What is a PCB?
A PCB is a flat board made of insulating material, such as fiberglass or plastic, with conductive copper traces printed on its surface. These traces connect various electronic components, such as resistors, capacitors, and integrated circuits (ICs), to form a complete electronic circuit. PCBs provide a stable and reliable platform for these components to function together.
Types of PCBs
There are several types of PCBs, each with its own unique features and applications. The main types of PCBs are:
- Single-sided PCBs
- Double-sided PCBs
- Multi-layer PCBs
- Flexible PCBs
- Rigid-Flex PCBs
- High Density Interconnect (HDI) PCBs
- Metal Core PCBs
- Aluminum PCBs
1. Single-sided PCBs
Single-sided PCBs, also known as single-layer PCBs, have conductive traces on only one side of the board. The other side is usually left bare or used for component labeling. These PCBs are the simplest and most cost-effective type, making them ideal for low-complexity projects and prototypes.
Advantages of Single-sided PCBs
- Low cost
- Easy to design and manufacture
- Suitable for low-density circuits
- Quick turnaround time
Disadvantages of Single-sided PCBs
- Limited routing options
- Not suitable for complex circuits
- Lower durability compared to other types
Applications of Single-sided PCBs
- Simple electronic devices (e.g., calculators, toys)
- Low-power amplifiers
- Educational projects
2. Double-sided PCBs
Double-sided PCBs have conductive traces on both sides of the board, allowing for more complex routing and higher component density compared to single-sided PCBs. The two layers are connected using vias, which are small holes drilled through the board and plated with conductive material.
Advantages of Double-sided PCBs
- Increased routing options
- Higher component density
- Better signal integrity
- Improved heat dissipation
Disadvantages of Double-sided PCBs
- Higher cost compared to single-sided PCBs
- More complex design and manufacturing process
- Potential for crosstalk between layers
Applications of Double-sided PCBs
- Power supplies
- Amplifiers
- Automotive electronics
- Industrial control systems
3. Multi-layer PCBs
Multi-layer PCBs consist of three or more conductive layers separated by insulating material. These layers are interconnected using vias, allowing for even more complex routing and higher component density than double-sided PCBs. Multi-layer PCBs are commonly used in high-speed digital circuits and devices with limited space.
Advantages of Multi-layer PCBs
- High component density
- Excellent signal integrity
- Reduced electromagnetic interference (EMI)
- Improved heat dissipation
Disadvantages of Multi-layer PCBs
- High cost due to complex manufacturing process
- Longer design and production time
- Difficult to repair or modify
Applications of Multi-layer PCBs
- Smartphones and tablets
- Computers and laptops
- Medical devices
- Aerospace and defense systems
PCB Type | Layers | Complexity | Cost | Applications |
---|---|---|---|---|
Single-sided | 1 | Low | Low | Simple devices, prototypes |
Double-sided | 2 | Medium | Medium | Power supplies, automotive electronics |
Multi-layer | 3+ | High | High | Smartphones, computers, medical devices |
4. Flexible PCBs
Flexible PCBs, or flex PCBs, are made using a flexible insulating material, such as polyimide or polyester, with conductive traces printed on its surface. These PCBs can bend and twist without damaging the circuits, making them ideal for applications with limited space or requiring movable parts.
Advantages of Flexible PCBs
- Flexibility and durability
- Lightweight and thin profile
- Reduced assembly time and costs
- Improved signal integrity
Disadvantages of Flexible PCBs
- Higher cost compared to rigid PCBs
- Limited component options due to flexible nature
- More complex design and manufacturing process
Applications of Flexible PCBs
- Wearable electronics
- Medical implants
- Aerospace and military equipment
- Automotive electronics
5. Rigid-Flex PCBs
Rigid-Flex PCBs combine the benefits of both rigid and flexible PCBs. They consist of rigid PCB sections connected by flexible PCB sections, allowing for a more compact and reliable design. Rigid-Flex PCBs are often used in applications requiring high density and reliability in a limited space.
Advantages of Rigid-Flex PCBs
- Combines benefits of rigid and flexible PCBs
- Reduced size and weight
- Improved reliability and durability
- Simplified assembly process
Disadvantages of Rigid-Flex PCBs
- High cost due to complex manufacturing process
- Longer design and production time
- Limited flexibility compared to pure flex PCBs
Applications of Rigid-Flex PCBs
- Aerospace and defense systems
- Medical devices
- Industrial control systems
- High-end consumer electronics
6. High Density Interconnect (HDI) PCBs
HDI PCBs are designed to accommodate a high number of components in a small area. They feature fine pitch traces, small vias, and high layer counts, enabling the creation of highly compact and complex electronic devices. HDI PCBs are commonly used in advanced electronic applications where space is at a premium.
Advantages of HDI PCBs
- High component density
- Improved signal integrity
- Reduced size and weight
- Enhanced thermal performance
Disadvantages of HDI PCBs
- High cost due to advanced manufacturing techniques
- Complex design and layout process
- Potential for signal integrity issues if not designed properly
Applications of HDI PCBs
- Smartphones and wearable devices
- High-performance computing
- Aerospace and defense systems
- Medical imaging equipment
7. Metal Core PCBs
Metal Core PCBs (MCPCBs) feature a metal substrate, typically aluminum, instead of the traditional fiberglass substrate. The metal core helps dissipate heat more efficiently, making MCPCBs ideal for applications generating significant heat, such as high-power LEDs and power electronics.
Advantages of Metal Core PCBs
- Excellent thermal conductivity
- Improved reliability and longevity
- Reduced size and weight
- Enhanced mechanical stability
Disadvantages of Metal Core PCBs
- Higher cost compared to traditional PCBs
- Limited design flexibility due to metal substrate
- Potential for thermal expansion mismatch
Applications of Metal Core PCBs
- High-power LED lighting
- Automotive electronics
- Power converters and inverters
- High-performance computing
8. Aluminum PCBs
Aluminum PCBs are a type of metal core PCB that uses an aluminum substrate for improved thermal management. They are similar to MCPCBs but specifically designed for applications requiring even better heat dissipation, such as high-power RF amplifiers and laser diodes.
Advantages of Aluminum PCBs
- Superior thermal conductivity compared to MCPCBs
- Excellent mechanical stability
- Reduced size and weight
- Improved reliability and longevity
Disadvantages of Aluminum PCBs
- High cost due to specialized manufacturing process
- Limited design flexibility
- Potential for galvanic corrosion if not properly insulated
Applications of Aluminum PCBs
- High-power RF amplifiers
- Laser diodes and LED drivers
- Automotive power electronics
- Industrial control systems
Frequently Asked Questions (FAQ)
-
What is the most common type of PCB?
The most common type of PCB is the double-sided PCB, which offers a good balance between cost, complexity, and performance. Double-sided PCBs are widely used in various applications, from consumer electronics to industrial control systems. -
What are the main factors to consider when choosing a PCB type?
When choosing a PCB type, consider the following factors: - Circuit complexity and component density
- Signal integrity and speed requirements
- Thermal management needs
- Mechanical requirements (flexibility, durability)
- Size and weight constraints
-
Cost and production time
-
Can different types of PCBs be combined in a single design?
Yes, different types of PCBs can be combined in a single design. For example, rigid-flex PCBs combine rigid and flexible sections to create a more compact and reliable design. Additionally, HDI techniques can be applied to various PCB Types to increase component density and performance. -
What are the main challenges in PCB design and manufacturing?
The main challenges in PCB design and manufacturing include: - Ensuring signal integrity and minimizing electromagnetic interference
- Managing thermal dissipation and mechanical stress
- Achieving high component density while maintaining manufacturability
- Balancing cost, performance, and reliability
-
Keeping up with advancing technologies and changing industry standards
-
How do I choose the right PCB manufacturer for my project?
When choosing a PCB manufacturer, consider the following factors: - Experience and expertise in the specific PCB type and application
- Quality control and certification (e.g., ISO, UL, RoHS)
- Production capabilities and capacity
- Turnaround time and customer support
- Pricing and minimum order quantities
- Reputation and customer reviews
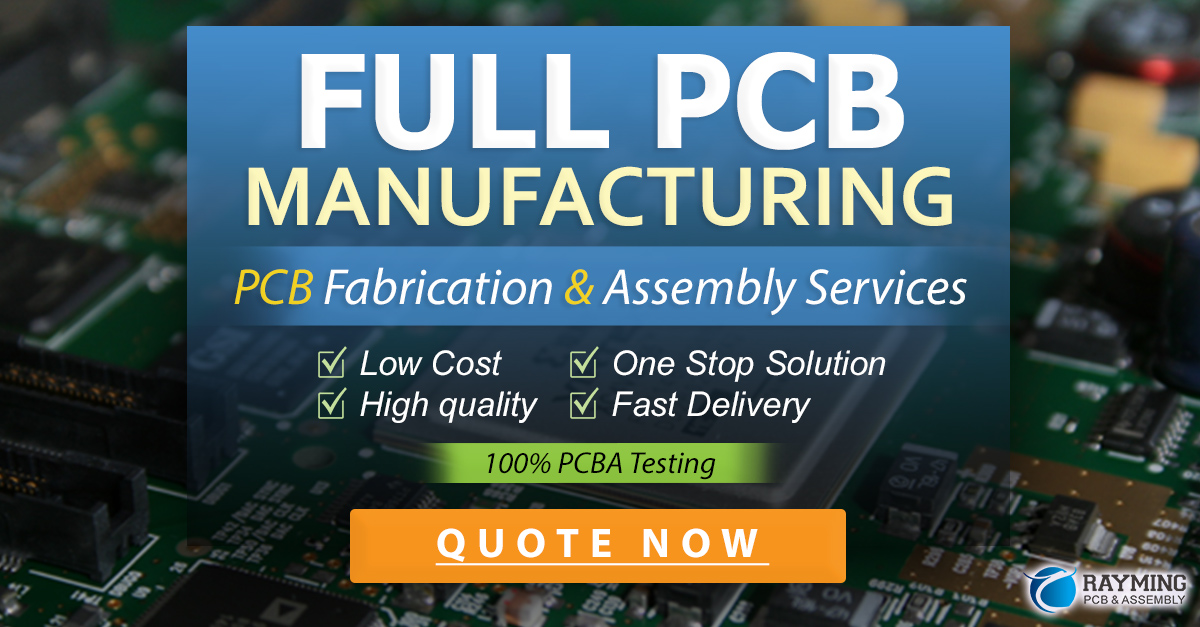
Conclusion
PCBs are essential components in the electronics industry, and understanding the various types of PCBs is crucial for designing and manufacturing successful electronic devices. Each PCB type has its own advantages, disadvantages, and applications, and selecting the right type depends on the specific requirements of the project.
As technology advances, PCB design and manufacturing processes continue to evolve, enabling the creation of more complex, compact, and reliable electronic devices. By staying informed about the latest PCB technologies and best practices, engineers and manufacturers can ensure their products remain competitive in the ever-changing electronics landscape.
Leave a Reply