What is Soldering?
Soldering is a process that involves melting a low-temperature metal alloy (solder) to join two or more metal surfaces together. The solder fills the gap between the metal surfaces, creating a strong electrical and mechanical bond. Soldering is widely used in electronics to join components to printed circuit boards (PCBs), wires to connectors, and more.
Tools and Materials Required for Soldering
Before you start soldering, you’ll need to gather the necessary tools and materials. Here’s a list of the essential items you’ll need:
Soldering Iron
A soldering iron is the most important tool for soldering. It consists of a heated metal tip that melts the solder and a handle that allows you to hold and manipulate the iron. Soldering Irons come in various wattages, with higher wattages suitable for larger components and lower wattages for smaller, more delicate work.
Solder
Solder is the metal alloy that is melted to join the metal surfaces together. It typically consists of a mixture of tin and lead, although lead-free solder is becoming increasingly common due to environmental and health concerns. Solder comes in various diameters and compositions, with thinner solder being easier to work with for smaller components.
Soldering Iron Stand
A soldering iron stand is a must-have accessory that helps to keep your soldering iron safe and secure when not in use. It typically consists of a heavy base with a spring-loaded holder that grips the soldering iron handle.
Sponge or Brass Wool
A damp sponge or brass wool is used to clean the tip of the soldering iron between uses. This helps to remove any oxidation or excess solder that may have accumulated on the tip, ensuring a clean and efficient heat transfer.
Flux
Flux is a chemical compound that helps to remove oxides from the metal surfaces being soldered, promoting better solder adhesion and preventing oxidation during the soldering process. Flux comes in various forms, including pastes, liquids, and pens.
Tweezers
Tweezers are useful for holding small components in place while soldering, as well as for manipulating wires and other delicate parts.
Wire Cutters
Wire cutters are used to trim excess wire leads after soldering, as well as for cutting wires to the appropriate length before soldering.
Safety Glasses
Safety glasses are important for protecting your eyes from any solder splashes or fumes that may be generated during the soldering process.
Preparing for Soldering
Before you start soldering, it’s important to prepare your workspace and materials properly. Here are some steps to follow:
- Clean the metal surfaces to be soldered with isopropyl alcohol to remove any dirt, grease, or oxidation.
- Tin the tip of the soldering iron by applying a small amount of solder to the tip and wiping it on the damp sponge or brass wool. This helps to improve heat transfer and prevents oxidation of the tip.
- Apply flux to the metal surfaces to be soldered, either with a brush or by dipping the component leads into the flux.
- Position the components to be soldered, using tweezers or other tools to hold them in place if necessary.
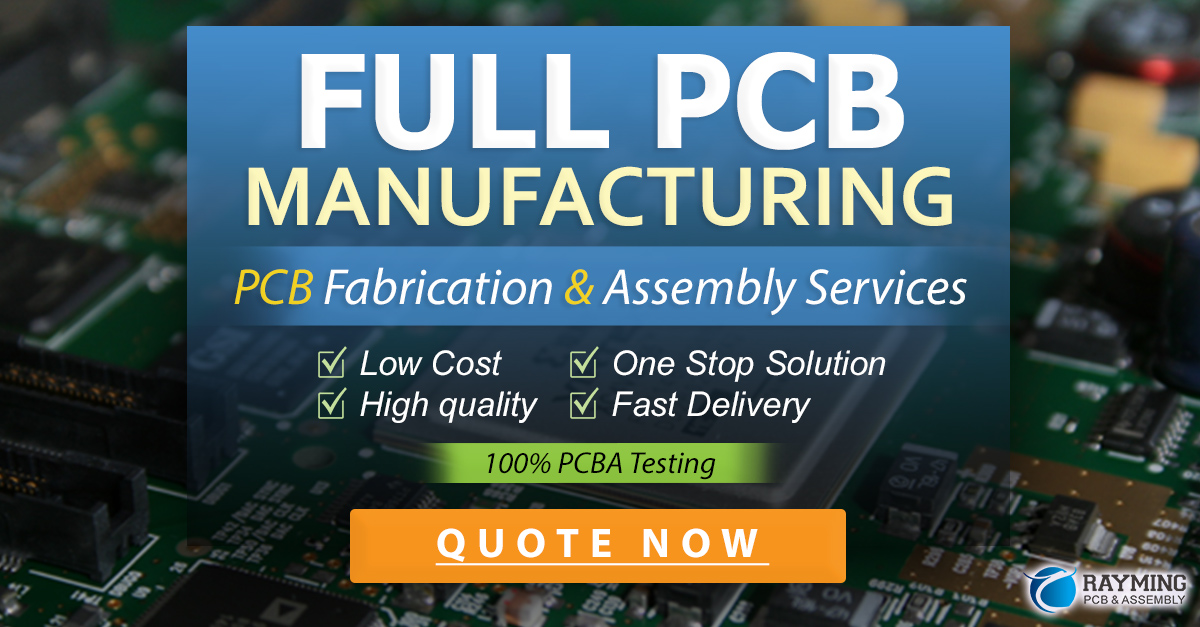
Basic Soldering Techniques
Now that you’ve prepared your workspace and materials, it’s time to start soldering. Here are the basic steps for making a solder joint:
- Heat the metal surfaces to be soldered by touching the soldering iron tip to them for a few seconds.
- Apply solder to the heated metal surfaces, allowing it to flow around the joint and fill any gaps.
- Remove the soldering iron and allow the solder to cool and solidify for a few seconds.
- Inspect the solder joint to ensure that it is smooth, shiny, and completely filled with solder.
Here are some tips for achieving strong, reliable solder joints:
- Use the appropriate amount of solder for the size of the components being joined. Too little solder may result in a weak joint, while too much solder can cause bridging between adjacent joints.
- Keep the soldering iron tip clean and tinned throughout the soldering process to ensure good heat transfer and prevent oxidation.
- Use the appropriate temperature for the type of solder and components being used. Too low a temperature may result in poor solder flow and adhesion, while too high a temperature can damage components or cause the solder to become brittle.
- Work quickly and efficiently to minimize the amount of time the components are exposed to heat, which can cause damage or degradation over time.
Advanced Soldering Techniques
Once you’ve mastered the basic soldering techniques, you may want to try some more advanced techniques for specific applications. Here are a few examples:
Surface Mount Soldering
Surface mount components are smaller and more delicate than through-hole components, and require a different soldering technique. To solder surface mount components, you’ll need a fine-tipped soldering iron and tweezers to hold the components in place. Apply a small amount of solder to one of the component pads on the PCB, then use the tweezers to position the component and hold it in place while touching the soldering iron tip to the other pad to reflow the solder.
Desoldering
Desoldering involves removing solder from a joint in order to remove a component or correct a mistake. To desolder a joint, you’ll need a desoldering pump or desoldering wick. Heat the joint with the soldering iron, then quickly remove the iron and use the desoldering tool to suck up the molten solder.
Rework and Repair
Rework and repair involves modifying or repairing existing solder joints or components. This may involve removing and replacing components, adding jumper wires to bypass damaged traces, or reflowing solder joints to improve their strength and reliability. Rework and repair requires a steady hand and a good understanding of the circuit being worked on.
Safety Considerations
Soldering involves working with hot tools and molten metal, so it’s important to take appropriate safety precautions to avoid injury or damage. Here are some safety tips to keep in mind:
- Always wear safety glasses to protect your eyes from solder splashes or fumes.
- Work in a well-ventilated area to avoid inhaling solder fumes, which can be harmful to your health.
- Use a soldering iron with a grounded tip to avoid electric shock.
- Never touch the hot soldering iron tip or molten solder with your bare hands.
- Keep flammable materials away from the soldering area to avoid fire hazards.
- Dispose of used solder and other waste materials properly to avoid environmental contamination.
Troubleshooting Common Soldering Problems
Even with the best techniques and materials, soldering problems can sometimes occur. Here are some common soldering problems and how to troubleshoot them:
Problem | Possible Causes | Solutions |
---|---|---|
Cold joint | Insufficient heat, dirty or oxidized surfaces, insufficient flux | Reheat the joint and apply more solder and flux if necessary |
Bridging | Too much solder, components too close together | Use a solder wick or desoldering pump to remove excess solder |
Insufficient wetting | Dirty or oxidized surfaces, insufficient flux, incorrect solder composition | Clean the surfaces thoroughly and apply more flux, use the correct solder composition for the application |
Lifted Pads | Excessive heat or mechanical stress | Use a lower soldering iron temperature and avoid applying too much pressure to the components |
Solder balls | Too much solder, incorrect soldering iron temperature | Use a solder wick or desoldering pump to remove excess solder, adjust the soldering iron temperature |
FAQ
- What is the difference between lead-based and lead-free solder?
-
Lead-based solder contains a mixture of tin and lead, while lead-free solder uses alternative metals such as silver, copper, or bismuth. Lead-free solder is becoming more common due to environmental and health concerns, but it typically requires higher Soldering Temperatures and may be more difficult to work with than lead-based solder.
-
Can I use a regular household iron for soldering?
-
No, a regular household iron is not suitable for soldering. Soldering requires a specialized tool that can reach and maintain the high temperatures needed to melt solder, typically between 600-800°F (315-425°C). Using a regular iron can result in poor solder joints and damage to the components being soldered.
-
How often should I replace my soldering iron tip?
-
Soldering iron tips should be replaced when they become worn, pitted, or oxidized, which can affect their heat transfer and soldering performance. The lifespan of a soldering iron tip depends on factors such as the quality of the tip, the frequency of use, and the type of solder and flux used. In general, a well-maintained soldering iron tip can last for several months to a year or more.
-
Can I solder without using flux?
-
While it is possible to solder without using flux, it is not recommended. Flux helps to remove oxides and other contaminants from the metal surfaces being soldered, promoting better solder flow and adhesion. Soldering without flux can result in poor solder joints, reduced reliability, and increased risk of damage to the components being soldered.
-
How can I practice soldering without risking damage to expensive components?
- One way to practice soldering without risking damage to expensive components is to use a soldering practice kit or board. These kits typically include a PCB with various components and pads for practicing different soldering techniques, as well as instructions and tips for improving your skills. You can also practice soldering on scrap PCBs or components, or by assembling simple electronic kits or projects.
Conclusion
Soldering is a valuable skill for anyone involved in electronics, from hobbyists to professionals. By understanding the tools, materials, and techniques involved in soldering, you can create strong, reliable solder joints that will last for years. Remember to always prioritize safety and take the necessary precautions to avoid injury or damage, and don’t be afraid to practice and experiment with different techniques to improve your skills over time. With patience, persistence, and attention to detail, anyone can become a skilled solderer and take their electronics projects to the next level.
Leave a Reply