What is ICT?
In-Circuit Testing, or ICT, is an automated testing method used to verify the functionality and quality of PCBs. It involves using a specialized test fixture that makes contact with various points on the PCB, allowing the tester to measure and compare the electrical characteristics of each component against predefined specifications. This process helps identify manufacturing defects, such as short circuits, open circuits, incorrect component values, and missing or misplaced components.
How ICT Works
The ICT process typically follows these steps:
-
Test Fixture Design: A custom test fixture is designed specifically for the PCB being tested. The fixture consists of a bed of nails that matches the contact points on the PCB.
-
PCB Placement: The PCB is placed on the test fixture, ensuring proper alignment between the contact points and the bed of nails.
-
Electrical Testing: The ICT machine applies electrical signals to the PCB through the test fixture and measures the response at various points. This allows the machine to verify the presence, orientation, and value of each component on the board.
-
Comparison and Analysis: The measured values are compared against the expected values defined in the test program. Any deviations are flagged as potential defects.
-
Reporting: The ICT machine generates a detailed report indicating the pass/fail status of each tested PCB, along with information about any identified defects.
Benefits of ICT in PCB Production
Implementing ICT in your PCB production process offers several significant benefits:
-
Early Defect Detection: ICT allows you to identify defects early in the manufacturing process, reducing the risk of defective products reaching later stages of assembly or the end customer.
-
Improved Product Quality: By catching and correcting defects early, ICT helps ensure that your PCBs meet the required quality standards, resulting in a more reliable end product.
-
Reduced Costs: Identifying defects early in the production process minimizes the cost associated with rework, scrap, and warranty claims.
-
Increased Efficiency: ICT is an automated process that can test PCBs quickly and accurately, reducing the time and labor required for manual testing.
-
Comprehensive Testing: ICT can test a wide range of components and their interconnections, providing a thorough assessment of the PCB’s functionality.
Implementing ICT in Your PCB Production Process
To effectively implement ICT in your PCB production process, consider the following steps:
-
Define Test Requirements: Determine the specific test requirements for your PCBs, including the components to be tested, test points, and acceptable tolerance ranges.
-
Design for Testability: Ensure that your PCB design incorporates features that facilitate ICT, such as test points, adequate spacing between components, and clear labeling.
-
Select an ICT System: Choose an ICT system that meets your testing requirements and is compatible with your PCB design. Consider factors such as test coverage, speed, and ease of use.
-
Develop Test Programs: Create test programs that define the specific tests to be performed on each PCB, including the expected values and tolerance ranges for each component.
-
Integrate ICT into Production: Incorporate ICT into your production workflow, ensuring that all PCBs undergo testing at the appropriate stage.
-
Analyze and Optimize: Regularly analyze the results of your ICT process and use the data to identify areas for improvement in your PCB design and manufacturing processes.
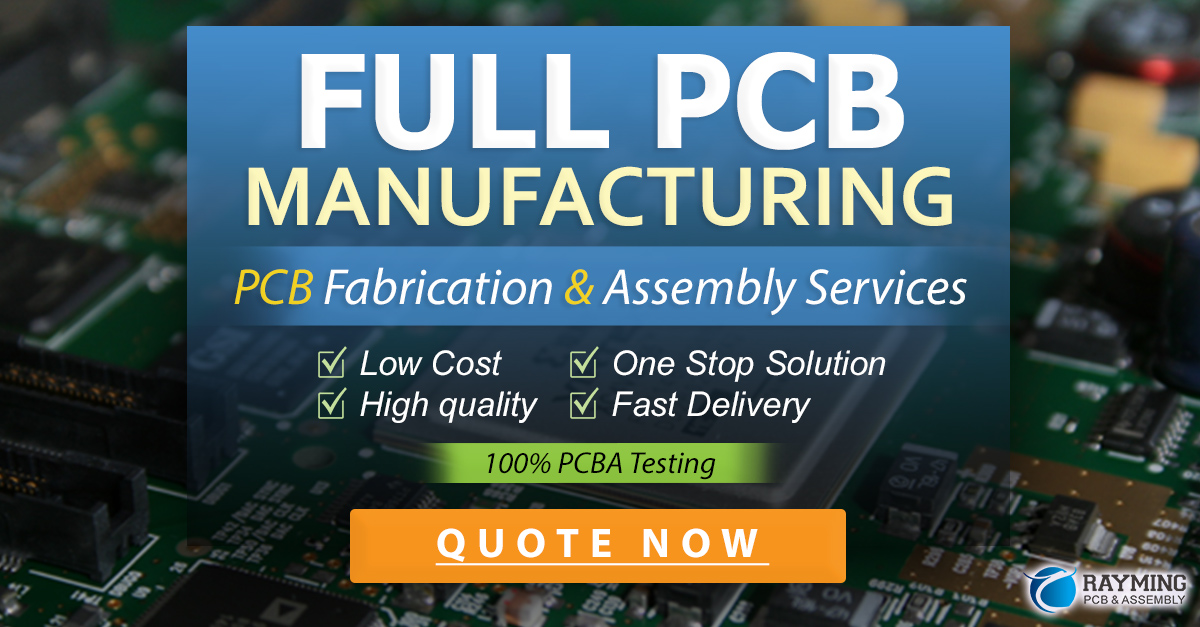
Common ICT Challenges and Solutions
While ICT offers numerous benefits, there are also some challenges that manufacturers may face when implementing this testing method. Here are a few common challenges and their potential solutions:
Challenge | Solution |
---|---|
Test Fixture Complexity | Invest in advanced fixture design software and work closely with experienced fixture designers to create efficient and reliable test fixtures. |
Limited Test Coverage | Supplement ICT with other testing methods, such as boundary scan or functional testing, to achieve comprehensive test coverage. |
High Initial Investment | Consider the long-term benefits of ICT, such as improved product quality and reduced rework costs, when evaluating the return on investment. |
Adapting to Design Changes | Establish a strong collaboration between design and test teams to ensure that design changes are communicated effectively and test programs are updated accordingly. |
Frequently Asked Questions (FAQ)
-
Q: What types of defects can ICT detect?
A: ICT can detect a wide range of defects, including short circuits, open circuits, incorrect component values, and missing or misplaced components. -
Q: Can ICT be used for both through-hole and surface-mount components?
A: Yes, ICT can be used to test both through-hole and surface-mount components on a PCB. -
Q: How does ICT differ from functional testing?
A: ICT focuses on testing individual components and their interconnections, while functional testing verifies the overall functionality of the assembled PCB or product. -
Q: Is ICT suitable for low-volume production?
A: While ICT is most cost-effective for high-volume production, it can still be beneficial for low-volume runs, particularly for complex or high-reliability products. -
Q: Can ICT be performed on PCBs with conformal coating?
A: Yes, ICT can be performed on PCBs with conformal coating, but it may require specialized test probes and fixtures to ensure proper contact with the test points.
Conclusion
In-Circuit Testing is a powerful tool for ensuring the quality and reliability of PCBs in electronics manufacturing. By detecting and identifying defects early in the production process, ICT helps manufacturers produce high-quality products while reducing costs and improving efficiency. Implementing ICT in your PCB production process requires careful planning, design considerations, and the selection of an appropriate test system. By understanding the benefits and challenges of ICT and following best practices for implementation, you can harness the full potential of this testing method to enhance your PCB production capabilities and deliver superior products to your customers.
Leave a Reply