Alumina (aluminum oxide) is an excellent thermal conductor compared to most electrical insulators due to its high thermal conductivity. This makes alumina well suited for thermal management applications requiring both electrical insulation and heat dissipation.
Key Properties
Alumina possesses a unique combination of properties:
- High electrical resistivity – Excellent electrical insulator
- Good thermal conductivity – Dissipates heat effectively
- High strength – Withstands physical stresses
- Thermal stability – Low expansion, high melting point
- Chemically inert – Resists corrosion and weathering
This enables using alumina in applications with simultaneous electrical, thermal and mechanical demands.
Thermal Conductivity
The thermal conductivity of alumina is what gives it good heat transfer capabilities despite being an electrical insulator.
Typical thermal conductivity values for various alumina grades:
- 85-95% Alumina: 20-30 W/mK
- 96% Alumina: 24-28 W/mK
- 99% Alumina: 30-35 W/mK
For comparison, other common materials:
- Copper: 400 W/mK
- Aluminum: 237 W/mK
- Stainless steel: ~15 W/mK
- FR4: 0.25 W/mK
So while far below metals, alumina has 100-1000 times the thermal conductivity of polymeric insulators like FR4.
This allows alumina to dissipate localized heat generation through conduction far more effectively than electrical insulators.
Heat Transfer Mechanisms
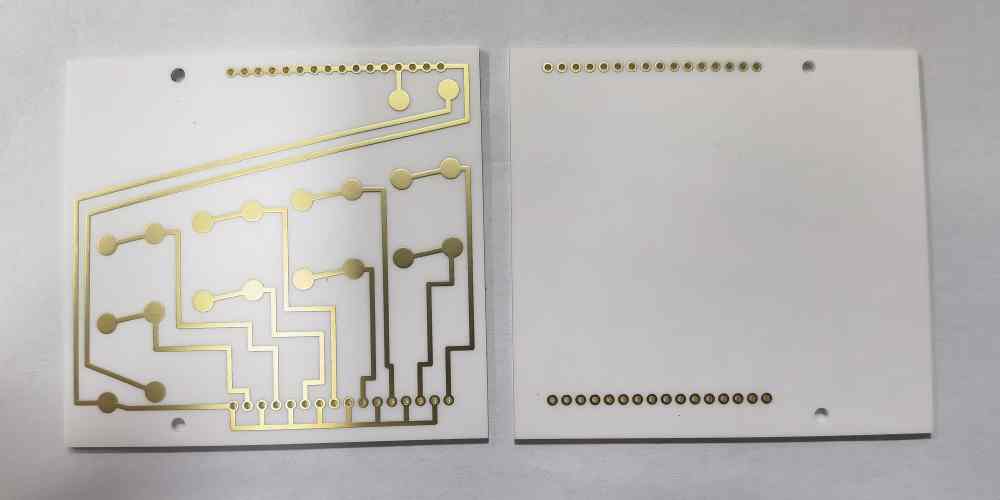
There are three mechanisms of heat transfer relevant to PCB substrates:
Conduction – Heat transfer through a solid material due to interactions between atoms and electrons. Improved by higher thermal conductivity.
Convection – Heat transfer via fluid motion in gas or liquid. Enhanced by increasing fluid velocity.
Radiation – Emission of thermal radiation as infrared photons. Increased by higher surface emissivity.
Of these, conduction is the dominant mechanism in PCBs. Alumina’s high thermal conductivity directly enhances conductive heat transfer.
For optimal thermal performance, PCB designers should also utilize convection with air flow and radiation with black ceramic surfaces.
Applications Utilizing Alumina’s Thermal Properties
Some examples leveraging alumina’s thermal conductivity:
Power electronics – Alumina substrates manage heat in power converters and inverters for industrial equipment and electric vehicles.
LED lighting – High brightness LEDs require electrically insulating but thermally conductive PCBs which alumina provides.
Automotive electronics – Alumina PCBs withstand high temps in engine compartments and transmission controls while preventing short circuits.
Aerospace – Radio frequency (RF) modules and radars benefit from alumina’s stability and heat dissipation in extreme environments.
Medical – Thermal conductivity allows safe heat dissipation in body-contact devices like probes while ensuring electrical safety.
Industrial heating – Silicon carbide, molybdenum or tungsten heating elements bond to alumina plates, tubes or beds for conductivity and high temp resistance.
Semiconductor fabrication – High purity alumina used as thermally conductive ceramic support structures and heaters in semiconductor production equipment.
Lasers – Alumina maintains precision alignment of optical components in high power lasers while removing heat from gain media and diodes.
This wide range of applications highlights alumina’s versatility as a thermally conductive electrical insulator.
Alumina PCB Substrates
A prime example of leveraging alumina’s thermal properties is with alumina PCB substrates.
Alumina ceramic PCBs have excellent thermal conductivity compared to standard glass reinforced FR4 laminates to handle heat dissipation in high power circuits.
Alumina PCB substrate with 94% alumina content
Some key advantages of alumina PCBs:
- Thermal conductivity up to 100X higher than FR4
- Electrically insulating – high resistivity and dielectric strength
- Thin substrates promote heat spreading
- Withstands high temperatures up to 800°C
- Complements high frequency circuits with low loss
- Direct bonding of components to alumina surfaces
- Match coefficient of expansion between alumina and conductors
- High purity alumina for exacting electrical parameters
These attributes make alumina PCBs ideal for RF power amplifiers, LED modules, power semiconductor switching circuits, and other demanding applications.
Thermal Management Design Factors
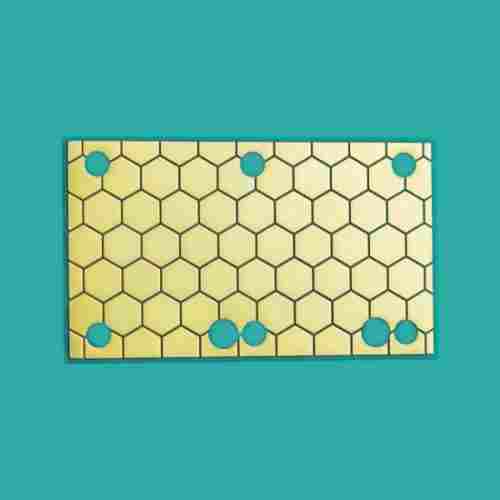
To fully utilize alumina’s thermal conduction abilities in PCB design, certain guidelines should be followed:
- Minimize alumina substrate thickness to reduce thermal resistance
- Incorporate thermal vias under hot components
- Use thermally conductive fillers like gold or silver in vias
- Attach large heat sinks and heat spreaders to alumina
- Utilize thermal reliefs to isolate heated regions
- Position components for shortest heat conduction paths
- Maximize exposed alumina surface area
- Directly solder components to alumina surfaces
- Incorporate air flow for forced convection cooling
- Consider supplemental liquid cooling
PCB designers should perform thermal modeling and analysis to optimize layouts and stacking arrangements to exploit alumina’s superior thermal conductivity over conventional circuit board materials.
Alumina Thermal Conductivity vs Temperature
For precision applications, it is important to account for the effects of temperature on alumina’s thermal conductivity.
Thermal conductivity declines with increasing temperature. The reduction is more gradual above room temperature than the sharp drop off seen in metals.
Thermal conductivity vs temperature for various purity aluminas
This is why alumina is suitable for extremely high temperature applications up to 1000-1800°C where metals would suffer rapid loss of conductivity.
Is Alumina Thermally Isotropic?
Alumina is considered thermally isotropic, meaning its thermal conductivity is nearly equal along different crystal orientations.
This contrasts with highly anisotropic materials like graphite where the thermal conductivity varies dramatically with crystal alignment.
Isotropic behavior simplifies thermal analysis and design with alumina since orientation effects can be neglected.
Alumina Thermal Conductivity FAQ
Is alumina a good thermal conductor?
Yes, alumina has relatively high thermal conductivity for an electrical insulator, typically 20-35 W/mK. This allows effective heat dissipation in electrically insulating packages and circuit boards. Alumina’s thermal conductivity is far above polymers like FR4 epoxy.
Why is alumina thermally conductive?
Alumina’s crystalline structure and strong interatomic bonding allows efficient heat conduction through vibrations and propagation without electrical conductivity. High purity and dense microstructures improve thermal conductivity.
How does alumina compare to aluminum thermal conductivity?
Aluminum has a thermal conductivity around 200 W/mK over 6 times higher than alumina. But alumina provides electrical insulation that aluminum lacks. For applications needing both heat transfer and electrical isolation, alumina is far superior to plastics and polymers.
Is alumina thermally conductive?
Yes, alumina has good thermal conductivity relative to its electrical resistivity making it thermally conductive. This allows dissipating localized heat generation while maintaining surrounding electrical insulation.
Is alumina thermally isotropic?
Alumina exhibits approximately thermally isotropic behavior, meaning its thermal conductivity is similar along different crystal directions. This simplifies analysis compared to highly anisotropic materials like graphite.
Leave a Reply