What is IPC-A-600?
IPC-A-600 is a widely recognized standard published by the Association Connecting Electronics Industries (IPC) that provides acceptance criteria for printed circuit boards (PCBs). This standard is essential for ensuring the quality and reliability of PCBs used in various electronic applications. It defines the acceptable conditions of boards based on different classes, which correspond to the intended end-use of the product.
Key aspects of IPC-A-600:
- Visual acceptance criteria for PCBs
- Defect classifications and severity levels
- Workmanship standards for PCB Fabrication
- Inspection guidelines and methods
IPC Acceptability Classes
The IPC-A-600 standard defines three main classes of acceptance criteria for PCBs, each with specific requirements and allowances for various defects and imperfections. These classes are determined by the intended use of the PCB and the level of reliability required for the application.
Class 1: General Electronic Products
Class 1 is the least stringent acceptance criteria and is suitable for general electronic products where the main requirement is the function of the completed assembly. This class allows for some imperfections that do not affect the functionality or reliability of the PCB.
Typical applications for Class 1 PCBs include:
– Consumer electronics
– Low-cost products
– Non-critical applications
Class 2: Dedicated Service Electronic Products
Class 2 acceptance criteria are more rigorous than Class 1 and are intended for use in dedicated service electronic products where extended life and performance are required. This class has stricter requirements for defects and imperfections that could impact the reliability and durability of the PCB.
Typical applications for Class 2 PCBs include:
– Communications equipment
– Industrial controls
– Automotive electronics
– Medical devices (non-life-sustaining)
Class 3: High Reliability Electronic Products
Class 3 is the most stringent acceptance criteria and is reserved for high-reliability electronic products where continued performance or performance-on-demand is critical. This class has the tightest requirements for defects and imperfections, as any issues could result in catastrophic failures or safety hazards.
Typical applications for Class 3 PCBs include:
– Aerospace systems
– Military equipment
– Life-support medical devices
– Critical infrastructure components
Defect Categories and Severity Levels
IPC-A-600 classifies defects into various categories and assigns severity levels based on their potential impact on the functionality, reliability, and safety of the PCB. Some of the main defect categories include:
- Conductor defects
- Solder mask defects
- Laminate defects
- Hole and via defects
- Marking and labeling defects
Each defect category has specific criteria for acceptance based on the class of the PCB. The severity levels range from minor imperfections that have no impact on the PCB’s performance to critical defects that can cause failures or safety issues.
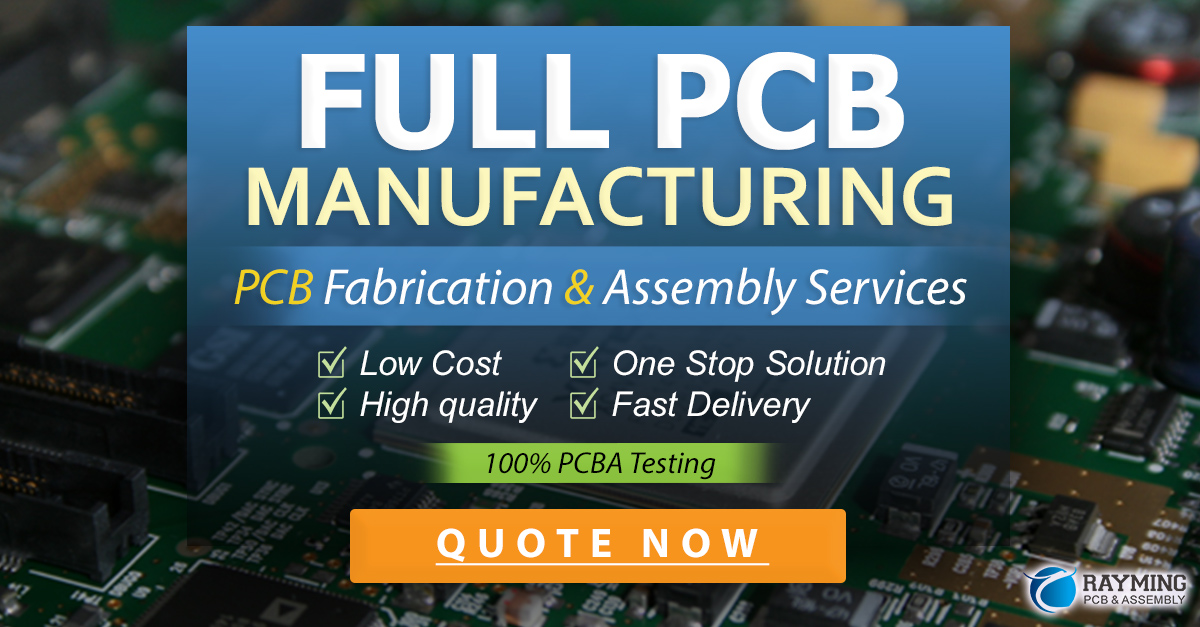
Inspection Methods and Guidelines
IPC-A-600 provides guidelines for inspecting PCBs to ensure they meet the specified acceptance criteria. The standard recommends a combination of visual inspection and measurement techniques to assess the quality of the PCB.
Visual Inspection
Visual inspection is the primary method for evaluating the acceptability of PCBs. Inspectors should use appropriate lighting, magnification, and viewing angles to examine the board for defects and imperfections. The standard provides detailed descriptions and images of acceptable and unacceptable conditions for each defect category.
Measurement Techniques
In addition to visual inspection, IPC-A-600 recommends using various measurement techniques to verify that the PCB meets the dimensional and physical requirements. These techniques include:
- Caliper measurements
- Micrometer measurements
- Optical comparator measurements
- Automated Optical Inspection (AOI)
- X-ray inspection
The choice of measurement technique depends on the specific requirement being verified and the accuracy needed.
Frequently Asked Questions (FAQ)
-
Q: What is the difference between Class 2 and Class 3 acceptance criteria?
A: Class 2 acceptance criteria are intended for dedicated service electronic products that require extended life and performance, while Class 3 criteria are reserved for high-reliability products where continued performance or performance-on-demand is critical. Class 3 has the most stringent requirements for defects and imperfections. -
Q: Can a PCB be classified as both Class 1 and Class 2?
A: No, a PCB must be classified under a single class based on its intended end-use and the level of reliability required. The classes are mutually exclusive. -
Q: What is the role of automated optical inspection (AOI) in IPC-A-600?
A: AOI is a measurement technique recommended by IPC-A-600 for verifying that a PCB meets the specified dimensional and physical requirements. It is particularly useful for inspecting large quantities of boards or detecting defects that may be difficult to identify through manual visual inspection. -
Q: Does IPC-A-600 cover the acceptance criteria for assembLED PCBs?
A: No, IPC-A-600 focuses on the acceptance criteria for bare PCBs prior to assembly. For acceptance criteria related to assembLED PCBs, refer to the IPC-A-610 standard. -
Q: How often should inspectors be trained on the IPC-A-600 standard?
A: Inspectors should receive initial training on the IPC-A-600 standard and periodic refresher training to ensure they are up-to-date with the latest requirements and inspection methods. The frequency of refresher training may vary depending on the organization and the complexity of the PCBs being inspected.
Conclusion
IPC-A-600 is a critical standard for ensuring the quality and reliability of printed circuit boards. By defining acceptance criteria based on three classes – Class 1 for general electronic products, Class 2 for dedicated service products, and Class 3 for high-reliability products – the standard provides a framework for evaluating PCBs based on their intended end-use.
Inspectors and quality control professionals should be well-versed in the defect categories, severity levels, and inspection methods outlined in IPC-A-600 to effectively assess the acceptability of PCBs. By adhering to this standard, manufacturers can produce PCBs that meet the required performance and reliability levels for their specific applications.
Leave a Reply