Introduction to PCB Cutting
Printed Circuit Boards (PCBs) are essential components in modern electronics. They provide a platform for mounting and connecting various electronic components to create functional circuits. PCB cutting is a crucial process in the manufacturing and prototyping of PCBs, allowing for the creation of custom shapes and sizes to fit specific project requirements. In this comprehensive guide, we will explore the different methods and techniques for cutting PCBs, helping you achieve precise and professional results.
Why Cutting PCBs is Important
PCB cutting serves several important purposes in the electronics industry:
-
Customization: Cutting PCBs allows for the creation of custom shapes and sizes to fit specific project enclosures or space constraints.
-
Prototyping: During the prototyping phase, PCB cutting enables quick iterations and modifications to test and refine circuit designs.
-
Manufacturing: In mass production, PCB cutting is necessary to separate individual boards from larger panels, ensuring consistent and accurate dimensions.
-
Repair and Modification: Cutting techniques can be used to remove damaged sections of a PCB or to modify existing boards for repairs or upgrades.
Safety Precautions for PCB Cutting
Before diving into the various PCB cutting methods, it’s essential to prioritize safety. PCB cutting involves the use of sharp tools and may generate dust particles, so take the following precautions:
- Wear protective eyewear to shield your eyes from debris and dust.
- Use a dust mask or respirator to avoid inhaling PCB dust particles.
- Wear gloves to protect your hands from sharp edges and cuts.
- Work in a well-ventilated area to minimize exposure to fumes or dust.
- Clean up any debris or dust generated during the cutting process to maintain a safe work environment.
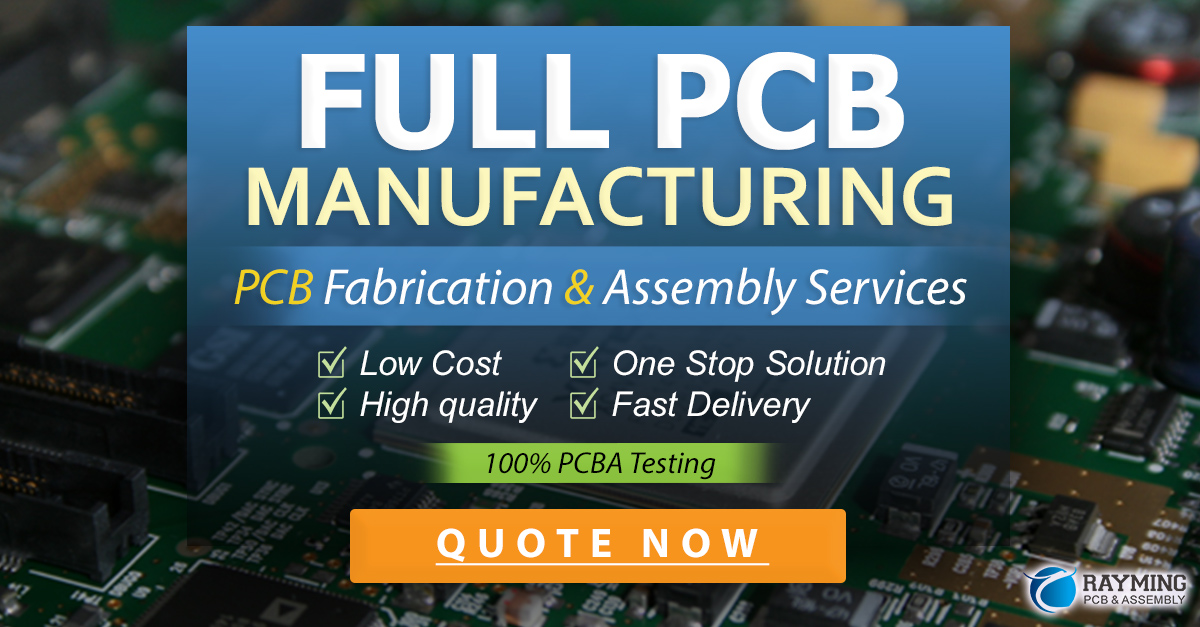
PCB Cutting Methods
There are several methods for cutting PCBs, each with its own advantages and limitations. Let’s explore the most common techniques:
1. Manual Cutting
Manual cutting is a simple and accessible method for cutting PCBs, suitable for small-scale projects or quick prototyping. It involves using hand tools like scissors, utility knives, or manual PCB shears.
Tools for Manual PCB Cutting
-
Scissors: Regular scissors can be used for cutting thin, single-sided PCBs. However, they may not provide the cleanest or most precise cuts.
-
Utility Knife: A sharp utility knife can be used to score and snap PCBs along a straight line. This method works best for thin, single-sided boards.
-
Manual PCB Shears: Manual PCB shears are specialized tools designed for cutting PCBs. They provide cleaner and more precise cuts compared to scissors or utility knives.
Techniques for Manual PCB Cutting
- Scoring and Snapping:
- Use a straightedge or ruler to guide your cutting tool along the desired line.
- Apply firm pressure to score the PCB surface, creating a deep groove.
-
Snap the PCB along the scored line by applying pressure on both sides.
-
Shearing with Manual PCB Shears:
- Align the PCB with the cutting edge of the manual shears.
- Apply steady pressure to cut through the PCB material.
- Repeat the process for any remaining cuts.
Manual cutting is suitable for simple, straight cuts on thin PCBs. However, it may not provide the precision and clean edges required for more complex designs or thicker boards.
2. Rotary Tool Cutting
Rotary tools, such as Dremel or similar brands, offer a versatile and efficient method for cutting PCBs. These tools use high-speed rotating bits to cut through the PCB material.
Tools for Rotary Tool PCB Cutting
-
Rotary Tool: A rotary tool with adjustable speed settings is essential for PCB cutting. Popular brands include Dremel, Proxxon, and Wen.
-
Cutting Bits: Various cutting bits can be used with rotary tools, such as fiberglass-reinforced cut-off wheels, diamond-coated cutting discs, or carbide-tipped bits. Choose a bit suitable for cutting PCB material.
-
Safety Equipment: Wear protective eyewear, a dust mask, and gloves when using a rotary tool to ensure safety.
Techniques for Rotary Tool PCB Cutting
- Straight Cuts:
- Secure the PCB firmly using clamps or a vise.
- Mark the desired cutting line on the PCB.
- Attach the appropriate cutting bit to the rotary tool.
- Align the cutting bit with the marked line and slowly guide it along the PCB, applying steady pressure.
-
Keep the rotary tool perpendicular to the PCB surface to ensure a clean, straight cut.
-
Curved or Complex Cuts:
- For curved or intricate cuts, use a thin cutting bit with a small diameter.
- Carefully guide the rotary tool along the desired path, maintaining a steady hand and speed.
- Use a template or stencil to assist with complex shapes or patterns.
Rotary tool cutting provides more precision and versatility compared to manual methods. It allows for both straight and curved cuts, making it suitable for a wider range of PCB designs.
3. CNC PCB Cutting
Computer Numerical Control (CNC) machines offer the highest level of precision and automation for PCB cutting. CNC routers or mills use computer-controlled cutting tools to achieve accurate and repeatable cuts.
Advantages of CNC PCB Cutting
-
Precision: CNC machines provide exceptional precision, ensuring consistent and accurate cuts.
-
Automation: CNC cutting eliminates the need for manual handling, reducing human error and increasing production efficiency.
-
Versatility: CNC machines can handle a wide range of PCB materials and thicknesses, making them suitable for various projects.
CNC PCB Cutting Process
- Design Preparation:
- Create a digital design file (e.g., Gerber or DXF) of the desired PCB shape and dimensions.
- Import the design file into the CNC machine’s software.
-
Set up the cutting parameters, such as tool paths, cutting depths, and feed rates.
-
Machine Setup:
- Load the PCB material onto the CNC machine’s work area.
- Secure the PCB using appropriate fixturing or adhesive methods.
-
Install the suitable cutting tool (e.g., end mill or router bit) into the CNC machine’s spindle.
-
Cutting Process:
- Start the CNC machine and initiate the cutting process.
- The machine will automatically follow the programmed tool paths, cutting the PCB according to the design file.
-
Monitor the cutting process to ensure proper operation and make any necessary adjustments.
-
Post-Processing:
- Once the cutting is complete, remove the PCB from the CNC machine.
- Clean the PCB to remove any debris or dust generated during the cutting process.
- Inspect the PCB for any defects or irregularities and make any necessary corrections.
CNC PCB cutting offers the highest level of precision and repeatability, making it ideal for high-volume production or projects requiring intricate designs and tight tolerances.
Selecting the Right PCB Cutting Method
Choosing the appropriate PCB cutting method depends on several factors, including:
-
Project requirements: Consider the complexity of the PCB design, desired shape, and dimensions.
-
PCB material and thickness: Different cutting methods may be more suitable for specific PCB materials and thicknesses.
-
Production volume: Manual methods are suitable for small-scale projects, while CNC cutting is more efficient for high-volume production.
-
Available tools and resources: Consider the tools and equipment you have access to, as well as your budget and skill level.
PCB Cutting Method | Advantages | Limitations |
---|---|---|
Manual Cutting | – Low cost – Accessible tools – Suitable for simple, straight cuts |
– Limited precision – Not suitable for complex shapes or thick PCBs |
Rotary Tool Cutting | – Versatile (straight and curved cuts) – Moderate precision – Relatively affordable |
– Requires skill and steady hands – May not be as precise as CNC cutting |
CNC PCB Cutting | – High precision and repeatability – Automated process – Suitable for complex designs and high volumes |
– Higher cost – Requires specialized equipment and software |
Tips for Successful PCB Cutting
To achieve the best results when cutting PCBs, consider the following tips:
-
Plan and measure carefully: Take accurate measurements and double-check your cutting lines before proceeding.
-
Use the appropriate tools: Select the right cutting tools based on your chosen method and the specific requirements of your project.
-
Secure the PCB: Ensure the PCB is firmly secured to prevent shifting or vibration during the cutting process.
-
Take your time: Rush cuts can lead to inaccuracies or damage to the PCB. Work at a steady pace and prioritize precision over speed.
-
Clean up debris: Remove any dust or debris generated during the cutting process to maintain a clean work environment and prevent contamination of the PCB.
-
Practice and refine your technique: PCB cutting skills improve with practice. Start with simpler projects and gradually work your way up to more complex designs.
Frequently Asked Questions (FAQ)
-
Q: Can I use a regular saw to cut PCBs?
A: While it is possible to use a regular saw, such as a hacksaw or coping saw, it is not recommended. Regular saws may cause excessive vibration and chipping, resulting in rough edges and potential damage to the PCB. It’s better to use specialized tools designed for PCB cutting. -
Q: How do I ensure straight cuts when cutting PCBs manually?
A: To ensure straight cuts, use a straightedge or ruler as a guide. Score the PCB along the desired line using a sharp cutting tool, applying firm and consistent pressure. Then, snap the PCB along the scored line by supporting it on both sides and applying pressure. -
Q: What safety precautions should I take when cutting PCBs?
A: Always wear protective eyewear to shield your eyes from debris and dust. Use a dust mask or respirator to avoid inhaling PCB dust particles. Wear gloves to protect your hands from sharp edges and cuts. Work in a well-ventilated area and clean up any debris or dust generated during the cutting process. -
Q: Can I cut Multilayer PCBs using the same methods as single-layer PCBs?
A: Yes, you can cut multilayer PCBs using the same methods as single-layer PCBs. However, multilayer PCBs are typically thicker and may require more powerful tools or longer cutting times. Be cautious not to delaminate or damage the internal layers during the cutting process. -
Q: How do I remove the rough edges after cutting a PCB?
A: To remove rough edges, you can use a fine-grit sandpaper or a PCB edge beveling tool. Gently sand or file the edges until they are smooth and even. Be careful not to apply too much pressure, as it may damage the PCB traces or components near the edges.
Conclusion
PCB cutting is a vital skill in the world of electronics, enabling the creation of custom shapes and sizes for various projects. Whether you choose manual cutting, rotary tool cutting, or CNC PCB cutting, understanding the techniques and best practices is essential for achieving precise and professional results.
Remember to prioritize safety, select the appropriate tools and methods based on your project requirements, and take your time to ensure accurate cuts. With practice and attention to detail, you’ll be able to confidently cut PCBs for your electronics projects.
As you explore the fascinating world of PCB design and fabrication, mastering the art of PCB cutting will open up new possibilities and empower you to bring your creative ideas to life. Happy cutting!
Leave a Reply