Introduction to PCB Assembly
Printed Circuit Board (PCB) assembly is the process of attaching electronic components to a PCB to create a functional electronic device. Low volume PCB assembly refers to the production of a small number of PCBs, typically less than 1,000 units. This guide will provide a comprehensive overview of the low volume PCB assembly process, including the steps involved, the equipment and materials required, and best practices for achieving high-quality results.
Why Low Volume PCB Assembly is Important
Low volume PCB assembly is essential for prototyping, testing, and small-scale production of electronic devices. It allows manufacturers to quickly and cost-effectively produce small batches of PCBs without the need for expensive tooling or large minimum order quantities. This flexibility is particularly valuable for startups, hobbyists, and companies developing new products or testing market demand.
The Low Volume PCB Assembly Process
The low volume PCB assembly process consists of several key steps, each of which is critical to achieving a high-quality final product. These steps include:
- PCB Design and Fabrication
- Solder Paste Application
- Component Placement
- Reflow Soldering
- Inspection and Testing
- Conformal Coating and Potting (optional)
Step 1: PCB Design and Fabrication
The first step in the low volume PCB assembly process is to design and fabricate the PCB itself. This involves creating a schematic diagram of the circuit, laying out the components and traces on the board, and generating the necessary files for manufacturing. PCB design software, such as Altium Designer or KiCad, is typically used for this purpose.
Once the design is complete, the PCB is fabricated using a process called photolithography. This involves applying a photoresist coating to a copper-clad substrate, exposing it to light through a photomask, and then etching away the unwanted copper to create the desired circuit pattern. The resulting PCB is then cleaned, drilled, and coated with a protective solder mask and silkscreen layer.
Step 2: Solder Paste Application
The next step in the low volume PCB assembly process is to apply solder paste to the pads on the PCB where the components will be placed. Solder paste is a mixture of tiny solder particles suspended in a flux medium, which helps to clean and prepare the surfaces for soldering.
Solder paste can be applied manually using a syringe or stencil, or automatically using a solder paste printer. The latter method is preferred for low volume PCB assembly, as it ensures a consistent and accurate application of the paste.
Step 3: Component Placement
Once the solder paste has been applied, the next step is to place the components onto the PCB. This can be done manually using tweezers or a pick-and-place machine, depending on the complexity of the board and the number of components involved.
When placing components manually, it is important to ensure that they are oriented correctly and seated properly on the pads. A magnifying glass or microscope can be helpful for this purpose. When using a pick-and-place machine, the components are typically supplied on reels or trays and are automatically placed onto the board using a vacuum nozzle.
Step 4: Reflow Soldering
After the components have been placed, the next step is to reflow solder the board. This involves heating the PCB and components to a temperature high enough to melt the solder particles in the paste, allowing them to flow and form a strong mechanical and electrical connection between the components and the board.
Reflow soldering is typically done using a reflow oven, which precisely controls the temperature profile of the board over time. The temperature profile consists of several stages, including preheat, soak, reflow, and cooling. Each stage is carefully optimized to ensure that the solder melts and flows properly without damaging the components or the board.
Step 5: Inspection and Testing
After the PCB has been reflow soldered, it is important to inspect and test it to ensure that it is functioning properly and meets all of the necessary quality standards. This typically involves a combination of visual inspection, automated optical inspection (AOI), and electrical testing.
Visual inspection involves examining the board under a microscope or magnifying glass to look for any obvious defects or issues, such as bridging, tombstoning, or insufficient solder. AOI uses a camera and computer vision algorithms to automatically detect and classify defects on the board. Electrical testing involves using a variety of test equipment, such as multimeters, oscilloscopes, and function generators, to verify that the board is functioning as intended and meets all of the necessary performance specifications.
Step 6: Conformal Coating and Potting (optional)
In some cases, it may be necessary or desirable to apply a conformal coating or potting material to the PCB to protect it from moisture, dust, or other environmental hazards. Conformal coating is a thin, protective layer that is applied over the surface of the board and components, while potting involves encapsulating the board and components in a thick, protective material such as epoxy or silicone.
Conformal coating and potting can help to improve the reliability and longevity of the PCB, particularly in harsh or demanding environments. However, they also add additional cost and complexity to the assembly process and may not be necessary for all applications.
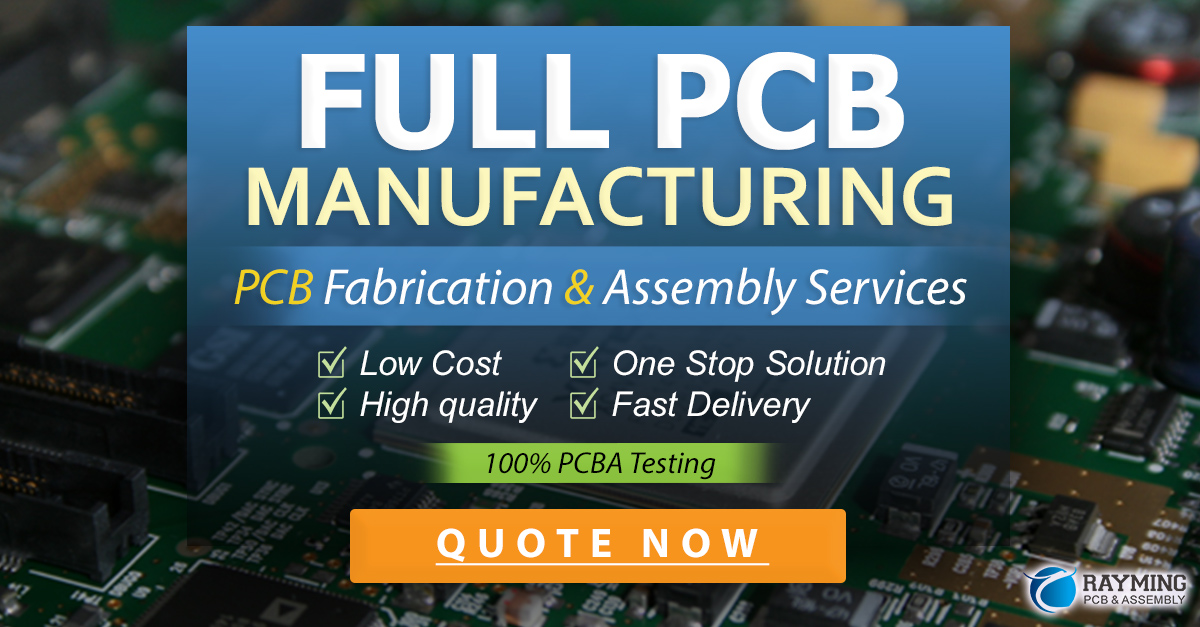
Equipment and Materials Required for Low Volume PCB Assembly
Low volume PCB assembly requires a variety of specialized equipment and materials, including:
- PCB design software
- PCB Fabrication equipment (photolithography, etching, drilling, etc.)
- Solder paste and flux
- Solder paste printer or stencil
- Pick-and-place machine or tweezers
- Reflow oven
- Inspection and testing equipment (microscope, AOI, multimeter, oscilloscope, etc.)
- Conformal coating or potting equipment (optional)
The specific equipment and materials required will depend on the complexity and requirements of the particular PCB being assembled, as well as the volume and budget of the project.
Best Practices for Low Volume PCB Assembly
To ensure the best possible results when performing low volume PCB assembly, it is important to follow a few key best practices:
- Use high-quality components and materials
- Follow proper handling and storage procedures for components and PCBs
- Use a consistent and repeatable process for each step of the assembly
- Carefully control the reflow soldering temperature profile to avoid damaging components or the board
- Perform thorough inspection and testing to identify and correct any issues early in the process
- Document the process and results for future reference and continuous improvement
By following these best practices and carefully controlling each step of the low volume PCB assembly process, it is possible to achieve high-quality, reliable results even with small batch sizes and limited resources.
FAQs
1. What is the minimum order quantity for low volume PCB assembly?
There is no hard and fast rule for the minimum order quantity for low volume PCB assembly, as it can vary depending on the specific supplier and project requirements. However, most low volume PCB assembly services can accommodate orders as small as 1-10 pieces, with some offering even lower minimums for prototyping or testing purposes.
2. How long does low volume PCB assembly typically take?
The lead time for low volume PCB assembly can vary depending on the complexity of the board, the components involved, and the supplier’s workload and capabilities. However, most low volume PCB assembly services can deliver completed boards within 1-2 weeks, with some offering expedited options for faster turnaround times.
3. How much does low volume PCB Assembly Cost?
The cost of low volume PCB assembly can vary widely depending on the complexity of the board, the number of components involved, and the specific supplier and service options chosen. In general, low volume PCB assembly tends to be more expensive on a per-unit basis than high volume production, due to the fixed costs associated with setting up and running the assembly process. However, many low volume PCB assembly services offer competitive pricing and discounts for larger orders or repeat business.
4. What file formats are required for low volume PCB assembly?
Most low volume PCB assembly services require a variety of standard file formats for the PCB design and bill of materials (BOM), including:
- Gerber files (.gbr) for the PCB layout and artwork
- Drill files (.drl) for the hole locations and sizes
- Pick-and-place files (.csv or .txt) for the component placement information
- BOM files (.csv or .xlsx) for the list of components and quantities required
Some suppliers may also require additional files or information, such as assembly drawings, test specifications, or special instructions, depending on the specific requirements of the project.
5. Can low volume PCB assembly be used for production?
While low volume PCB assembly is primarily used for prototyping, testing, and small batch production, it can also be used for larger scale production in some cases. This is particularly true for niche or specialized products with low overall demand, or for products that require frequent design changes or updates. However, for most high volume production applications, it is generally more cost-effective to use dedicated high volume PCB assembly services that can offer lower per-unit costs and faster turnaround times.
Conclusion
Low volume PCB assembly is a critical process for prototyping, testing, and small-scale production of electronic devices. By understanding the steps involved, the equipment and materials required, and the best practices for achieving high-quality results, it is possible to successfully assemble PCBs in small batches with limited resources. Whether you are a startup, hobbyist, or established company, low volume PCB assembly can provide the flexibility and cost-effectiveness needed to bring your electronic product ideas to life.
Leave a Reply