Introduction to PCB Layout Design
Printed Circuit Board (PCB) layout design is a crucial step in the development of electronic devices. It involves arranging electronic components and routing traces on a board to create a functional circuit. A well-designed PCB layout ensures reliable performance, reduces manufacturing costs, and minimizes the risk of errors during assembly.
In this comprehensive guide, we will walk you through the essential steps and best practices for designing a PCB layout. Whether you are a beginner or an experienced designer, this article will provide you with valuable insights and techniques to optimize your PCB layouts.
Understanding the PCB Design Process
Before diving into the specifics of PCB layout design, let’s briefly overview the overall PCB design process. The typical steps involved are:
- Schematic Design: Create a schematic diagram that represents the electrical connections between components.
- Component Selection: Choose appropriate components based on the circuit requirements and specifications.
- PCB Layout Design: Arrange components and route traces on the board while considering factors such as signal integrity, power distribution, and manufacturing constraints.
- Design Rule Check (DRC): Verify that the PCB layout adheres to the manufacturing and design rules specified by the fabrication house.
- Gerber File Generation: Generate Gerber files, which are the industry-standard format for PCB Fabrication.
- Fabrication and Assembly: Send the Gerber files to a PCB fabrication house for manufacturing and assembly.
Key Considerations for PCB Layout Design
When designing a PCB layout, several key factors need to be considered to ensure optimal performance and manufacturability. Let’s explore these considerations in detail.
Component Placement
Proper component placement is essential for a well-designed PCB layout. Here are some guidelines to follow:
- Functionality: Group components based on their functional blocks to minimize the length of traces and improve signal integrity.
- Thermal Management: Place components that generate significant heat, such as power regulators and high-speed processors, away from temperature-sensitive components and provide adequate thermal relief.
- Mechanical Constraints: Consider the mechanical constraints of the enclosure or housing, such as mounting holes, connectors, and user interface elements.
- Signal Integrity: Place critical components, such as clock sources and high-speed interfaces, close to their associated components to minimize signal reflections and crosstalk.
Routing Techniques
Efficient routing is crucial for ensuring signal integrity and minimizing electromagnetic interference (EMI). Consider the following techniques:
- Trace Width and Spacing: Determine appropriate trace widths based on the current carrying capacity and impedance requirements. Maintain adequate spacing between traces to prevent crosstalk and short circuits.
- Ground Planes: Use solid ground planes to provide a low-impedance return path for signals and reduce EMI. Consider using multiple ground planes for different signal types (e.g., analog and digital grounds).
- Via Placement: Minimize the number of vias and place them strategically to reduce signal reflections and improve manufacturability. Use via stitching for high-speed signals to maintain signal integrity.
- Length Matching: Match the lengths of critical signal traces, such as differential pairs and clock lines, to ensure proper timing and reduce signal skew.
Power Distribution
Proper power distribution is essential for maintaining a stable and noise-free power supply to the components. Consider the following practices:
- Power Planes: Use dedicated power planes to distribute power evenly across the board. Use separate planes for different voltage levels to minimize crosstalk.
- Decoupling Capacitors: Place decoupling capacitors close to the power pins of components to minimize power supply noise and provide local energy storage.
- Voltage Regulators: Position voltage regulators close to the components they supply to minimize voltage drop and improve regulation.
Signal Integrity
Signal integrity is crucial for ensuring reliable communication between components and preventing signal distortion. Consider the following techniques:
- Impedance Control: Use controlled impedance traces for high-speed signals to minimize reflections and maintain signal quality. Calculate the required trace width and spacing based on the dielectric properties of the PCB material.
- Termination: Properly terminate high-speed signals using resistors or other termination techniques to minimize reflections and ringing.
- Crosstalk Reduction: Minimize crosstalk by increasing the spacing between adjacent traces, using guard traces, or employing differential signaling.
- EMI Reduction: Implement EMI reduction techniques such as proper grounding, shielding, and filtering to minimize electromagnetic interference.
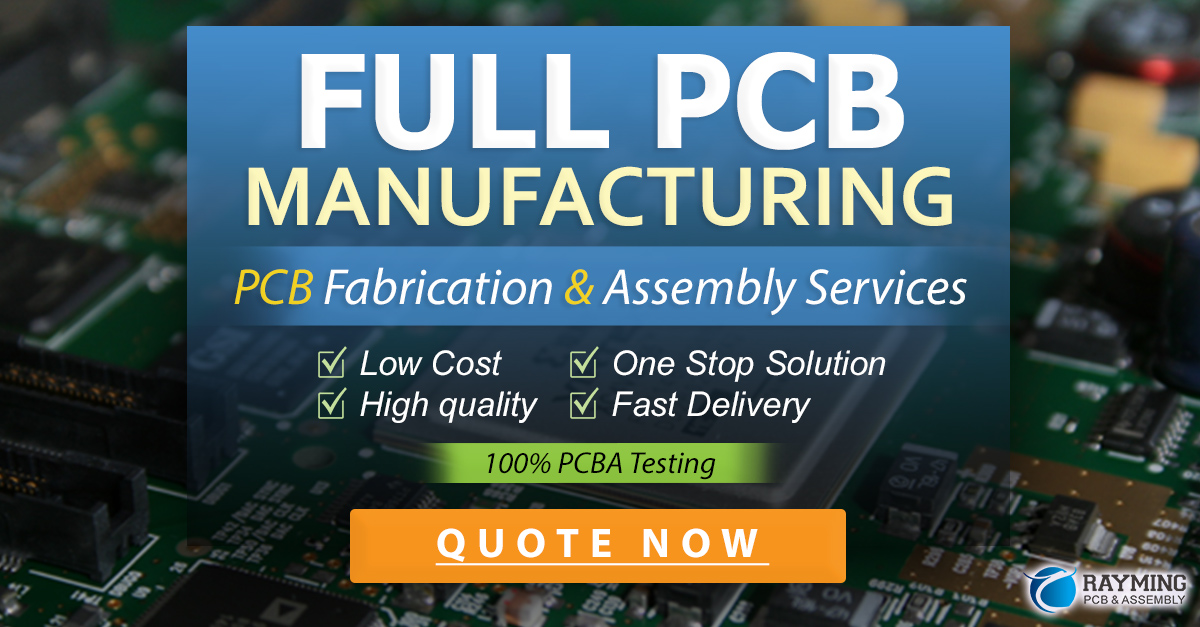
PCB Layer Stackup
The PCB layer stackup refers to the arrangement of copper layers and dielectric materials in a PCB. Proper layer stackup design is essential for signal integrity, power distribution, and manufacturability. Consider the following guidelines:
- Number of Layers: Determine the required number of layers based on the complexity of the circuit, signal routing requirements, and cost constraints.
- Signal Layers: Designate specific layers for signal routing, typically on the outer layers for easy access and inner layers for dense routing.
- Power and Ground Planes: Dedicate layers for power and ground planes to provide low-impedance paths for power distribution and minimize noise.
- Dielectric Material: Choose appropriate dielectric materials based on the desired electrical properties, such as dielectric constant and loss tangent.
Design Rule Check (DRC)
Before finalizing the PCB layout, it is crucial to perform a Design Rule Check (DRC) to ensure that the layout adheres to the manufacturing and design rules specified by the fabrication house. The DRC process verifies the following aspects:
- Trace Width and Spacing: Check if the trace widths and spacing meet the minimum requirements specified by the fabrication house.
- Clearance: Verify that the clearance between components, traces, and other features is sufficient to prevent short circuits and manufacturing issues.
- Hole Size and Spacing: Ensure that the hole sizes and spacing for vias and mounting holes meet the fabrication requirements.
- Solder Mask and Silkscreen: Check the solder mask and silkscreen layers for proper coverage and legibility.
Generating Gerber Files
Once the PCB layout is finalized and has passed the DRC, the next step is to generate Gerber files. Gerber files are the industry-standard format used by PCB fabrication houses to manufacture the board. The Gerber files include information such as:
- Copper Layers: The copper patterns for each layer of the PCB.
- Solder Mask: The solder mask layer that protects the copper traces and prevents short circuits.
- Silkscreen: The silkscreen layer that contains component designators, labels, and other text.
- Drill Files: The files that specify the locations and sizes of holes for vias and mounting.
It is essential to carefully review the generated Gerber files to ensure accuracy and completeness before sending them to the fabrication house.
Best Practices for PCB Layout Design
To optimize your PCB layout design, consider the following best practices:
- Use a Grid System: Align components and traces to a grid system to maintain consistency and ease of routing.
- Keep Traces Short: Minimize the length of traces to reduce signal reflections, crosstalk, and power losses.
- Avoid 90-Degree Angles: Use 45-degree angles or curved traces instead of 90-degree angles to minimize signal reflections and improve manufacturability.
- Provide Adequate Clearance: Maintain sufficient clearance between components, traces, and other features to prevent short circuits and facilitate assembly.
- Use Copper Pours: Fill unused areas of the PCB with copper pours connected to ground to improve shielding and reduce EMI.
- Document Your Design: Provide clear and comprehensive documentation, including schematics, bill of materials (BOM), and assembly instructions, to facilitate manufacturing and troubleshooting.
Frequently Asked Questions (FAQ)
1. What software is commonly used for PCB layout design?
Some popular PCB layout design software include:
– Altium Designer
– KiCad
– Eagle
– OrCAD
– Mentor Graphics PADS
2. How do I choose the appropriate trace width for my PCB layout?
The appropriate trace width depends on factors such as the current carrying capacity, voltage drop, and impedance requirements. You can use online trace width calculators or consult the IPC-2221 standard for guidelines on trace width selection.
3. What is the purpose of a ground plane in a PCB layout?
A ground plane serves as a low-impedance return path for signals, helps reduce electromagnetic interference (EMI), and provides shielding. It also helps distribute heat evenly across the board.
4. How can I minimize crosstalk in my PCB layout?
To minimize crosstalk, you can:
– Increase the spacing between adjacent traces
– Use guard traces or ground planes between sensitive signals
– Employ differential signaling for high-speed signals
– Route sensitive signals on different layers
5. What are the common pitfalls to avoid in PCB layout design?
Some common pitfalls to avoid in PCB layout design include:
– Inadequate component placement and spacing
– Incorrect trace width and spacing
– Lack of proper grounding and power distribution
– Neglecting signal integrity and EMI considerations
– Failing to perform a thorough Design Rule Check (DRC)
Conclusion
Designing a PCB layout requires careful consideration of various factors, including component placement, routing techniques, power distribution, signal integrity, and manufacturability. By following the guidelines and best practices outlined in this article, you can create reliable and efficient PCB layouts that meet your design requirements.
Remember to thoroughly review your design, perform a Design Rule Check (DRC), and generate accurate Gerber files before sending your board for fabrication. Continuously learn from your experiences and stay updated with the latest industry standards and techniques to improve your PCB layout design skills.
With practice and attention to detail, you can master the art of PCB layout design and bring your electronic projects to life with confidence.
Leave a Reply