What is HASL?
HASL is a surface finish that involves immersing the PCB in a molten solder bath, typically consisting of a tin-lead alloy. The excess solder is then blown off the surface using hot air, leaving a thin, even layer of solder on the copper traces. HASL has been a popular choice for many years due to its low cost and ease of application.
Advantages of HASL
- Cost-effective: HASL is one of the most economical surface finishes available.
- Good solderability: The solder layer provides excellent wetting properties for component assembly.
- Quick turnaround: HASL is a relatively fast process, allowing for shorter lead times.
Disadvantages of HASL
- Uneven surface: The hot air leveling process can result in an uneven surface, which may cause issues with fine-pitch components.
- Thermal shock: The high temperature of the molten solder bath can cause thermal stress on the PCB.
- Environmental concerns: Traditional HASL uses lead-based solder, which has environmental and health implications.
What is ENIG?
ENIG is a two-layer surface finish that consists of an electroless nickel layer followed by a thin immersion gold layer. The nickel layer serves as a barrier to prevent copper migration, while the gold layer provides excellent solderability and protection against oxidation.
Advantages of ENIG
- Flat surface: ENIG provides a flat, even surface that is ideal for fine-pitch components and surface mount technology (SMT).
- Long shelf life: The gold layer offers excellent oxidation resistance, allowing for a longer shelf life compared to HASL.
- RoHS Compliance: ENIG is a lead-free process, making it compliant with Restriction of Hazardous Substances (RoHS) regulations.
Disadvantages of ENIG
- Higher cost: ENIG is more expensive than HASL due to the use of gold and the more complex process.
- Black pad: In some cases, a nickel-gold intermetallic compound can form, resulting in a “black pad” that can cause solderability issues.
- Sensitive to handling: The thin gold layer can be easily damaged by improper handling or storage.
HASL-ENIG Comparison
Property | HASL | ENIG |
---|---|---|
Cost | Low | High |
Surface Flatness | Uneven | Flat |
Shelf Life | Shorter | Longer |
RoHS Compliance | No (lead-based) | Yes |
Solderability | Good | Excellent |
Thermal Stress | High | Low |
Fine-Pitch Compatibility | Limited | Excellent |
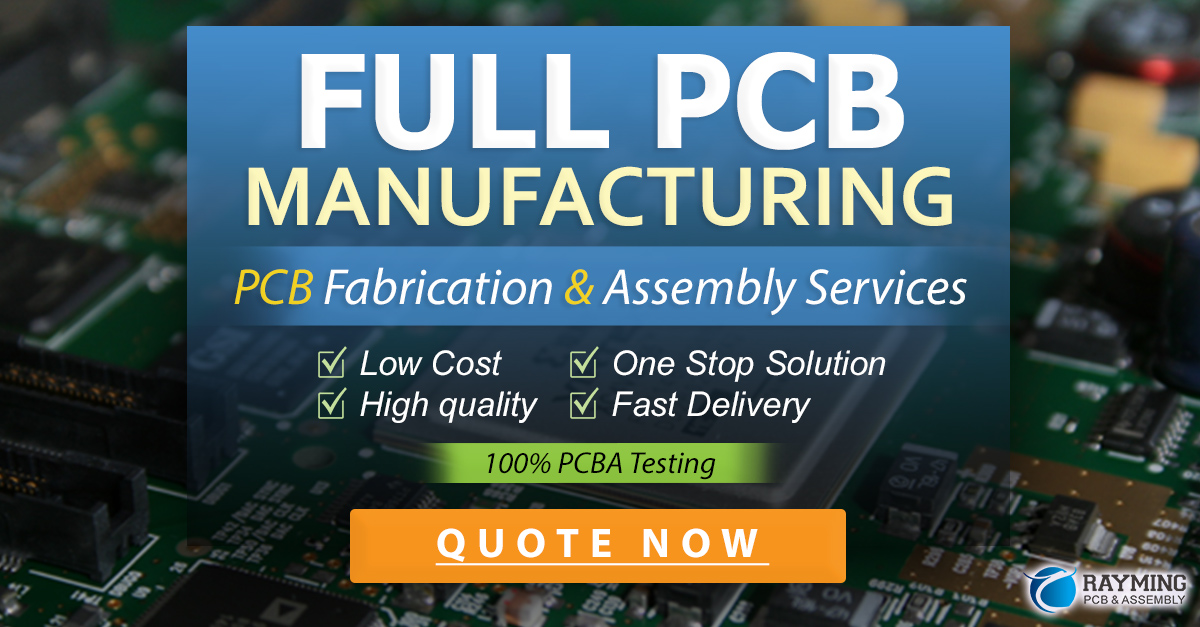
10 Tips on How to Choose Enig Plating
- Consider your budget: ENIG is more expensive than HASL, so ensure that it fits within your project’s financial constraints.
- Evaluate your component requirements: If your PCB design includes fine-pitch components or SMT, ENIG’s flat surface is more suitable.
- Assess your shelf life needs: If your PCBs need to be stored for an extended period before assembly, ENIG’s oxidation resistance is beneficial.
- Ensure RoHS compliance: If your project must adhere to RoHS regulations, ENIG is the better choice.
- Analyze your PCB’s thermal requirements: If your PCB will be subjected to high temperatures during assembly or operation, ENIG’s lower thermal stress is advantageous.
- Consider your assembly process: ENIG’s excellent solderability can lead to improved yields and fewer defects during assembly.
- Evaluate your supplier’s capabilities: Ensure that your chosen PCB Manufacturer has experience and expertise in applying ENIG surface finish.
- Assess your handling and storage procedures: ENIG’s thin gold layer requires proper handling and storage to prevent damage.
- Conduct thorough testing: Before committing to ENIG, perform solderability and reliability tests to ensure it meets your specific requirements.
- Consider alternative surface finishes: While ENIG is an excellent choice for many applications, other surface finishes like Immersion Silver (IAg) or Electroless Palladium Immersion Gold (EPIG) may be more suitable for your specific needs.
FAQ
-
Q: Is ENIG always the best choice for PCB Surface Finish?
A: No, the choice of surface finish depends on various factors such as budget, component requirements, shelf life, and compliance with regulations. HASL or other surface finishes may be more suitable in certain situations. -
Q: Can ENIG be used for both through-hole and surface mount components?
A: Yes, ENIG is compatible with both through-hole and surface mount components. Its flat surface and excellent solderability make it particularly well-suited for fine-pitch and SMT components. -
Q: How does ENIG compare to other lead-free surface finishes?
A: ENIG is one of several lead-free surface finishes available, such as IAg and EPIG. Each finish has its own advantages and disadvantages, and the choice depends on factors such as cost, solderability, and specific application requirements. -
Q: What causes the “black pad” issue with ENIG, and how can it be prevented?
A: The “black pad” issue occurs when a nickel-gold intermetallic compound forms, resulting in a non-solderable surface. This can be prevented by proper process control during ENIG application, including maintaining appropriate nickel and gold layer thicknesses and ensuring proper pre-treatment of the PCB surface. -
Q: Can ENIG be reworked if necessary?
A: Yes, ENIG can be reworked, but it requires careful handling and proper techniques to avoid damaging the surface finish. Rework should be performed by experienced technicians using appropriate tools and procedures.
In conclusion, choosing between HASL and ENIG surface finishes for your PCB project requires careful consideration of various factors, including budget, component requirements, shelf life, and compliance with regulations. By understanding the advantages and disadvantages of each finish and following the 10 tips provided for selecting ENIG plating, you can make an informed decision that best suits your specific needs. Remember to work closely with your PCB manufacturer and conduct thorough testing to ensure the success of your project.
Leave a Reply