Factors Affecting PCB Prototype Cost
1. Board Size and Complexity
The size and complexity of your PCB design significantly impact the overall prototype cost. Larger boards require more materials and take longer to manufacture, resulting in higher costs. Additionally, complex designs with intricate routing, multiple layers, and high component density will also increase the price.
Board Size | Complexity | Estimated Cost |
---|---|---|
Small (< 50 sq. cm) | Simple (1-2 layers) | $50 – $200 |
Medium (50-200 sq. cm) | Moderate (4-6 layers) | $200 – $500 |
Large (> 200 sq. cm) | High (8+ layers) | $500 – $1,500+ |
2. Number of Layers
The number of layers in your PCB directly affects the prototype cost. Each additional layer requires more materials, processing time, and labor, leading to higher costs. Here’s a breakdown of how the number of layers can impact the price:
Number of Layers | Estimated Cost Increase |
---|---|
1-2 | Base cost |
4 | +20-40% |
6 | +40-60% |
8+ | +60-100%+ |
3. Material Selection
The choice of PCB material also plays a role in determining the prototype cost. Standard FR-4 is the most common and economical option, while high-performance materials like Rogers or Polyimide will increase costs due to their superior electrical and thermal properties.
Material | Estimated Cost Increase |
---|---|
FR-4 | Base cost |
Rogers | +50-100% |
Polyimide | +100-200% |
4. Surface Finish
The surface finish of your PCB prototype affects both the cost and the performance of the final product. Common surface finishes include:
- HASL (Hot Air Solder Leveling)
- Lead-free HASL
- ENIG (Electroless Nickel Immersion Gold)
- OSP (Organic Solderability Preservative)
HASL is the most economical option, while ENIG offers superior durability and flatness at a higher cost.
Surface Finish | Estimated Cost Increase |
---|---|
HASL | Base cost |
Lead-free HASL | +10-20% |
ENIG | +20-40% |
OSP | +5-15% |
5. Quantity
The number of prototypes you order will also affect the overall cost. Most PCB manufacturers offer discounts for higher quantities, as the setup costs can be spread across more units. However, for prototyping purposes, it’s generally recommended to order only the minimum number required for testing and validation.
Quantity | Estimated Cost per Unit |
---|---|
1-5 | Full price |
10-50 | -10-20% |
50-100 | -20-30% |
100+ | -30-50% |
6. Turnaround Time
The turnaround time for your PCB prototype is another factor that can influence the cost. Faster turnaround times often come with a premium price, as manufacturers need to prioritize your order and potentially work overtime to meet the deadline.
Turnaround Time | Estimated Cost Increase |
---|---|
Standard (7-15 days) | Base cost |
Expedited (3-6 days) | +50-100% |
Rush (1-2 days) | +100-200% |
Additional Costs to Consider
Beyond the direct costs of PCB prototyping, there are several additional expenses to keep in mind:
- Design software and tools
- Components and materials for assembly
- Testing and validation equipment
- Shipping and handling fees
- Taxes and import duties (if applicable)
These costs can add up quickly, so it’s essential to factor them into your overall budget.
Choosing the Right PCB Prototype Manufacturer
With numerous PCB prototype manufacturers available, it’s crucial to select one that balances cost, quality, and service. Consider the following factors when making your decision:
- Reputation and experience
- Quality control processes
- Customer support and communication
- Capabilities and technology
- Pricing and discounts
Don’t hesitate to request quotes from multiple manufacturers and compare their offerings to find the best fit for your project and budget.
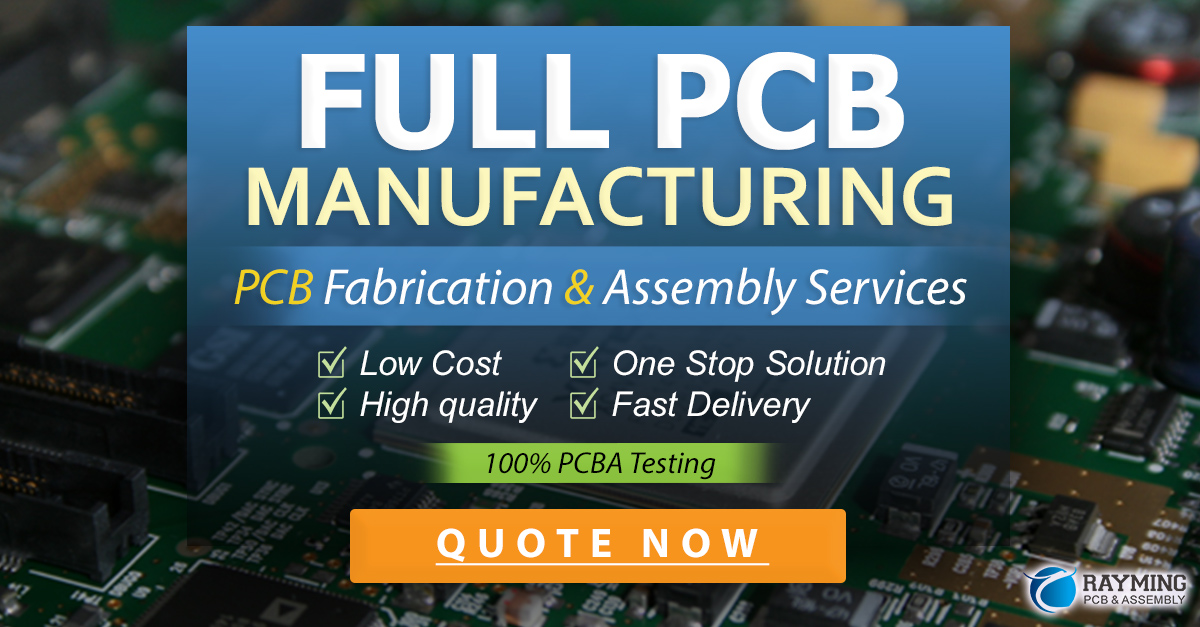
Cost-Saving Strategies
To help minimize your PCB prototype costs, consider the following strategies:
- Optimize your design for manufacturability
- Use standard materials and components whenever possible
- Minimize the number of layers and board size
- Choose a cost-effective surface finish
- Plan ahead to avoid rush fees
- Order in larger quantities if feasible
By implementing these strategies, you can effectively reduce your PCB prototype costs without compromising on quality or functionality.
Conclusion
PCB prototype cost is a critical consideration for any electronic design project. By understanding the various factors that influence the price, you can make informed decisions and allocate your budget effectively. Remember to balance cost with quality, and choose a reputable manufacturer that can deliver reliable prototypes within your timeframe and budget.
Frequently Asked Questions (FAQ)
-
Q: What is the average cost of a PCB prototype?
A: The average cost of a PCB prototype can range from $50 to $1,500 or more, depending on the size, complexity, materials, and other factors discussed in this article. -
Q: How can I reduce my PCB prototype costs?
A: To reduce PCB prototype costs, optimize your design for manufacturability, use standard materials and components, minimize layers and board size, choose a cost-effective surface finish, plan ahead to avoid rush fees, and consider ordering in larger quantities if possible. -
Q: What is the fastest turnaround time for PCB Prototypes?
A: The fastest turnaround time for PCB prototypes is typically 1-2 days, but this comes with a significant cost premium. Standard turnaround times range from 7-15 days. -
Q: Do I need to use high-performance materials for my PCB prototype?
A: The choice of materials depends on your specific application and requirements. Standard FR-4 is sufficient for most prototypes, but high-performance materials like Rogers or Polyimide may be necessary for demanding applications. -
Q: How do I choose the right PCB prototype manufacturer?
A: When selecting a PCB prototype manufacturer, consider factors such as reputation, experience, quality control processes, customer support, capabilities, and pricing. Request quotes from multiple manufacturers and compare their offerings to find the best fit for your project and budget.
Leave a Reply