Introduction to EasyEDA and Common Issues
EasyEDA is a powerful, web-based EDA (Electronic Design Automation) tool for designing, simulating, and producing printed circuit boards (PCBs). It offers schematic capture, circuit simulation, PCB layout, and more in an easy-to-use interface accessible from any web browser.
While EasyEDA simplifies the PCB design process, users may still encounter various issues and problems. Some common problems include:
- Schematic capture issues (component placement, wiring, netlists)
- Circuit simulation problems (SPICE models, simulation errors)
- PCB layout difficulties (component placement, routing, design rule checks)
- Manufacturing file generation issues (Gerber files, drill files, BOM)
This guide provides step-by-step troubleshooting tips for solving these types of problems in EasyEDA. By following the advice and instructions, you can overcome obstacles, complete your designs, and successfully manufacture your PCBs.
Solving Schematic Capture Problems in EasyEDA
Component Selection and Placement
One of the first steps in schematic capture is selecting and placing components. EasyEDA provides an extensive built-in library of components. However, you may encounter issues such as:
- Desired component not found in library
- Incorrect component footprint
- Difficulty placing or moving components
To solve component selection and placement problems, try these tips:
-
Thoroughly search the built-in EasyEDA libraries before creating a new component. Use the search box and filter options to find the part you need.
-
If you can’t find the exact part, look for a similar generic component that you can modify to match your needs. For example, use a generic resistor and change its value.
-
To make a new component, right-click in the component library window and select “New Component.” Enter the component details and save it to “My Parts” for easy future access.
-
Verify that components have the correct PCB footprint assigned to them. This is critical for proper PCB layout later. Open the component properties to check or modify the footprint.
-
If you have trouble placing or moving a component, make sure it is not locked. Right-click and choose “Unlock” if needed. Also ensure “Auto Router Obstacle” is unchecked unless you want the part to stay fixed.
Wiring and Netlists
After placing components, you need to wire them together to define the circuit connections and generate the netlist for layout. Wiring problems can include:
- Messy or unclear wire routing
- Missing or incorrect wire connections
- ERC (electrical rule check) errors
- Incorrect netlist generation
Follow these guidelines to troubleshoot wiring and netlist issues:
-
To clean up messy wiring, select the wires and right-click to choose “Reroute Selected Wires.” EasyEDA will automatically optimize the routing.
-
Use the “Show/Hide Rats Nest” button to toggle visibility of airwires indicating missing connections. Connect any dangling airwires.
-
Run the ERC tool under “Design Rule Check” to find and fix any electrical errors like unconnected wires, shorted nets, etc. Double-click an error in the ERC results to zoom to its location.
-
Before generating the netlist, go to “View” and enable “Net Coloring.” Visually confirm that wires you expect to be connected share the same color.
-
After generating the netlist, open the “.net” file and verify the connections match your expectations. Correct any errors in the schematic and re-generate the netlist.
Overcoming Circuit Simulation Issues
SPICE Models
EasyEDA includes a SPICE circuit simulator for verifying designs. For successful simulation, you need accurate SPICE models for the components in your circuit. Common SPICE model problems include:
- Missing models for certain components
- Incorrect or incompatible model parameters
- Convergence errors during simulation
Use these techniques to solve SPICE model issues:
-
For common generic parts like resistors and capacitors, EasyEDA will automatically assign default SPICE models. Verify the automatically chosen model is appropriate for your component.
-
For specialized parts like ICs, you may need to manually assign the SPICE model. Check the component datasheet or vendor website for the SPICE model or simulation parameters.
-
If you can’t find the exact SPICE model, search for a compatible model with similar specifications. Minor differences in model parameters are usually okay for basic simulations.
-
Make sure the SPICE model is in the correct format and has the proper file extension (“.lib” or “.cir” for ngspice). Convert models in other formats if needed.
-
If you get convergence errors, try adjusting the simulation parameters like maximum timestep and relative tolerance. Consult the EasyEDA documentation for guidance on SPICE options.
Simulation Errors and Troubleshooting
Besides model issues, other problems can occur when running simulations in EasyEDA. Some examples are:
- Simulation fails to start
- Nonsensical or unexpected results
- Slow simulation performance
Debug circuit simulation problems with these steps:
-
Make sure your schematic is complete and passes ERC. Simulation won’t run if there are any electrical rule errors.
-
Check that you’ve specified the correct simulation type (AC, DC, transient) and set up the input sources and output probes properly.
-
Click “Run the Document” before “Run the Simulation.” This updates the netlist and simulation settings to match the current schematic.
-
Start with a simple simulation and verify the results make sense. Then gradually enable more complex analysis options and review the results at each stage.
-
If simulation is slow, try reducing the time span, increasing the timestep, or lowering max iterations. Break large circuits into smaller subcircuits to simulate separately.
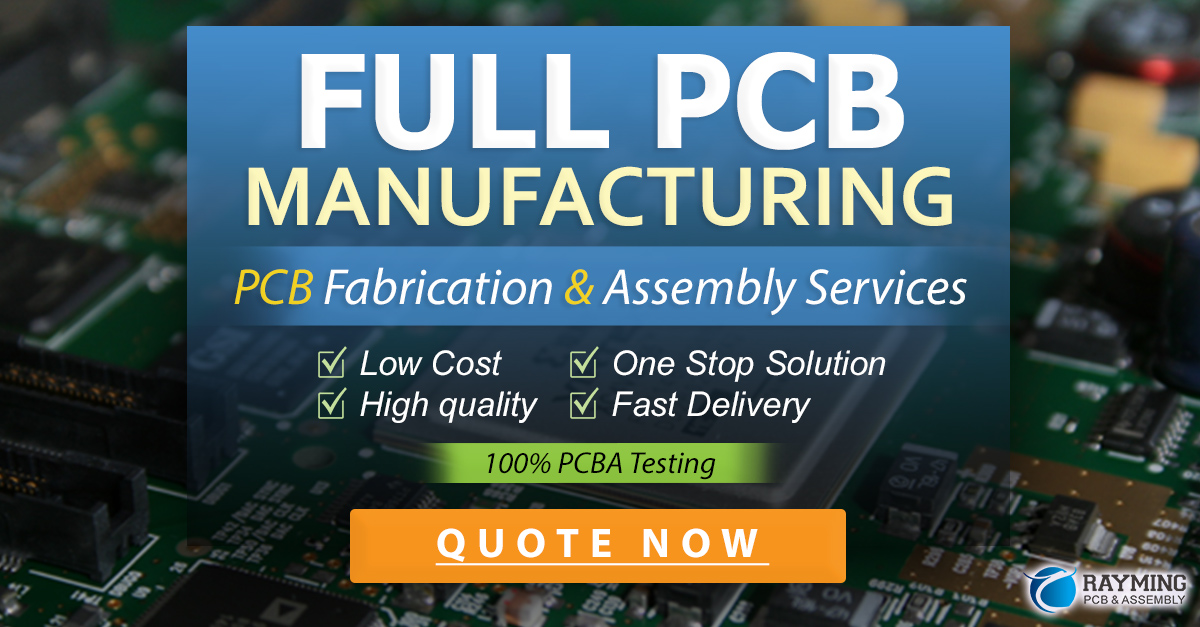
Troubleshooting PCB Layout Problems
Component Placement and Footprints
PCB layout starts with arranging components on the board. Parts must have correct footprints and be placed to minimize wiring while avoiding interference. Issues can arise such as:
- Components overlapping or too close
- Incorrect footprint size or pinout
- Inefficient Component Arrangement for routing
Tackle PCB component placement problems with this advice:
-
Use the “Design Rule Check” (DRC) tool in the PCB editor to find and fix overlapping components and other placement errors.
-
Verify that the footprint matches the physical dimensions and pinout of your component. Open the footprint in the library editor to check.
-
If needed, create a new footprint or modify an existing one. Make sure to double-check all dimensions and pad assignments.
-
Arrange components to minimize wiring length and complexity. Put related components close together. Avoid crossing wires when possible.
-
Consider mechanical factors like connector placement, mounting holes, and keep-out areas when placing components. Refer to your enclosure or mechanical drawings.
Routing and Design Rule Checks
After placing components, you route traces to connect the parts according to the netlist. Routing can be tricky, especially for dense designs or high-speed signals. Problems include:
- Routes violating design rules (e.g. trace spacing)
- Traces too thin or too close to board edge
- Analog/digital crosstalk and noise
- Insufficient copper pour and grounding
Use these tips to resolve common routing headaches:
-
Set up your PCB design rules at the start of layout. Specify trace width, spacing, drill size, etc. based on your PCB manufacturer’s capabilities.
-
Run DRC frequently to catch rule violations early. aim to fix them as you go rather than waiting until the end.
-
If you’re having trouble routing a dense area, try rearranging the components. Rotate them or swap their locations to open up more space.
-
To reduce crosstalk and noise, separate analog and digital sections of the board. Route sensitive signals away from noisy ones like power lines or high-speed clocks.
-
After finishing routing, add copper pours on the top and bottom layers. This helps with grounding, shielding, and heat dissipation. Make sure to stitch pours together with vias.
Generating Manufacturing Files
Gerber Files and Drill Files
When your PCB layout is complete, you need to generate the manufacturing files to send to a PCB fab house. These include Gerber files for each layer and drill files. Some common issues are:
- Wrong Gerber file format
- Missing drill hits or plated holes
- Incorrect layer stackup or board outline
Implement these practices to create trouble-free manufacturing files:
-
Consult with your PCB manufacturer about their preferred Gerber and drill file formats. Some common options are RS-274X, Gerber X2, and Excellon.
-
In the “Generate PCB fabrication File” dialog, make sure all the necessary copper, mask, silk, and drill layers are selected. Do not include the component overlay layers.
-
Double-check that the drill file accounts for all the holes in the board, including vias, mounting holes, and plated through holes. Review the drill file in a Gerber viewer.
-
Verify that the PCB outline is a fully closed shape on the mechanical layer. Use the “Design Rule Check” to find any gaps or overlaps.
-
Send the generated files to your manufacturer for a pre-production review before placing your final order. They can alert you of any manufacturability issues.
Bill of Materials (BOM)
In addition to the fabrication files, you also need to generate the bill of materials (BOM) for PCB Assembly. The BOM lists all the components, quantities, and part numbers. Typical BOM problems include:
- Inconsistent or missing part numbers
- Incorrect quantities or reference designators
- Incompatible BOM file format
Ensure an accurate BOM by following these guidelines:
-
Assign unique part numbers to each component in the schematic. Use the “Annotate” tool to quickly number the parts.
-
Fill out the “Value” and “Footprint” fields for every component in the schematic. This data carries over to the BOM.
-
Double-check the quantities and reference designators in the exported BOM file. Compare them against the schematic and PCB layout to verify accuracy.
-
Use a spreadsheet format like CSV or Excel for the BOM file. Most PCB assembly houses can import these formats into their systems.
-
Include any special assembly instructions or non-standard parts in the BOM. Communicate clearly with your assembler to avoid mistakes.
Frequently Asked Questions (FAQ)
Q1: How do I create a custom component in EasyEDA?
A1: To create a custom component, open the library manager, right-click, and select “New Component.” Enter the component details like name, description, and pins. Then assign a schematic symbol and PCB footprint. Save the component and place it on your schematic.
Q2: What is the best way to learn EasyEDA?
A2: The best way to learn EasyEDA is a combination of reading tutorials, watching videos, and hands-on practice. Start with the official EasyEDA documentation and work through the beginner guides. Supplement with YouTube tutorial videos. Then practice applying the skills to design your own simple circuits.
Q3: Why am I getting errors when running circuit simulation?
A3: Simulation errors can occur for several reasons. First, make sure your schematic passes ERC and the netlist is up-to-date. Then check that all components have SPICE models and the models are compatible. Finally, verify the simulation settings and analysis options are configured properly for your circuit.
Q4: How do I share my EasyEDA project with others?
A4: To share a project, open the “Project” menu and click “Share Project.” You can share by email, public URL link, or embed in a web page. Set the access permissions to control what others can do (view, comment, edit). Collaborators will receive an invite to open the shared project.
Q5: Where can I get more help with EasyEDA?
A5: If you need more help, consult the official EasyEDA documentation at docs.easyeda.com. You can also post questions in the EasyEDA user forum at easyeda.com/forum or on EDA-related StackExchange sites. For one-on-one assistance, consider hiring a freelance expert on platforms like Upwork.
Conclusion
EasyEDA is a user-friendly yet feature-rich tool for designing and manufacturing electronics. While it streamlines many aspects of the process, problems can still arise during schematic capture, simulation, PCB layout, and production.
This guide provided practical tips for troubleshooting common issues encountered in EasyEDA. Following this advice will help you overcome obstacles and successfully complete your projects. Remember, the key is methodically isolating the source of the problem through careful review and targeted corrections.
Don’t be afraid to experiment, consult documentation, and seek help from the EasyEDA community when needed. With practice and persistence, you’ll master the art of Troubleshooting EasyEDA. Happy designing!
Leave a Reply