despite these challenges, military PCB fabrication companies continue to innovate and improve their processes to meet the evolving needs of the defense industry.
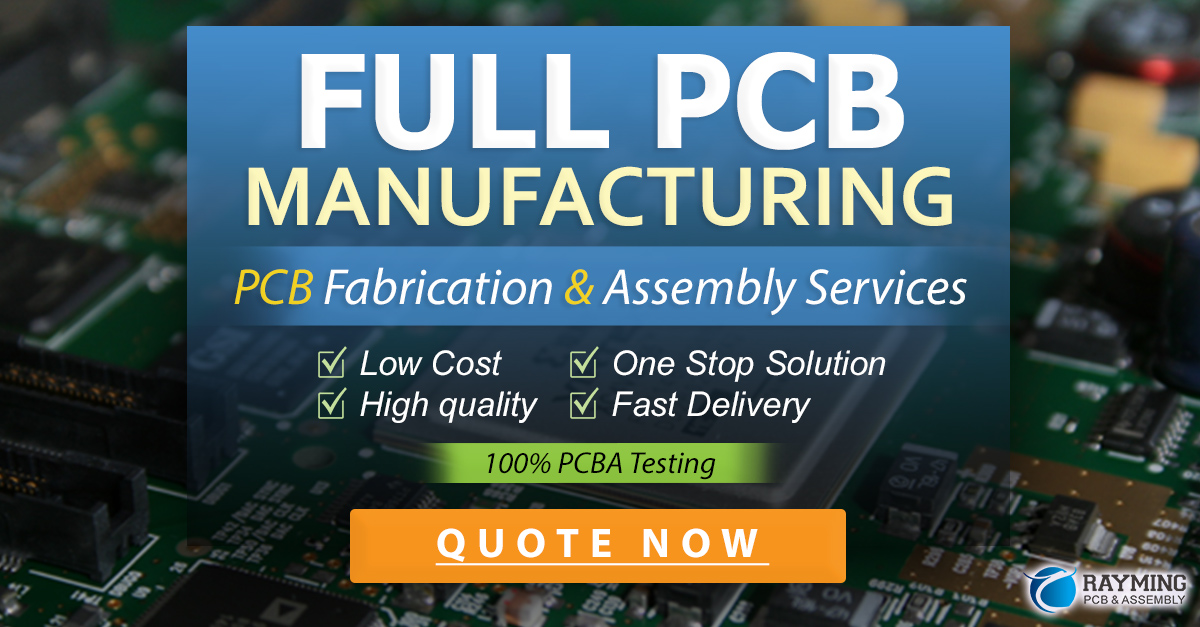
Materials Used in Military PCBs
To ensure the durability and reliability of military PCBs, fabrication companies use a variety of specialized materials:
- High-Temperature Laminates: These materials, such as polyimide and PTFE, can withstand extreme temperatures without degrading.
- Conformal Coatings: Applied to the surface of the PCB, conformal coatings protect against moisture, dust, and other environmental hazards.
- Copper Alloys: High-performance copper alloys, like beryllium copper, offer improved strength and thermal conductivity compared to standard copper.
- Advanced Soldermasks: Military-grade soldermasks provide enhanced protection against chemicals, abrasion, and high temperatures.
The use of these specialized materials contributes to the overall robustness and longevity of military PCBs.
Testing and Certification of Military PCBs
To ensure that military PCBs meet the required standards, fabrication companies conduct extensive testing and certification processes:
- Environmental Testing: PCBs are subjected to various environmental conditions, such as extreme temperatures, humidity, and vibration, to assess their durability.
- Electrical Testing: Boards undergo rigorous electrical testing to verify their functionality and performance.
- X-Ray Inspection: X-ray imaging is used to detect any internal defects or anomalies that may not be visible on the surface.
- Certification: Military PCBs must be certified to the relevant military standards, such as MIL-PRF-31032 and MIL-PRF-55110.
These testing and certification processes help to guarantee the quality and reliability of military PCBs.
Future Trends in Military PCB Fabrication
As technology advances and the needs of the military evolve, PCB fabrication companies must adapt to stay ahead of the curve. Some of the future trends in military PCB fabrication include:
- Miniaturization: The demand for smaller, more compact PCBs continues to grow, driving the development of advanced packaging techniques and high-density interconnects.
- Embedded Components: Integrating components directly into the PCB substrate can save space and improve performance.
- 3D Printing: Additive manufacturing techniques, such as 3D printing, may be used to create complex PCB structures and reduce lead times.
- Increased Automation: Automated manufacturing processes can help to improve consistency, reduce costs, and increase production capacity.
By embracing these trends, military PCB fabrication companies can continue to provide cutting-edge solutions for the defense industry.
Frequently Asked Questions (FAQ)
-
Q: What is the difference between mil-spec and aerospace-grade PCBs?
A: Mil-spec PCBs are designed to meet military standards, while aerospace-grade PCBs are specifically designed for use in aircraft and spacecraft. Aerospace-grade PCBs may have even more stringent requirements than mil-spec boards. -
Q: How long does it typically take to manufacture a military PCB?
A: Lead times for military PCBs can vary depending on the complexity of the design and the required testing and certification. On average, lead times can range from 4 to 12 weeks, but some projects may take longer. -
Q: Can military PCB fabrication companies produce both rigid and flexible PCBs?
A: Yes, many military PCB fabrication companies have the capability to produce both rigid and flexible PCBs, as well as rigid-flex hybrid designs. -
Q: Are there any specific certifications that military PCB fabrication companies must have?
A: Fabrication companies must be certified to produce PCBs that meet military standards, such as MIL-PRF-31032 and MIL-PRF-55110. They may also need to maintain certifications such as ISO 9001 and AS9100. -
Q: How can I ensure that my military PCB design is manufacturable?
A: To ensure manufacturability, it’s essential to work closely with your chosen fabrication company throughout the design process. They can provide guidance on material selection, design rules, and testing requirements to help you create a design that is both functional and manufacturable.
In conclusion, military PCB fabrication is a highly specialized field that requires expertise, advanced materials, and rigorous testing and certification processes. By partnering with experienced fabrication companies and staying informed about the latest trends and technologies, the defense industry can continue to push the boundaries of what is possible with military-grade PCBs.
Leave a Reply