What is a Hydrogen Sensor?
A hydrogen sensor is a safety device designed to detect the presence of hydrogen gas in the surrounding environment. These sensors are capable of measuring hydrogen concentrations in real-time and triggering alarms or safety measures when the levels exceed predetermined thresholds. The primary purpose of a hydrogen sensor is to prevent accidents, explosions, and fires caused by hydrogen leaks or accumulations.
The Importance of Hydrogen Sensors
Ensuring Safety in Hydrogen Applications
Hydrogen’s high flammability and wide explosive range (4-75% in air) make it a potential hazard in various applications. Even small leaks or accumulations of hydrogen can lead to catastrophic consequences if not detected and addressed promptly. Hydrogen sensors play a vital role in ensuring safety by continuously monitoring the environment and alerting personnel to any potential dangers.
Compliance with Regulations and Standards
Various industries and applications involving hydrogen are subject to stringent safety regulations and standards. These regulations often mandate the use of hydrogen sensors to ensure compliance and maintain a safe working environment. Failure to adhere to these regulations can result in legal consequences and jeopardize the safety of personnel and facilities.
Protecting Assets and Infrastructure
Hydrogen leaks and explosions can cause significant damage to assets and infrastructure, leading to costly repairs, downtime, and loss of productivity. By detecting hydrogen leaks early, sensors help prevent such incidents and protect valuable assets, ultimately saving companies time and money.
Types of Hydrogen Sensors
Several types of hydrogen sensors are available, each with its own working principles and advantages. The most common types include:
Electrochemical Sensors
Electrochemical hydrogen sensors operate based on the oxidation of hydrogen gas at an electrode surface. They consist of a sensing electrode, a counter electrode, and an electrolyte. When hydrogen gas comes into contact with the sensing electrode, it oxidizes and generates an electrical current proportional to the hydrogen concentration. These sensors are known for their high sensitivity, selectivity, and fast response times.
Catalytic Sensors
Catalytic hydrogen sensors, also known as pellistor sensors, rely on the combustion of hydrogen gas on a catalytic surface. They consist of two elements: an active bead coated with a catalyst and a reference bead. When hydrogen gas comes into contact with the active bead, it combusts, causing a temperature increase. The temperature difference between the active and reference beads is measured and correlated to the hydrogen concentration. Catalytic sensors are durable and have a long lifespan but may be affected by catalyst poisoning.
Semiconductor Sensors
Semiconductor hydrogen sensors utilize the change in electrical conductivity of a semiconductor material in the presence of hydrogen gas. These sensors typically consist of a metal oxide semiconductor (MOS) layer deposited on a substrate. When hydrogen gas interacts with the MOS layer, it alters its electrical conductivity, which is measured and correlated to the hydrogen concentration. Semiconductor sensors are compact, cost-effective, and have a wide detection range.
Optical Sensors
Optical hydrogen sensors leverage the interaction of hydrogen gas with light to detect its presence. They can be based on various optical phenomena, such as absorption, fluorescence, or refractive index changes. These sensors use a light source, a sensing material, and a detector. When hydrogen gas interacts with the sensing material, it alters the optical properties, which are detected and analyzed to determine the hydrogen concentration. Optical sensors offer high selectivity, immunity to electromagnetic interference, and the ability to operate in harsh environments.
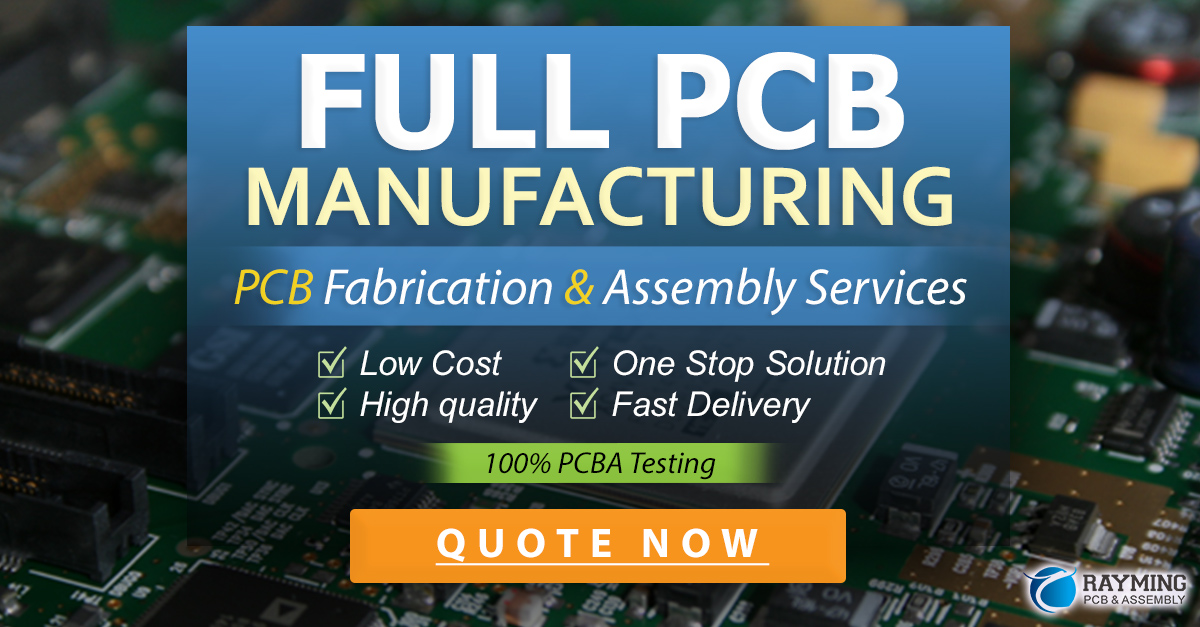
Working Principles of Hydrogen Sensors
Electrochemical Sensing
Electrochemical hydrogen sensors work on the principle of electrochemical oxidation. When hydrogen gas diffuses through a permeable membrane and reaches the sensing electrode, it oxidizes and releases electrons. These electrons flow through an external circuit, generating a current proportional to the hydrogen concentration. The counter electrode balances the electrochemical reaction, while the electrolyte facilitates the ion transport between the electrodes.
Catalytic Combustion
Catalytic hydrogen sensors rely on the combustion of hydrogen gas on a catalytic surface. The active bead, coated with a catalyst such as platinum or palladium, promotes the combustion of hydrogen when it comes into contact with the gas. The heat generated during combustion increases the temperature of the active bead, while the reference bead remains at ambient temperature. The temperature difference between the beads is measured using a Wheatstone bridge circuit and correlated to the hydrogen concentration.
Semiconductor Conductivity
Semiconductor hydrogen sensors exploit the change in electrical conductivity of a metal oxide semiconductor material in the presence of hydrogen gas. When hydrogen molecules interact with the MOS layer, they dissociate and diffuse into the material, altering its electrical properties. The change in conductivity is measured and correlated to the hydrogen concentration. The sensitivity and selectivity of semiconductor sensors can be enhanced by incorporating noble metal catalysts or using nanostructured materials.
Optical Sensing
Optical hydrogen sensors utilize the interaction of hydrogen gas with light to detect its presence. Various optical phenomena can be employed, such as absorption, fluorescence, or refractive index changes. In absorption-based sensors, hydrogen gas absorbs specific wavelengths of light, reducing the intensity of the transmitted or reflected light. Fluorescence-based sensors rely on the quenching or enhancement of fluorescence emission in the presence of hydrogen. Refractive index-based sensors measure the change in the refractive index of a sensing material upon exposure to hydrogen gas. The optical changes are detected and analyzed to determine the hydrogen concentration.
Applications of Hydrogen Sensors
Hydrogen sensors find applications in various industries and sectors where hydrogen is used or produced. Some key applications include:
Fuel Cell Systems
Fuel cells, which convert hydrogen and oxygen into electricity, require hydrogen sensors to ensure safe operation. These sensors monitor the hydrogen concentration in the fuel cell stack, detecting any leaks or abnormalities. They help prevent hydrogen accumulation, which can lead to explosions or damage to the fuel cell components.
Hydrogen Refueling Stations
As the demand for hydrogen-powered vehicles grows, the need for safe and reliable hydrogen refueling stations becomes crucial. Hydrogen sensors are deployed in these stations to monitor the hydrogen concentration during refueling operations. They detect leaks or accumulations of hydrogen, triggering alarms and safety measures to prevent accidents.
Industrial Processes
Many industrial processes, such as petroleum refining, chemical manufacturing, and metallurgy, involve the use or production of hydrogen. Hydrogen sensors are installed in these facilities to monitor the hydrogen levels in various process streams, storage tanks, and pipelines. They help prevent hydrogen-related accidents and ensure compliance with safety regulations.
Aerospace and Aviation
Hydrogen is used as a propellant in rocket engines and as a potential fuel for aircraft. Hydrogen sensors play a critical role in ensuring the safe handling and storage of hydrogen in these applications. They monitor the hydrogen concentration in propulsion systems, fuel tanks, and surrounding areas to detect leaks and prevent hazardous situations.
Laboratory and Research Facilities
Laboratories and research facilities often handle hydrogen gas for various experiments and applications. Hydrogen sensors are installed in these environments to monitor the hydrogen concentration and ensure the safety of personnel. They detect leaks or accidental releases of hydrogen, triggering alarms and initiating emergency procedures.
Future Prospects and Challenges
Advancements in Sensor Technology
The field of hydrogen sensor technology is continuously evolving, with ongoing research and development efforts aimed at improving sensor performance, reliability, and cost-effectiveness. Advancements in materials science, nanotechnology, and manufacturing techniques are enabling the development of highly sensitive, selective, and durable hydrogen sensors. Researchers are exploring novel sensing materials, such as graphene, metal-organic frameworks (MOFs), and nanocomposites, to enhance sensor capabilities.
Integration with Internet of Things (IoT)
The integration of hydrogen sensors with the Internet of Things (IoT) is a promising trend that enables remote monitoring, data analytics, and predictive maintenance. By connecting hydrogen sensors to IoT platforms, real-time data can be collected, analyzed, and visualized, allowing for early detection of anomalies and proactive safety measures. IoT integration also facilitates remote control and automation of safety systems, enhancing overall efficiency and responsiveness.
Challenges and Limitations
Despite the advancements in hydrogen sensor technology, several challenges and limitations persist. One of the main challenges is the development of sensors that can operate reliably in harsh environments, such as high temperatures, pressures, or corrosive atmospheres. Ensuring long-term stability and calibration of sensors is another challenge, as drift and degradation can affect accuracy over time. Additionally, the cost of hydrogen sensors remains a barrier to widespread adoption, particularly in cost-sensitive applications.
Frequently Asked Questions (FAQ)
-
Q: What is the detection range of hydrogen sensors?
A: The detection range of hydrogen sensors varies depending on the type and design of the sensor. Most hydrogen sensors can detect hydrogen concentrations from a few parts per million (ppm) to the lower explosive limit (LEL) of 4% by volume in air. Some sensors are capable of detecting even higher concentrations. -
Q: How often should hydrogen sensors be calibrated?
A: The calibration frequency of hydrogen sensors depends on factors such as the sensor type, operating conditions, and manufacturer recommendations. Generally, hydrogen sensors should be calibrated at least annually to ensure accurate and reliable performance. In critical applications or harsh environments, more frequent calibration may be necessary. -
Q: Can hydrogen sensors detect other gases?
A: Hydrogen sensors are designed to specifically detect hydrogen gas. However, some sensors may exhibit cross-sensitivity to other gases with similar properties, such as carbon monoxide or hydrocarbons. It is important to select sensors with high selectivity to hydrogen and consider the potential presence of interfering gases in the application environment. -
Q: What is the response time of hydrogen sensors?
A: The response time of hydrogen sensors varies depending on the sensor technology and design. Electrochemical sensors typically have fast response times, ranging from a few seconds to a minute. Catalytic sensors may have slightly slower response times, while semiconductor and optical sensors can have response times in the range of seconds to minutes. -
Q: How long do hydrogen sensors last?
A: The lifespan of hydrogen sensors depends on factors such as the sensor type, operating conditions, and maintenance practices. Electrochemical sensors typically have a lifespan of 2-3 years, while catalytic sensors can last up to 5 years or more. Semiconductor and optical sensors can have longer lifespans, but their performance may degrade over time due to aging effects or contamination.
Conclusion
Hydrogen sensors are essential safety devices that play a critical role in ensuring the safe use and handling of hydrogen in various applications. By detecting hydrogen leaks and accumulations in real-time, these sensors help prevent accidents, comply with regulations, and protect assets and infrastructure. The different types of hydrogen sensors, including electrochemical, catalytic, semiconductor, and optical sensors, offer unique advantages and working principles suited for specific requirements.
As the demand for clean energy and the adoption of hydrogen technologies continue to grow, the importance of hydrogen sensors will only increase. Ongoing research and development efforts are focused on improving sensor performance, reliability, and cost-effectiveness. The integration of hydrogen sensors with IoT platforms opens up new possibilities for remote monitoring, data analytics, and predictive maintenance.
However, challenges such as operating in harsh environments, ensuring long-term stability, and reducing costs need to be addressed to facilitate widespread adoption. Continued advancements in sensor technology, materials science, and manufacturing processes will be crucial in overcoming these challenges and realizing the full potential of hydrogen sensors in enabling a safer and more sustainable hydrogen economy.
Leave a Reply