What is Pad Synchronization?
Pad synchronization refers to the process of ensuring that the pads in your PCB layout match up with the corresponding pads defined in your schematic or logical design. It involves:
- Verifying that all the necessary pads are present in both the schematic and layout
- Checking that the pads are properly connected to the correct nets
- Ensuring that the pad properties (such as shape, size, drill hole, etc.) match between the logical and physical designs
Proper pad synchronization is essential because any mismatches or discrepancies can lead to connectivity issues, manufacturing problems, or even complete failure of the assembled PCB. It’s a critical step in the design process that requires attention to detail and a systematic approach.
The Importance of Synchronizing Pads
There are several key reasons why synchronizing your pads logic and layout is so important:
1. Ensuring Correct Connectivity
The primary purpose of pad synchronization is to guarantee that your PCB will have the correct electrical connections as intended in your schematic. If pads are mismatched or not properly connected, it can result in open or short circuits, leading to malfunctions or complete failure of the board.
2. Facilitating Proper Manufacturing
Pad synchronization is also critical for ensuring your PCB can be properly manufactured. The pad properties in your layout need to match the logical definitions so that the correct footprints are used for each component. Mismatched pads can cause issues with soldering, assembly, and inspection.
3. Enabling Design Reuse
Having synchronized pads also facilitates design reuse and modification. If you need to update your schematic or create a new layout based on an existing design, having the pads properly matched up makes it much easier to port the logical design and minimizes the risk of introducing errors.
4. Improving Design Efficiency
Taking the time to synchronize your pads upfront can actually improve your overall design efficiency. By catching and correcting any mismatches early, you avoid lengthy troubleshooting later on when issues crop up during manufacturing or assembly. It’s much more time-efficient to get the pad synchronization right the first time.
The Pad Synchronization Process
Now that we understand the importance of pad synchronization, let’s look at the actual process of synchronizing pads between your logic and layout. While the exact steps may vary somewhat depending on your EDA tools, the general flow is as follows:
1. Create the Schematic
The first step is to create your schematic or logical design. This is where you define the components, nets, and connections that make up your circuit. As you place components, pay attention to the pad definitions and make sure they match the footprints you plan to use in the layout.
2. Generate a Netlist
Once your schematic is complete, the next step is to generate a netlist. The netlist is a text file that captures all the connectivity information from your schematic, including the components, pads, nets, and pin assignments. It serves as the link between your logical and physical designs.
3. Import the Netlist into Your Layout Tool
With the netlist generated, you can now import it into your PCB layout tool. This process maps the logical definitions from the schematic to the physical components and footprints in your layout. The EDA tool will read in the netlist and attempt to match up the pads and connections.
4. Resolve Any Discrepancies
During the netlist import, your EDA tool will likely flag any discrepancies or mismatches between the schematic and layout. This is where you need to carefully review each issue and determine how to resolve it. Common problems include:
- Missing pads in the layout
- Incorrect pad types or sizes
- Unmatched net names
- Inconsistent pin assignments
To resolve these issues, you’ll need to make the necessary changes in either the schematic or layout (or both) to bring them into alignment. This may involve updating footprints, renaming nets, or reassigning pins.
5. Verify the Synchronization
After resolving any discrepancies, it’s important to verify that the pad synchronization is complete and accurate. Most EDA tools have a “design rule check” (DRC) function that can compare the schematic and layout and flag any remaining issues. Run the DRC and carefully review the results to ensure there are no outstanding mismatches.
6. Update and Re-synchronize as Needed
Pad synchronization is not a one-time event but rather an ongoing process throughout the design cycle. As you make changes and updates to your schematic or layout, it’s important to re-run the synchronization process to ensure the two stay in alignment. Make sure to generate an updated netlist, re-import it into your layout tool, and verify the synchronization again after any significant changes.
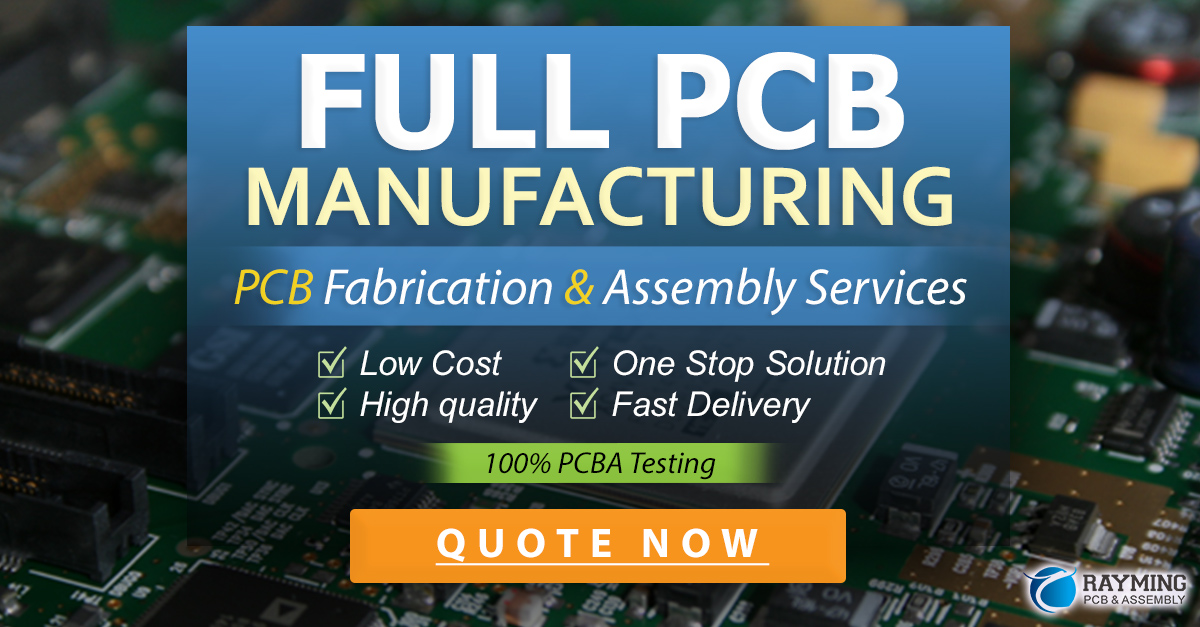
Best Practices for Effective Pad Synchronization
To ensure a smooth and efficient pad synchronization process, there are several best practices and guidelines to follow:
1. Use Consistent Naming Conventions
One of the most important things you can do to facilitate pad synchronization is to use clear and consistent naming conventions for your components, nets, and pads. This makes it much easier to match up the logical and physical elements and avoid confusion. Some tips for effective naming:
- Use descriptive names that indicate the function or purpose of each element
- Follow a consistent format and syntax for names (e.g. “Resistor_1”, “Capacitor_2”, etc.)
- Avoid using special characters or spaces in names, which can cause issues with some tools
2. Choose Appropriate Footprints
When selecting footprints for your components in the schematic, make sure they match the actual physical parts you plan to use in the layout. Using incorrect or mismatched footprints is a common source of pad synchronization issues. Some guidelines:
- Use footprints from a trusted library or create your own based on manufacturer datasheets
- Double-check the pad sizes, shapes, and spacing to ensure they match the real component
- Consider the manufacturing tolerances and assembly requirements when choosing footprints
3. Define Net Classes and Constraints
Another way to improve pad synchronization is to define net classes and constraints in your schematic. This allows you to specify things like trace widths, spacing, via sizes, and differential pairs upfront, which can then be carried over to the layout. Benefits of using net classes and constraints:
- Ensures consistent routing and layout for critical nets
- Reduces the risk of manual errors or oversights
- Makes it easier to ensure your layout meets your design requirements
4. Communicate Design Intent
If you’re working with a larger design team, it’s important to clearly communicate the design intent and requirements to all stakeholders. This includes providing detailed documentation, schematics, and constraints files to the layout designers. The more information you can provide upfront, the easier it will be to achieve proper pad synchronization and avoid misunderstandings.
5. Leverage EDA Tool Automation
Modern EDA tools offer a range of features and automation to assist with pad synchronization. Take advantage of these capabilities to streamline your process and reduce the risk of errors. Some examples:
- Automatic footprint assignment based on component properties
- Real-time design rule checking to flag synchronization issues as you work
- Batch processing and scripting to handle repetitive tasks
- Integration between schematic and layout tools to facilitate data exchange
By leveraging the automation features in your EDA tools, you can significantly speed up the pad synchronization process and improve the overall quality of your designs.
Troubleshooting Common Issues
Even with the best practices and processes in place, issues can still arise during pad synchronization. Here are some of the most common problems and how to troubleshoot them:
1. Missing or Unmatched Pads
If you encounter missing or unmatched pads during synchronization, the first step is to determine the root cause. Some possible reasons:
- The footprint assigned in the schematic doesn’t match the actual component
- The pad numbers or names are inconsistent between the schematic and layout
- There are missing or extra pads in either the schematic or footprint
To resolve these issues, double-check the component and footprint assignments, verify the pad numbers and names, and make any necessary updates to bring the two into alignment.
2. Incorrect Net Connections
Another common issue is incorrect or missing net connections after synchronization. This can happen if:
- The net names are inconsistent between the schematic and layout
- There are shorts or open circuits in the schematic or layout
- The routing or placement in the layout is introducing unintended connections
To troubleshoot these issues, carefully review the net assignments in both the schematic and layout, and use your EDA tool’s connectivity highlighting and tracing features to identify any discrepancies. Make the necessary changes to correct any shorts, opens, or incorrect connections.
3. Inconsistent Constraints and Rules
If you’re seeing violations or inconsistencies in your design rules or constraints after synchronization, it may be due to:
- Incorrect or missing constraints defined in the schematic
- Overridden or conflicting rules in the layout
- Inconsistent settings between the schematic and layout tools
To resolve these issues, review your constraint definitions in the schematic and make sure they match your intended design requirements. Double-check any rule settings in your layout tool and ensure they are consistent with the schematic. If necessary, re-import the netlist and constraints into your layout tool to ensure the latest data is being used.
Frequently Asked Questions
1. How often should I synchronize my pads?
It’s a good practice to synchronize your pads after any significant changes to your schematic or layout. This includes adding or removing components, updating net assignments, or modifying footprints. At a minimum, you should synchronize before generating your final manufacturing files to ensure everything is properly aligned.
2. What if I can’t find a footprint that matches my component?
If you can’t find a suitable footprint in your EDA tool’s library, you may need to create a custom footprint. This involves measuring the physical dimensions and pad layout of your component and creating a new footprint that matches those specifications. Make sure to double-check your measurements and verify the final footprint against the manufacturer’s datasheet.
3. Can I Synchronize pads across multiple schematic pages or layout files?
Yes, most EDA tools support synchronization across multiple pages or files. The process typically involves generating a master netlist that combines all the individual pages or files, and then importing that master netlist into your layout tool. Make sure to follow your EDA tool’s specific instructions for multi-page or multi-file synchronization.
4. What if I have a large number of synchronization issues to resolve?
If you have a large number of synchronization issues, it may be more efficient to address them in batches rather than individually. Most EDA tools have batch processing or scripting capabilities that allow you to apply changes to multiple items at once. This can save significant time and effort, especially for larger or more complex designs.
5. How can I prevent pad synchronization issues in the future?
The best way to prevent pad synchronization issues is to follow best practices and establish a clear design process that includes regular synchronization checks. This may involve:
- Defining and communicating design standards and conventions to all team members
- Using automation and scripting to handle repetitive tasks and reduce the risk of manual errors
- Implementing version control and change management processes to track and manage design changes
- Conducting regular design reviews and quality checks to catch issues early in the process
By being proactive and establishing a robust design process, you can minimize the risk of pad synchronization issues and ensure a smoother, more efficient design cycle.
Conclusion
Synchronizing your pads logic and layout is a critical step in the PCB design process that ensures your board will be functional, manufacturable, and reliable. By following the steps and best practices outlined in this article, you can streamline your synchronization process, catch and resolve issues early, and ultimately create higher-quality designs.
Remember, pad synchronization is an ongoing process that requires attention to detail, communication, and a systematic approach. By staying vigilant and regularly verifying the alignment between your logical and physical designs, you can avoid costly mistakes and delays down the line.
With the right tools, processes, and mindset, you can master the art of pad synchronization and take your PCB designs to the next level. Happy designing!
Leave a Reply