What is UV Soldermask and Why Use It?
UV soldermask is a photoimageable coating that is applied to the copper traces on a printed circuit board (PCB) to protect them from corrosion, prevent solder bridges from forming during assembly, and provide electrical insulation between conductors. Unlike traditional liquid soldermask which requires screen printing, UV soldermask can be applied and patterned using photolithography for more precision. This makes it ideal for fine-pitch surface mount designs.
There are several benefits to using UV soldermask on your PCBs:
- Protection from oxidation and corrosion
- Prevents solder bridging
- Insulates between adjacent traces
- Seals the board against moisture and contaminants
- Provides a professional, finished appearance
- Allows for finer pitch designs compared to liquid mask
While professionally manufactured boards will always have soldermask applied, you can also coat your own prototype or hobby PCBs at home using off-the-shelf UV soldermask products. Applying your own soldermask allows you to quickly make professional-looking boards without having to send them out for fabrication.
Required Tools and Materials
To apply UV soldermask at home, you will need the following tools and materials:
Item | Description |
---|---|
UV Soldermask | Photoimageable soldermask, available in several colors (green, blue, red, black, white, yellow). Shipped in lightproof bottles. |
Photomask | Transparencies or photomask film printed with the inverse soldermask pattern (clear where you want mask removed). |
UV Exposure Unit | Exposes the applied soldermask. Can use the sun, UV nail curing lamp, or purpose-built UV exposure box. |
Developing Tank | Plastic or glass tray for immersing board in developer solution. |
Developer Solution | Sodium carbonate (washing soda) dissolved in water. Typically 1-2% solution. |
Rinse Tank | Tray or sink for rinsing developed boards. |
Squeegee or Foam Brush | For spreading soldermask evenly on the board surface. |
Isopropyl Alcohol and Lint-Free Wipes | For cleaning the board prior to applying soldermask. |
Disposable Gloves | Protects hands from uncured soldermask and developer solution. |
Well-Ventilated Work Area | UV soldermask gives off fumes before curing. Work in a garage, outside, or by an open window. |
Step 1: Prepare the Board
The first step is to thoroughly clean the copper board to remove any grease, oils, fingerprints, or oxidation that could prevent the soldermask from adhering properly.
-
Put on disposable gloves to avoid getting oils from your skin on the board.
-
Wet a lint-free wipe generously with isopropyl alcohol (IPA). Avoid using paper towels or rags that could leave fibers behind.
-
Thoroughly wipe down both sides of the board, making sure to clean the entire surface. Pay special attention to the corners and edges.
-
Allow the board to air dry completely before proceeding. Handle only by the edges to avoid re-contaminating the surface.
For best results, cleaning should be done immediately before applying the soldermask. If the board sits out too long it can begin to oxidize again.
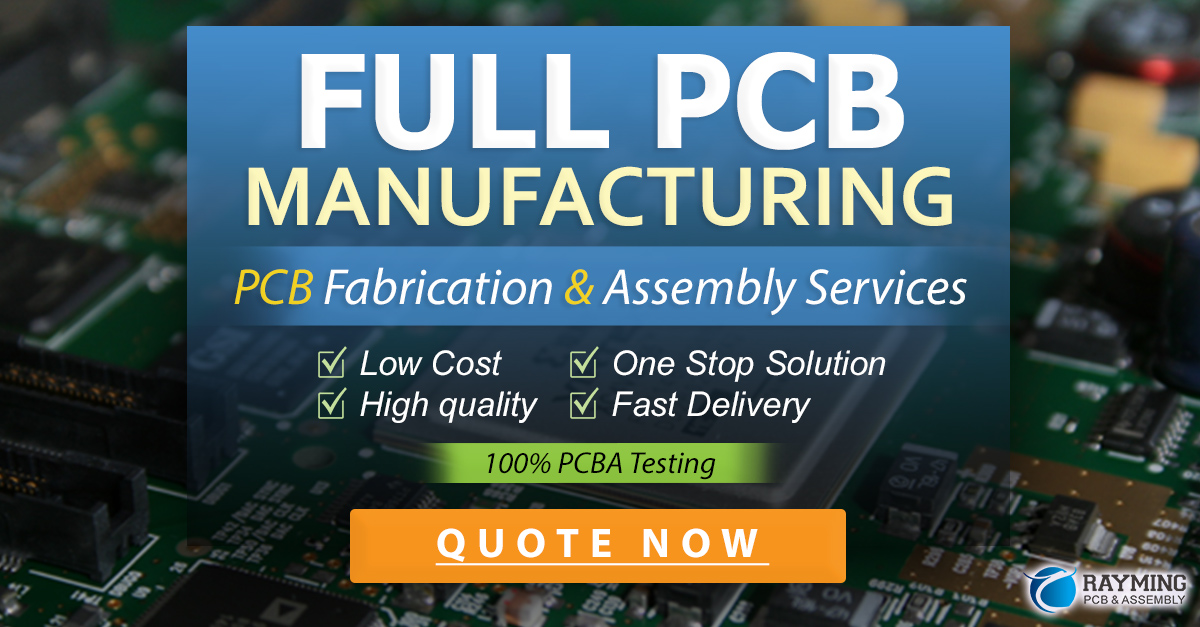
Step 2: Apply UV Soldermask
With the board cleaned and dried, you’re ready to apply an even coat of UV soldermask to the copper surfaces.
-
Place the clean board on a flat, level, disposable surface. A sheet of cardboard works well.
-
Gently shake or stir the bottle of UV soldermask to ensure it is fully mixed. Open carefully as contents are under pressure.
-
Pour a quarter-sized dollop of soldermask onto the center of the board.
-
Using a squeegee or foam brush, spread the soldermask evenly across the entire surface of the board, including into any holes or vias. The layer should be 1-2 mils thick.
-
Check the board surface carefully for any missed spots or thin areas and touch up as needed. The copper should be completely covered on both sides.
-
Allow the board to sit undisturbed for 5-10 minutes so the soldermask can self-level and air bubbles can dissipate.
-
While the soldermask is self-leveling, clean up any drips or spills with IPA before they can dry. UV soldermask is extremely difficult to remove once cured.
Tips for applying soldermask:
- Work in a dust-free environment to avoid particles getting stuck in the wet soldermask. A clean room is ideal but not necessary for hobby work.
- If the soldermask is too thick or viscous to spread easily, it can be thinned slightly by stirring in a few drops of IPA.
- For double-sided boards, apply soldermask to the top side first, allow to dry, then carefully flip over and coat the bottom.
Step 3: UV Exposure
Once the soldermask has leveled and dried enough that it is no longer tacky to the touch (about 30 minutes), it is ready to be selectively exposed to UV light in order to cure the coating everywhere except the desired pad openings.
-
In a dimly lit room, place the photomask on top of the board, carefully aligning it to the pads. The printed black areas should cover any pads that you want the soldermask removed from.
-
If using a UV exposure unit, place the board inside and expose according to the manufacturer’s instructions, typically 2-5 minutes.
-
If using sunlight, take the board outside and place it in direct sun for 10-15 minutes per side. Avoid exposing the board to sunlight for too long as it can overheat and damage the mask.
-
After exposure, a faint outline of the pads should be visible in the soldermask. If not, repeat the exposure for half the initial time and check again.
-
Gently peel off the photomask and discard. The unexposed areas will remain soft and sticky while the exposed soldermask will be dry to the touch.
UV Exposure Tips:
- For best results, use a photomask printed on transparency film with a laser printer or photocopier. Inkjet-printed masks may not be fully opaque.
- Make sure there is direct contact between the photomask and soldermask. Any gaps will allow light leaks and improperly exposed areas.
- The required exposure time will vary based on the strength of the UV light source and the thickness of the soldermask. Start with a shorter time and gradually increase as needed.
- Avoid over-exposing the board as this can make the soldermask brittle and difficult to remove from the pads.
Step 4: Developing
The final step is to develop away the unexposed areas of soldermask, revealing the bare copper pads underneath. This is done by immersing the board in a mildly caustic developer solution.
-
Prepare a 1-2% sodium carbonate solution in the developing tray by dissolving 1-2 tsp washing soda per 4 cups (1 liter) of lukewarm water.
-
Wearing gloves, carefully place the exposed board in the developer bath and gently agitate for 1-2 minutes or until all the unexposed soldermask has dissolved away.
-
Remove the board and rinse thoroughly under running water for 1 minute to remove all traces of developer.
-
Use a soft bristle brush to lightly scrub the pads, ensuring any residual soldermask is removed. Rinse again.
-
Allow the board to air dry completely before handling.
-
Inspect the board closely under bright light to verify all pads are cleanly developed and free of any soldermask residue. Repeat developing if needed.
-
For added durability, the board can be baked in a 250F (120C) oven for 30 minutes to fully crosslink the soldermask polymer. This is optional but will result in a harder, more scratch-resistant coating.
Developing Tips:
- Minimize the time the board spends in the developer. Over-developing can cause the masked areas to swell and lift around the edges.
- Use a fresh developer solution for each board. The sodium carbonate gets “used up” over time and becomes less effective.
- If the pads are not fully developed after 2 minutes, the board was likely under-exposed. Try exposing for a longer time on the next attempt.
- Very thin traces may be damaged by overly aggressive rinsing or brushing during developing. Go gently and use a soft brush.
Troubleshooting Common Issues
Problem | Possible Causes | Solutions |
---|---|---|
Soldermask not sticking to board | – Copper not thoroughly cleaned – Oils/contaminants on board surface – Humidity too high during application |
– Clean board with fresh IPA and lint-free wipe – Allow board to fully dry before applying – Apply in a humidity-controlled environment |
Pads not developing cleanly | – Underexposed – Photomask not making good contact – Developer too weak or cold – Insufficient developing time |
– Increase UV exposure time in 30s increments – Ensure photomask is pressed tightly to board – Make fresh batch of 1-2% developer solution – Develop for a full 2 minutes, agitating gently |
Mask pulling away from trace edges | – Over-developing – Aggressive rinsing after developing – Applying soldermask too thick |
– Limit developing time to 2 minutes max – Reduce water pressure when rinsing board – Apply in a thinner 1-2 mil layer and expose longer |
Soldermask tacky after curing | – Under-cured – Humidity too high during curing |
– Expose board for 50% longer – Bake board after developing to fully cure |
FAQ
What is the shelf life of UV soldermask?
Unopened, UV soldermask has a shelf life of 6-12 months when stored in a cool, dark place. Once opened, it should be used within 30 days for best results as it will slowly cure under ambient light. Always keep the bottle tightly capped when not in use.
Can I use regular solder with a UV soldermask coated board?
Yes, UV soldermask is fully compatible with both leaded and lead-free solder. The mask will withstand brief contact with a soldering iron without damage, although care should be taken not to apply heat for longer than necessary to avoid discoloring or burning the coating.
Are there any health risks to working with UV soldermask?
The main hazard is the uncured soldermask, which can cause skin and eye irritation. Always wear gloves and avoid getting uncured material on your skin. Work in a well-ventilated area as the mask gives off fumes before hardening. Once fully cured, soldermask is generally inert and non-toxic.
What is the resolution limit of UV soldermask?
For applying at home, the practical limit is around 4 mil (0.1mm) traces and spaces, although professionally applied UV soldermask can achieve 2 mil or smaller geometries. If your design has very fine pitched SMD pads, applying soldermask may be tricky and will require a extremely precise alignment of the photomask to the pads.
Can I mix my own UV soldermask color?
Yes, you can blend standard colors together to create custom shades, just keep in mind that the pigments may affect the curing time compared to off-the-shelf mixtures. You’ll likely need to experiment with exposure times anytime you change the soldermask formulation. Also, be sure to mix colors from the same manufacturer to ensure compatibility.
Leave a Reply