Introduction to Laser PCB Technology
Printed Circuit Boards (PCBs) are essential components in modern electronic devices. They provide a platform for mounting and connecting electronic components, enabling the creation of complex circuits. Traditional PCB manufacturing processes involve multiple steps, including etching, drilling, and plating, which can be time-consuming and costly. However, with the advent of laser technology, PCB manufacturing has become more efficient and precise. Laser exposure machines have revolutionized the PCB industry, offering numerous benefits over conventional methods.
What is a Laser Exposure Machine?
A laser exposure machine is a device that uses high-powered lasers to create patterns on a photoresist-coated PCB substrate. The laser beam is precisely controlled and guided by a computer-aided design (CAD) file, which contains the circuit layout information. The laser selectively exposes the photoresist, creating a pattern that matches the desired circuit design. After exposure, the PCB undergoes a series of chemical processes to develop and etch the exposed areas, revealing the conductive copper traces.
Advantages of Laser Exposure Machines in PCB Manufacturing
Laser exposure machines offer several advantages over traditional PCB manufacturing methods:
-
High Precision: Laser exposure machines can achieve extremely high resolutions, enabling the creation of intricate and dense circuit patterns. The laser beam can be focused to a very small spot size, allowing for precise control over the exposure process. This level of precision is essential for manufacturing high-density PCBs used in advanced electronic devices.
-
Increased Efficiency: Laser exposure machines can significantly reduce the time required for PCB manufacturing. Unlike traditional methods that involve multiple steps and manual operations, laser exposure is a highly automated process. The laser can quickly and accurately expose the desired pattern onto the PCB substrate, reducing the overall processing time. This increased efficiency translates to faster turnaround times and higher production volumes.
-
Cost-Effectiveness: While the initial investment in a laser exposure machine may be higher compared to traditional equipment, the long-term cost benefits are significant. Laser exposure machines require fewer consumables and have lower maintenance costs. Additionally, the increased efficiency and precision of laser exposure result in reduced waste and fewer defects, leading to cost savings in the overall manufacturing process.
-
Environmental Friendliness: Laser exposure machines are more environmentally friendly compared to traditional PCB manufacturing methods. They eliminate the need for harmful chemicals used in the etching process, such as ferric chloride or ammonium persulfate. Laser exposure also reduces the amount of waste generated during manufacturing, as it minimizes the need for physical masks and reduces the consumption of photoresist materials.
How Laser Exposure Machines Work
Laser Exposure Process
The laser exposure process involves several key steps:
-
PCB Design: The first step is to create a detailed CAD file of the desired circuit layout. This file contains information about the traces, pads, and other features of the PCB.
-
Substrate Preparation: The PCB substrate, typically a copper-clad laminate, is cleaned and coated with a photoresist material. The photoresist is sensitive to light and will change its chemical properties when exposed to the laser beam.
-
Laser Exposure: The prepared PCB substrate is placed in the laser exposure machine. The machine reads the CAD file and uses high-powered lasers to selectively expose the photoresist according to the circuit pattern. The laser beam is precisely controlled to ensure accurate exposure of the desired areas.
-
Development: After exposure, the PCB substrate is subjected to a development process. The exposed areas of the photoresist are removed, revealing the underlying copper layer. The unexposed areas remain intact, protecting the copper from the subsequent etching process.
-
Etching: The developed PCB substrate is then placed in an etching solution, typically an acidic or alkaline solution that dissolves the exposed copper. The protected areas of the copper remain untouched, forming the conductive traces of the circuit.
-
Stripping and Finishing: After etching, the remaining photoresist is stripped away, leaving the final PCB with the desired circuit pattern. Additional finishing processes, such as soldermask application and silkscreen printing, may be applied to enhance the PCB’s functionality and appearance.
Laser Exposure Machine Components
A typical laser exposure machine consists of several key components:
-
Laser Source: The heart of the laser exposure machine is the laser source. It generates the high-powered laser beam used for exposing the photoresist. Common laser types used in PCB exposure machines include UV lasers, fiber lasers, and CO2 lasers.
-
Beam Delivery System: The beam delivery system is responsible for guiding and focusing the laser beam onto the PCB substrate. It includes mirrors, lenses, and other optical components that direct and shape the laser beam for precise exposure.
-
XY Positioning System: The XY positioning system enables precise movement of the laser beam relative to the PCB substrate. It consists of high-precision linear stages or galvanometer scanners that control the laser beam’s position and speed. This allows for accurate exposure of the desired circuit pattern.
-
Computer Control System: The laser exposure machine is controlled by a computer system that reads the CAD file and translates it into machine instructions. The computer controls the laser parameters, such as power, pulse duration, and scanning speed, to ensure optimal exposure results.
-
Substrate Handling System: The substrate handling system is responsible for loading and unloading the PCB substrates into the laser exposure machine. It may include automated conveyor belts, robotic arms, or manual loading mechanisms to ensure efficient and precise substrate handling.
Applications of Laser PCB Technology
Laser PCB technology has found applications in various industries due to its precision, efficiency, and versatility. Some of the key applications include:
Consumer Electronics
Laser PCB technology is widely used in the manufacturing of consumer electronic devices, such as smartphones, tablets, laptops, and wearables. These devices require high-density PCBs with intricate circuit patterns to accommodate the increasing functionality and miniaturization demands. Laser exposure machines enable the production of these complex PCBs with high precision and reliability.
Automotive Electronics
The automotive industry relies heavily on electronic systems for various functions, including engine control, infotainment, safety features, and autonomous driving capabilities. Laser PCB technology is employed in the manufacturing of automotive electronic components, such as engine control units (ECUs), sensors, and displays. The high precision and reliability offered by laser exposure machines ensure the production of robust and reliable automotive PCBs.
Medical Devices
Medical devices, such as implantable devices, diagnostic equipment, and monitoring systems, require PCBs with strict reliability and performance requirements. Laser PCB technology enables the manufacturing of high-quality medical device PCBs with precise circuit patterns and tight tolerances. The non-contact nature of laser exposure also ensures a clean and contamination-free manufacturing process, which is crucial for medical applications.
Aerospace and Defense
The aerospace and defense industries demand PCBs with exceptional reliability, durability, and performance under extreme conditions. Laser PCB technology is employed in the manufacturing of PCBs for avionics systems, communication equipment, and military electronics. The precision and consistency provided by laser exposure machines ensure the production of high-quality PCBs that can withstand harsh environments and meet stringent industry standards.
Industrial Automation
Industrial automation systems, such as process control, robotics, and machine vision, rely on PCBs for various functions. Laser PCB technology enables the manufacturing of industrial-grade PCBs with high precision and reliability. The ability to create dense circuit patterns and handle high-power requirements makes laser exposure machines well-suited for industrial automation applications.
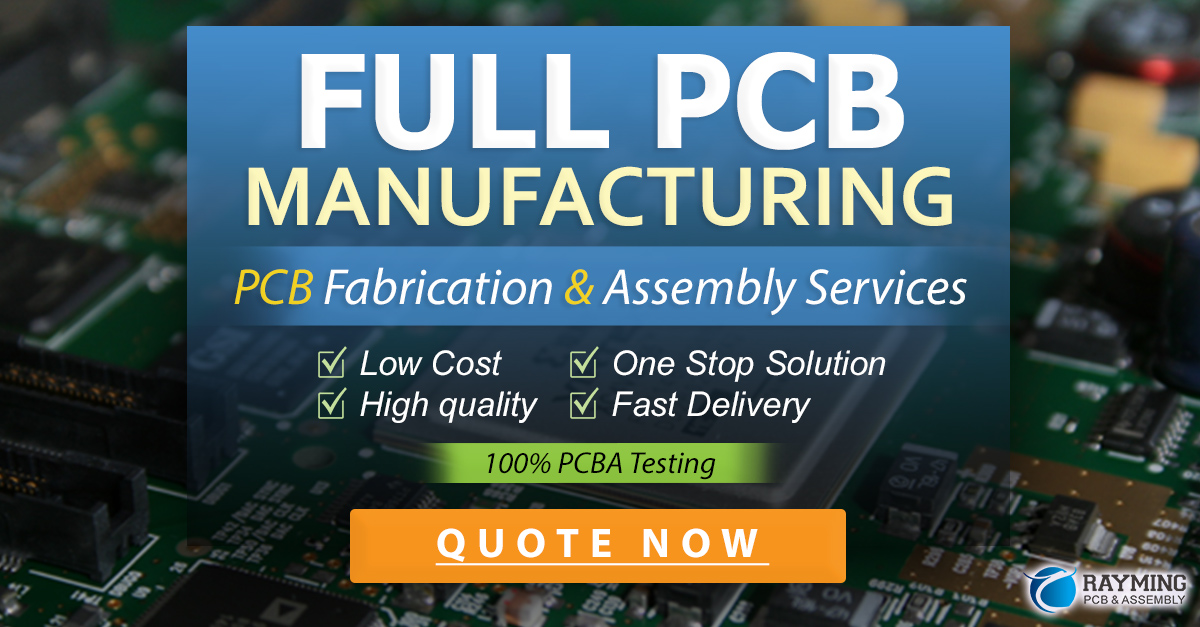
Future Trends in Laser PCB Technology
As the demand for advanced electronic devices continues to grow, laser PCB technology is expected to evolve and improve. Some of the future trends in laser PCB technology include:
Increased Resolution and Precision
Laser exposure machines are continuously improving in terms of resolution and precision. Advancements in laser technology, such as shorter wavelengths and smaller spot sizes, enable the creation of even finer circuit patterns. This trend towards higher resolution and precision will enable the manufacturing of PCBs with increasingly complex and dense layouts.
Faster Processing Speeds
The need for faster PCB manufacturing is driving the development of laser exposure machines with higher processing speeds. Improvements in laser power, scanning systems, and control algorithms will enable faster exposure times, reducing the overall manufacturing cycle. This will result in increased production throughput and shorter lead times.
Integration with Additive Manufacturing
Laser PCB technology is being explored in combination with additive manufacturing techniques, such as 3D printing. By integrating laser exposure with additive manufacturing, it becomes possible to create three-dimensional PCBs with embedded components and interconnects. This integration opens up new possibilities for PCB design and functionality, enabling the creation of more compact and efficient electronic devices.
Intelligent Process Control
The integration of intelligent process control systems in laser PCB manufacturing is expected to increase. Machine learning algorithms and real-time monitoring systems can optimize the laser exposure process, ensuring consistent and high-quality results. Intelligent process control can automatically adjust laser parameters based on material properties, environmental conditions, and process feedback, minimizing defects and improving overall manufacturing efficiency.
Environmental Sustainability
As environmental sustainability becomes a growing concern, laser PCB technology is expected to play a role in reducing the environmental impact of PCB manufacturing. The elimination of harmful chemicals and the reduction of waste associated with laser exposure machines contribute to a more environmentally friendly manufacturing process. Future developments in laser PCB technology may focus on further reducing energy consumption and increasing the use of eco-friendly materials.
Frequently Asked Questions (FAQ)
-
What are the advantages of laser exposure machines over traditional PCB manufacturing methods?
Laser exposure machines offer several advantages, including high precision, increased efficiency, cost-effectiveness, and environmental friendliness. They enable the creation of intricate and dense circuit patterns, reduce processing time, minimize waste, and eliminate the need for harmful chemicals used in traditional etching processes. -
What types of lasers are commonly used in laser exposure machines?
Common laser types used in PCB exposure machines include UV lasers, fiber lasers, and CO2 lasers. The choice of laser depends on factors such as the desired resolution, material compatibility, and processing speed. -
Can laser exposure machines handle different PCB substrate materials?
Yes, laser exposure machines can handle a variety of PCB substrate materials, including FR-4, polyimide, and flexible substrates. The laser parameters can be adjusted to accommodate different material properties and ensure optimal exposure results. -
How does the resolution of laser exposure machines compare to traditional PCB manufacturing methods?
Laser exposure machines can achieve significantly higher resolutions compared to traditional PCB manufacturing methods. They can create circuit patterns with feature sizes in the range of a few microns, enabling the production of high-density PCBs with fine pitch and trace widths. -
Are laser exposure machines suitable for high-volume PCB production?
Yes, laser exposure machines are well-suited for high-volume PCB production. Their high processing speeds, automation capabilities, and minimal maintenance requirements make them efficient for large-scale manufacturing. They can handle high throughput demands while maintaining consistent quality and precision.
Conclusion
Laser exposure machines have revolutionized the PCB manufacturing industry, offering numerous benefits over traditional methods. With their high precision, increased efficiency, cost-effectiveness, and environmental friendliness, laser PCB technology has become a preferred choice for a wide range of applications. From consumer electronics to automotive, medical devices to aerospace and defense, laser exposure machines enable the production of high-quality PCBs with intricate and dense circuit patterns.
As the demand for advanced electronic devices continues to grow, laser PCB technology is expected to evolve and improve. Advancements in laser technology, faster processing speeds, integration with additive manufacturing, intelligent process control, and environmental sustainability are some of the future trends shaping the laser PCB industry.
By embracing laser PCB technology, manufacturers can stay competitive in the rapidly evolving electronics industry. The precision, efficiency, and versatility offered by laser exposure machines will continue to drive innovation and enable the creation of cutting-edge electronic devices that shape our future.
Parameter | Traditional PCB Manufacturing | Laser PCB Manufacturing |
---|---|---|
Resolution | Limited by etching process | High, sub-micron features |
Efficiency | Multiple steps, time-consuming | Highly automated, faster processing |
Cost | Higher consumable and maintenance costs | Lower long-term costs due to reduced waste and defects |
Environmental Impact | Uses harmful chemicals for etching | Eliminates need for harmful chemicals |
Flexibility | Limited by physical masks | Easily adaptable to design changes |
In summary, laser exposure machines have transformed the PCB manufacturing landscape, offering a more precise, efficient, cost-effective, and environmentally friendly solution. As technology advances and the demand for high-performance electronic devices grows, laser PCB technology will continue to play a crucial role in shaping the future of the electronics industry.
Leave a Reply