Introduction to PCB Design Rules in KiCAD
Printed circuit board (PCB) design rules are a critical aspect of creating high-quality, manufacturable PCB layouts using EDA software like KiCAD. Design rules help ensure that your PCB will function as intended and can be reliably manufactured by defining constraints and guidelines for various aspects of the layout, such as track widths, clearances, via sizes, and more.
In this article, we’ll dive deep into the world of PCB design rules in KiCAD, exploring the different types of rules available, how to set them up in your projects, and best practices for optimizing your layouts. Whether you’re a beginner or an experienced PCB designer, understanding and properly applying design rules is essential for creating successful PCB designs.
The Importance of PCB Design Rules
PCB design rules serve several critical purposes in the design process:
- Ensuring manufacturability
- Maintaining signal integrity
- Preventing short circuits and other defects
- Facilitating assembly and testing
- Compliance with industry standards and regulations
By adhering to well-defined design rules, you can avoid costly mistakes, delays, and redesigns, ultimately saving time and money while delivering a high-quality product.
Types of PCB Design Rules in KiCAD
KiCAD offers a comprehensive set of design rules that cover various aspects of PCB layout. Some of the key types of design rules include:
Track Width and Clearance Rules
These rules define the minimum allowed width for tracks (also known as traces or routes) and the minimum clearance between tracks and other elements on the PCB, such as pads, vias, and copper fills. Proper track width and clearance ensure sufficient current-carrying capacity, prevent short circuits, and maintain signal integrity.
Layer | Minimum Track Width | Minimum Clearance |
---|---|---|
Top Copper | 0.2 mm | 0.2 mm |
Bottom Copper | 0.2 mm | 0.2 mm |
Inner Layer 1 | 0.15 mm | 0.15 mm |
Inner Layer 2 | 0.15 mm | 0.15 mm |
Via Size and Drill Rules
Via size and drill rules specify the minimum and maximum allowed diameters for vias and their associated drill holes. These rules ensure proper plating and reliable connections between layers while considering manufacturing capabilities and costs.
Via Type | Minimum Diameter | Maximum Diameter | Minimum Drill Size |
---|---|---|---|
Through-hole | 0.6 mm | 1.0 mm | 0.3 mm |
Blind/Buried | 0.4 mm | 0.8 mm | 0.2 mm |
Micro | 0.2 mm | 0.4 mm | 0.1 mm |
Copper Fill Rules
Copper fill rules define the minimum clearance between copper fills (also known as copper pours or planes) and other elements on the PCB, as well as the minimum width of copper fills. These rules help ensure proper grounding, shielding, and thermal management while preventing short circuits and manufacturability issues.
Copper Fill Type | Minimum Clearance | Minimum Width |
---|---|---|
Ground Plane | 0.3 mm | 0.5 mm |
Power Plane | 0.3 mm | 0.5 mm |
Signal Fill | 0.2 mm | 0.3 mm |
Silk Screen and Solder Mask Rules
Silk screen and solder mask rules specify the minimum clearances and widths for silk screen (text and graphics) and solder mask openings on the PCB. These rules ensure legibility, proper insulation, and accurate placement of components during assembly.
Element | Minimum Clearance | Minimum Width |
---|---|---|
Silk Screen Text | 0.15 mm | 0.15 mm |
Silk Screen Graphics | 0.2 mm | 0.2 mm |
Solder Mask Opening | 0.05 mm | 0.1 mm |
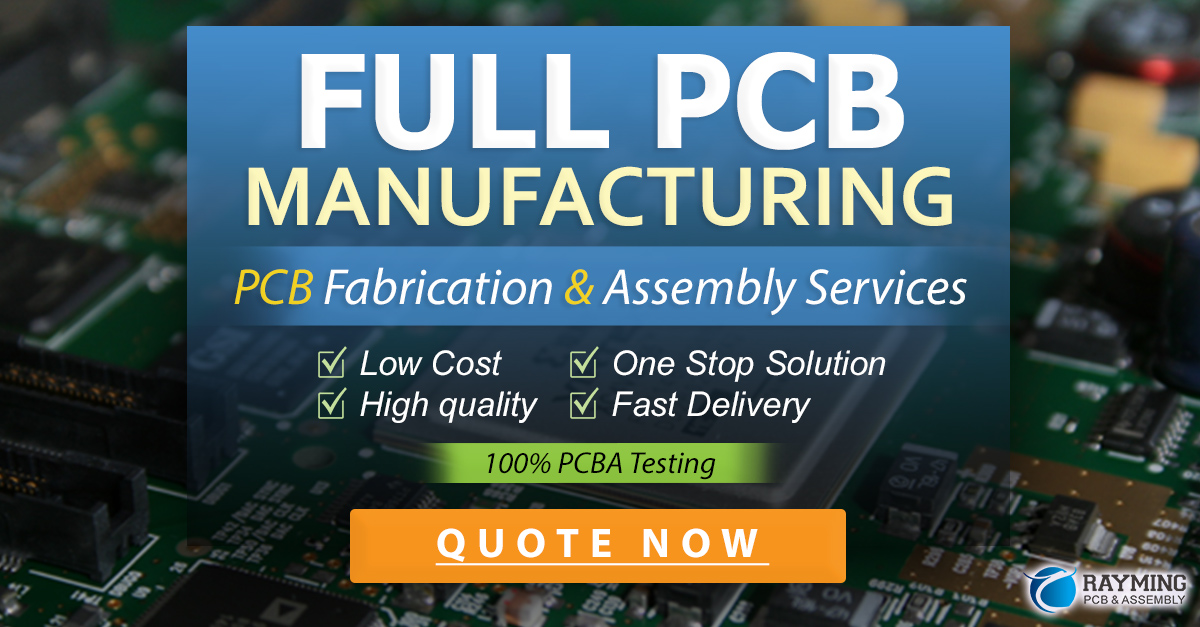
Setting Up PCB Design Rules in KiCAD
To set up and manage PCB design rules in KiCAD, you’ll primarily work with the PCB Rules dialog, which can be accessed from the PCB Editor by clicking on “Design Rules” in the top menu.
Global and Specific Design Rules
KiCAD allows you to define both global and specific design rules. Global rules apply to the entire PCB, while specific rules can be assigned to individual nets, components, or regions of the board. Specific rules override global rules, giving you fine-grained control over your layout.
Net Classes and Differential Pairs
Net classes and differential pairs are powerful tools for managing design rules in KiCAD. By grouping nets with similar requirements into classes, you can easily apply specific rules to a set of nets, streamlining the design process and ensuring consistency.
Differential pairs are a special type of net class used for high-speed, differential signaling. KiCAD provides dedicated tools for defining and routing differential pairs, with automatic impedance control and length matching.
Design Rule Checker (DRC)
KiCAD’s Design Rule Checker (DRC) is an essential tool for verifying that your PCB layout complies with the defined design rules. The DRC scans your layout and reports any violations, allowing you to identify and fix issues before sending your design for manufacturing.
To run the DRC, click on “Perform Design Rules Check” in the PCB Editor’s top menu. The DRC Results dialog will display any violations found, along with their locations and details. Double-clicking on a violation will center the view on the affected area, making it easy to find and resolve issues.
Best Practices for Optimizing PCB Layouts with Design Rules
- Start with conservative rules and refine as needed
- Use net classes and differential pairs to streamline rule management
- Regularly run the DRC and address violations promptly
- Consider manufacturability and assembly requirements when defining rules
- Document and communicate design rules with your team and manufacturers
- Stay updated with industry standards and best practices
- Use rule templates and projects to ensure consistency across designs
FAQ
1. What happens if I violate a PCB design rule?
Violating a PCB design rule can lead to various issues, such as manufacturability problems, signal integrity degradation, or even complete failure of the PCB. The DRC will flag any violations, allowing you to address them before sending your design for manufacturing.
2. Can I change design rules mid-project?
Yes, you can modify design rules at any point during your project. However, be aware that changing rules may require adjustments to your existing layout, and it’s essential to re-run the DRC after making any changes to ensure compliance.
3. How do I know what values to set for my design rules?
The appropriate values for your design rules depend on various factors, such as the PCB’s intended application, the manufacturing capabilities of your chosen fab house, and the specific requirements of your components and circuits. Consult with your manufacturer, reference industry standards, and review datasheets and application notes to determine suitable rule values.
4. Can I use different design rules for different parts of my PCB?
Yes, KiCAD allows you to define specific rules that apply to individual nets, components, or regions of your PCB. This flexibility enables you to optimize your layout for different requirements, such as high-speed signals, power delivery, or RF circuits.
5. Are there any automated tools for setting up design rules in KiCAD?
KiCAD does not have fully automated tools for setting up design rules, as the appropriate rules depend on your specific project requirements. However, you can use rule templates and import rules from previous projects to streamline the setup process and ensure consistency across designs.
Conclusion
PCB design rules are a critical component of creating successful, manufacturable PCB layouts using KiCAD. By understanding the different types of rules available, properly setting them up in your projects, and following best practices for optimization, you can ensure that your designs meet the highest standards of quality and reliability.
Remember to regularly run the DRC, communicate with your team and manufacturers, and stay updated with industry standards and best practices. With a solid grasp of PCB design rules and the powerful tools provided by KiCAD, you’ll be well-equipped to tackle even the most challenging PCB design projects.
Leave a Reply