Introduction to PCB Vias
Printed Circuit Boards (PCBs) are essential components in modern electronics. They provide a platform for mounting and interconnecting electronic components, enabling the creation of complex circuits. One crucial aspect of PCB design is the use of vias, which are small conductive holes that allow electrical connections between different layers of a multi-layer PCB. In this article, we will dive deep into the world of PCB vias, exploring their types, applications, design considerations, and manufacturing processes.
What are PCB Vias?
PCB vias are small holes drilled through a printed circuit board that are plated with a conductive material, typically copper. They provide electrical connectivity between different layers of a multi-layer PCB, allowing signals and power to travel from one layer to another. Vias are essential for creating compact and efficient PCB designs, as they enable the use of multiple layers to route traces and connect components.
Types of PCB Vias
There are several types of PCB vias, each with its own characteristics and applications. Let’s explore the most common types:
-
Through-hole Vias: These are the most basic type of vias, consisting of a hole drilled through the entire thickness of the PCB. Through-hole vias are plated with copper to provide electrical conductivity. They are typically used for mounting through-hole components or for providing structural support to the board.
-
Blind Vias: Blind vias are holes that start from one surface of the PCB and terminate at an inner layer, without reaching the opposite surface. They are used to connect an outer layer to one or more inner layers, allowing for more compact and efficient routing of traces.
-
Buried Vias: Buried vias are holes that are entirely embedded within the inner layers of a PCB, without reaching either surface. They are used to connect two or more inner layers, providing additional routing options and reducing the overall size of the PCB.
-
Micro Vias: Micro vias are very small vias, typically less than 0.15mm in diameter. They are used in high-density PCB designs to connect fine-pitch components or to create high-density interconnects between layers. Micro vias are usually created using laser drilling or photolithography techniques.
-
Stacked Vias: Stacked vias are a combination of multiple vias stacked on top of each other, connecting several layers of a PCB. They are used when a direct connection is required between non-adjacent layers, reducing the need for additional routing space.
Here’s a table summarizing the different types of PCB vias:
Via Type | Description |
---|---|
Through-hole | Drilled through the entire PCB thickness, plated with copper |
Blind | Starts from one surface and terminates at an inner layer |
Buried | Entirely embedded within inner layers, not reaching surfaces |
Micro | Very small vias (<0.15mm) for high-density designs |
Stacked | Multiple vias stacked to connect non-adjacent layers |
PCB Via Design Considerations
Designing PCB vias requires careful consideration of various factors to ensure optimal performance, reliability, and manufacturability. Let’s discuss some key design considerations:
Via Size and Spacing
The size and spacing of vias are critical factors in PCB design. The via diameter should be large enough to allow for proper plating and to maintain structural integrity, but small enough to minimize the space they occupy on the board. The spacing between vias should also be considered to avoid electrical and thermal interference, as well as to ensure manufacturability.
The following table provides general guidelines for via sizes and spacing:
Via Type | Diameter (mm) | Pad Size (mm) | Spacing (mm) |
---|---|---|---|
Through-hole | 0.3 – 1.0 | 0.6 – 1.5 | 0.8 – 2.0 |
Blind | 0.2 – 0.5 | 0.4 – 0.8 | 0.6 – 1.2 |
Buried | 0.2 – 0.5 | 0.4 – 0.8 | 0.6 – 1.2 |
Micro | 0.05 – 0.15 | 0.1 – 0.3 | 0.2 – 0.5 |
Note that these are general guidelines, and the actual dimensions may vary depending on the specific PCB design, manufacturing capabilities, and industry standards.
Via Placement and Routing
The placement and routing of vias are crucial for ensuring signal integrity and minimizing interference. When placing vias, consider the following:
-
Signal Integrity: Place vias close to the components they are connecting to minimize the length of the signal path. This reduces signal reflections and improves overall signal integrity.
-
Thermal Management: Avoid placing vias too close to heat-generating components, as they can act as thermal conductors and transfer heat to other layers of the PCB.
-
Manufacturing Constraints: Consider the manufacturing capabilities of your PCB fabricator when placing vias. Ensure that the via sizes and spacing are within their manufacturing tolerances to avoid issues during production.
When routing traces through vias, follow these guidelines:
-
Minimize Via Count: Use the minimum number of vias necessary to achieve the desired connectivity. Excessive use of vias can increase manufacturing costs and decrease reliability.
-
Avoid Acute Angles: Route traces through vias at angles close to 90 degrees to minimize signal reflections and improve signal integrity.
-
Provide Adequate Clearance: Ensure sufficient clearance between vias and other components, traces, and board edges to avoid shorts and manufacturing issues.
Via-in-Pad Design
Via-in-pad design is a technique where vias are placed directly on component pads, eliminating the need for additional traces between the pad and via. This approach saves space and simplifies the PCB layout. However, it requires careful consideration of the following factors:
-
Solder Mask Design: Ensure that the solder mask aperture is large enough to accommodate both the component pad and the via. This prevents solder from wicking into the via during the assembly process.
-
Via Filling: Consider filling the via with a non-conductive material, such as epoxy, to prevent solder from entering the via and causing shorts or reliability issues.
-
Component Compatibility: Verify that the components being used are compatible with via-in-pad design. Some components may have specific requirements or limitations.
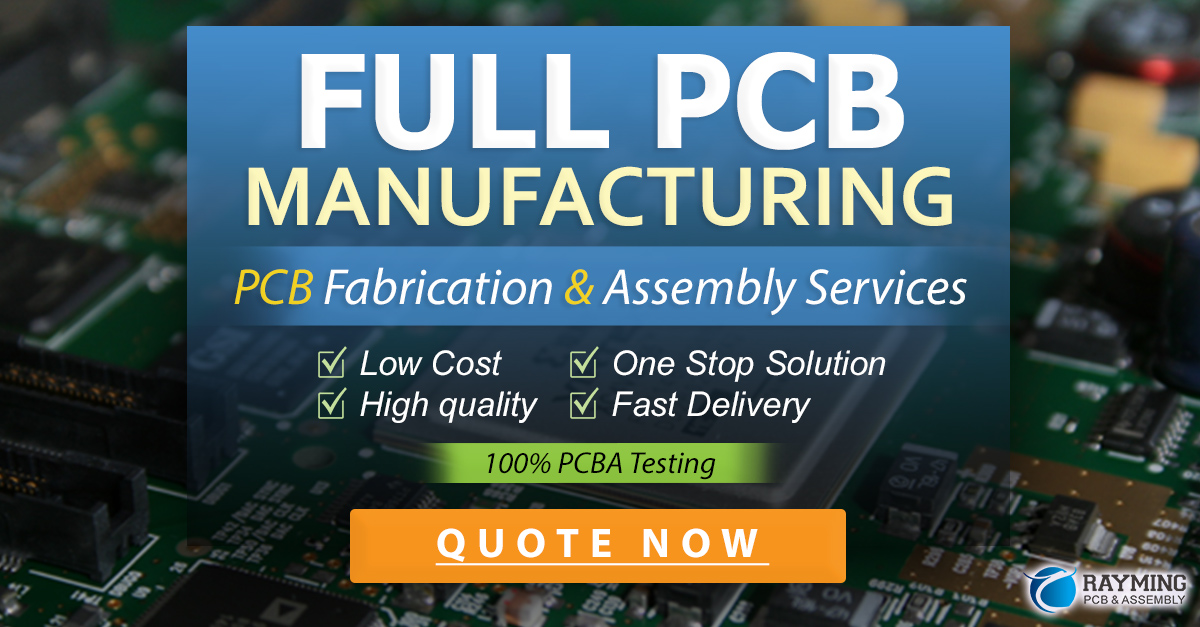
PCB Via Manufacturing Processes
The manufacturing of PCB vias involves several processes to ensure proper electrical connectivity and reliability. Let’s explore the key manufacturing processes:
Drilling
The first step in via manufacturing is drilling holes through the PCB substrate. There are two main drilling methods:
-
Mechanical Drilling: This method uses a high-speed drill bit to create holes in the PCB. Mechanical drilling is suitable for larger via sizes and is the most common method for through-hole vias.
-
Laser Drilling: Laser drilling uses a focused laser beam to ablate the PCB substrate and create smaller, more precise holes. This method is often used for creating micro vias and blind vias.
Plating
After drilling, the via holes are plated with a conductive material, typically copper, to provide electrical conductivity. There are two primary plating methods:
-
Electroless Plating: This process involves depositing a thin layer of copper onto the via walls using a chemical reduction process. Electroless plating provides a uniform coating and is suitable for high-aspect-ratio vias.
-
Electrolytic Plating: In this process, an electric current is applied to the PCB, causing copper ions to be deposited onto the via walls. Electrolytic plating is faster than electroless plating and is commonly used for larger via sizes.
Via Filling
In some cases, vias may be filled with a non-conductive material to improve thermal management, prevent solder wicking, or provide structural support. Common via filling materials include epoxy, resin, and conductive paste. Via filling can be done using various methods, such as screen printing, stencil printing, or vacuum-assisted filling.
Via Capping
Via capping is a process where a conductive material, such as copper or gold, is deposited over the top of a via to seal it and provide a flat surface for component mounting. Via capping is often used in high-density PCB designs to enable via-in-pad techniques and improve reliability.
FAQ
- What is the purpose of vias in PCBs?
-
Vias provide electrical connectivity between different layers of a multi-layer PCB, allowing signals and power to travel from one layer to another.
-
What are the different types of PCB vias?
-
The different types of PCB vias include through-hole vias, blind vias, buried vias, micro vias, and stacked vias.
-
What factors should be considered when designing vias?
-
When designing vias, consider factors such as via size and spacing, placement and routing, signal integrity, thermal management, and manufacturing constraints.
-
What is via-in-pad design, and what are its benefits?
-
Via-in-pad design is a technique where vias are placed directly on component pads, eliminating the need for additional traces. It saves space and simplifies the PCB layout but requires careful consideration of solder mask design, via filling, and component compatibility.
-
What are the key manufacturing processes involved in creating PCB vias?
- The key manufacturing processes for PCB vias include drilling (mechanical or laser), plating (electroless or electrolytic), via filling, and via capping.
Conclusion
PCB vias are essential components in modern electronics, enabling the creation of compact and efficient multi-layer PCBs. Understanding the types of vias, design considerations, and manufacturing processes is crucial for designing reliable and high-performance electronic devices.
By carefully selecting the appropriate via types, optimizing their placement and routing, and considering manufacturing constraints, designers can create PCBs that meet the demanding requirements of today’s electronic applications. As technology advances, the use of advanced via techniques, such as micro vias and via-in-pad design, will become increasingly important for achieving higher density and improved performance.
In conclusion, a thorough understanding of PCB vias is essential for anyone involved in electronic design and manufacturing. By staying up-to-date with the latest techniques and best practices, designers and engineers can create innovative and reliable electronic products that push the boundaries of what is possible.
Leave a Reply