Understanding solder pads in Eagle
Solder pads in Eagle are copper areas on the PCB where components are soldered in place. They provide both electrical connection and mechanical stability for the components. Pads come in various sizes and shapes depending on the component package type (through-hole, surface-mount, etc.).
Eagle represents pads as a separate library object that can be placed on the board and connected with traces/copper polygons. The pad object specifies the pad’s size, shape, drill hole (if applicable), and properties.
Pad Shapes and Sizes
Eagle supports several standard pad shapes including:
Shape | Description |
---|---|
Square | A square-shaped pad commonly used for through-hole components |
Round | A circular pad used for both through-hole and SMD parts |
Octagon | An octagonal pad sometimes used for through-hole to allow better soldering |
Long | An elongated rectangular pad used for connectors, switches, etc. |
Offset | A round pad with the drill hole offset from center |
Pad sizes are specified by their X and Y dimensions in millimeters or inches. For plated through-holes, you also specify the drill hole size. SMD pads have no drill size.
Common pad sizes for standard through-hole components are:
Component | Pad Diameter | Drill Diameter |
---|---|---|
Resistor | 0.07″ | 0.032″ |
Capacitor | 0.07″ | 0.032″ |
DIP IC | 0.07″ | 0.032″ |
Header Pin | 0.07″ | 0.04″ |
For SMD, pad sizes match the component package – e.g. 0603, 0805, 1206, SOIC, QFP, etc.
Pad Properties
In addition to size/shape, pads have several key properties:
- Name – A unique identifier for the pad, e.g. “1”, “A5”, “GND”
- Pad Type – Thru-hole, top layer SMD, bottom layer SMD, etc.
- Layer – The layer the pad copper resides on (1-16). Thru-hole pads span all layers.
- Net – The electrical net the pad is part of
- Stop Mask – Determines solder mask opening over copper
- Cream Mask – Determines solder paste stencil opening for SMD
Setting appropriate properties is important for correct fabrication of your board.
Creating a New Solder Pad
To create a new solder pad from scratch in Eagle:
- Open the Eagle Board Editor
- Click the Pad tool icon or type
pad
in the command line - In the Pad dialog, specify:
- Pad shape (square, round, long, offset)
- Pad dimensions (diameter or X/Y size)
- Drill diameter (for thru-hole pads)
- Stop/cream mask settings
- Click OK to create the pad object
- Click to place the pad on the board
The new pad will appear on the board at your selected location. You can move it by clicking and dragging.
To edit an existing pad, right-click it and choose Properties. This reopens the Pad dialog to make changes.
Placing Solder Pads from a Library
Rather than creating pads from scratch, you’ll often place them from the component’s package library definition. To do this:
- Click the Add tool or type
add
- Browse to the library and package you want, e.g. “rcl” for resistors and capacitors
- Select the desired package and click OK
- Move cursor to location and click to place package
The package will be placed on the board with pads in the component’s predefined layout. You can modify individual pads as needed by editing their properties.
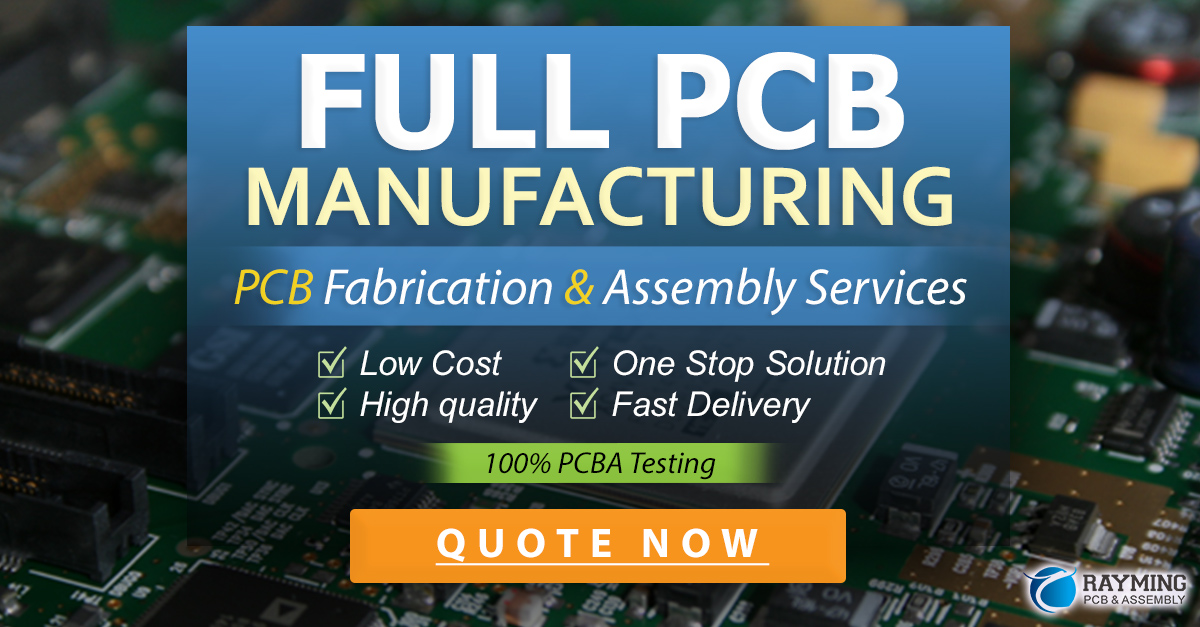
Connecting Pads with Traces and Polygons
Once pads are placed for components, you need to connect them with copper traces or polygons to form the nets of your circuit.
To route a trace between pads:
- Click the Route tool or type
route
- Left-click on the first pad to start the trace
- Move cursor to second pad, using click-and-drag to define trace path
- Click on second pad to finish the trace
Alternatively, you can use the Autorouter to automatically route traces between pads based on your netlist.
To connect a pad with a copper fill polygon:
- Draw the polygon shape using the Polygon tool
- Name the polygon with the net name
- Set the polygon properties (layer, isolate, etc.)
- Click Ratsnest to fill interior of polygon with copper
Pads inside the polygon area will be connected to that net.
Guidelines for Solder Pad Design
When laying out solder pads on your PCB, there are some best practices to follow:
Pad Size and Spacing
- Use pad sizes appropriate for the component package
- Provide enough space between adjacent pads to prevent solder bridges
- Follow manufacturer datasheets for recommended footprints
Solder Mask and Paste Mask
- Generally use a solder mask opening 0.05mm larger than pad on all sides
- For SMD, size paste mask to 80-90% of pad area to prevent bridging
- Provide at least 0.15mm webbing between mask openings
Thermal Relief and Spokes
- Use thermal relief connections on pads connected to large copper fills
- Thermal spokes help conduct heat away during soldering
- Typical spoke width is 0.25-0.4mm with 0.8-1.0mm air gap
Solderable Metals
- Ensure pad surface is a solderable finish (HASL, ENIG, OSP, etc.)
- Avoid using non-solderable metals like aluminum or titanium
- Check fab house capabilities for finished metal options and color
Testpoints and Fiducials
- Include test point pads for critical signals to aid debugging
- Place fiducial pads on fabrication and assembly layers for machine vision alignment
- Typical fiducial is 1mm copper circle with 2mm solder mask opening
By sizing pads correctly, ensuring proper mask openings, and following good layout practices, you’ll get better results when soldering components on your PCB.
FAQ
What’s the difference between a pad and a via?
Pads are the surface copper areas where components are soldered. Vias are copper-plated holes that connect signals between board layers, but do not have components soldered to them. Pads often have larger diameters than vias.
Can I use different pad shapes for the same component?
Yes, you can use different pad shapes for a single component, such as square pads on one side and round on the other. However, it’s generally best to be consistent with pad shapes for manufacturability and symmetry.
What is the minimum pad-to-pad spacing?
The minimum spacing depends on your PCB fab house capabilities. Typical minimums are 0.006″ (0.15mm) for basic designs, or 0.003″ (0.075mm) for advanced processes. Consult with your fab house for their specific specs. Tighter spacing requires better process control.
How do I change the solder mask color on my pads?
The mask color is determined when your board is fabricated, based on the solder mask material used (green, red, blue, black, white, etc.). You can specify the mask color in your fab drawing, or select it when ordering from the fab house. The mask opening in your CAD design determines where copper is exposed and solder wets to the pad.
What size pad should I use for a given component package?
Use the component manufacturer’s recommended pad layout for that package if available. Otherwise, common footprints are published in datasheets, application notes, and online CAD libraries. Typical pad sizes range from 0.02″ for small chips up to 0.1″ or larger for connectors and power components.
By carefully designing your solder pads in Eagle following these tips, you’ll create PCBs that are easier to assemble and more reliable in operation. As you gain experience with pad layout, you’ll develop an intuitive feel for optimal pad sizes, shapes, and spacing for various components and manufacturing processes.
Leave a Reply