Understanding Thermal dissipation
Thermal dissipation refers to the process of removing heat from a system and transferring it to the surrounding environment. This is essential to maintain the temperature of the system within its operating limits and prevent overheating, which can lead to reduced performance, component damage, and even complete system failure.
Mechanisms of Heat Transfer
To effectively dissipate heat, it is important to understand the three primary mechanisms of heat transfer:
-
Conduction: Heat transfer through direct contact between two objects or materials. Heat flows from the hotter object to the cooler object until thermal equilibrium is reached.
-
Convection: Heat transfer through the movement of fluids (liquids or gases). As the fluid moves, it carries heat away from the source and distributes it throughout the surrounding environment.
-
Radiation: Heat transfer through electromagnetic waves, without the need for a physical medium. All objects emit and absorb thermal radiation, with the net heat transfer depending on the temperature difference between the objects.
Passive Cooling Techniques
Passive cooling techniques rely on natural heat transfer mechanisms and do not require any external power input. These methods are often simple, cost-effective, and reliable.
Heat Sinks
Heat sinks are among the most common passive cooling solutions. They are designed to increase the surface area available for heat dissipation, allowing for more efficient heat transfer to the surrounding environment. Heat sinks are typically made of materials with high thermal conductivity, such as aluminum or copper, and feature fins or pins to maximize surface area.
Material | Thermal Conductivity (W/mK) |
---|---|
Aluminum | 205 |
Copper | 401 |
Silver | 429 |
Gold | 318 |
When selecting a heat sink, consider factors such as material, size, and fin design to ensure optimal performance for your specific application.
Thermal Interface Materials (TIMs)
Thermal interface materials are used to improve heat transfer between two surfaces, such as a heat source (e.g., a processor) and a heat sink. TIMs help to fill any air gaps or irregularities between the surfaces, which would otherwise impede heat transfer. Common TIMs include:
- Thermal greases
- Thermal pads
- Phase change materials (PCMs)
Proper application of TIMs is essential to ensure effective heat transfer and prevent air pockets or voids that could hinder performance.
Natural Convection
Natural convection relies on the natural movement of air caused by temperature differences. As air near a heat source warms up, it becomes less dense and rises, allowing cooler air to take its place. This continuous cycle of air movement helps to dissipate heat away from the source.
To optimize natural convection, consider the following:
- Orientation: Position the heat source and any associated heat sinks or fins to allow for unobstructed airflow.
- Ventilation: Ensure adequate ventilation around the system to allow for the efficient exchange of warm and cool air.
- Enclosure design: Use enclosures with vents or perforations to promote airflow while still providing protection for the components.
Active Cooling Techniques
Active cooling techniques involve the use of external power to facilitate heat transfer and improve cooling performance. These methods are often employed when passive cooling alone is insufficient to maintain the desired temperature range.
Fans
Fans are a simple and effective way to enhance convection cooling. By actively moving air across heat sinks or other heat-dissipating surfaces, fans can significantly improve heat transfer rates. When selecting a fan, consider factors such as:
- Airflow: Measured in cubic feet per minute (CFM), higher airflow generally results in better cooling performance.
- Static pressure: The fan’s ability to overcome resistance to airflow, which is important when used with dense heat sinks or in restrictive enclosures.
- Noise level: Measured in decibels (dB), higher noise levels may be acceptable in some applications but not in others, such as personal computers or audio equipment.
Fan Size (mm) | Typical Airflow Range (CFM) | Typical Noise Range (dB) |
---|---|---|
40 x 40 x 10 | 3 – 8 | 15 – 25 |
60 x 60 x 15 | 10 – 25 | 20 – 35 |
80 x 80 x 25 | 20 – 40 | 25 – 40 |
120 x 120 x 25 | 40 – 80 | 30 – 45 |
Liquid Cooling
Liquid cooling systems use a liquid coolant to absorb heat from the source and transfer it to a radiator, where it is dissipated to the surrounding environment. Liquid cooling can be more effective than air cooling, as liquids generally have higher thermal conductivities and heat capacities than air.
Liquid cooling systems typically consist of the following components:
- Waterblock: A heat exchanger that sits directly on the heat source, absorbing heat into the coolant.
- Radiator: A heat exchanger that dissipates heat from the coolant into the surrounding air.
- Pump: Circulates the coolant through the system.
- Reservoir (optional): Stores excess coolant and helps with filling and bleeding the system.
Liquid cooling can be further classified into two main types:
- All-in-one (AIO) liquid coolers: Pre-assembled, closed-loop systems that are easy to install and maintain.
- Custom liquid cooling loops: User-designed and assembled systems that offer greater flexibility and customization but require more expertise to set up and maintain.
Thermoelectric Cooling (TEC)
Thermoelectric cooling, also known as Peltier cooling, uses the Peltier effect to create a heat flux between the junction of two different materials when an electric current is applied. TECs consist of a series of p-type and n-type semiconductor elements sandwiched between two ceramic plates. When a DC current is applied, heat is absorbed on one side (cold side) and released on the other (hot side).
TECs can be used for spot cooling of specific components or for creating sub-ambient temperatures. However, they have relatively low efficiency compared to other cooling methods and generate additional heat that must be dissipated from the hot side.
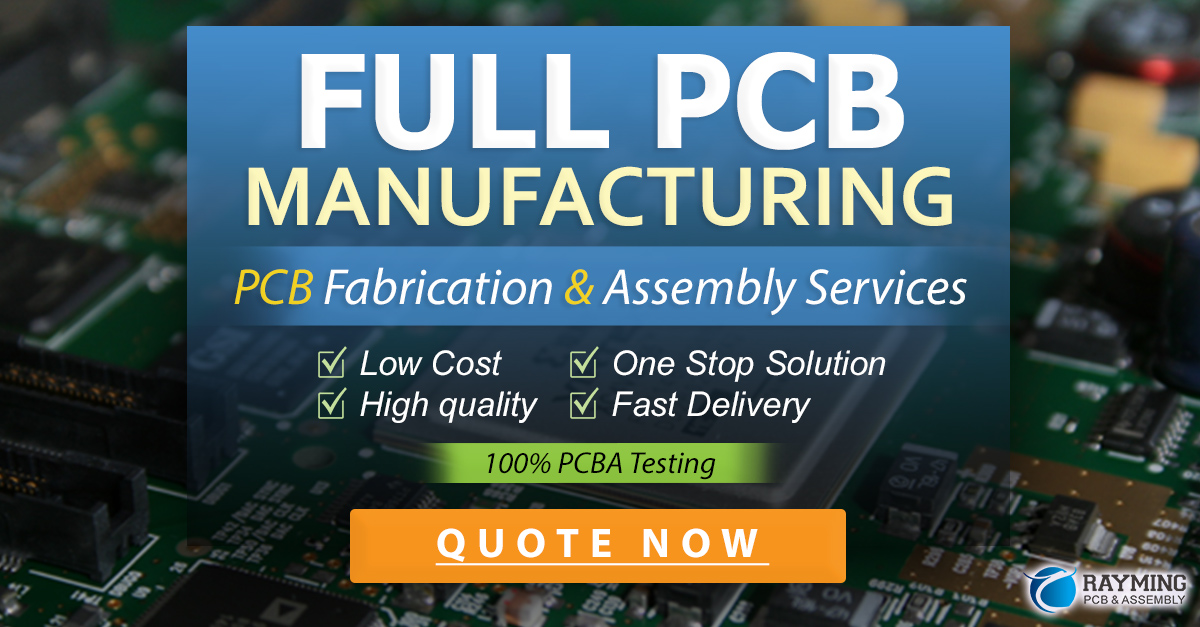
Advanced Cooling Techniques
In addition to the conventional cooling methods discussed above, there are several advanced techniques that can be employed for more demanding thermal management applications.
Vapor Chamber Cooling
Vapor chambers are essentially flat heat pipes that use phase change to transfer heat. They consist of a sealed chamber containing a small amount of working fluid, typically water or alcohol. As heat is applied to one side of the vapor chamber, the fluid evaporates, carrying heat to the cooler side where it condenses and releases the heat. The condensed fluid then returns to the hot side through capillary action, repeating the cycle.
Vapor chambers offer several advantages over traditional heat spreaders:
- High thermal conductivity: The phase change process allows for very efficient heat transfer across the vapor chamber.
- Uniform temperature distribution: Vapor chambers help to spread heat evenly across their surface, minimizing hot spots.
- Thin form factor: Vapor chambers can be made very thin, making them suitable for applications with limited space.
Immersion Cooling
Immersion cooling involves submerging the entire electronic system or component in a dielectric liquid coolant. The liquid directly contacts the heat-generating components, absorbing heat and transferring it away from the source. The heated liquid can then be cooled using a heat exchanger or by circulating it through a separate cooling system.
Immersion cooling offers several benefits:
- High cooling capacity: Direct liquid contact provides excellent heat transfer rates.
- Reduced thermal resistance: Eliminating the need for thermal interface materials reduces the overall thermal resistance between the heat source and the coolant.
- Simplicity: Immersion cooling can simplify system design by eliminating the need for individual heatsinks and cooling components.
However, immersion cooling also presents some challenges, such as the need for compatible materials, fluid maintenance, and the potential for leaks or spills.
Optimizing Thermal Dissipation
To achieve optimal thermal dissipation, consider the following best practices:
-
Understand the thermal characteristics of your system: Identify the primary heat sources, expected heat loads, and any thermal constraints or limitations.
-
Select appropriate cooling methods: Choose cooling techniques that best suit your application based on factors such as heat load, available space, power consumption, and cost.
-
Use thermal simulation and modeling: Employ thermal simulation software to predict system behavior, identify potential hot spots, and optimize cooling solutions before physical prototyping.
-
Monitor and control temperature: Implement temperature monitoring and control systems to ensure that your cooling solution is performing as expected and to prevent overheating.
-
Regularly maintain cooling components: Clean and replace cooling components as needed to ensure optimal performance and prevent dust or debris from impeding heat transfer.
Frequently Asked Questions (FAQ)
- What is the most effective cooling method for high-power electronic devices?
The most effective cooling method depends on the specific application and its requirements. For high-power electronics, liquid cooling or vapor chamber cooling may be the most suitable option due to their high cooling capacities and efficiency.
- Can I combine multiple cooling techniques for better performance?
Yes, combining multiple cooling techniques can often provide better performance than using a single method alone. For example, using a liquid cooling system in conjunction with high-performance thermal interface materials can help to maximize heat transfer from the source to the coolant.
- How often should I replace my thermal paste?
The lifespan of thermal paste depends on factors such as the quality of the paste, the operating temperature, and the environment. As a general rule, it is recommended to replace thermal paste every 2-3 years or whenever you notice a significant decrease in cooling performance.
- What is the difference between a heat sink and a heat spreader?
A heat sink is a passive cooling device designed to dissipate heat from a heat source to the surrounding environment, typically using fins or pins to increase surface area. A heat spreader, on the other hand, is a flat plate or vapor chamber that helps to evenly distribute heat across its surface, often used in conjunction with a heat sink to improve overall cooling performance.
- Can I use liquid cooling in a system that will be transported frequently?
While liquid cooling can be used in systems that are transported, it is important to take precautions to prevent leaks or spills during transit. This may involve using specialized fittings and tubing, securing the components properly, and ensuring that the system is drained or filled with a non-conductive fluid before transport.
In conclusion, achieving effective thermal dissipation is essential for maintaining optimal system performance and reliability. By understanding the various cooling techniques available and employing best practices for thermal management, designers and engineers can create robust, efficient, and long-lasting solutions for a wide range of applications.
Leave a Reply