What is PCB Etching?
PCB etching is the process of chemically removing unwanted copper from a printed circuit board (PCB) to create the desired electrical connections. It involves applying a resist layer to protect the copper traces that should remain, then submerging the PCB in an etchant solution to dissolve away the unprotected copper.
PCB etching is a key step in the PCB Fabrication process. It allows complex circuits to be produced on a copper-clad substrate in a precise and repeatable way. Etching is used for both prototype and production PCBs.
Types of PCB Etching
There are two main methods used for PCB etching:
-
Subtractive etching – The traditional method where a resist is applied over the full copper layer and then selectively removed to expose areas to be etched away. Also known as print-and-etch.
-
Additive etching – A newer method where the resist is selectively applied only where copper traces are needed. The exposed copper is then built up through electroplating. Requires a more complex process but reduces waste.
This guide will focus on the subtractive method as it is more commonly used, especially for prototyping and small-scale production.
Materials and Equipment Needed
Before getting started with PCB etching, you’ll need to gather the following materials and equipment:
Consumables
Item | Description |
---|---|
PCB blanks | Copper-clad boards, either single or double sided |
Resist | Etch-resistant ink or transfer film applied to PCB |
Etchant | Chemical solution (e.g. ferric chloride) to dissolve copper |
Acetone | For cleaning PCBs before and after etching |
Isopropyl alcohol | For cleaning PCBs and removing resist |
Tools & Equipment
Item | Description |
---|---|
Laser printer | For printing etch resist onto transfer film |
UV exposure unit | For transferring resist pattern and exposing photoresist |
Etching tank | Heated, bubbled tank for immersing PCBs in etchant |
Drill or punch | For making holes in PCBs for vias and component leads |
Protective equipment | Gloves, goggles, apron for handling chemicals safely |
Step-by-Step PCB Etching Process
Follow these steps to etch your own PCBs:
1. Design your PCB layout
The first step is to design your circuit schematic and lay out the PCB traces, pads, and vias using EDA (electronic design automation) software. Make sure to follow good PCB layout practices and design for manufacturability (DFM).
2. Print the etch resist
Once your design is ready, you need to transfer the etch resist pattern onto the PCB. The most common methods are:
-
Toner transfer – Print a mirrored version of the layout onto special transfer paper using a laser printer, then iron it onto the clean PCB surface to transfer the toner as etch resist.
-
Photoresist film – Apply a light-sensitive film to the PCB, then use a UV exposure unit to transfer the pattern and develop the resist.
-
Direct printing – Use a special inkjet printer to apply etch-resistant ink directly onto the PCB in the desired pattern.
3. Prepare the etchant solution
The most commonly used etchant is ferric chloride (FeCl3) solution. It’s an acidic solution that dissolves copper metal through an oxidation reaction.
To prepare the bath, carefully pour the ferric chloride crystals into warm water in the etching tank and stir until fully dissolved. The ideal concentration is around 40-45% FeCl3 by weight. Heat the solution to 50-55°C (120-130°F) for optimal etching speed.
Other etchants like ammonium persulfate and cupric chloride can also be used. Always check the MSDS and follow the manufacturer’s instructions for mixing and safety.
4. Etch the PCB
With the etchant ready and resist applied, it’s time to etch the PCB:
- Carefully lower the PCB into the etching tank with the copper side facing up. Use tongs or a basket to avoid direct contact with the solution.
- Agitate the solution by gently rocking the tank or using an aquarium bubbler to ensure even etching.
- Monitor the etching progress every few minutes. The exposed copper should gradually dissolve away, revealing the PCB substrate underneath.
- Once all the unwanted copper is removed, use the tongs to remove the PCB and immediately rinse it thoroughly with water to stop the etching reaction.
Etching typically takes 10-30 minutes depending on the solution temperature, agitation, and copper thickness. Don’t leave the PCB in the etchant longer than needed as it can start to undercut the resist and damage the traces.
5. Strip the etch resist
After etching, the etch resist needs to be removed to expose the remaining copper traces:
- For toner transfer, scrub the PCB with acetone to dissolve the toner. Steel wool can help remove stubborn spots.
- For photoresist, use a resist stripper solution per the manufacturer’s instructions, or scrub with acetone.
- Direct etch-resistant ink can usually be removed with isopropyl alcohol.
With the resist removed, inspect the PCB closely for any defects or discontinuities in the traces. Use a multimeter to verify the connections.
6. Clean and finish the PCB
To protect the exposed copper traces from oxidation and prepare the PCB for assembly:
- Clean the PCB thoroughly with isopropyl alcohol to remove any grease, dust or chemical residues.
- Drill any required holes for through-hole component leads and vias. Use a drill press or punch for best results.
- Apply a solder mask if desired to cover the bare copper. This can be done with a UV-curable liquid solder mask and exposure unit, or by applying a solder mask foil with a laminator.
- Apply a silkscreen legend to label components, values, logos etc. This is typically done by screen printing a UV-curable ink.
Your PCB is now ready for final assembly and soldering of components. Congratulations, you’ve made your own PCB!
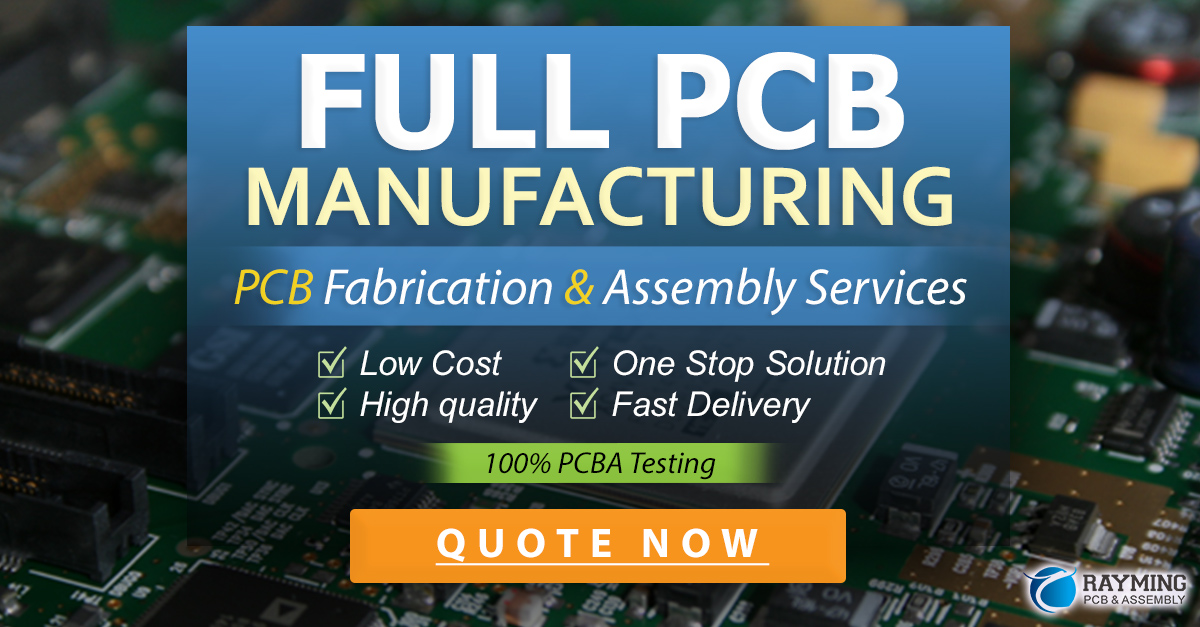
PCB Etching Tips & Tricks
Here are some tips to help you get the best results with PCB etching:
-
Use fresh etchant – Etchant solutions become exhausted over time and with use, slowing down etching. Regularly replace or replenish the solution for consistent results. The color change from brown to green indicates exhausted ferric chloride.
-
Control the temperature – Etchant activity increases with temperature, so keep it consistent for predictable etch times. Don’t exceed 55°C or it may attack the resist. Use an aquarium heater for stable heating.
-
Agitate the solution – Good circulation of the etchant over the PCB surface speeds up etching and promotes even copper removal. A bubbler or magnetic stirrer works well.
-
Don’t etch too long – Over-etching will cause undercutting of traces and loss of fine pitch features. Start checking 2/3 of the way through the expected etch time and pull the PCB out once the unwanted copper is gone.
-
Etch both sides separately – For double-sided PCBs, etch one side at a time. This avoids alignment issues and allows you to use different designs on each side if needed.
-
Clean and protect the PCB – Bare Copper PCBs will quickly oxidize so clean and coat them as soon as possible after etching. A hot air solder leveler (HASL) can be used to apply a thin layer of solder as a protective finish.
-
Dispose of chemicals properly – Etchant solutions are hazardous and should never be dumped down the drain. Check with your local waste disposal authority for guidelines on proper disposal or recycling of chemicals.
FAQ
What is the best etchant to use for PCBs?
Ferric chloride is the most common and readily available etchant. It provides good etch quality and is relatively safe compared to alternatives. Ammonium persulfate is also used and can provide faster etching. Cupric chloride is another option but is more hazardous.
How long does it take to etch a PCB?
Etch times vary based on the etchant type and concentration, temperature, agitation, and copper thickness. As a rough guide, a 1 oz copper board in fresh ferric chloride at 50°C will take around 10 minutes to etch. Always monitor the progress closely.
Can I reuse the etchant solution?
Yes, ferric chloride and other etchants can be reused multiple times until they become exhausted. The speed of etching will gradually slow down with each use. To extend the life, you can regenerate ferric chloride by bubbling air through it to re-oxidize the iron.
What is the best way to apply etch resist?
Toner transfer is a popular method as it uses a standard laser printer and cheap transfer paper. The main downside is the manual nature of ironing on the toner. Photoresist provides more precision and repeatability but requires a UV exposure unit. Direct inkjet printing of resist is fast and simple but requires a dedicated printer.
How do I dispose of used etchant safely?
Etchant solutions contain dissolved copper and are considered hazardous waste. They should never be dumped down the drain or into the environment. Contact your local waste authority for disposal instructions. Ferric chloride can be converted into solid ferric hydroxide sludge which is easier to dispose of by neutralizing it with a base like sodium hydroxide or sodium carbonate.
Conclusion
PCB etching is a critical step in the PCB fabrication process that requires attention to detail and proper safety precautions. By following the steps outlined in this guide and using the right materials and techniques, you can quickly learn to produce your own Prototype PCBs at home or in the lab. As with any skill, practice and experimentation will help you refine your process and achieve professional-looking results. Always prioritize safety and sustainability by using appropriate protective equipment and properly disposing of chemical waste. With these tips in mind, you’re ready to start etching your own PCBs!
Leave a Reply