What is Tented via clearance?
Tented via clearance, also known as hole edge to solder mask edge clearance, is a crucial aspect of printed circuit board (PCB) design. It refers to the distance between the edge of a Via hole and the edge of the surrounding solder mask opening. This clearance is essential for ensuring proper insulation and preventing short circuits between the via and nearby traces or components.
In PCB Manufacturing, vias are small holes drilled through the board to connect different layers of the circuit. These vias can be filled, partially filled, or left open, depending on the design requirements. Tented vias are a specific type of via where the solder mask covers the top and/or bottom of the via hole, leaving only a small opening around the edge.
Importance of Tented Via Clearance
Maintaining appropriate tented via clearance is important for several reasons:
-
Insulation: Adequate clearance between the via hole and solder mask edge prevents short circuits and ensures proper insulation between the via and adjacent traces or components.
-
Manufacturing Reliability: Sufficient clearance allows for proper solder mask application and reduces the risk of solder mask breakage or peeling during the manufacturing process.
-
Signal Integrity: Proper tented via clearance helps maintain signal integrity by minimizing the chances of unintended connections or signal leakage.
-
Compliance with Industry Standards: Adhering to recommended tented via clearance guidelines ensures compliance with industry standards and manufacturing best practices.
Factors Affecting Tented Via Clearance
Several factors influence the determination of appropriate tented via clearance:
Via Size and Aspect Ratio
The size of the via hole and its aspect ratio (the ratio of the hole depth to its diameter) play a significant role in determining the required clearance. Smaller via sizes and higher aspect ratios generally require larger clearances to ensure proper solder mask coverage and prevent manufacturing issues.
Solder Mask Material Properties
The properties of the solder mask material, such as its viscosity, flow characteristics, and curing process, can impact the minimum achievable clearance. Different solder mask materials may have varying requirements for minimum clearance to ensure proper adhesion and coverage.
PCB Manufacturing Capabilities
The capabilities of the PCB manufacturing facility, including the precision of their drilling and solder mask application processes, can influence the achievable tented via clearance. Advanced manufacturing equipment and techniques may allow for tighter clearances, while older or less precise equipment may require larger clearances to ensure reliability.
Design Requirements and Constraints
The specific design requirements and constraints of the PCB, such as the overall board size, component density, and signal integrity considerations, can impact the choice of tented via clearance. In some cases, tighter clearances may be necessary to accommodate dense layouts or high-speed signals, while other designs may allow for larger clearances to improve manufacturability.
Recommended Tented Via Clearance Guidelines
Industry standards and best practices provide guidelines for recommended tented via clearance based on via size and other factors. The following table presents general recommendations for minimum tented via clearance:
Via Hole Diameter | Minimum Tented Via Clearance |
---|---|
0.2 mm – 0.4 mm | 0.05 mm – 0.1 mm |
0.4 mm – 0.8 mm | 0.1 mm – 0.15 mm |
0.8 mm – 1.2 mm | 0.15 mm – 0.2 mm |
1.2 mm – 1.6 mm | 0.2 mm – 0.25 mm |
1.6 mm – 2.0 mm | 0.25 mm – 0.3 mm |
It’s important to note that these are general guidelines, and the actual clearance requirements may vary depending on the specific manufacturing capabilities, solder mask material, and design constraints. It’s always recommended to consult with the PCB Manufacturer and adhere to their specific guidelines for tented via clearance.
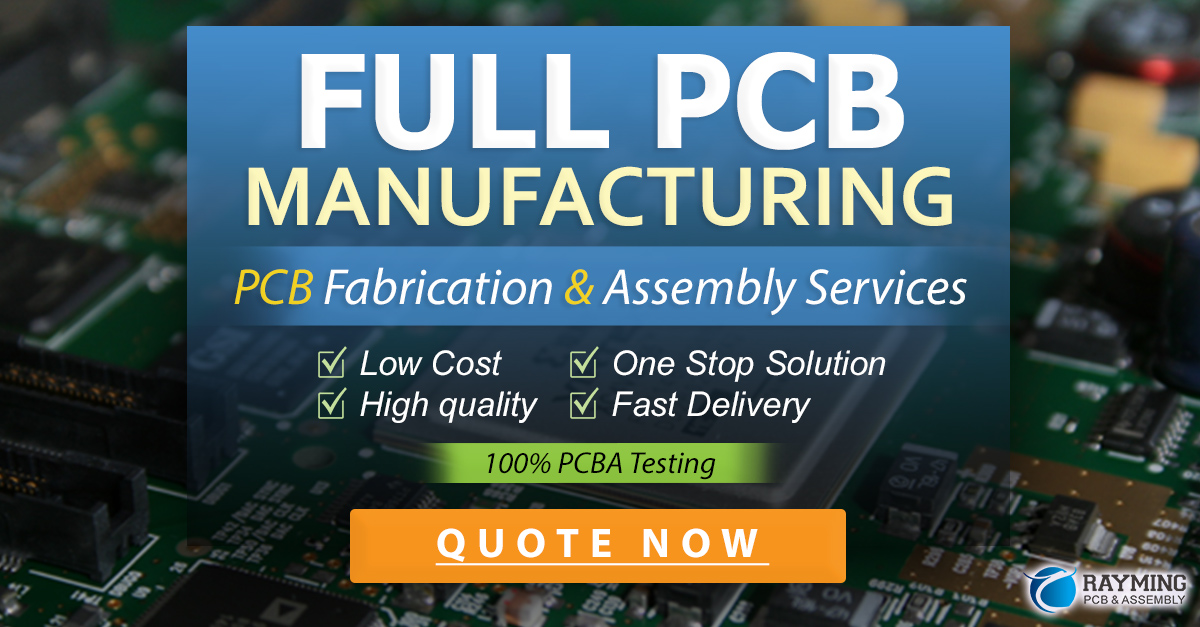
Best Practices for Tented Via Design
To ensure optimal tented via performance and manufacturability, consider the following best practices:
-
Use appropriate via sizes: Choose via sizes that are compatible with the PCB manufacturing capabilities and allow for sufficient tented via clearance. Avoid using excessively small or large vias that may pose manufacturing challenges.
-
Maintain consistent clearance: Ensure that the tented via clearance is consistent across the PCB Design. Inconsistent clearances can lead to manufacturing issues and potential reliability problems.
-
Consider solder mask material: Select a solder mask material that is compatible with the desired tented via clearance and offers good flow and adhesion properties. Consult with the PCB manufacturer for recommendations.
-
Optimize via placement: Place tented vias strategically to minimize the impact on adjacent traces and components. Avoid placing vias too close to other features that may interfere with the solder mask coverage.
-
Conduct design reviews: Perform thorough design reviews to ensure that the tented via clearance meets the manufacturing requirements and industry standards. Collaborate with the PCB manufacturer to address any potential issues or concerns.
-
Test and validate: Conduct appropriate testing and validation to verify the integrity and reliability of the tented vias. This may include electrical testing, visual inspection, and environmental stress testing.
Frequently Asked Questions (FAQ)
-
What is the purpose of tented vias in PCB design?
Tented vias serve several purposes in PCB design, including providing electrical connectivity between layers, improving signal integrity, and protecting the via from environmental factors such as moisture and contaminants. -
How does tented via clearance affect PCB manufacturability?
Tented via clearance directly impacts PCB manufacturability. Insufficient clearance can lead to solder mask breakage, peeling, or incomplete coverage, which can cause short circuits or other manufacturing defects. Adequate clearance ensures proper solder mask application and reduces the risk of manufacturing issues. -
Can tented via clearance be adjusted based on specific design requirements?
Yes, tented via clearance can be adjusted based on specific design requirements. In some cases, tighter clearances may be necessary to accommodate dense layouts or high-speed signals, while other designs may allow for larger clearances to improve manufacturability. It’s important to consult with the PCB manufacturer and adhere to their guidelines. -
What are the consequences of insufficient tented via clearance?
Insufficient tented via clearance can lead to various issues, such as short circuits, signal integrity problems, and reduced reliability. It can also cause manufacturing defects, such as solder mask breakage or incomplete coverage, which can result in costly rework or scrap. -
How can designers ensure optimal tented via clearance in their PCB Layouts?
To ensure optimal tented via clearance, designers should follow industry guidelines and best practices, such as using appropriate via sizes, maintaining consistent clearance, considering solder mask material properties, optimizing via placement, conducting design reviews, and performing thorough testing and validation. Collaboration with the PCB manufacturer is also crucial to address any specific requirements or constraints.
Conclusion
Tented via clearance, or hole edge to solder mask edge clearance, is a critical aspect of PCB design that ensures proper insulation, manufacturing reliability, signal integrity, and compliance with industry standards. By understanding the factors that influence tented via clearance, following recommended guidelines, and adhering to best practices, designers can create PCB layouts that are manufacturable, reliable, and perform optimally.
Maintaining appropriate tented via clearance requires careful consideration of via sizes, solder mask material properties, manufacturing capabilities, and design constraints. Collaboration with the PCB manufacturer is essential to ensure that the design meets their specific guidelines and requirements.
By prioritizing tented via clearance in PCB design, designers can minimize the risk of manufacturing defects, improve overall reliability, and ensure the long-term performance of the electronic device. As technology advances and PCB designs become more complex, understanding and implementing proper tented via clearance techniques will remain a crucial skill for designers in the electronics industry.
Leave a Reply