What are LED PCBs?
LED PCBs are printed circuit boards that are engineered to provide power and control signals to light-emitting diodes (LEDs). They feature conductive tracks, pads, and other features etched from copper sheets laminated onto a non-conductive substrate. The LEDs are mounted directly onto the PCB and soldered in place.
Unlike traditional PCBs designed for general electronics, LED PCBs have unique requirements to properly power and regulate the current going to the LEDs. They often have thicker copper traces to handle higher currents, use aluminum substrates to dissipate heat, and include constant-current drivers to provide a stable current to the LEDs.
Advantages of LED PCBs
LED PCBs offer several benefits over other LED mounting and assembly methods:
- Compact size – PCBs allow LEDs to be densely packed into small spaces
- Efficient heat dissipation – Aluminum PCBs and thermal vias draw heat away from the LEDs, improving lifespan and performance
- Simplified assembly – The PCB itself serves as the mechanical support and electrical connections for the LEDs
- Design flexibility – PCBs can be customized into any size and shape to fit the end application
- Improved reliability – Robust PCB construction provides better protection than loose wires or flimsy circuits
How Do LED PCBs Work?
An LED PCB functions by providing a controlled power source and mounting platform for the LEDs. The main components are:
LEDs
Surface mount device (SMD) LEDs are soldered directly onto the copper pads of the PCB. The number, type, color, and arrangement of the LEDs depends on the lighting requirements of the application. High power LEDs may be used for general illumination, while smaller LEDs can be used for indicators, displays, or accent lighting.
Driver Circuits
LEDs require a precise constant current to operate efficiently and maintain a stable brightness and color. LED drivers are specialized circuits that regulate the current delivered to the LEDs. They may be simple current-limiting resistors for low-power LEDs, or more advanced constant-current drivers with dimming and thermal protection features for high-power LEDs.
Power Regulation
The driver circuit is powered from a DC source, typically 12V or 24V for lighting applications. An onboard voltage regulator steps this voltage down to the forward voltage of the LEDs, which may range from 2V to 6V depending on the LED type and color. Bypass capacitors smooth out any ripples in the power supply to prevent flickering.
Substrate
Most LED PCBs use a 1.6mm thick FR-4 glass epoxy substrate for its low cost and good mechanical strength. However, high-power LED PCBs often use an aluminum substrate for its excellent thermal conductivity. The aluminum helps spread heat evenly across the board and dissipate it into the environment.
LED PCB Design Considerations
Designing an LED PCB requires careful planning to ensure optimal electrical, thermal, and optical performance. The main considerations are:
LED Selection
The type, number, and arrangement of LEDs must be chosen based on the desired luminous flux (brightness), color, beam angle, and power consumption of the application. The forward voltage and current of the LEDs determines the driver circuit design.
Driver Circuit
The driver circuit must be designed to provide a constant current at the required forward voltage of the LEDs. Factors such as the input voltage range, maximum output current, dimming requirements, and protection features must be considered. For high power LEDs, a switching constant-current driver is often used for best efficiency.
Thermal Management
LEDs produce a significant amount of heat that must be dissipated to prevent overheating and premature failure. The PCB design must include adequate thermal management features such as:
- Aluminum substrate for high thermal conductivity
- Thermal vias to transfer heat from the LED thermal pad to the substrate
- Copper pours and thick traces to spread heat evenly across the board
- Heatsinks or fans to actively remove heat from the board
Circuit Protection
LED PCBs must include protection features to prevent damage from electrical faults such as overcurrent, overvoltage, reverse polarity, and electrostatic discharge (ESD). Fuses, transient voltage suppressors (TVS), and Zener diodes are commonly used for circuit protection.
Optical Considerations
The placement and orientation of the LEDs on the PCB affects the optical performance of the final product. Factors such as LED spacing, beam angle, and color mixing must be considered to achieve the desired illumination pattern and color uniformity.
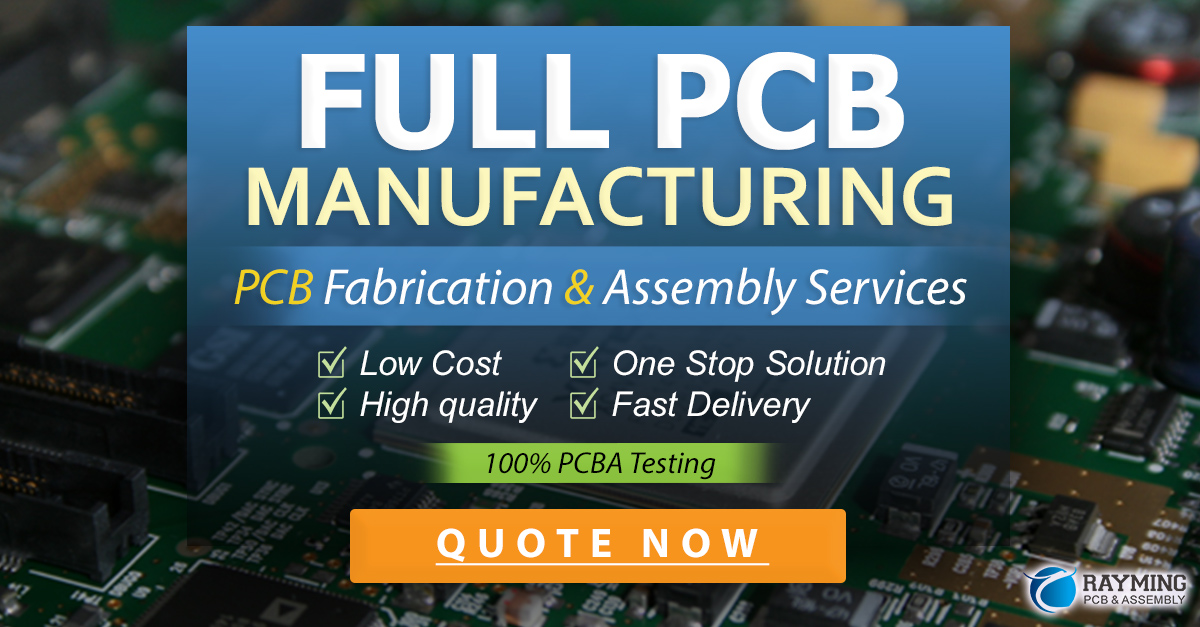
Manufacturing LED PCBs
LED PCBs are manufactured using standard PCB fabrication processes, with some additional steps to accommodate the unique requirements of LEDs.
PCB Fabrication
The PCB is fabricated by etching the copper traces and pads onto the substrate material. For aluminum PCBs, a thin layer of dielectric material is laminated onto the aluminum to insulate the copper layer. Holes are drilled for component leads and vias.
Solder Mask and Silkscreen
A solder mask is applied to the PCB to protect the copper traces from oxidation and prevent solder bridging. The solder mask is typically white for LED PCBs to maximize light reflection. A silkscreen layer is added to label components and provide assembly instructions.
LED Mounting
The LEDs are mounted onto the PCB using surface mount technology (SMT). A solder paste is applied to the LED pads, and the LEDs are placed onto the paste using a pick-and-place machine. The board is then run through a reflow oven to melt the solder and permanently attach the LEDs.
Assembly and Testing
The remaining components such as drivers, resistors, and capacitors are soldered onto the board. The completed assembly is then tested for proper operation and optical performance. This may involve a burn-in period to check for any early failures.
Applications of LED PCBs
LED PCBs are used in a wide variety of lighting applications, including:
- General illumination – Ceiling lights, desk lamps, track lighting
- Automotive lighting – Headlights, tail lights, interior lighting
- Display backlighting – LCD TVs, monitors, instrument panels
- Signs and displays – Channel letters, light boxes, digital signage
- Indicators and markers – Exit signs, warning lights, beacons
- Portable lighting – Flashlights, headlamps, lanterns
- Horticulture lighting – Grow lights, aquarium lighting, greenhouse lighting
Frequently Asked Questions
What is the difference between an LED PCB and a regular PCB?
LED PCBs are designed specifically to power and control LEDs, while regular PCBs are general-purpose boards for a wide range of electronic components. LED PCBs have thicker copper traces and thermal management features to handle the higher currents and heat generated by LEDs.
Can I use a regular PCB for LEDs?
It is possible to use a regular PCB for low-power indicator LEDs, but it is not recommended for high-power illumination LEDs. Regular PCBs lack the necessary thermal management and current handling capabilities needed for proper LED operation and longevity.
What is the best substrate material for LED PCBs?
Aluminum is the best substrate material for high-power LED PCBs due to its excellent thermal conductivity. However, FR-4 glass epoxy is sufficient for low-power LED applications and is more cost-effective.
How do I select the right LED driver for my PCB?
The LED driver must be selected based on the forward voltage and current requirements of the LEDs, as well as the input voltage range and desired dimming and protection features. It is recommended to use a constant-current driver with a higher maximum output current than required for the best efficiency and regulation.
How do I ensure good color consistency across multiple LED PCBs?
To ensure good color consistency, use LEDs from the same bin and manufacturer, and carefully control the LED current and temperature. Use a constant-current driver with good line and load regulation, and consider using a feedback system to adjust the LED current based on the measured color output.
Conclusion
LED PCBs are a critical component in the design and manufacturing of LED lighting products. By combining electrical, thermal, and optical design considerations, LED PCBs provide a compact, efficient, and reliable platform for powering and controlling LEDs.
When designing an LED PCB, careful attention must be paid to the selection of LEDs, driver circuits, thermal management, and protection features to ensure optimal performance and longevity. The PCB must be manufactured using appropriate processes and materials to meet the unique requirements of LED applications.
LED PCBs enable a wide range of lighting applications, from general illumination to specialty applications such as horticulture and automotive lighting. As LED technology continues to advance, the design and manufacturing of LED PCBs will play an increasingly important role in the development of energy-efficient, high-performance lighting solutions.
Leave a Reply