Introduction to HDI PCB Stackup
High Density Interconnect (HDI) PCBs have become increasingly popular in the electronics industry due to their ability to accommodate high component density and complex circuitry in a compact form factor. HDI PCB stackup refers to the arrangement of copper layers, dielectric materials, and vias within the PCB structure. Choosing the right HDI PCB stackup is crucial for ensuring optimal performance, reliability, and manufacturability of your PCB design.
In this article, we will explore the different types of HDI PCB Stackups and help you determine which stackup type is best suited for your specific PCB requirements.
What is HDI PCB Stackup?
An HDI PCB stackup is a cross-sectional representation of the layers and materials used in an HDI PCB. It defines the number and arrangement of copper layers, the type and thickness of dielectric materials, and the placement of vias and other interconnects. The stackup plays a critical role in determining the electrical, thermal, and mechanical properties of the PCB.
A typical HDI PCB stackup consists of the following components:
-
Copper Layers: These are the conductive layers that carry electrical signals and power throughout the PCB. HDI PCBs typically have 4 to 16 copper layers.
-
Dielectric Materials: These are the insulating layers that separate the copper layers and provide electrical isolation. Common dielectric materials include FR-4, Rogers, and polyimide.
-
Vias: These are the vertical interconnects that allow signals to pass between different copper layers. HDI PCBs utilize various types of vias, such as blind vias, buried vias, and microvias.
-
Solder Mask: This is a protective coating applied to the outer layers of the PCB to prevent short circuits and improve solderability.
-
Silkscreen: This is a printed layer on the PCB surface that provides component identification and assembly information.
Types of HDI PCB Stackups
There are several types of HDI PCB stackups, each with its own advantages and limitations. The choice of stackup depends on factors such as the number of layers, the required signal integrity, the component density, and the manufacturing cost. Let’s explore the most common types of HDI PCB stackups:
1. 1+N+1 Stackup
The 1+N+1 stackup is the simplest and most cost-effective HDI PCB stackup. It consists of a core layer (N) sandwiched between two outer layers (1+1). The outer layers are typically used for component placement and routing, while the core layer is used for power and ground planes.
Advantages:
– Low cost
– Easy to manufacture
– Suitable for simple designs with low layer count
Limitations:
– Limited routing density
– Limited signal integrity performance
– Not suitable for complex designs with high layer count
2. 2+N+2 Stackup
The 2+N+2 stackup is an extension of the 1+N+1 stackup, with an additional outer layer on each side. This stackup provides more routing flexibility and signal integrity compared to the 1+N+1 stackup.
Advantages:
– Improved routing density
– Better signal integrity performance
– Suitable for moderately complex designs
Limitations:
– Higher cost than 1+N+1 stackup
– Limited layer count compared to more advanced stackups
3. 3+N+3 Stackup
The 3+N+3 stackup further increases the number of outer layers to three on each side of the core layer. This stackup offers even greater routing density and signal integrity compared to the 2+N+2 stackup.
Advantages:
– High routing density
– Excellent signal integrity performance
– Suitable for complex designs with high component density
Limitations:
– Higher cost than 2+N+2 stackup
– Increased manufacturing complexity
4. Any Layer HDI Stackup
The Any Layer HDI stackup is the most advanced and flexible HDI PCB stackup. It allows for the placement of microvias in any layer of the PCB, providing the highest level of routing density and design flexibility.
Advantages:
– Maximum routing density
– Unlimited design flexibility
– Suitable for the most complex and demanding PCB designs
Limitations:
– Highest cost among HDI PCB stackups
– Requires advanced manufacturing capabilities
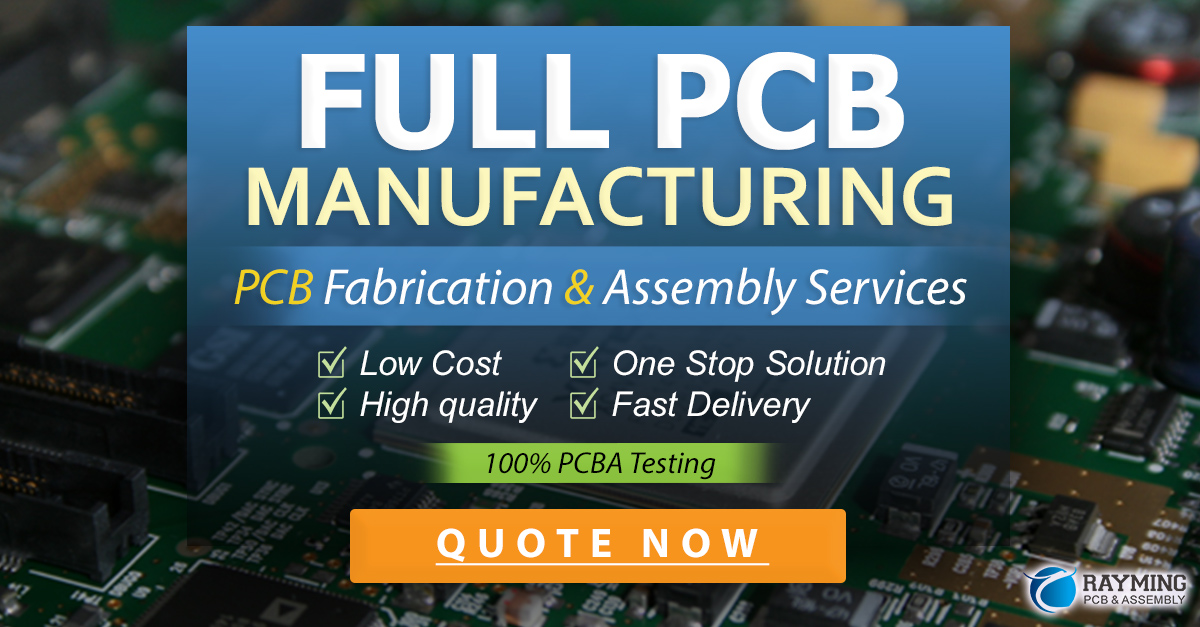
Choosing the Right HDI PCB Stackup
To determine the most suitable HDI PCB stackup for your design, consider the following factors:
-
Design Complexity: Evaluate the complexity of your PCB design, including the number of components, signal traces, and power requirements. More complex designs may require higher layer counts and more advanced stackups.
-
Signal Integrity: Assess the signal integrity requirements of your design. High-speed and sensitive signals may demand better isolation and shielding, which can be achieved with appropriate stackup choices.
-
Manufacturing Cost: Consider the manufacturing cost implications of different stackup options. Generally, higher layer counts and more advanced stackups result in higher manufacturing costs.
-
Manufacturing Capabilities: Ensure that your chosen stackup can be manufactured reliably by your PCB fabrication partner. Some advanced stackups may require specialized manufacturing capabilities.
-
board thickness: Consider the overall thickness of the PCB and the impact of different stackup options on the final board thickness. Some applications may have strict thickness constraints.
Here’s a comparison table of the different HDI PCB stackups:
Stackup Type | Layers | Routing Density | Signal Integrity | Cost | Complexity |
---|---|---|---|---|---|
1+N+1 | 3-4 | Low | Low | Low | Simple |
2+N+2 | 6-8 | Medium | Medium | Medium | Moderate |
3+N+3 | 9-12 | High | High | High | Complex |
Any Layer | 12+ | Very High | Very High | Very High | Very Complex |
FAQ
-
What is the minimum feature size achievable with HDI PCBs?
HDI PCBs can typically achieve a minimum feature size of 3 mil (75 microns) for traces and spaces, and 4 mil (100 microns) for via diameters. -
Can HDI PCBs be used for high-power applications?
Yes, HDI PCBs can be designed to handle high-power applications by incorporating appropriate copper weights, dielectric materials, and thermal management techniques. -
Are HDI PCBs more expensive than traditional PCBs?
Yes, HDI PCBs are generally more expensive than traditional PCBs due to their higher layer counts, smaller feature sizes, and advanced manufacturing requirements. -
What are the benefits of using blind and buried vias in HDI PCBs?
Blind and buried vias in HDI PCBs enable higher routing density, improved signal integrity, and better utilization of board space by freeing up the outer layers for component placement. -
How do I ensure the manufacturability of my HDI PCB design?
To ensure the manufacturability of your HDI PCB design, follow the design guidelines provided by your PCB fabrication partner, use appropriate design rules and constraints, and communicate closely with the fabricator throughout the design process.
Conclusion
Choosing the right HDI PCB stackup is essential for achieving optimal performance, reliability, and manufacturability in your PCB design. By understanding the different types of HDI PCB stackups and their advantages and limitations, you can make an informed decision based on your specific design requirements.
Consider factors such as design complexity, signal integrity, manufacturing cost, and manufacturing capabilities when selecting the most suitable HDI PCB stackup for your project. By working closely with your PCB fabrication partner and following best design practices, you can unlock the full potential of HDI technology in your electronic products.
Leave a Reply