Introduction to PCB Prototypes
Printed Circuit Board (PCB) prototypes are essential for testing and validating electronic designs before mass production. They allow engineers and designers to identify and fix any issues with the circuit design, component placement, and functionality. PCB prototypes are especially crucial for complex designs that require multiple layers and high-density component placement.
In this article, we will discuss low-cost options for creating 1 to 4 layer PCB prototypes, including the advantages and disadvantages of each method. We will also provide tips for optimizing your PCB prototype design and reducing costs without compromising quality.
Understanding PCB Layers
Before diving into the various methods for creating PCB prototypes, it’s important to understand the concept of PCB layers. A PCB layer refers to the number of conductive copper layers within the board. The most common PCB layer configurations are:
- Single Layer (1L): A single conductive layer on one side of the substrate.
- Double Layer (2L): Two conductive layers, one on each side of the substrate.
- Four Layer (4L): Four conductive layers, with two inner layers sandwiched between the top and bottom layers.
As the number of layers increases, so does the complexity and cost of the PCB prototype. However, multi-layer PCBs offer several advantages, such as:
- Increased routing density
- Better signal integrity
- Reduced electromagnetic interference (EMI)
- Improved heat dissipation
Low-Cost PCB Prototype Methods
1. PCB Milling
PCB milling is a subtractive manufacturing process that uses a computer-controlled milling machine to remove copper from a pre-laminated PCB substrate. This method is ideal for creating quick and low-cost PCB prototypes, especially for single or double-layer designs.
Advantages:
– Fast turnaround times
– Low setup costs
– Suitable for small quantities (1-10 pieces)
– Allows for easy design modifications
Disadvantages:
– Limited to 1-2 layers
– Lower precision compared to other methods
– Not suitable for high-density designs or fine-pitch components
2. PCB etching
PCB etching is a chemical process that removes unwanted copper from a PCB substrate, leaving behind the desired circuit pattern. This method involves applying a photoresist layer to the copper, exposing it to UV light through a photomask, and then etching away the unprotected copper using a chemical solution.
Advantages:
– Low cost for small quantities
– Suitable for 1-2 layer designs
– Can achieve higher precision than PCB milling
Disadvantages:
– Longer turnaround times compared to PCB milling
– Requires additional equipment and chemicals
– Limited to 1-2 layers
– Not suitable for high-density designs or fine-pitch components
3. PCB Printing
PCB printing is an additive manufacturing process that uses conductive ink to print the circuit pattern directly onto the PCB substrate. This method is relatively new and is still being developed for widespread use.
Advantages:
– Rapid prototyping
– Suitable for low-cost, low-volume production
– Potential for multi-layer designs
– Environmentally friendly (no chemicals or waste)
Disadvantages:
– Limited material options
– Lower conductivity compared to traditional copper PCBs
– Still an emerging technology with limited availability
4. PCB Fabrication Houses
PCB fabrication houses are professional manufacturers that specialize in producing high-quality PCB prototypes and production runs. They offer a wide range of services, including multi-layer designs, high-density layouts, and advanced features such as blind and buried vias.
Advantages:
– High-quality, reliable results
– Capable of producing 1-4 layer (or more) designs
– Suitable for high-density layouts and fine-pitch components
– Offers additional services (e.g., assembly, testing, and inspection)
Disadvantages:
– Higher costs compared to in-house methods
– Longer turnaround times (typically 1-2 weeks)
– Minimum order quantities may apply
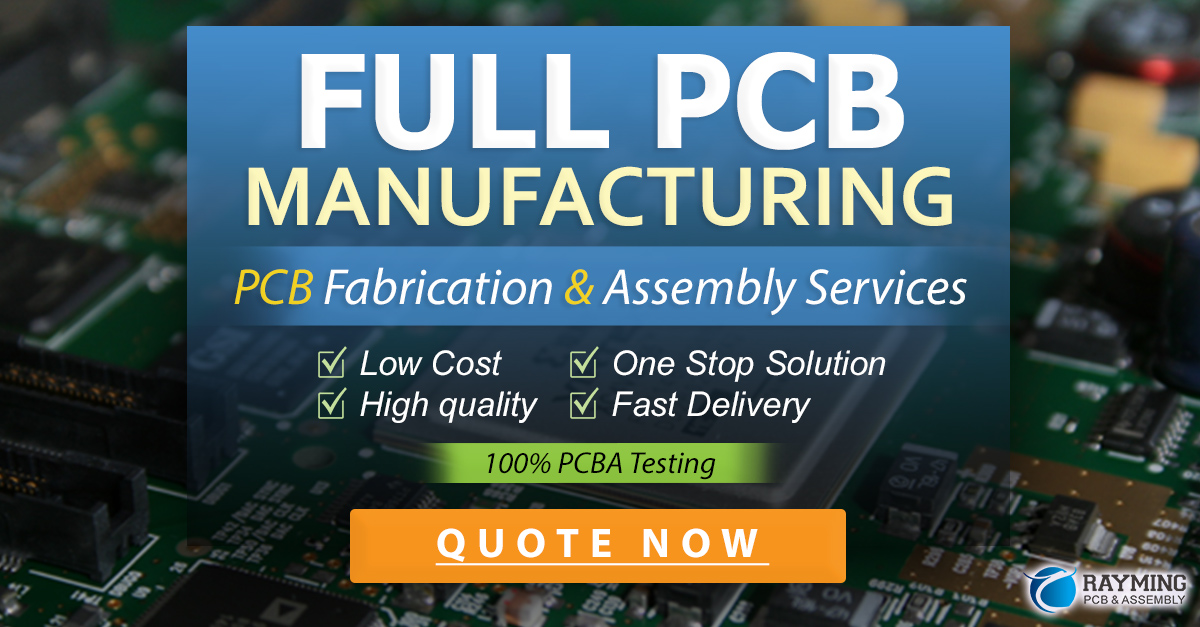
Choosing the Right PCB Prototype Method
Selecting the appropriate PCB prototype method depends on several factors, including:
- Number of layers required
- Design complexity and density
- Required precision and accuracy
- Quantity needed
- Budget and timeline constraints
Use the following table as a general guide to help choose the best method for your PCB prototype:
Method | Layers | Complexity | Precision | Quantity | Cost | Turnaround |
---|---|---|---|---|---|---|
PCB Milling | 1-2 | Low | Medium | 1-10 | Low | Fast |
PCB Etching | 1-2 | Low | Medium | 1-20 | Low | Medium |
PCB Printing | 1-4 | Medium | Medium | 1-50 | Medium | Fast |
PCB Fabrication Houses | 1-4+ | High | High | 1-1000+ | High | Slow |
Optimizing Your PCB Prototype Design
To ensure the best results and minimize costs when creating your PCB prototype, consider the following tips:
- Keep the design as simple as possible, especially for 1-2 layer boards.
- Use standard component sizes and footprints to avoid custom manufacturing costs.
- Maintain proper trace width and spacing to ensure signal integrity and manufacturability.
- Incorporate ground planes and power planes to reduce EMI and improve power distribution.
- Use vias strategically to connect layers and minimize board size.
- Follow the manufacturer’s design guidelines and constraints for your chosen prototype method.
- Always double-check your design files before submitting them for production.
Frequently Asked Questions (FAQ)
- What is the cheapest method for creating a PCB prototype?
-
For simple 1-2 layer designs, PCB milling and etching are typically the most cost-effective methods. However, the total cost will depend on the specific design requirements and the quantity needed.
-
How long does it take to receive a PCB prototype from a fabrication house?
-
Turnaround times for PCB fabrication houses typically range from 1-2 weeks, depending on the complexity of the design and the manufacturer’s workload. Some companies offer expedited services for an additional fee.
-
Can I create a multi-layer PCB prototype using in-house methods?
-
While PCB milling and etching are generally limited to 1-2 layer designs, PCB printing technology is advancing rapidly and may soon offer a viable option for low-cost, in-house multi-layer prototyping.
-
What are the advantages of using a PCB fabrication house?
-
PCB fabrication houses offer high-quality, reliable results and can handle complex designs with multiple layers and high-density layouts. They also provide additional services such as assembly, testing, and inspection.
-
How can I reduce the cost of my PCB prototype without sacrificing quality?
- To minimize costs, keep your design as simple as possible, use standard component sizes and footprints, and follow the manufacturer’s design guidelines. Additionally, consider using a cost-effective prototype method for initial testing and validation before investing in a higher-quality fabrication house prototype.
Conclusion
Creating low-cost 1 to 4 layer PCB prototypes is essential for validating electronic designs and bringing products to market quickly and efficiently. By understanding the various prototype methods available and their respective advantages and disadvantages, you can choose the best option for your specific needs and budget.
Remember to optimize your PCB design for simplicity, manufacturability, and cost-effectiveness, and always work with reputable suppliers and manufacturers to ensure the highest quality results.
With the right approach and tools, you can create reliable, high-performance PCB prototypes that lay the foundation for successful electronic products.
Leave a Reply