PCB Material Selection
The choice of material for a PCB is crucial, as it affects the board’s electrical, thermal, and mechanical properties. The most common PCB materials include:
FR-4
FR-4 is a glass-reinforced epoxy laminate and the most widely used PCB material. It offers good electrical insulation, mechanical strength, and thermal stability. FR-4 is suitable for most general-purpose applications.
High-Frequency Materials
For high-frequency applications, such as RF and microwave circuits, specialized materials like Rogers, Teflon, and ceramic-based laminates are used. These materials have lower dielectric loss and better-controlled dielectric constant, enabling better signal integrity at high frequencies.
Flexible PCBs
Flexible PCBs use thin, flexible substrates like polyimide or polyester. They are ideal for applications requiring bendability or space constraints, such as wearable devices or compact electronics.
Metal Core PCBs
Metal core PCBs (MCPCBs) have a metal base, usually aluminum, for enhanced thermal dissipation. They are used in high-power applications, such as LED lighting or power electronics, where efficient heat management is critical.
Material | Typical Applications | Key Properties |
---|---|---|
FR-4 | General-purpose electronics | Good insulation, strength, and thermal stability |
High-Frequency | RF, microwave, and high-speed digital circuits | Low dielectric loss, controlled dielectric constant |
Flexible | Wearable devices, compact electronics | Bendability, space savings |
Metal Core | High-power applications, LED lighting | Enhanced thermal dissipation |
PCB Layer Stack-up
The layer stack-up refers to the arrangement of conductive and insulating layers in a PCB. It determines the board’s thickness, impedance control, and signal integrity. Common layer stack-ups include:
Single-Layer PCBs
Single-layer PCBs have one conductive layer, typically used for simple, low-cost projects or prototypes.
Double-Layer PCBs
Double-layer PCBs have two conductive layers, one on each side of the insulating substrate. They offer more routing options and better signal integrity than single-layer boards.
Multi-Layer PCBs
Multi-layer PCBs have three or more conductive layers, separated by insulating layers. They provide even more routing density and better signal integrity, making them suitable for complex designs and high-speed applications.
Layer Count | Typical Applications | Key Benefits |
---|---|---|
Single | Simple projects, prototypes | Low cost, easy to fabricate |
Double | General-purpose electronics | Improved routing, better signal integrity |
Multi | Complex designs, high-speed applications | High routing density, excellent signal integrity |
PCB Trace Width and Spacing
The width and spacing of PCB traces (the conductive paths connecting components) are critical factors in PCB design. They affect the board’s current-carrying capacity, impedance, and manufacturability.
Trace Width
Trace width is determined by the current-carrying requirements and the PCB manufacturing capabilities. Wider traces can carry more current but occupy more space. The IPC-2221 standard provides guidelines for trace width based on current requirements and temperature rise.
Trace Spacing
Trace spacing refers to the distance between adjacent traces. It is dictated by the PCB manufacturing capabilities and the voltage difference between traces. Adequate spacing is necessary to prevent short circuits and ensure reliable operation. The IPC-2221 standard also provides recommendations for trace spacing based on the voltage difference and the PCB material.
Trace Parameter | Key Considerations | Relevant Standards |
---|---|---|
Width | Current-carrying capacity, space constraints | IPC-2221 |
Spacing | Voltage difference, manufacturing capabilities | IPC-2221 |
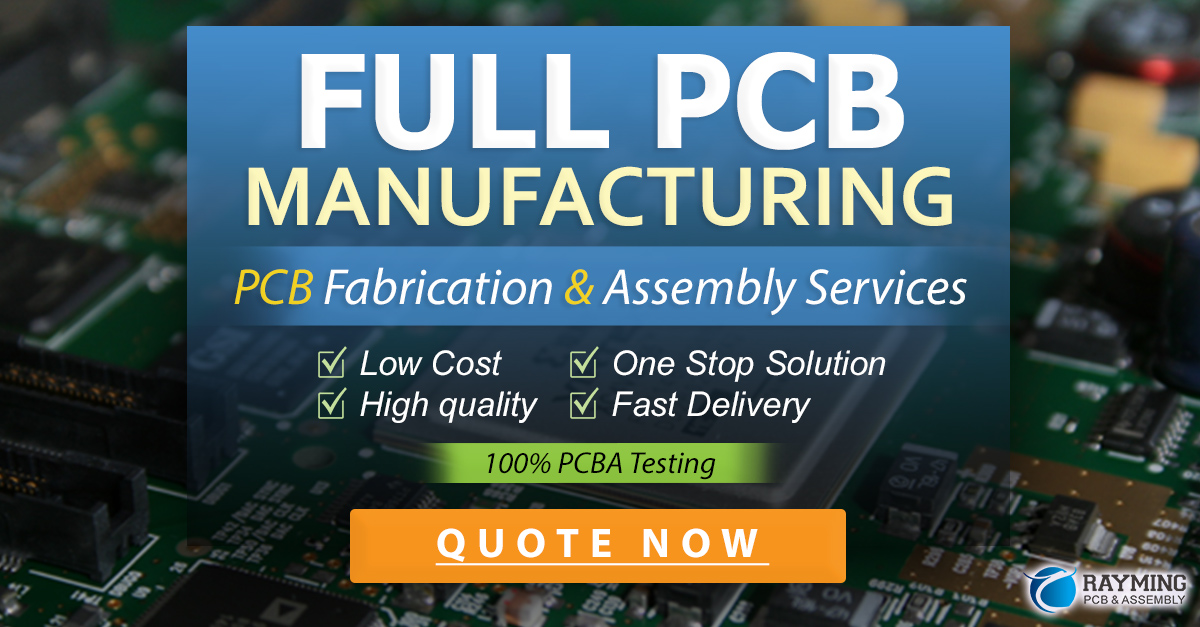
PCB Via Design
Vias are conductive holes that connect different layers of a PCB. They are essential for routing signals and power between layers. The main types of vias include:
Through-Hole Vias
Through-hole vias go through the entire thickness of the PCB. They are the most common and easiest to manufacture but occupy more space than other types.
Blind Vias
Blind vias connect an outer layer to an inner layer but do not go through the entire board thickness. They save space and improve routing density but are more challenging to manufacture.
Buried Vias
Buried vias connect inner layers without reaching either outer layer. They offer the highest routing density but are the most complex and expensive to manufacture.
Via Type | Connects | Key Benefits |
---|---|---|
Through-Hole | All layers | Easy to manufacture, widely available |
Blind | Outer layer to inner layer | Space savings, improved routing density |
Buried | Inner layers only | Highest routing density |
PCB Surface Finish
The surface finish is the coating applied to the exposed copper traces and pads on a PCB. It protects the copper from oxidation and enhances the board’s solderability. Common surface finishes include:
Hot Air Solder Leveling (HASL)
HASL involves dipping the PCB in molten solder and then using hot air to level the solder on the surface. It is a low-cost and widely available finish but results in an uneven surface.
Organic Solderability Preservative (OSP)
OSP is a thin, organic coating that protects the copper. It is inexpensive and easy to apply but has a limited shelf life and may require special handling.
Electroless Nickel Immersion Gold (ENIG)
ENIG consists of a nickel layer covered by a thin gold layer. It provides excellent solderability, flatness, and durability. However, it is more expensive than other finishes.
Finish | Key Properties | Typical Applications |
---|---|---|
HASL | Low cost, widely available, uneven surface | General-purpose electronics |
OSP | Inexpensive, easy to apply, limited shelf life | Consumer electronics, short-term storage |
ENIG | Excellent solderability, flatness, durability | High-reliability applications, long-term storage |
PCB Assembly Methods
The choice of assembly method depends on the components used, the production volume, and the required reliability. The two main assembly methods are:
Through-Hole Assembly
Through-hole assembly involves inserting component leads through holes in the PCB and soldering them on the opposite side. It is suitable for larger components and provides strong mechanical connections. However, it is slower and less automated than surface-mount assembly.
Surface-Mount Assembly
Surface-mount assembly involves placing components directly on the PCB surface and soldering them using reflow or wave soldering processes. It allows for smaller components, higher component density, and faster, more automated assembly. However, it requires more precise component placement and can be more challenging for manual assembly.
Assembly Method | Key Characteristics | Typical Applications |
---|---|---|
Through-Hole | Strong mechanical connections, larger components | High-power electronics, connectors, displays |
Surface-Mount | Smaller components, higher density, faster assembly | Most modern electronics, high-volume production |
Frequently Asked Questions (FAQ)
1. What is the difference between a PCB and a printed wiring board (PWB)?
Printed circuit boards (PCBs) and printed wiring boards (PWBs) are often used interchangeably. However, a PWB technically refers to a board with only conductive traces, while a PCB includes both traces and components.
2. Can I mix through-hole and surface-mount components on the same PCB?
Yes, it is possible to have both through-hole and surface-mount components on the same PCB. This is called a mixed-technology or hybrid assembly. However, it may increase the complexity and cost of the assembly process.
3. What is the difference between a rigid and a flexible PCB?
A rigid PCB uses a solid, inflexible substrate material, such as FR-4. A flexible PCB uses a thin, flexible substrate, such as polyimide. Rigid PCBs are more common and suitable for most applications, while flexible PCBs are used when bendability or space savings are required.
4. How do I choose the right PCB material for my application?
The choice of PCB material depends on factors such as the operating environment, frequency range, thermal requirements, and cost. FR-4 is suitable for most general-purpose applications, while high-frequency materials are used for RF and microwave circuits. Metal core PCBs are used for high-power applications that require efficient heat dissipation.
5. What are the advantages of using blind and buried vias in a PCB?
Blind and buried vias offer several advantages over through-hole vias. They save space on the outer layers, allowing for higher component density and more efficient routing. Blind vias can also improve signal integrity by reducing the via stub effect. However, blind and buried vias are more complex and expensive to manufacture compared to through-hole vias.
In conclusion, the construction of a printed circuit board involves several key factors, including material selection, layer stack-up, trace width and spacing, via design, surface finish, and assembly methods. Understanding these factors and making informed decisions based on the specific application requirements are essential for designing reliable, high-performance PCBs.
Leave a Reply