Introduction to Innerlayer imaging
Innerlayer imaging is a crucial process in the manufacturing of multilayer printed circuit boards (PCBs). It involves transferring the circuit pattern onto the copper-clad laminate, which will be used as an inner layer in the final PCB Stack-Up. The accuracy and precision of innerlayer imaging directly impact the functionality, reliability, and performance of the Multilayer PCB.
Importance of Innerlayer Imaging
Innerlayer imaging plays a vital role in the fabrication of multilayer PCBs for several reasons:
-
Circuit Pattern Transfer: Innerlayer imaging transfers the desired circuit pattern onto the copper-clad laminate, ensuring that the conductive traces and pads are accurately reproduced on the inner layers of the PCB.
-
Registration and Alignment: Precise innerlayer imaging is essential for maintaining proper registration and alignment between the different layers of the multilayer PCB. Misalignment can lead to connectivity issues and reduced reliability.
-
Signal Integrity: The quality of innerlayer imaging directly affects signal integrity in high-speed and high-frequency applications. Poor imaging can result in signal distortion, crosstalk, and electromagnetic interference (EMI).
-
Manufacturing Efficiency: Accurate innerlayer imaging reduces the likelihood of defects and improves the overall manufacturing efficiency by minimizing the need for rework or scrapping of defective boards.
Innerlayer Imaging Techniques
There are several techniques used for innerlayer imaging in multilayer PCB manufacturing. The choice of technique depends on factors such as the desired resolution, throughput, and cost. Here are some commonly used innerlayer imaging techniques:
1. Photolithography
Photolithography is the most widely used method for innerlayer imaging in PCB manufacturing. It involves the following steps:
-
Photoresist Application: A light-sensitive polymer, called photoresist, is applied evenly onto the copper-clad laminate using techniques like spin coating or roller coating.
-
Exposure: The photoresist-coated laminate is exposed to ultraviolet (UV) light through a photomask, which contains the desired circuit pattern. The UV light causes a chemical change in the exposed areas of the photoresist.
-
Development: The exposed laminate is then developed using a chemical developer solution. The developer removes either the exposed (positive photoresist) or unexposed (negative photoresist) areas of the photoresist, revealing the underlying copper pattern.
-
Etching: The developed laminate undergoes an etching process, where the exposed copper areas are chemically removed, leaving behind the desired circuit pattern protected by the remaining photoresist.
-
Stripping: Finally, the remaining photoresist is stripped off, leaving the copper circuit pattern on the laminate surface.
Photolithography offers high resolution and is suitable for fine-pitch designs. However, it requires the use of expensive photomasks and has a relatively lower throughput compared to other techniques.
2. Direct Imaging (DI)
Direct imaging is a maskless imaging technique that has gained popularity in recent years. It eliminates the need for physical photomasks by directly exposing the photoresist-coated laminate using a digital imaging system. The main advantages of direct imaging include:
-
Flexibility: DI allows for quick and easy changes to the circuit design without the need for new photomasks, reducing lead times and costs.
-
High Resolution: DI systems can achieve high resolutions, enabling the fabrication of fine-pitch designs and high-density interconnects (HDI).
-
Registration Accuracy: DI offers excellent registration accuracy, as the imaging is performed directly on the laminate without the need for manual alignment of photomasks.
However, DI systems have a higher initial investment cost compared to traditional photolithography
setups, and the imaging speed may be slower for large panel sizes.
3. Laser Direct Imaging (LDI)
Laser direct imaging (LDI) is a specific type of direct imaging that uses lasers to expose the photoresist. LDI systems employ high-power lasers, typically in the UV wavelength range, to selectively expose the photoresist according to the digital circuit pattern data. LDI offers several advantages:
-
High Speed: LDI systems can achieve high imaging speeds, making them suitable for high-volume production.
-
Fine Feature Resolution: LDI can produce extremely fine features and narrow trace widths, enabling the fabrication of high-density designs.
-
Depth of Focus: LDI has a large depth of focus, allowing for consistent imaging on non-planar surfaces or in the presence of substrate thickness variations.
However, LDI systems have a higher capital cost compared to other imaging techniques, and the laser source may require frequent maintenance and calibration.
Innerlayer Imaging Process Flow
The innerlayer imaging process flow typically involves the following steps:
-
Material Preparation: The copper-clad laminate is cleaned and prepared for photoresist application. This may include surface roughening to improve photoresist adhesion.
-
Photoresist Application: The photoresist is applied evenly onto the laminate surface using techniques like spin coating or roller coating. The thickness and uniformity of the photoresist layer are critical for successful imaging.
-
Pre-baking: The photoresist-coated laminate is pre-baked to remove solvents and improve adhesion. The pre-baking temperature and duration are carefully controlled to avoid overheating or underheating.
-
Imaging: The laminate is exposed to light (UV or laser) through a photomask or using a direct imaging system. The exposure time and energy are optimized based on the photoresist type and thickness.
-
Post-baking: After exposure, the laminate may undergo a post-baking step to further crosslink the exposed photoresist and improve its resistance to the developer solution.
-
Developing: The exposed laminate is developed using a chemical developer solution. The developer removes either the exposed or unexposed areas of the photoresist, depending on the photoresist type (positive or negative).
-
Inspection: The developed laminate is inspected for defects, such as incomplete development, residual photoresist, or pattern distortions. Automated optical inspection (AOI) systems are commonly used for this purpose.
-
Etching: The developed laminate undergoes an etching process to remove the exposed copper areas, leaving behind the desired circuit pattern protected by the remaining photoresist.
-
Stripping: The remaining photoresist is stripped off using a chemical stripper solution, revealing the final copper circuit pattern on the laminate surface.
-
Post-etching Inspection: The etched laminate is inspected again to ensure that the circuit pattern is accurately reproduced and free from defects such as over-etching or under-etching.
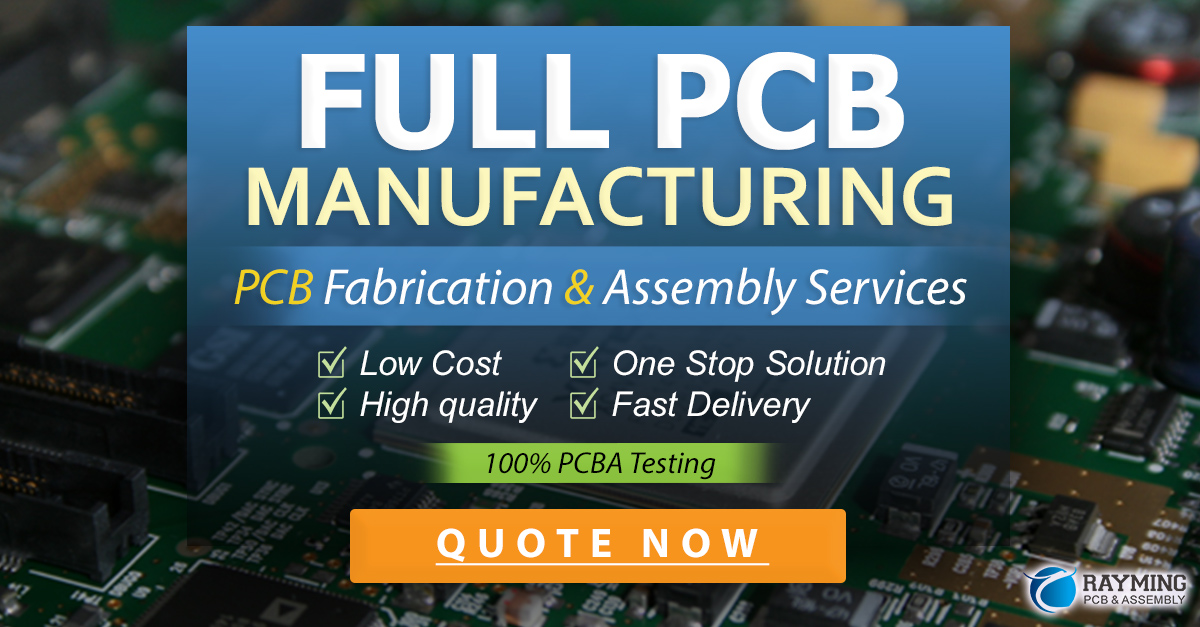
Challenges in Innerlayer Imaging
Innerlayer imaging presents several challenges that need to be addressed to ensure high-quality results:
-
Resolution and Feature Size: As PCB designs become more complex and miniaturized, achieving high resolution and fine feature sizes becomes increasingly challenging. Advanced imaging techniques and materials are required to meet these demands.
-
Registration and Alignment: Maintaining accurate registration and alignment between the different layers of a multilayer PCB is crucial. Misalignment can lead to connectivity issues and reduced reliability. Proper process control and advanced registration systems are necessary to minimize alignment errors.
-
Substrate Surface Quality: The surface quality of the copper-clad laminate can affect the adhesion and uniformity of the photoresist layer. Surface contamination, oxidation, or roughness can lead to defects in the imaged pattern. Proper substrate preparation and cleaning are essential for achieving high-quality imaging results.
-
Photoresist Thickness and Uniformity: The thickness and uniformity of the photoresist layer are critical factors in innerlayer imaging. Variations in photoresist thickness can result in non-uniform exposure and development, leading to pattern distortions or defects. Precise photoresist application methods and process control are necessary to maintain consistent photoresist thickness across the laminate.
-
Exposure and Development Control: Accurate control of exposure and development parameters is essential for achieving the desired circuit pattern. Overexposure or underexposure can lead to pattern distortions or incomplete development. Proper optimization of exposure time, energy, and developer concentration is required to ensure reliable imaging results.
-
Etching and Stripping: The etching and stripping processes must be carefully controlled to avoid over-etching or under-etching of the copper circuit pattern. Incomplete stripping of the photoresist can lead to residual contamination and affect subsequent processing steps. Proper selection of etchants, etch rates, and stripping chemicals is necessary to achieve clean and accurate circuit patterns.
Advancements in Innerlayer Imaging
Innerlayer imaging technology continues to evolve to meet the increasing demands of modern PCB designs. Some notable advancements include:
-
High-resolution Direct Imaging: Advanced direct imaging systems, such as those based on laser or multi-wavelength UV LEDs, offer improved resolution and imaging speed. These systems enable the fabrication of fine-pitch designs and high-density interconnects (HDI) with greater accuracy and efficiency.
-
Photoresist Materials: New photoresist materials have been developed to improve resolution, sensitivity, and processability. For example, chemically amplified resists (CARs) offer higher sensitivity and resolution compared to traditional photoresists. Additionally, dry film photoresists have gained popularity due to their ease of use and consistency in thickness.
-
Inkjet Imaging: Inkjet imaging is an emerging technology that uses inkjet printheads to selectively deposit photoresist or etch-resistant ink onto the copper-clad laminate. This approach offers the potential for high-resolution imaging without the need for photomasks or expensive imaging equipment.
-
Automated Inspection: Advanced automated optical inspection (AOI) systems have been developed to detect and analyze defects in the imaged circuit pattern. These systems use high-resolution cameras and machine vision algorithms to identify issues such as shorts, opens, or pattern distortions. Automated inspection helps improve quality control and reduce the reliance on manual inspection.
-
Computational Lithography: Computational lithography techniques, such as optical proximity correction (OPC) and source mask optimization (SMO), are being applied to innerlayer imaging to compensate for imaging distortions and improve pattern fidelity. These techniques involve modifying the photomask or imaging parameters based on computational models to achieve the desired circuit pattern on the laminate.
Conclusion
Innerlayer imaging is a critical process in the manufacturing of Multilayer PCBs. It plays a vital role in transferring the desired circuit pattern onto the inner layers of the PCB, ensuring proper functionality, reliability, and performance. Various imaging techniques, such as photolithography, direct imaging, and laser direct imaging, are used depending on the specific requirements of the PCB design.
To achieve high-quality innerlayer imaging results, it is essential to address challenges such as resolution, registration, substrate surface quality, photoresist thickness and uniformity, exposure and development control, and etching and stripping processes. Advancements in imaging technology, materials, and automation are continuously being developed to meet the increasing demands of modern PCB designs.
By understanding the principles, techniques, and challenges involved in innerlayer imaging, PCB manufacturers can optimize their processes, improve yields, and deliver high-quality multilayer PCBs that meet the ever-evolving needs of the electronics industry.
Frequently Asked Questions (FAQ)
- Q: What is the purpose of innerlayer imaging in Multilayer PCB Manufacturing?
A: Innerlayer imaging is used to transfer the desired circuit pattern onto the copper-clad laminate that will be used as an inner layer in the multilayer PCB stack-up. It ensures that the conductive traces and pads are accurately reproduced on the inner layers of the PCB, enabling proper connectivity and functionality.
- Q: What are the common techniques used for innerlayer imaging?
A: The most common techniques for innerlayer imaging include photolithography, direct imaging (DI), and laser direct imaging (LDI). Photolithography uses a photomask and UV light to expose the photoresist, while DI and LDI use digital imaging systems to directly expose the photoresist without the need for a physical photomask.
- Q: Why is registration accuracy important in innerlayer imaging?
A: Registration accuracy is crucial in innerlayer imaging because it ensures that the different layers of the multilayer PCB are properly aligned. Misalignment can lead to connectivity issues, signal integrity problems, and reduced reliability of the final PCB Assembly. Precise registration is necessary to maintain the desired electrical performance and functionality of the PCB.
- Q: What are some challenges faced during the innerlayer imaging process?
A: Some common challenges in innerlayer imaging include achieving high resolution and fine feature sizes, maintaining accurate registration and alignment between layers, ensuring proper substrate surface quality, controlling photoresist thickness and uniformity, optimizing exposure and development parameters, and managing etching and stripping processes to avoid defects.
- Q: How are advancements in innerlayer imaging technology addressing the challenges?
A: Advancements in innerlayer imaging technology, such as high-resolution direct imaging systems, improved photoresist materials, inkjet imaging, automated inspection, and computational lithography techniques, are helping to address the challenges associated with innerlayer imaging. These advancements enable the fabrication of fine-pitch designs, improve pattern fidelity, enhance quality control, and increase overall manufacturing efficiency.
Innerlayer Imaging Technique | Advantages | Disadvantages |
---|---|---|
Photolithography | – High resolution – Suitable for fine-pitch designs |
– Requires expensive photomasks – Lower throughput compared to other techniques |
Direct Imaging (DI) | – Flexibility in design changes – High resolution – Excellent registration accuracy |
– Higher initial investment cost – Slower imaging speed for large panel sizes |
Laser Direct Imaging (LDI) | – High imaging speed – Fine feature resolution – Large depth of focus |
– Higher capital cost – Requires frequent maintenance and calibration of laser source |
Leave a Reply