Introduction to PCB laser drilling
PCB laser drilling is an advanced technology used in the manufacturing of printed circuit boards (PCBs). It involves using high-powered lasers to create precise micro-vias and holes in PCBs. Laser drilling enables the creation of much smaller, more accurate holes compared to traditional mechanical drilling methods.
PCB laser drilling has become increasingly important as electronics continue to get smaller and more complex. The ultra-small vias created by laser drilling are essential for high-density interconnect (HDI) PCBs used in compact, sophisticated electronic devices like smartphones.
In this article, we’ll take an in-depth look at how PCB laser drilling works, the different types of lasers used, and the key advantages laser drilling provides over other methods. We’ll also examine some challenges and best practices when implementing laser drilling in PCB production.
How PCB Laser Drilling Works
The Laser Drilling Process
The basic process of PCB laser drilling involves focusing a high-energy laser beam onto the surface of the PCB substrate to vaporize and remove material, creating a hole. The laser beam is pulsed rapidly, with each pulse vaporizing a small amount of material. By pulsing the laser thousands of times per second, a hole is gradually drilled through the PCB.
Here is a step-by-step overview of a typical PCB laser drilling process:
-
The PCB panel is loaded onto the laser drilling machine and precisely positioned using fiducial marks and high-resolution cameras.
-
The laser parameters (pulse energy, repetition rate, number of pulses, etc.) are set based on the specific job requirements – the material, thickness, and desired hole size.
-
The laser beam, focused to a very small spot size (typically 15-50 microns), is rapidly pulsed and scanned across the PCB surface by a galvanometer mirror system. This allows drilling multiple holes simultaneously.
-
As the laser beam hits the PCB, each pulse vaporizes a small amount of dielectric material, gradually ablating a hole through the board. The vaporized material is ejected out of the hole.
-
For thicker PCBs or smaller holes, the laser beam may need to make multiple passes, pulsing and ablating material with each pass until the hole is completely drilled through.
-
After drilling, the PCB may undergo additional cleaning processes to remove any debris or redeposited material around the hole perimeter.
The entire process is computer-controlled using CAM (computer-aided manufacturing) data generated from the PCB design files. Modern laser drilling machines can drill thousands of holes per second with exceptional accuracy and repeatability.
Types of Lasers Used
There are two main types of lasers used in PCB Drilling: UV lasers and CO2 lasers. Each type has its own strengths and is suited for different applications.
UV Lasers
UV lasers, also known as excimer lasers, use ultraviolet light with wavelengths typically in the 193-355nm range. Common types include KrF (krypton fluoride) lasers at 248nm and frequency-tripled Nd:YAG (neodymium-doped yttrium aluminum garnet) lasers at 355nm.
UV lasers are the most widely used for PCB drilling due to several advantages:
- Short wavelength enables very small focused spot sizes for drilling micro-vias down to 15-50 microns diameter
- High energy photons directly break molecular bonds in the PCB dielectric material, vaporizing it cleanly with minimal thermal effects
- Well-suited for drilling a variety of PCB materials including FR4, polyimide, and high-Tg laminates
- Fast drilling speeds with high repetition rates up to 100 kHz
The main drawback of UV lasers is higher operating cost compared to CO2 due to the more complex laser system and shorter operational lifetimes of the laser gases and optics.
CO2 Lasers
CO2 lasers use infrared light at a much longer wavelength, typically 9.3-10.6 microns. They work by heating and thermally vaporizing the PCB material.
Advantages of CO2 lasers include:
- Lower cost and complexity compared to UV laser systems
- Well-suited for drilling larger holes >150 microns in diameter
- Efficient removal of non-homogeneous PCB materials like woven glass reinforced substrates
However, CO2 lasers have some limitations:
- Longer wavelength limits the minimum focused spot size and hole diameter achievable
- Thermal ablation mechanism causes more heat-affected zones (HAZ) around drilled holes
- Not well-suited for drilling micro-vias in multilayer HDI PCB designs
In general, UV lasers are preferred for most PCB drilling applications, especially high-density designs requiring small micro-vias. CO2 lasers still play a role for certain niche applications involving larger holes or speciality material combinations.
Advantages of PCB Laser Drilling
PCB laser drilling provides several key advantages compared to traditional mechanical drilling methods:
Smaller Hole Sizes
One of the biggest advantages of laser drilling is the ability to create much smaller holes than is possible with mechanical drills. UV lasers can produce holes as small as 15-50 microns in diameter, well beyond the limits of even the smallest mechanical drill bits.
This is crucial for HDI PCB designs which require large numbers of micro-vias to interconnect high-density BGA and CSP components. Smaller vias enable tighter routing density and more compact PCB layouts.
Improved Hole Quality
Laser drilled holes have superior hole wall quality compared to mechanically drilled holes. The laser vaporization process produces smooth, straight hole walls with no nail-heading or bell-mouthing effects.
The cleaner hole geometry is beneficial for reliable plating and copper deposition during subsequent manufacturing steps. It helps ensure consistent impedance and signal integrity, especially important for high-frequency RF/microwave PCBs.
Faster Drilling Speeds
Laser drilling is significantly faster than mechanical drilling for small holes. With drilling rates up to 5000 holes per second, UV laser systems can outpace even the fastest multi-spindle mechanical drills.
This is due to:
– No time wasted on tool changes – the laser can adjust parameters to drill different sizes on the fly
– Ability to drill staggered hole patterns across the entire PCB panel in one step
– No issues with drill bit breakage or wear
Faster drilling translates to shorter cycle times, improved throughput, and lower cost per hole, especially for complex PCBs with large numbers of holes.
Greater Design Flexibility
Laser drilling enables greater flexibility in terms of where holes can be placed on the PCB. Mechanical drills are limited by the need to avoid intersecting internal copper layers and planes. Lasers have no such restrictions.
Holes can be drilled into internal pads or through copper planes without issue. Blind and buried vias of varying depths can easily be produced by controlling the laser pulses. This allows more creative and space-efficient PCB layouts.
Reduced Wear & Consumables
Another advantage is the fact that there are no drill bits or other consumables to be constantly replaced. Mechanical drills wear down and break frequently when drilling large numbers of small holes in abrasive PCB substrates.
With laser drilling, the only consumables are the laser gases which are replaced on much longer intervals. This reduces downtime and material waste.
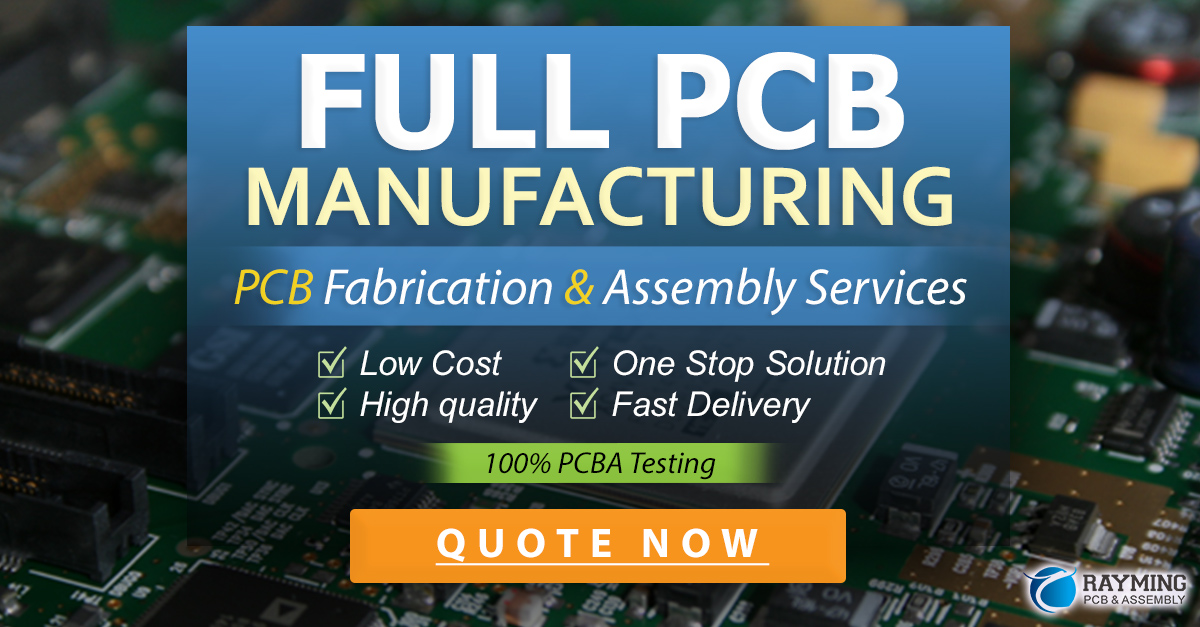
Challenges & Considerations
While laser drilling provides many benefits, there are some challenges and considerations to keep in mind:
Heat Effects
The laser ablation process generates intense localized heat which can cause thermal damage around the drilled hole. Charring, heat-affected zones (HAZ), and redeposited debris are common issues that must be minimized.
Careful control of laser parameters like pulse energy, duration, and repetition rate is necessary to achieve clean, precise holes. Post-drilling cleaning processes may be required.
Drilling Thicker Boards
Drilling through thicker PCBs >1mm can be challenging for UV lasers. The high aspect ratios required limit the minimum hole size achievable and may necessitate multiple passes which slows the drilling speed.
Hybrid approaches combining UV and CO2 lasers or mechanical drilling are sometimes used for thick boards with a mix of small and large holes.
Capital Equipment Cost
Industrial UV laser drilling systems represent a significant capital investment, often costing upwards of $1 million USD. The high equipment cost must be justified by production volume and hole density requirements.
However, the total cost per hole is often lower than mechanical drilling for large numbers of small holes due to the speed advantage. CO2 laser systems are less costly but more limited in terms of hole size and quality.
Frequently Asked Questions (FAQ)
What is the smallest hole size that can be laser drilled in a PCB?
UV lasers can typically drill holes as small as 15-50 microns (0.006-0.002 inches) in diameter, depending on the material and thickness. CO2 lasers are limited to larger holes >150 microns.
How fast is laser drilling compared to mechanical drilling?
UV laser drilling can achieve speeds up to 5000 holes per second for small micro-vias, significantly faster than mechanical drilling. The speed advantage is most pronounced for large numbers of holes <0.2mm in diameter.
What materials can be laser drilled?
Most common PCB dielectric materials including FR4, polyimide, and high-Tg laminates are compatible with UV laser drilling. CO2 lasers can handle a wider range of materials including ceramics and glass-reinforced substrates.
Is laser drilling more expensive than mechanical drilling?
The capital equipment cost for UV laser drilling systems is higher than mechanical drills. However, the total cost per hole is often lower for high hole counts due to the speed advantage and elimination of consumables like drill bits. CO2 laser systems have a lower capital cost.
What are the key advantages of laser drilling over mechanical drilling?
The main advantages of laser drilling include smaller hole sizes, improved hole quality, faster drilling speeds, greater design flexibility, and reduced consumables and tool wear. These benefits are most significant for HDI PCBs with large numbers of micro-vias.
Conclusion
PCB laser drilling is a powerful technology that has become indispensable for manufacturing the high-density interconnects required in today’s advanced electronics. By enabling smaller, more precise holes to be drilled at high speeds, laser drilling overcomes the limitations of traditional mechanical methods.
As PCB designs continue to push the boundaries of miniaturization and complexity, laser drilling will play an increasingly vital role. Understanding the capabilities, advantages, and tradeoffs of UV and CO2 laser systems is important for optimizing PCB fabrication processes.
While laser drilling involves significant capital investment and some unique challenges, the benefits in terms of hole quality, speed, and design flexibility make it a compelling choice for a growing range of applications. As laser technology continues to advance, even smaller vias and faster drilling speeds will be possible, further expanding the horizons of PCB design and manufacturing.
| Laser Type | Wavelength | Hole Size | Drilling Speed | Relative Cost |
|------------|------------|-----------|----------------|---------------|
| UV | 193-355nm | 15-50μm | Fast (5000/sec)| High |
| CO2 | 9.3-10.6μm | >150μm | Moderate | Medium |
| Drilling Method | Minimum Hole Size | Speed for Small Holes | Consumables | Capital Cost |
|-----------------|-------------------|------------------------|-------------|--------------|
| UV Laser | 15-50μm | Fast (5000/sec) | Gases | High |
| CO2 Laser | >150μm | Moderate | Gases | Medium |
| Mechanical | >200μm | Slow | Drill Bits | Low |
Leave a Reply